National Science Centre (NCN) supports fundamental research by funding research projects carried out by individual researches and research teams, both on the domestic and international level, as well as doctoral fellowships and post-doctoral internships. NCN announces calls for proposals four times a year. The NCN grantee must be employed at a Polish host institution.
OPUS is a funding opportunity intended for a wide range of applicants. The research proposal submitted under this scheme may include the purchase or construction of research equipment.
PRELUDIUM is a funding opportunity intended for pre-doctoral researchers.
In November 2020, National Science Centre has approved and subsidized two new projects from IPPT PAN:
- Project: Multiscale investigation of deformation and damage behavior of novel hybrid metal matrix composites. Experimental studies and numerical modeling (OPUS), coordinator: Szymon Nosewicz
Hybrid metal matrix composites (HMMCs) are the new and improved version of metal matrix composites (MMCs) becoming one of the most advanced materials group used for aerospace, automotive, defense and general engineering applications. HMMCs are formed by reinforcing the metal matrix by two or more material types of varying properties, or two different sizes of the same material. Comparing to MMCs, they can be tailored to have superior properties such as enhanced high-temperature performance, high specific strength and stiffness, increased wear resistance, better thermal and mechanical fatigue and creep resistance. Due to their possible applications, the deformation and damage behavior is one of the most crucial issues in the context of durability and long-term performance of HMMCs.
The mechanical properties of HMMCs can be efficiently predicted by the multiscale modeling approach, which has seen widespread application in various scientific and engineering disciplines. It allows taking into account the structural composite features at different scales, such as microscopic (the type of matrix material, reinforcement volume and size, the quality of the metal/ceramic interface) or/and atomistic one (the density of material defects, the grains orientations and the type of grain boundaries). The phenomena at lower scales affect the composite behavior at a macroscopic scale.
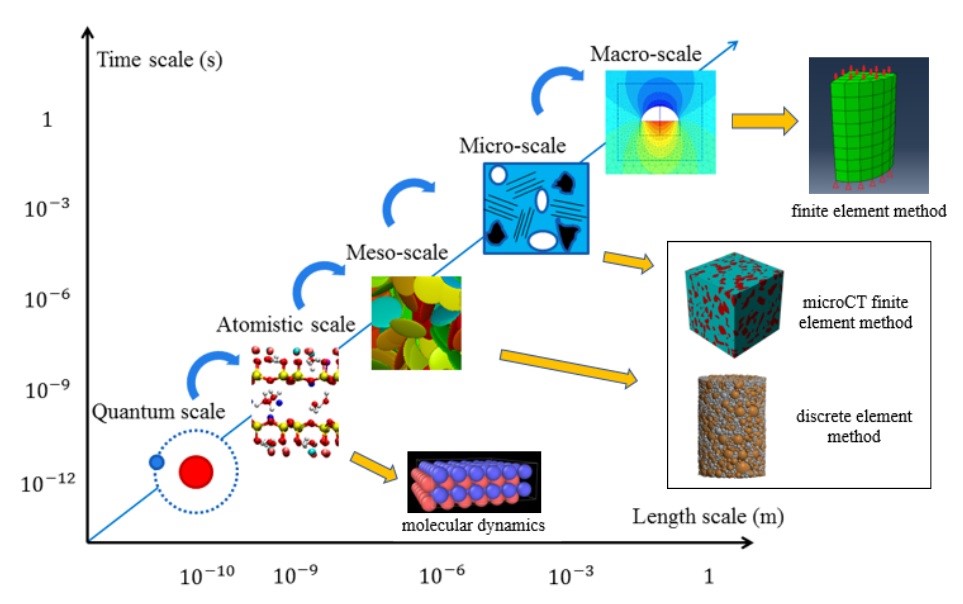
Within the proposed project, development, implementation and validation of numerical models predicting the deformation behavior up to damage of hybrid metal matrix composites will be performed for different scales: atomistic, microscopic and macroscopic one (Fig. 1). Different approaches and different numerical models appropriate for each scale will be employed. The molecular dynamics (MD) simulations will be performed to study at the atomistic scale the strength of each composites components: metal matrix, ceramic reinforcement and metal-ceramic interface. MD simulations allow determining the input parameters of micromechanical models - discrete and micro-CT finite element. By taking into account the composite microstructure, microscopic models will provide data for macroscopic modeling. The top of the multiscale approach will be a numerical simulation of small punch test, which is a new method of material strength determination gaining more and more recognition. The numerical models will be validated using the results of own experimental studies performed within this project. Experimental studies consist of mechanical properties tests performed at three scales: nano-, micro- and macroscopic one. The experimental and numerical approach will be used to model the deformation behavior and strength of three kinds of composites. The intermetallic (NiAl) based material reinforced with hybrid ceramic (Al2O3) particles with different size has been selected as a representative material of a class of novel composite materials characterized by the brittle type of deformation. The two representatives of ductile materials are the copper (Cu) and nickel (Ni) matrix composites reinforced by (micron+submicron+nano) multisized silicon carbide (SiC) particles. Ni-SiC composite will be developed as a new innovative metal matrix composite manufactured by sintering techniques. Deformation behavior and damage properties of composites will be studied in respect to their volume content and reinforcement composition.
