1. |
Jia B.♦, Rusinek A., Pesci R.♦, Bahi S.♦, Bernier R.♦, Thermo-viscoplastic behavior of 304 austenitic stainless steel at various strain rates and temperatures: testing, modeling and validation,
INTERNATIONAL JOURNAL OF MECHANICAL SCIENCES, ISSN: 0020-7403, DOI: 10.1016/j.ijmecsci.2019.105356, Vol.170, pp.105356-1-18, 2020 Abstract: This paper presents a systematic study of the thermo-viscoplastic behavior of a 304 austenitic stainless steel (ASS). The experiments were conducted over a wide range of strain rates (10^−3 s^−1 to 3270 s^−1) and temperatures (-163°C to 172°C), for which the deformation behavior of 304 ASS becomes more complex due to the strain-induced martensitic transformation (SIMT) effect. Dynamic tests at low/elevated temperatures were conducted using the Hopkinson technique coupled with a cooling device/heating furnace, and temperature distribution within the specimen was verified to be uniform. Experimental results showed that the strain hardening rate of 304 ASS was strongly affected by SIMT effect. For quasi-static tests (10^−3 s^−1 to 1 s^−1) at low temperatures (-163°C to -20°C), the stress-strain relations exhibited an S-shape and a second strain hardening phenomenon. The strain rate sensitivity and temperature sensitivity of 304 ASS were also different from metallic materials deformed by dislocation glide. Several unexpected phenomena including the negative strain rate sensitivity and the changing temperature sensitivity from quasi-static to dynamic tests were observed. Based on experimental results, an extension of the Rusinek-Klepaczko (RK) model considering SIMT effect was used to simulate the deformation behavior of 304 ASS: it predicted flow stress curves of 304 ASS above -60°C correctly. In addition, to validate the extended RK model and the identified model parameters, numerical simulations of ballistic impact tests of 304 ASS plates at various temperatures were carried out, showing a good agreement with experiments. Keywords: 304 austenitic stainless steel, strain rate sensitivity, temperature sensitivity, constitutive model, ballistic impact test Affiliations:
Jia B. | - | École nationale supérieure d'arts et métiers (FR) | Rusinek A. | - | IPPT PAN | Pesci R. | - | École nationale supérieure d'arts et métiers (FR) | Bahi S. | - | Lorraine University (FR) | Bernier R. | - | National Engineering School of Metz (ENIM) (FR) |
| 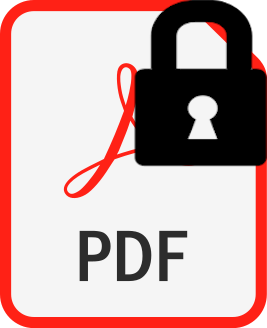 |
2. |
Massaq A.♦, Rusinek A., Klosak M.♦, Bahi S.♦, Arias A.♦, Strain rate effect on the mechanical behavior of polyamide composites under compression loading,
COMPOSITE STRUCTURES, ISSN: 0263-8223, DOI: 10.1016/j.compstruct.2019.01.101, Vol.214, pp.114-122, 2019 Abstract: This paper presents an experimental study on the effect of strain rate on the compressive behavior of polyamide composites. Contrary to thermoset woven reinforced composites, thermoplastic woven reinforced composites have always received less interest despite its excellent damage and impact resistances. In this context, this work aims to study the behavior of fiber reinforced thermoplastic composites submitted to high strain rate in compression. The tested material is a thermoplastic composite made of armor tissue of equilibrate glass fiber and the matrix is composed of Polyamide 6 (PA6/Glass). The material is prepared with the fibers woven in 0/90 direction. The compressive mechanical response of PA6/Glass composite was determined in the transverse and longitudinal fibers directions at quasi-static and high strain rates. The hydraulic machine and Split Hopkinson Pressure Bar experiments were conducted to determine the dynamic and quasi static compressive deformation and fracture of the PA6/Glass at strain rates from 10^−5 s^−1 to 1 s^−1 and 100 s^−1 to 2500 s^−1, respectively. In this work, the main goals were to determine the strain rate effect on: elastic modulus, failure stress and failure energy as a function of the loading direction. The strain rate sensitivity of the failure stress level and failure energy were observed. In addition, the failure mechanism was characterized by examining the fracture surfaces using the scanning electron microscopy (SEM) method. In quasi-static conditions of loading, the material reached its capacity due to the formation of shear bands, that concerned all three tested compression directions. In dynamics, the failure took place by shearing followed by delamination. In case of dynamic loading in the direction perpendicular to fibers, the observations made by SEM showed that the failure of the composite had a fragile nature. Keywords: woven composite, dynamic behaviour, dynamic fracture, Split Hopkinson pressure bar, failure energy, anisotropy, strain rate Affiliations:
Massaq A. | - | Caddi Ayad University (MA) | Rusinek A. | - | IPPT PAN | Klosak M. | - | other affiliation | Bahi S. | - | Lorraine University (FR) | Arias A. | - | other affiliation |
| 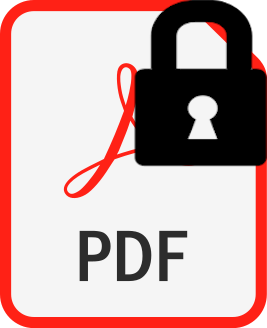 |