1. |
Liu X.♦, Jin S.♦, Ming M.♦, Fan C.♦, Liu H.♦, Politis D.J.♦, Kopeć M., A high throughput in-situ measurement of heat transfer in successive non-isothermal forming of sheet alloys,
Journal of Manufacturing Processes, ISSN: 1526-6125, DOI: 10.1016/j.jmapro.2024.08.048, Vol.129, pp.77-91, 2024 Abstract: The measurement and control of the heat transfer of sheet alloys in successive non-isothermal forming cycles is crucial to achieve the desired post-form properties and microstructure, which could not as of yet be realized by using traditional test facilities. In the present research, a novel heat transfer measurement facility was designed to generate and subsequently measure the in-situ heat transfer from a sheet alloy to multi-mediums such as forming tools, air, lubricant and coating. More importantly, the facility was able to use a single sheet alloy sample to perform successive non-isothermal forming cycles, and subsequently obtain high throughput experimental results including the temperature evolution, cooling rate, mechanical properties and microstructures of the alloy. The high throughput in-situ heat transfer measurement facility identified that the cooling rate of AA7075 was 152 °C/s and the mechanical strength was over 530 MPa in the 1st forming cycle. However, it decreased to less than the critical value of 100 °C/s in the successive 10th forming cycle, leading to a low mechanical strength of only 487 MPa. The identified variations that occur in the successive non-isothermal forming cycles would improve the consistency and accuracy of part performance in large-scale manufacturing. Keywords: High throughput in-situ measurement,Heat transfer,Successive non-isothermal forming,Sheet alloys,Microstructure Affiliations:
Liu X. | - | Imperial College London (GB) | Jin S. | - | other affiliation | Ming M. | - | other affiliation | Fan C. | - | other affiliation | Liu H. | - | Imperial College London (GB) | Politis D.J. | - | Imperial College London (GB) | Kopeć M. | - | IPPT PAN |
| 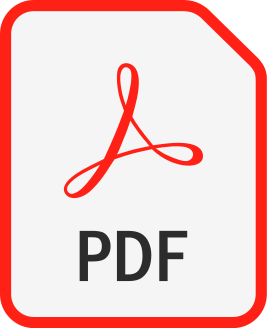 |
2. |
Kopeć M., Politis D.♦, Advances in Sheet Metal Forming Processes of Lightweight Alloys,
Materials, ISSN: 1996-1944, DOI: 10.3390/ma16093293, Vol.16, No.3293, pp.1-4, 2023, EDITORIAL Abstract: With the continuously growing need for more fuel-efficient and sustainable vehicles, the characterization and modeling of metal-forming processes have been indispensable in the development of new products. In the automotive and aviation sector, low-strength structural components are commonly produced from aluminum alloys, and higher-strength structural components are made from ultra-high-strength steels (UHSSs) and titanium alloys. The main issue experienced during the hot forming of complex-shaped components from difficult-to-form alloys is that they are time-, energy-, and cost-intensive. The aircraft industry currently uses methods such as superplastic forming (SPF), superplastic forming with diffusion bonding (SPF-DB), hot stretch forming, hot gas-pressure forming, and isothermal hot forming. Moreover, novel techniques have been developed to produce complex-shaped structural components including solution heat treatment, forming and in-die quenching (HFQ), quick-plastic forming, hot stamping using rapid heating, and fast light alloy stamping technology (FAST). Affiliations:
Kopeć M. | - | IPPT PAN | Politis D. | - | Imperial College London (GB) |
| 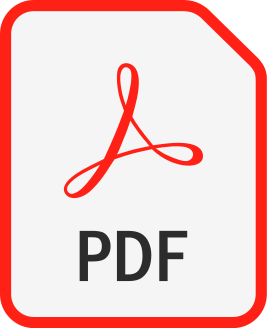 |
3. |
Liu X.♦, Di B.♦, Yu X.♦, Liu H.♦, Dhawan S.♦, Politis D.J.♦, Kopeć M., Wang L.♦, Development of a Formability Prediction Model for Aluminium Sandwich Panels with Polymer Core,
Materials, ISSN: 1996-1944, DOI: 10.3390/ma15124140, Vol.15, No.12, pp.4140-1-12, 2022 Abstract: In the present work, the compatibility relationship on the failure criteria between aluminium and polymer was established, and a mechanics-based model for a three-layered sandwich panel was developed based on the M-K model to predict its Forming Limit Diagram (FLD). A case study for a sandwich panel consisting of face layers from AA5754 aluminium alloy and a core layer from polyvinylidene difluoride (PVDF) was subsequently conducted, suggesting that the loading path of aluminium was linear and independent of the punch radius, while the risk for failure of PVDF increased with a decreasing radius and an increasing strain ratio. Therefore, the developed formability model would be conducive to the safety evaluation on the plastic forming and critical failure of composite sandwich panels. Keywords: formability, M-K model, failure criteria, composite sandwich panel Affiliations:
Liu X. | - | Imperial College London (GB) | Di B. | - | Imperial College London (GB) | Yu X. | - | Imperial College London (GB) | Liu H. | - | Imperial College London (GB) | Dhawan S. | - | Imperial College London (GB) | Politis D.J. | - | Imperial College London (GB) | Kopeć M. | - | IPPT PAN | Wang L. | - | Imperial College London (GB) |
| 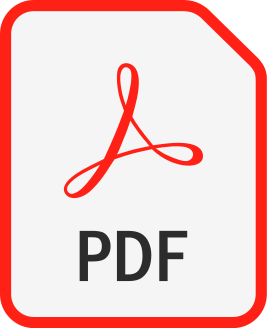 |
4. |
Szczęsny G.♦, Kopeć M., Politis D.J.♦, Kowalewski Z.L., Łazarski A.♦, Szolc T., A review on biomaterials for orthopaedic surgery and traumatology: from past to present,
Materials, ISSN: 1996-1944, DOI: 10.3390/ma15103622, Vol.15, No.10, pp.3622-1-20, 2022 Abstract: The principal features essential for the success of an orthopaedic implant are its shape, dimensional accuracy, and adequate mechanical properties. Unlike other manufactured products, chemical stability and toxicity are of increased importance due to the need for biocompatibility over an implants life which could span several years. Thus, the combination of mechanical and biological properties determines the clinical usefulness of biomaterials in orthopaedic and musculoskeletal trauma surgery. Materials commonly used for these applications include stainless steel, cobalt-chromium and titanium alloys, ceramics, polyethylene, and poly(methyl methacrylate) (PMMA) bone cement. This study reviews the properties of commonly used materials and the advantages and disadvantages of each, with special emphasis on the sensitivity, toxicity, irritancy, and possible mutagenic and teratogenic capabilities. In addition, the production and final finishing processes of implants are discussed. Finally, potential directions for future implant development are discussed, with an emphasis on developing advanced personalised implants, according to a patient’s stature and physical requirements. Keywords: orthopaedic surgical procedures, biomaterials, implants, biocompatible materials, alloys, ceramic, polyethylene Affiliations:
Szczęsny G. | - | Medical University of Warsaw (PL) | Kopeć M. | - | IPPT PAN | Politis D.J. | - | Imperial College London (GB) | Kowalewski Z.L. | - | IPPT PAN | Łazarski A. | - | Medical University of Warsaw (PL) | Szolc T. | - | IPPT PAN |
| 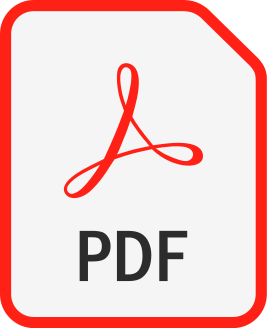 |
5. |
Kukla D., Kopeć M., Kowalewski Z.L., Politis D.J.♦, Jóźwiak S.♦, Senderowski C.♦, Thermal barrier stability and wear behavior of CVD deposited aluminide coatings for MAR 247 nickel superalloy,
Materials, ISSN: 1996-1944, DOI: 10.3390/ma13173863, Vol.13, No.17, pp.3863-1-11, 2020 Abstract: In this paper, aluminide coatings of various thicknesses and microstructural uniformity obtained using chemical vapor deposition (CVD) were studied in detail. The optimized CVD process parameters of 1040 °C for 12 h in a protective hydrogen atmosphere enabled the production of high density and porosity-free aluminide coatings. These coatings were characterized by beneficial mechanical features including thermal stability, wear resistance and good adhesion strength to MAR 247 nickel superalloy substrate. The microstructure of the coating was characterized through scanning electron microscopy (SEM), X-ray energy dispersive spectroscopy (EDS) and X-ray diffraction (XRD) analysis. Mechanical properties and wear resistance of aluminide coatings were examined using microhardness, scratch test and standardized wear tests, respectively. Intermetallic phases from the Ni-Al system at specific thicknesses (20-30 µm), and the chemical and phase composition were successfully evaluated at optimized CVD process parameters. The optimization of the CVD process was verified to offer high performance coating properties including improved heat, adhesion and abrasion resistance. Keywords: chemical vapor deposition, nickel alloys, coatings, X-ray analysis Affiliations:
Kukla D. | - | IPPT PAN | Kopeć M. | - | IPPT PAN | Kowalewski Z.L. | - | IPPT PAN | Politis D.J. | - | Imperial College London (GB) | Jóźwiak S. | - | Military University of Technology (PL) | Senderowski C. | - | other affiliation |
