1. |
Ryś M., Kursa M., Petryk H., Spontaneous emergence of deformation bands in single-crystal plasticity simulations at small strain,
COMPUTATIONAL MECHANICS, ISSN: 0178-7675, DOI: 10.1007/s00466-024-02519-8, pp.1-28, 2024 Abstract: In metal single crystals, the observed formation of deformation banding pattern has been explained by greater latent hardening of slip systems than their self-hardening, which promotes spatial segregation of plastic slips and lamination towards single-slip domains. Numerical studies focusing on the formation of deformation bands usually involved initial imperfections, boundary-induced heterogeneity, or the postulate of minimal global energy expenditure which additionally promoted non-uniformity of deformation. This article analyses the case when no such mechanism enforcing locally non-uniform deformation is implemented in the finite element (FE) method, while the global system of equations of incremental equilibrium is solved in a standard way. The new finding in this paper is that the deformation banding pattern can appear spontaneously in FE simulations of homogeneous single crystals even in the absence of any mechanism favouring deformation banding in the numerical code. This has been demonstrated in several examples in the small strain formalism using a plane-strain model in which the twelve fcc slip systems are reduced to three effective plastic slip mechanisms. Incremental slips are determined at the Gauss-point level either by incremental work minimization in the rate-independent case or by rate-dependent regularization. In the rate-independent approach, the trust-region algorithm is developed for the selection of active slip systems with the help of the augmented Lagrangian method. Conditions under which a banding pattern appears spontaneously or is suppressed are discussed. In particular, a critical rate sensitivity exponent is identified. Keywords: Crystal plasticity, Small strain, Slip-system selection, Path instability, Microstructure formation, Finite element method Affiliations:
Ryś M. | - | IPPT PAN | Kursa M. | - | IPPT PAN | Petryk H. | - | IPPT PAN |
| 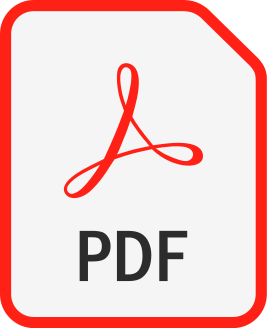 |
2. |
Rezaee Hajidehi M., Ryś M., Modeling the interaction between instabilities and functional degradation in shape memory alloys,
INTERNATIONAL JOURNAL OF MECHANICAL SCIENCES, ISSN: 0020-7403, DOI: 10.1016/j.ijmecsci.2024.109569, Vol.282, pp.109569-1-16, 2024 Abstract: Localization of the stress-induced martensitic phase transformation plays an important role in the fatigue behavior of shape memory alloys (SMAs). The phenomenon of return-point memory that is observed during the subloop deformation of a partially-transformed SMA is a clear manifestation of the interaction between localized phase transformation and degradation of the functional properties. The present study aims to demonstrate this structure–material interaction in the modeling of return-point memory. It seems that this crucial aspect has been overlooked in previous modeling studies. For this purpose, we developed a gradient- enhanced model of pseudoelasticity that incorporates the degradation of functional properties in its constitutive description. The model is employed to reproduce the hierarchical return-point memory in a pseudoelastic NiTi wire under isothermal uniaxial tension with nested subloops. Additionally, a detailed analysis is carried out for NiTi strip with a more complex transformation pattern. Our study highlights the subtle morphological changes of phase transformation under different loading scenarios and the resulting implications for return-point memory. Keywords: Shape memory alloys,Phase transformation,Functional degradation ,Propagating instabilities,Subloop deformation,Modeling Affiliations:
Rezaee Hajidehi M. | - | IPPT PAN | Ryś M. | - | IPPT PAN |
