1. |
Labra C.♦, Rojek J., Oñate E.♦, Discrete/Finite Element Modelling of Rock Cutting with a TBM Disc Cutter,
Rock Mechanics and Rock Engineering, ISSN: 0723-2632, DOI: 10.1007/s00603-016-1133-7, Vol.50, pp.621-638, 2017 Abstract: This paper presents advanced computer simulation of rock cutting process typical for excavation works in civil engineering. Theoretical formulation of the hybrid discrete/finite element model has been presented. The discrete and finite element methods have been used in different subdomains of a rock sample according to expected material behaviour, the part which is fractured and damaged during cutting is discretized with the discrete elements while the other part is treated as a continuous body and it is modelled using the finite element method. In this way, an optimum model is created, enabling a proper representation of the physical phenomena during cutting and efficient numerical computation. The model has been applied to simulation of the laboratory test of rock cutting with a single TBM (tunnel boring machine) disc cutter. The micromechanical parameters have been determined using the dimensionless relationships between micro- and macroscopic parameters. A number of numerical simulations of the LCM test in the unrelieved and relieved cutting modes have been performed. Numerical results have been compared with available data from in-situ measurements in a real TBM as well as with the theoretical predictions showing quite a good agreement. The numerical model has provided a new insight into the cutting mechanism enabling us to investigate the stress and pressure distribution at the tool–rock interaction. Sensitivity analysis of rock cutting performed for different parameters including disc geometry, cutting velocity, disc penetration and spacing has shown that the presented numerical model is a suitable tool for the design and optimization of rock cutting process. Keywords: rock cutting, disc cutters, TBM, numerical model, discrete/finite element method, simulation Affiliations:
Labra C. | - | Particle Analytics, Ltd. (GB) | Rojek J. | - | IPPT PAN | Oñate E. | - | International Center for Numerical Methods in Engineering (ES) |
| 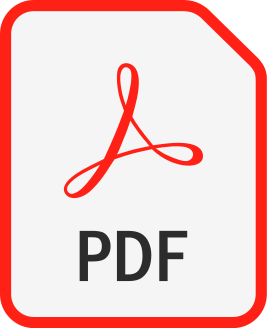 |
2. |
Oñate E.♦, Celigueta M.A.♦, Latorre S.♦, Casas G.♦, Rossi R.♦, Rojek J., Lagrangian analysis of multiscale particulate flows with the particle finite element method,
Computational Particle Mechanics, ISSN: 2196-4378, DOI: 10.1007/s40571-014-0012-9, Vol.1, pp.85-102, 2014 Abstract: We present a Lagrangian numerical technique for the analysis of flows incorporating physical particles of different sizes. The numerical approach is based on the particle finite element method (PFEM) which blends concepts from particle-based techniques and the FEM. The basis of the Lagrangian formulation for particulate flows and the procedure for modelling the motion of small and large particles that are submerged in the fluid are described in detail. The numerical technique for analysis of this type of multiscale particulate flows using a stabilized mixed velocity-pressure formulation and the PFEM is also presented. Examples of application of the PFEM to several particulate flows problems are given. Keywords: Lagrangian analysis, Multiscale particulate flows, Particle finite element method Affiliations:
Oñate E. | - | International Center for Numerical Methods in Engineering (ES) | Celigueta M.A. | - | International Center for Numerical Methods in Engineering (ES) | Latorre S. | - | International Center for Numerical Methods in Engineering (ES) | Casas G. | - | International Center for Numerical Methods in Engineering (ES) | Rossi R. | - | International Center for Numerical Methods in Engineering (ES) | Rojek J. | - | IPPT PAN |
| 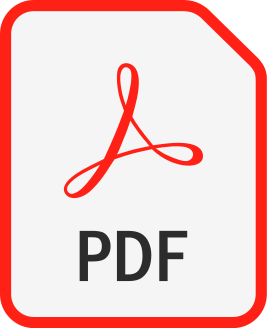 |
3. |
Rojek J., Labra C.♦, Su O.♦, Oñate E.♦, Comparative study of different discrete element models and evaluation of equivalent micromechanical parameters,
