1. |
Sciortino F.♦, Mir S.H.♦, Pakdel A.♦, Oruganti A.♦, Abe H.♦, Witecka A., Awang Shri D.N.♦, Rydzek G.♦, Ariga K.♦, Saloplastics as multiresponsive ion exchange reservoirs and catalyst supports,
Journal of Materials Chemistry A, ISSN: 2050-7488, DOI: 10.1039/d0ta05901c, Vol.8, No.34, pp.17713-17724, 2020 Abstract: Developing saloplastics composed of Compacted Polyelectrolyte Complexes (COPECs) represents a promising strategy for assembling multifunctional and processable polymer matrices in a simple manner. Here, a comprehensive investigation of the potential application of saloplastics as ion reactors for designing catalysts has been performed. First the propensity of saloplastics to exchange and concentrate ions has been elucidated through investigating the influence of Na+ to Cu2+ cation exchange within COPECs assembled from poly(methacrylic acid) (PMAA) and poly(allylamine hydrochloride) (PAH). The multi-scale responses of PMAA/PAH COPECs upon incubation with CuCl2 solutions at pH 3 and 4.5 were investigated chemically by ATR-FTIR, ICP, XPS, DSC and TGA, morphologically by SEM, and mechanically by strain-to-break measurements. Both the amplitude and the kinetics of the COPEC response were driven by the deprotonation rate of PMAA chains, enabling the formation of bridge complexes with Cu2+ and impacting the saloplastic's composition (water content and polyelectrolytes), structure (emergence of macropores) and mechanical properties. Kinetic-based tuning of the molality of copper ions trapped in PMAA/PAH COPECs was demonstrated, enabling the usage of saloplastics as reactors. This ability allowed controlling the growth of Cu(0) nanoparticles in saloplastics by thermal annealing, ultimately adjusting their catalytic activity toward carbon monoxide (CO) oxidation. This work highlights how the ionic reservoir properties of saloplastics must be accounted for when designing the applications of COPEC-based materials. Affiliations:
Sciortino F. | - | other affiliation | Mir S.H. | - | other affiliation | Pakdel A. | - | World Premier International Center for Materials Nanoarchitectonics (MANA) (JP) | Oruganti A. | - | other affiliation | Abe H. | - | other affiliation | Witecka A. | - | IPPT PAN | Awang Shri D.N. | - | Universiti Malaysia Pahang (MY) | Rydzek G. | - | National Institute for Materials Science (JP) | Ariga K. | - | National Institute for Materials Science (JP) |
| 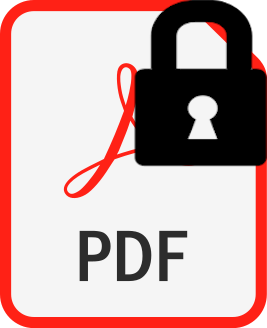 |
2. |
Rydzek G.♦, Pakdel A.♦, Witecka A., Shri D.N.A.♦, Gaudière F.♦, Nicolosi V.♦, Mokarian-Tabari P.♦, Schaaf P.♦, Boulmedais F.♦, Ariga K.♦, pH-Responsive Saloplastics Based on Weak Polyelectrolytes: From Molecular Processes to Material Scale Properties,
Macromolecules, ISSN: 0024-9297, DOI: 10.1021/acs.macromol.8b00609, Vol.51, No.12, pp.4424-4434, 2018 Abstract: Compact polyelectrolyte complexes (COPECs), also named saloplastics, represent a new class of material with high fracture strain and self-healing properties. Here, COPECs based on poly(methacrylic acid) (PMAA) and poly(allylamine hydrochloride) (PAH) were prepared by centrifugation at pH 7. The influence of postassembly pH changes was monitored chemically by ATR-FTIR, ICP, DSC, and TGA, morphologically by SEM, and mechanically by strain to break measurements. Postassembly pH stimuli misbalanced the charge ratio in COPECs, impacting their concentration in counterions, cross-link density, and polymer chain mobility. At the material level, changes were observed in the porosity, composition, water content, and mechanical properties of COPECs. The cross-link density was a prominent factor governing the saloplastic's composition and water content. However, the porosity and mechanical properties were driven by several factors including salt-induced plasticization and conformational changes of polyelectrolytes. This work illustrates how multiple-scale consequences arise from a single change in the environment of COPECs, providing insights for future design of stimuli-responsive materials. Affiliations:
Rydzek G. | - | National Institute for Materials Science (JP) | Pakdel A. | - | World Premier International Center for Materials Nanoarchitectonics (MANA) (JP) | Witecka A. | - | IPPT PAN | Shri D.N.A. | - | Universiti Malaysia Pahang (MY) | Gaudière F. | - | Université de Strasbourg (FR) | Nicolosi V. | - | Trinity College (IE) | Mokarian-Tabari P. | - | Trinity College (IE) | Schaaf P. | - | Institut National de la Santé et de la Recherche Médicale (FR) | Boulmedais F. | - | Université de Strasbourg (FR) | Ariga K. | - | National Institute for Materials Science (JP) |