| 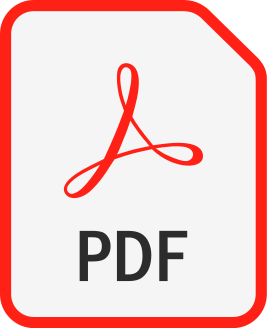 |
3. |
Kucharski S. J., Maj M., Ryś M., Petryk H., Size effects in spherical indentation of single crystal copper,
INTERNATIONAL JOURNAL OF MECHANICAL SCIENCES, ISSN: 0020-7403, DOI: 10.1016/j.ijmecsci.2024.109138, Vol.272, pp.1-15, 2024 Keywords: Hardness, Lattice rotation, Plasticity, Strain Gradient Affiliations:
Kucharski S. J. | - | IPPT PAN | Maj M. | - | IPPT PAN | Ryś M. | - | IPPT PAN | Petryk H. | - | IPPT PAN |
| 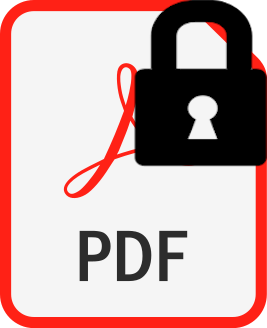 |
4. |
Ryś M., Stupkiewicz S., Petryk H., Micropolar regularization of crystal plasticity with the gradient-enhanced incremental hardening law,
International Journal of Plasticity, ISSN: 0749-6419, DOI: 10.1016/j.ijplas.2022.103355, Vol.156, pp.103355-1-20, 2022 Abstract: A new model of gradient crystal plasticity is developed in which the incompatibility of plastic deformation field is simultaneously included in two different ways. The first one is well known and incorporates the gradient effect of accumulated rotation of the crystallographic lattice on the kinematic hardening in the Cosserat crystal plasticity model. The second way incorporates the effect of the current incompatibility of lattice spin on the total dislocation density rate, resulting in an additional isotropic hardening term in the gradient-enhanced hardening law. The latter effect involves a natural length scale that is fully determined in terms of standard quantities of a non-gradient hardening law and evolves during plastic deformation. The relative significance of the two effects depends on the values of material parameters, which is demonstrated by the results of calculations of 1D and 3D examples for a Cu single crystal. If the second effect is predominant, then the Cosserat formulation provides only a regularization, and then the model can be used to predict size effects. This is shown by 3D simulations of the size effect in spherical indentation of a copper single crystal. Since the gradient-enhanced hardening law does not involve any adjustable parameter, the obtained agreement of the model prediction with the experimental indentation size effect on hardness can be regarded as surprisingly good. Keywords: gradient plasticity, crystal plasticity, Cosserat continuum, length scale, indentation size effect, 3D model Affiliations:
Ryś M. | - | IPPT PAN | Stupkiewicz S. | - | IPPT PAN | Petryk H. | - | IPPT PAN |
| 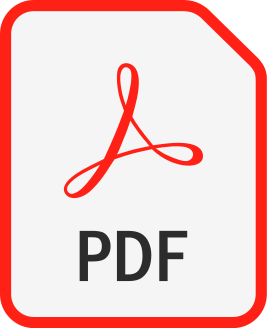 |
5. |
Ryś M., Forest S.♦, Petryk H., A micromorphic crystal plasticity model with the gradient-enhanced incremental hardening law,
International Journal of Plasticity, ISSN: 0749-6419, DOI: 10.1016/j.ijplas.2019.102655, Vol.128, pp.102655-1-21, 2020 Abstract: A model of crystal plasticity is developed in which the effects of plastic flow non-uniformity are described through the full dislocation density tensor. The micromorphic approach is used in which the dislocation density tensor is represented by the curl of an independent constitutive variable called microdeformation. The microdeformation tensor is enforced by an energetic penalty term to be close to the actual plastic distortion tensor. The curl of microdeformation tensor enters the constitutive model in two independent but complementary ways. First, it is an argument of the free energy density function, which describes the kinematic-type hardening in cyclic non-uniform deformation. Second, its rate influences the rates of critical resolved shear stresses, which corresponds to additional isotropic hardening caused by incompatibility of the plastic flow rate. The latter effect, missing in the standard slip-system hardening rule, is described in a simple manner that does not require any extra parameter in comparison to the non-gradient theory. In the proposed model there are two independent internal length scales whose interplay is examined by means of 1D and 2D numerical examples of plastic shearing of a single crystal. Keywords: gradient theory, crystal plasticity, dissipation, length scale, cyclic deformation, numerical regularization Affiliations:
Ryś M. | - | IPPT PAN | Forest S. | - | other affiliation | Petryk H. | - | IPPT PAN |
| 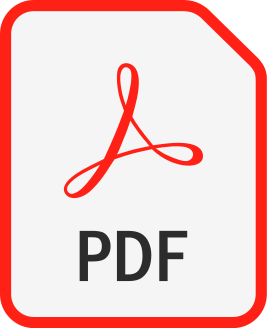 |
6. |
Ryś M., Egner H.♦, Energy equivalence based constitutive model of austenitic stainless steel at cryogenic temperatures,
INTERNATIONAL JOURNAL OF SOLIDS AND STRUCTURES, ISSN: 0020-7683, DOI: 10.1016/j.ijsolstr.2018.12.028, Vol.164, pp.52-65, 2019 Abstract: In the present work the constitutive model of 316L and 304 stainless steel subjected to mechanical loading at cryogenic temperatures is derived. Three main coupled dissipative phenomena taking place in the material: plastic flow, plastic strain-induced transformation from the primary phase (γ) to the secondary phase (α′), and evolution of micro-damage are considered using a thermodynamically consistent framework. The approach based on total energy equivalence, originally developed for damaged materials, is here extended to modelling not only damage but also phase transformation, in a consistent manner. The proposed model is implemented numerically and validated by means of parametric studies, and by comparison with the experimental results. Very good qualitative and quantitative results are obtained. Keywords: constitutive modelling, plasticity, damage, phase transformation, cryogenic temperatures Affiliations:
Ryś M. | - | IPPT PAN | Egner H. | - | Cracow University of Technology (PL) |
| 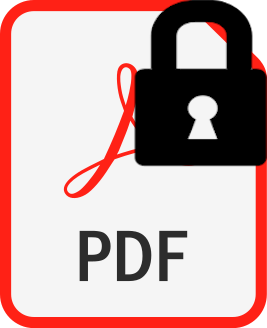 |
7. |
Ryś M., Petryk H., Gradient crystal plasticity models with a natural length scale in the hardening law,
International Journal of Plasticity, ISSN: 0749-6419, DOI: 10.1016/j.ijplas.2018.07.015, Vol.111, pp.168-187, 2018 Abstract: A class of crystal plasticity models based on the concept of microforces conjugate to slip-rate gradients is examined in the small strain framework. As an extension of the usual formulation, slip-rate gradients are introduced here into the incremental hardening law, including in this way a natural internal length scale derived recently in a closed form from relationships of the physically-based dislocation theory of plasticity. The condition for plastic flow on a crystallographic slip system involves other length scales, associated with the second-order gradients of slip and slip rate in energetic and dissipative terms, respectively. The interplay between the length-scales of physically different origin is illustrated by the examples of monotonic and cyclic deformation of one- and two-dimensional models of Cu single crystals with boundary constraints imposed on plastic slips. It is shown that selected earlier results are reproduced accurately if one or another length scale ceases to play an essential role. For cyclic deformations, the effects of the energetic length scale in the flow condition and of the natural length scale in the incremental hardening law can both be significant at the micron scale. Keywords: Gradient theory, Dissipation, Crystal plasticity, Length scale, Cyclic deformation Affiliations:
Ryś M. | - | IPPT PAN | Petryk H. | - | IPPT PAN |
| 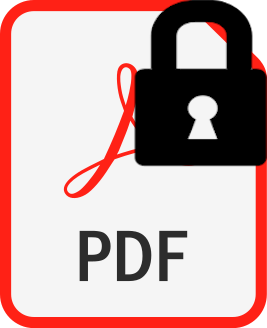 |
8. |
Ryś M., Skoczeń B.♦, Coupled constitutive model of damage affected two-phase continuum,