INTERNATIONAL JOURNAL OF SOLIDS AND STRUCTURES, ISSN: 0020-7683, DOI: 10.1016/j.ijsolstr.2012.02.032, Vol.49, pp.1497-1517, 2012 Abstract: Comparative studies of different discrete element models of a rock-type material are presented. The discrete element formulation employs spherical particles with the cohesive interaction model combining linear elastic behaviour with brittle failure. Numerical studies consisted in simulation of the uniaxial compression test. Two cylindrical specimens with particle size distributions yielding different degree of heterogeneity have been used. Macroscopic response produced by different discrete element models has been compared. The main difference between the compared models consists in the evaluation of micromechanical constitutive parameters. Two approaches are compared. In the first approach, the contact stiffness and strength parameters depend on the local particle size, while in the second approach, global uniform contact parameters are assumed for all the contacting pairs in function of average geometric measures characterizing the particle assembly. The size dependent contact parameters are calculated as functions of geometric parameters characterizing each contacting particle pair. As geometric scaling parameters, the arithmetic and harmonic means, as well as the minimum of the radii of two contacting particles are considered. Two different models with size dependent contact parameters are formulated. The performance of these models is compared with that of the discrete element model with global uniform contact parameters. Equivalence between the models with size dependent and uniform contact parameters has been checked. In search of this equivalence, different methods of evaluation of global uniform parameters have been studied. The contact stiffness has been evaluated in terms of the average radius of the particle assembly or in terms of the averages of the arithmetic and harmonic means of the contact pair radii, the geometric parameters used in the evaluation of the contact stiffness in the size-dependent models. The uniform contact strengths have been determined as functions of the averages of radii squares, squares of arithmetic radii means or squares of minimum radii of the contacting pairs.
For the more homogenous specimen, the models with local size dependent parameters and models with global uniform parameters give similar response. The models with uniform parameters evaluated according to the averages of the geometric parameters used in the evaluation of local parameters ensure better agreement with the respective models with size-dependent parameters than the models with uniform parameters evaluated according to the particle radii. Simulations using the more heterogenous specimen reveal differences between the considered models. There are significant differences in stress–strain curves as well as in the failure pattern. The models with local size-dependent parameters are more sensitive to the change of heterogeneity than the model with global uniform parameters. Keywords: Discrete element method, Brittle, Compression, Contact, Heterogeneity, Modelling Affiliations:
Rojek J. | - | IPPT PAN | Labra C. | - | Particle Analytics, Ltd. (GB) | Su O. | - | other affiliation | Oñate E. | - | International Center for Numerical Methods in Engineering (ES) |
| 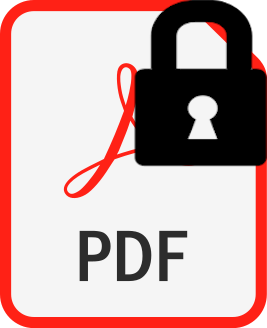 |
4. |
Rojek J., Oñate E.♦, Labra C.♦, Kargl H.♦, Discrete element simulation of rock cutting,