| 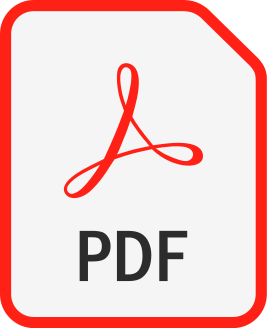 |
6. |
Wang K.♦, Kopeć M., Chang S.♦, Qu B.♦, Liu J.♦, Politis D.J.♦, Wang L.♦, Liu G.♦, Enhanced formability and forming efficiency for two-phase titanium alloys by fast light alloys stamping technology (FAST),
Materials & Design, ISSN: 0264-1275, DOI: 10.1016/j.matdes.2020.108948, pp.1-25, 2020 Abstract: During hot stamping of titanium alloys, insufficient forming temperatures result in limited material formability, whereas temperatures approaching the β phase transus also result in reduced formability due to phase transformation, grain coarsening and oxidation during the long-time heating. To solve this problem, Fast light Alloys Stamping Technology (FAST) is proposed in this paper, where fast heating is employed. Effects of heating parameters on the formability and post-form strength were studied by tensile tests. Forming of a wing stiffener was performed to validate this new process. Results show that microstructure of TC4 alloy after fast heating was in nonequilibrium state, which could enhance ductility significantly compared with the equilibrium state. When TC4 alloy was first heated to 950 °C with heating rate of 100 °C/s and then cooled to 700 °C, the elongation at 700 °C was more than 3 times that of a slow heating rate with soaking. Nano-scaled martensite with high dislocation density transformed from β phase was observed under fast heating condition. A complex shaped wing stiffener was successfully formed from TC4 titanium alloy in less than 70 s including heating, transfer and forming, and the post-form strength was almost the same with the initial blank. Keywords: titanium alloys, fast heating, hot stamping, formability, post-form strength Affiliations:
Wang K. | - | Imperial College London (GB) | Kopeć M. | - | IPPT PAN | Chang S. | - | Harbin Institiute of Technology (CN) | Qu B. | - | Harbin Institiute of Technology (CN) | Liu J. | - | Imperial College London (GB) | Politis D.J. | - | Imperial College London (GB) | Wang L. | - | Imperial College London (GB) | Liu G. | - | Harbin Institiute of Technology (CN) |
| 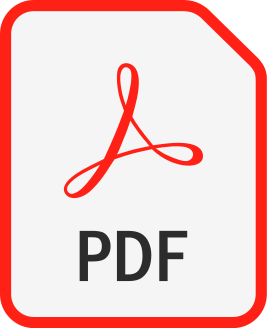 |
7. |
Kopeć M., Wang K.♦, Politis D.J.♦, Wang Y.♦, Wang L.♦, Lin J.♦, Formability and microstructure evolution mechanisms of Ti6Al4V alloy during a novel hot stamping process,
MATERIALS SCIENCE AND ENGINEERING A-STRUCTURAL MATERIALS PROPERTIES MICROSTRUCTURE AND PROCESSING, ISSN: 0921-5093, DOI: 10.1016/j.msea.2018.02.038, Vol.719, pp.72-81, 2018 Abstract: A novel hot stamping process for Ti6Al4V alloy using cold forming tools and a hot blank was presented in this paper. The formability of the material was studied through uniaxial tensile tests at temperatures ranging from 600 to 900 °C and strain rates ranging from 0.1 to 5 s-1. An elongation ranging from 30% to 60% could be achieved at temperatures ranging from 750 to 900°C respectively. The main microstructure evolution mechanisms varied with the deformation temperature, including recovery, phase transformation and recrystallization. The hardness of the material after deformation first decreased with the temperature due to recovery, and subsequently increased mainly due to the phase transformation. During the hot stamping tests, qualified parts could be formed successfully at heating temperatures ranging from 750 to 850°C. The forming failed at lower temperatures due to the limited ductility of the material. At temperatures higher than 900°C, extensive phase transformation of α to β occurred during the heating. During the transfer and forming, the temperature dropped significantly which led to the formation of transformed β, reduction of the formability and subsequent failure. The post-form hardness distribution demonstrated the same tendency as that after uniaxial tensile tests. Keywords: titanium alloys, Ti6Al4V, hot stamping, microstructure Affiliations:
Kopeć M. | - | IPPT PAN | Wang K. | - | Imperial College London (GB) | Politis D.J. | - | Imperial College London (GB) | Wang Y. | - | Beijing Aeronautical Manufacturing Technology Research Institute (CN) | Wang L. | - | Imperial College London (GB) | Lin J. | - | Imperial College London (GB) |
| 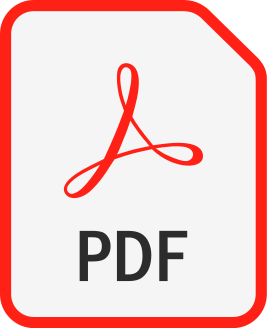 |