MECHANICS OF MATERIALS, ISSN: 0167-6636, DOI: 10.1016/j.mechmat.2017.08.015, Vol.115, pp.1-15, 2017 Abstract: A broad class of metastable materials, including selected alloys (e.g. stainless steels) used for applications in radiation environment (particle accelerators), is characterized by simultaneous occurrence of the plastic strain driven phase transformation and evolution of nano/micro damage. Plastic flow in such materials is usually accompanied by dynamic evolution of microstructure, resulting from the strain induced fcc-bcc phase transformation. Two-phase continuum is composed of austenitic matrix (fcc) and martensitic inclusions (bcc), represented by type Eshelby ellipsoidal entities embedded in ductile matrix. The matrix remains entirely plastic, and contains micro-cracks and micro-voids representing ductile damage. On the other hand, the inclusions are characterized by much higher yield stress and their behavior is generally brittle. Thus, brittle damage develops in the inclusions. The origin of damage is mechanical (manufacturing and load induced defects), and related to the source of radiation (primary or secondary particles flux). Among the lattice defects induced by radiation, the clusters of nano/micro voids are accounted for. The constitutive model takes into account the evolution of mechanically and radiation induced nano/micro damage in the presence of microstructure evolution, reflected by the plastic strain driven dynamic change of proportions between the matrix and the inclusions. The model is multiscale since the processes that occur at different scales (micro, meso, macro) are addressed, and coupled, since both phenomena: phase transformation and damage are described by coupled equations. Application to irradiated corrugated shells, components of thermo-mechanical compensation systems, are presented. Affiliations:
Ryś M. | - | IPPT PAN | Skoczeń B. | - | Cracow University of Technology (PL) |
| 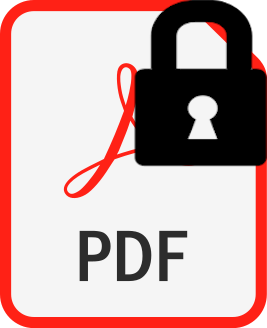 |
9. |
Egner H.♦, Ryś M., Total energy equivalence in constitutive modeling of multidissipative materials,
INTERNATIONAL JOURNAL OF DAMAGE MECHANICS, ISSN: 1056-7895, DOI: 10.1177/1056789516679496, Vol.26, No.3, pp.417-446, 2017 Abstract: In the present work, the total energy equivalence hypothesis was applied in constitutive modeling of engineering materials. The approach originally developed for damaged materials, was extended to modeling not only damage but also other dissipative phenomena, like phase transformation, in a consistent manner. The proposed model was examined by means of parametric studies to show its ability to reflect different experimentally observed features of real materials. Keywords: Constitutive modeling, dissipative material, plasticity, damage, phase transformation Affiliations:
Egner H. | - | Cracow University of Technology (PL) | Ryś M. | - | IPPT PAN |
| 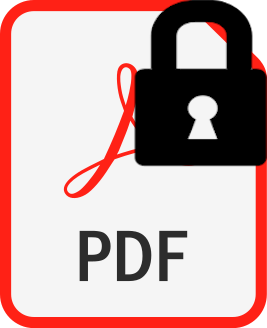 |
10. |
Ortwein R.♦, Ryś M.♦, Skoczeń B.♦, Damage evolution in a stainless steel bar undergoing phase transformation under torsion at cryogenic temperatures,
INTERNATIONAL JOURNAL OF DAMAGE MECHANICS, ISSN: 1056-7895, DOI: 10.1177/1056789516656746, Vol.25, No.7, pp.967-1016, 2016 Abstract: Phase transformation driven by plastic strains is commonly observed in austenitic stainless steels. In the present paper, this phenomenon is addressed in connection with damage evolution. A three-dimensional constitutive model has been derived, and scalar variables for damage and the volume fraction of the transformed phase were used. The model was solved using Abaqus UMAT user defined procedure, as well as by means of simplified one-dimensional approach for a twisted circular bar. Large experimental campaign of tests was performed, including martensite content measurements within the cross-section and on the surface of the bar during monotonic and cyclic loading. Based on the residual angle of twist, damage variable was calculated. The global response of torque versus the angle of twist was measured as well. Comparison between the experimental results and the results obtained from the simplified one-dimensional approach and from the full three-dimensional approach are presented. It turns out