INTERNATIONAL JOURNAL OF ROCK MECHANICS AND MINING SCIENCES, ISSN: 1365-1609, DOI: 10.1016/j.ijrmms.2011.06.003, Vol.48, pp.996-1010, 2011 Abstract: This paper presents numerical modelling of rock cutting processes. The model consists of a tool–rock system. The rock is modelled using the discrete element method, which is suitable to study problems of multiple material fracturing such as those involved in rock cutting. Both 2D and 3D models are considered in this work. The paper presents a brief overview of the theoretical formulation and calibration of the discrete element model by a methodology combining the dimensional analysis with simulation of the unconfined compressive strength (UCS) and indirect tension (Brazilian) tests. The rock cutting process with roadheader picks, which is typical for underground excavation, has been simulated. The results of the 2D and 3D analyses have been compared with one another, and numerical results have been compared with the available experimental data. Keywords: Rock cutting, Roadheader, Discrete element method, Simulation, Numerical model Affiliations:
Rojek J. | - | IPPT PAN | Oñate E. | - | International Center for Numerical Methods in Engineering (ES) | Labra C. | - | Particle Analytics, Ltd. (GB) | Kargl H. | - | Sandvik Mining and Construction GmbH (AT) |
| 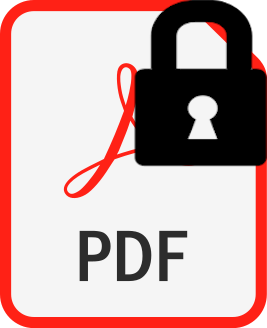 |
5. |
Labra C.♦, Rojek J., Oñate E.♦, Adaptive discrete/finite element coupling for rock cutting processes simulations,
Discrete Element Methods. Simulations of Discontinua: Theory and Applications, pp.428-433, 2010 | 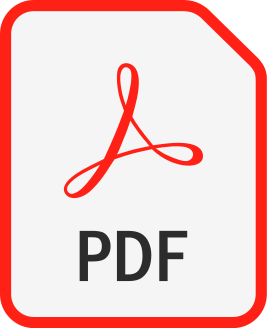 |
6. |
Rojek J., Labra C.♦, Oñate E.♦, Discrete element simulation of rock cutting with evaluation of tool wear,
Discrete Element Methods. Simulations of Discontinua: Theory and Applications, pp.388-393, 2010 | 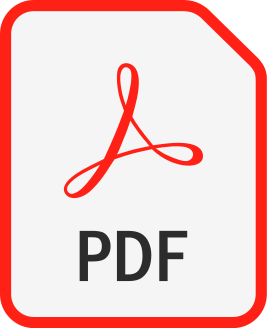 |
7. |
Labra C.♦, Rojek J., Oñate E.♦, Zarate F.♦, Advances in discrete element modelling of underground excavations,
ACTA GEOTECHNICA, ISSN: 1861-1125, DOI: 10.1007/s11440-008-0071-2, Vol.3, No.4, pp.317-322, 2008 Abstract: The paper presents advances in the discrete element modelling of underground excavation processes extending modelling possibilities as well as increasing computational efficiency. Efficient numerical models have been obtained using techniques of parallel computing and coupling the discrete element method with finite element method. The discrete element algorithm has been applied to simulation of different excavation processes, using different tools, TBMs and roadheaders. Numerical examples of tunnelling process are included in the paper, showing results in the form of rock failure, damage in the material, cutting forces and tool wear. Efficiency of the code for solving large scale geomechanical problems is also shown. Keywords: Coupling, Discrete element method, Finite element method, Parallel computation, Tunnelling Affiliations:
Labra C. | - | Particle Analytics, Ltd. (GB) | Rojek J. | - | IPPT PAN | Oñate E. | - | International Center for Numerical Methods in Engineering (ES) | Zarate F. | - | International Center for Numerical Methods in Engineering (ES) |
| 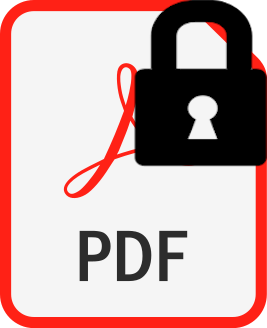 |
8. |
Rojek J., Oñate E.♦, Taylor R.L.♦, CBS-based stabilization in explicit solid dynamics,
INTERNATIONAL JOURNAL FOR NUMERICAL METHODS IN ENGINEERING, ISSN: 0029-5981, DOI: 10.1002/nme.1689, Vol.66, pp.1547-1568, 2006 | 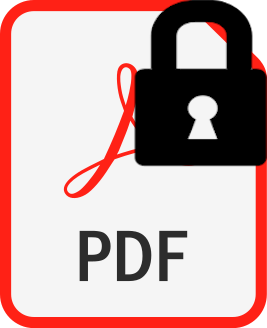 |
9. |
Oñate E.♦, Rojek J.♦, Chiumenti M.♦, Idelsohn S.R.♦, Del Pin F.♦, Aubry R.♦, Advances in stabilized finite element and particle methods for bulk forming processes,
COMPUTER METHODS IN APPLIED MECHANICS AND ENGINEERING, ISSN: 0045-7825, DOI: 10.1016/j.cma.2004.10.018, Vol.195, pp.6750-6777, 2006 Abstract: The paper describes some recent developments in finite element and particle methods for analysis of a wide range of bulk forming processes. The developments include new stabilized linear triangles and tetrahedra using finite calculus and a new procedure combining particle methods and finite element methods. Applications of the new numerical methods to casting, forging and other bulk metal forming problems and mixing processes are shown. Keywords: Bulk forming processes, Stabilized finite element method, Particle method, Particle finite element method, Mixing processes Affiliations:
Oñate E. | - | International Center for Numerical Methods in Engineering (ES) | Rojek J. | - | other affiliation | Chiumenti M. | - | International Center for Numerical Methods in Engineering (ES) | Idelsohn S.R. | - | International Center for Numerical Methods in Engineering (ES) | Del Pin F. | - | International Center for Numerical Methods in Engineering (ES) | Aubry R. | - | International Center for Numerical Methods in Engineering (ES) |
| 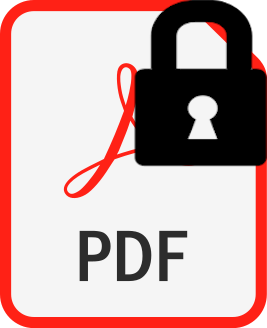 |
10. |
Rojek J., Zienkiewicz OC.♦, Onate E.♦, Postek E., Advances in FE explicit formulation for simulation of metalforming processes,
JOURNAL OF MATERIALS PROCESSING TECHNOLOGY, ISSN: 0924-0136, DOI: 10.1016/S0924-0136(01)00894-9, No.119, pp.41-47, 2001 Abstract: This paper presents some advances of finite element explicit formulation for simulation of metal forming processes. Because of their computational efficiency, finite element programs based on the explicit dynamic formulation proved to be a very attractive tool for the simulation of metal forming processes. The use of explicit programs in the sheet forming simulation is quite common, the possibilities of these codes in bulk forming simulation in our opinion are still not exploited sufficiently. In our paper, we will consider aspects of bulk forming simulation. We will present new formulations and algorithms developed for bulk metal forming within the explicit formulation. An extension of a finite element code for the thermomechanical coupled analysis is discussed. A new thermomechanical constitutive model developed by the authors and implemented in the program is presented. A new formulation based on the so-called split algorithm allows us to use linear triangular and tetrahedral elements in the analysis of large plastic deformations characteristic to forming processes. Linear triangles and tetrahedra have many advantages over quadrilateral and hexahedral elements. Linear triangles and tetrahedra based on the standard formulations exhibit volumetric locking and are not suitable for large plastic strain simulation. The new formulation allows to overcome this difficulty. New formulations and algorithms have been implemented in the finite element code Stampack developed at the International Centre for Numerical Methods in Engineering in Barcelona. Numerical examples illustrate some of the possibilities of the finite element code developed and validate new algorithms. Keywords: Explicit formulation, Forming simulation, Split algorithm Affiliations:
Rojek J. | - | IPPT PAN | Zienkiewicz OC. | - | other affiliation | Onate E. | - | International Center for Numerical Methods in Engineering (ES) | Postek E. | - | IPPT PAN |
| 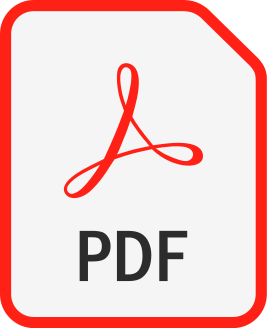 |
11. |
Rojek J., Onate E.♦, Postek E., Application of explicit FE codes to simulation of sheet and bulk metal forming processes,
JOURNAL OF MATERIALS PROCESSING TECHNOLOGY, ISSN: 0924-0136, DOI: 10.1016/S0924-0136(98)00169-1, No.80-81, pp.620-627, 1998 Abstract: This paper presents the application of an explicit dynamic finite element code for simulation of metal forming processes, of both sheet and bulk forming. The experiences reported here have been gained during the development and use of our own explicit program Stampack. An original formulation of a triangular shell element without rotational degrees of freedom is reviewed combining the explicit sheet forming simulation with the implicit springback analysis as well as the parallelization of the explicit program described. An extension of a finite element code for coupled thermomechanical analysis is discussed. A new thermomechanical constitutive model developed by the authors and implemented in the program is presented. Numerical examples illustrate some of the possibilities of the finite element code developed. Keywords: Metal forming, Sheet stamping, Finite element simulation, Explicit dynamic analysis, Thermomechanical analysis Affiliations:
Rojek J. | - | IPPT PAN | Onate E. | - | International Center for Numerical Methods in Engineering (ES) | Postek E. | - | IPPT PAN |
| 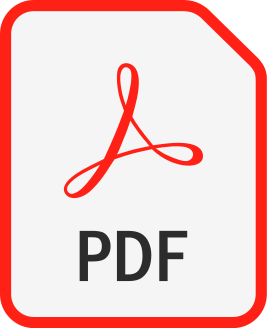 |