| 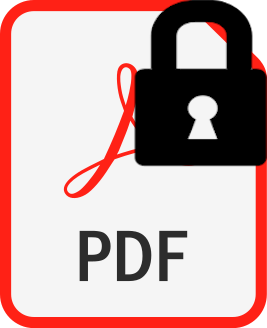 |
3. |
Pakdel A.♦, Witecka A., Rydzek G.♦, Shri D.N.A.♦, Nicolosi V.♦, A comprehensive analysis of extrusion behavior, microstructural evolution, and mechanical properties of 6063 Al–B4C composites produced by semisolid stir casting,
MATERIALS SCIENCE AND ENGINEERING A-STRUCTURAL MATERIALS PROPERTIES MICROSTRUCTURE AND PROCESSING, ISSN: 0921-5093, DOI: 10.1016/j.msea.2018.02.080, Vol.721, pp.28-37, 2018 Abstract: In this study, composites of aluminum alloy 6063 reinforced with 10 wt% boron carbide microparticles were successfully fabricated by a combination of spark plasma sintering and stir casting methods, followed by hot extrusion. A systematic study on the relationship between extrusion process variables (i.e. extrusion ratio, temperature, and punch speed) and porosity, particle refinement, particle distribution and consequently tensile properties and fracture behavior of the composites was performed. Extensive electron microscopy analysis and tensile testing of the composites revealed a multifactoral interdependency of microstructural evolution and mechanical properties on the extrusion process variables. For example, while increasing the extrusion ratio at higher temperatures led to moderate particle refinement, better densification of the composites, and improvement in mechanical properties, concurrent particle fragmentation and microvoid formation around the particles at lower temperatures had opposing effects on the mechanical behavior. We show that the dependency of mechanical properties on all such microstructural factors makes it difficult to predict optimum extrusion conditions in aluminum matrix composites. That is, unlike the common approach, extruding the composites at higher temperatures and achieving more reduction in area may not necessarily lead to the most favorable mechanical properties. Keywords: Aluminum matrix composite, Hot extrusion, Mechanical behavior, Microstructure, Spark plasma sintering, Stir casting Affiliations:
Pakdel A. | - | World Premier International Center for Materials Nanoarchitectonics (MANA) (JP) | Witecka A. | - | IPPT PAN | Rydzek G. | - | National Institute for Materials Science (JP) | Shri D.N.A. | - | Universiti Malaysia Pahang (MY) | Nicolosi V. | - | Trinity College (IE) |
| 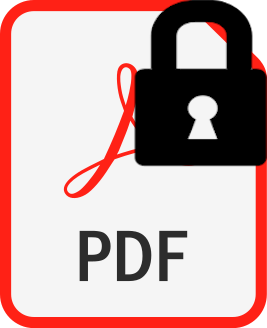 |
4. |
Pakdel A.♦, Witecka A., Rydzek G.♦, Shri D.N.A.♦, A comprehensive microstructural analysis of Al–WC micro- and nano-composites prepared by spark plasma sintering,
MATERIALS AND DESIGN, ISSN: 0264-1275, DOI: 10.1016/j.matdes.2017.01.064, Vol.119, pp.225-234, 2017 Abstract: There have been many investigations on metal matrix microcomposites produced by conventional casting routes; however, in the past decade, the focus has shifted more toward nanocomposites produced via solid state routes. To have a realistic view of performance prediction and optimum design of such composites, in this work Al matrix composites (AMCs) reinforced with WC microparticles, nanoparticles, and bimodal micro-/nano-particles were prepared by spark plasma sintering. The effects of particle size and concentration, and process variables (i.e. sintering temperature, duration, and pressure) on the evolution of microstructure, density and hardness of the composites were studied comprehensively. Full densification of AMCs with high particle concentration was problematic because of ceramic cluster formations in the microstructure. This effect was more emphasized in AMCs containing nanoparticles. AMCs with microparticles were more easily densified, but their hardness benefits were inferior. On the other hand, the mixture of micro- and nano-particles in Al-WC bimodal composites led to better matrix reinforcement integrity and an overall improvement in the microstructural properties. Finally, increasing the sintering temperature improved the microstructural features and hardness of the composites (more enhanced in high wt.% samples), but sintering duration and pressure did not have a big impact on the composite properties. Keywords: composite, nanoparticle, microparticle, powder metallurgy, SPS, microstructure Affiliations:
Pakdel A. | - | World Premier International Center for Materials Nanoarchitectonics (MANA) (JP) | Witecka A. | - | IPPT PAN | Rydzek G. | - | National Institute for Materials Science (JP) | Shri D.N.A. | - | Universiti Malaysia Pahang (MY) |
| 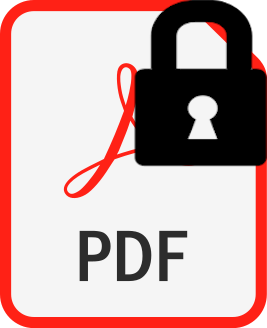 |