that one-dimensional formulation agrees quite well with full three-dimensional model. Thus, much simpler approach can effectively be used. Moreover, experimental results agree well in terms of the martensite content evolution and relation: torque versus the angle of twist. Damage evolution is correctly predicted in terms of the maximum values. Lastly, the evolution of damage during cyclic torsion is discussed, as the experimental results indicate rather surprising effect of unloading modulus recovery after each reversion of twist direction Keywords: Cryogenic temperatures, plastic strain-induced phase transformation, torsion, damage evolution, constitutive model, martensite, austenitic stainless steels Affiliations:
Ortwein R. | - | CERN (CH) | Ryś M. | - | other affiliation | Skoczeń B. | - | Cracow University of Technology (PL) |
| 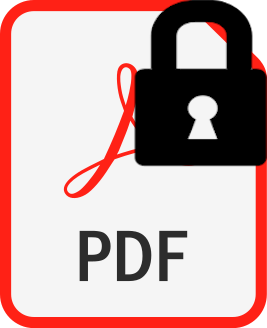 |
11. |
Ryś M.♦, Constitutive Modelling of Damage Evolution and Martensitic Transformation in 316L Stainless Steel,
ACTA MECHANICA ET AUTOMATICA, ISSN: 1898-4088, DOI: 10.1515/ama-2016-0020, Vol.10, No.2, pp.125-132, 2016 Abstract: n this work, the constitutive model, derived with the use of thermodynamic of irreversible processes framework is presented. The model is derived under the assumption of small strains. Plastic strain induced martensitic phase transformation is considered in the austenitic matrix where the volume fraction of the martensite is reflected by a scalar parameter. The austenitic matrix is assumed as the elastic-plastic material and martensitic phase is assumed as randomly distributed and randomly oriented inclusions. Both phases are affected by damage evolution but there is no distinction in the model between damage in austenite and martensite Keywords: Constitutive Modelling, Dissipative Materials, Phase Transformation, Damage Evolution Affiliations:
Ryś M. | - | other affiliation |
| 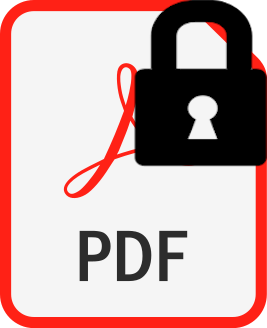 |
12. |
Egner H.♦, Skoczeń B.♦, Ryś M.♦, Constitutive and numerical modeling of coupled dissipative phenomena in 316L stainless steel at cryogenic temperatures,
International Journal of Plasticity, ISSN: 0749-6419, DOI: 10.1016/j.ijplas.2014.08.005, Vol.64, pp.113-133, 2015 Abstract: A macroscopic material model for simulation of coupled dissipative phenomena taking place in FCC metals and alloys at low temperatures is developed. Three phenomena: plastic flow, plastic strain induced transformation from the parent phase ( to the secondary phase ( and evolution of micro-damage are studied using a thermodynamically consistent framework. The experimental results indicate a correlation between decreasing damage rate and increasing martensite content. For the micro-damage evolution in the parent austenitic phase a generalization of the classical isotropic ductile damage concept to anisotropic model has been adopted. The kinetics of damage evolution is based on the accumulated plastic strain as a driving force of ductile damage. On the other hand, the deterioration of the brittle secondary phase is described by the damage evolution equation expressed in the form of tensorial function, where the damage tensor depends directly on the stresses applied. This formulation accounts both for the isotropic damage, and for the oriented damage due to different effects of the stress tensor. Total amount of damage in the representative volume element is obtained via the linear rule of mixture. The results obtained in the course of numerical simulations fit well the experimental data Keywords: B. Constitutive behavior, A. Microcracking, A. Phase transformation, Cryogenic temperature Affiliations:
Egner H. | - | Cracow University of Technology (PL) | Skoczeń B. | - | Cracow University of Technology (PL) | Ryś M. | - | other affiliation |
| 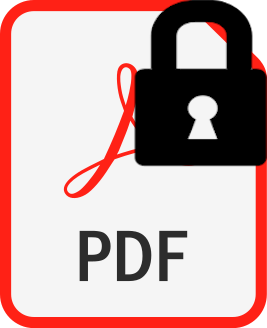 |