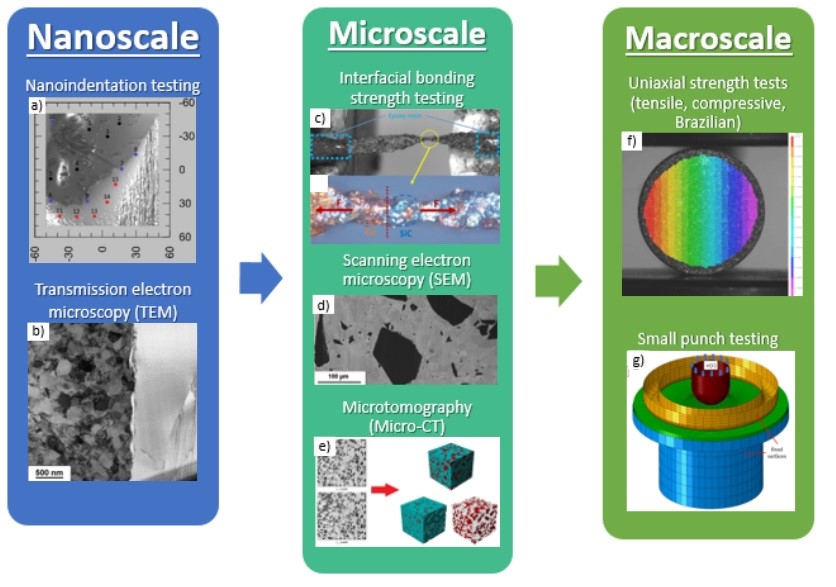
- Project: Impact of the 3D printing process on the acoustic properties of porous materials (PRELUDIUM), coordinator: Kamil Opiela
It is popularly known that porous materials are effective acoustic absorbers. They possess superior damping properties due to a specific internal structure consisting of a solid skeleton and 'voids' (pores) filled with fluid. Nowadays, continuously evolving additive manufacturing techniques allow forming porous samples with a definite microgeometry. However, their measured acoustic performance is usually different from designed because of some production flaws and other imperfections. Thus, adopting appropriate modelling enhancements that will accommodate computer simulations of wave propagation and sound absorption in such media to reality should eventually lead to substantial benefits from the practical point of view.
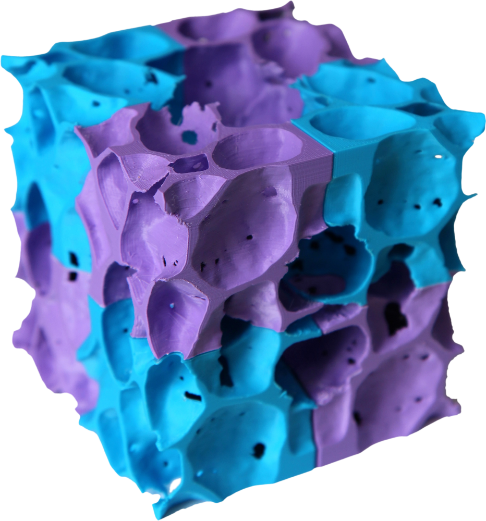
It has been shown that the acoustic wave attenuation in fabricated rigid porous layers is eminently underestimated by numerical calculations using standard models. Based on this observation, the major postulate that will be put forward in the project concerns the impact of the additive manufacturing technology on the acoustic properties of produced samples, and may be stated as follows: the three-dimensional (3D) printing process yields rough surfaces of a material skeleton so that some enhancements to the existing models of wave propagation in porous media are indispensable to get reliable simulations. According to another hypothesis, however, the substantial discrepancies may come from an extra microporosity, much smaller in characteristic dimensions of 'voids' than the main porous network, that has been unintentionally created within the skeleton at the forming stage. These two possibilities will be essentially checked in the course of the investigation comprising four main parts, namely: 1. Generation and re-design of periodic porous structures with open porosity; 2. 3D printing of material samples using various additive manufacturing technologies; 3. Evaluation of the fabricated specimens in terms of their effective acoustic properties (experiments in the impedance tube) and geometrical accordance to the corresponding computer-aided design model; and 4. Numerical studies based on existing (to a large extend recent) mathematical models and procedures for single- and dual-porosity materials. These activities will be carried out more or less simultaneously. First of all, the measurement data should be confronted with the results obtained from multiscale, microstructure-based modelling to validate and perhaps correct the implementation of original theoretical developments and scientific hypotheses. Secondly, the dimensions and shapes of the constructed periodic cells representative for the particular morphology of the investigated porous media need to be compared under a microscope with their manufactured equivalents.
There are at least threefold reasons for choosing this research topic. First, the accomplishment of the project objectives, especially those concerning the confirmation of the versatility and robustness of the utilised modelling, will definitely entail prompt further scientific developments within the framework of 3D-printed noise reducing materials, but not only. Invention of advanced goal-oriented sound absorbers with optimised microgeometry and of a moderate thickness (i.e. weight) being marked by an excellent performance at some considered frequency ranges still seems to be the subject of keen interest in the aviation and automotive industries. If the manufacturing of such modern porous structures will eventually meet with success, an invaluable positive social and environmental impact related to the overall noise attenuation appears quite self-evident. Last, but by no means least, some of the macroscopic material characteristics fed into the models for sound propagation and absorption in porous media (permeability, tortuosity, etc.) can also be relevant for other theories in applications different from acoustics, for instance in biotechnology, medicine, or geotechnics.
Fig.2.: Periodic unit cell representative for a real metal foam skeleton and composed of four non-periodic cells as well as their mirrored copies printed in the Fused Deposition Modelling 3D printing technology at 12.5x magnification