1. |
Rogala M.♦, Ferdynus M.♦, Kopeć M., The effect of multilevel spherical triggers on the crashworthiness capacity of thin-walled structures,
Aerospace Science and Technology, ISSN: 1270-9638, DOI: 10.1016/j.ast.2025.110299, Vol.163, No.110299, pp.1-18, 2025 Abstract: Progressive dynamic crushing remains a significant focus in contemporary research aimed at developing and optimizing energy-absorbing structures. This study investigates thin-walled passive energy absorbers featuring multi-level crush initiators in the form of spherical embossments. The experimental setup involved aluminum columns subjected to an impact energy of 1700 J. These columns were designed with varying numbers of embossment levels. Key parameters of the spherical embossments included diameters ranging from 12 to 36 mm and depths from 1.2 to 4.8 mm. Dynamic impact tests were conducted using an Instron Ceast 9350 HES drop tower, with deformation behavior captured via a Phantom Miro M310 high-speed camera. Complementary finite element analyses were also performed to obtain force-displacement responses and crushing efficiency indicators, enabling a comparative assessment of structural performance based on different crush initiator configurations. The results demonstrate that spherical embossments enhance the stability of the crushing process by reducing the peak crushing force. Furthermore, incorporating additional embossment levels increases the mean crushing force and improves the overall energy absorption efficiency of the passive energy absorber. Keywords: Multi-level trigger , Spherical embossment, Crashworthiness Affiliations:
Rogala M. | - | other affiliation | Ferdynus M. | - | other affiliation | Kopeć M. | - | IPPT PAN |
| 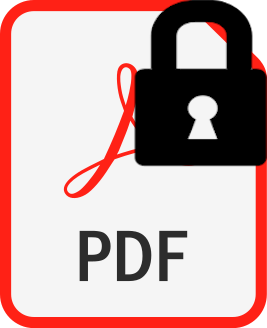 |
2. |
Tytko G.♦, Adamczyk-Habrajska M.♦, Linke Y.♦, Liu Z.♦, Kopeć M., High frequency eddy current method in inspection of aluminide coatings integrity after simulating service loads,
MEASUREMENT, ISSN: 0263-2241, DOI: 10.1016/j.measurement.2025.117356, Vol.252, No.117356, pp.1-11, 2025 Abstract: This study investigates the use of high-frequency eddy current testing (ECT) to assess the structural integrity of aluminide coatings on MAR-M247 nickel superalloy under simulated fatigue conditions. Aluminide coatings, deposited via chemical vapor deposition at thicknesses of 20 µm and 40 µm, were tested using custom-designed probes optimized for defect detection. Results demonstrate that substrate grain structure and coating thickness significantly influence coating durability, with fine-grain substrates exhibiting the least resistance changes and greatest fatigue tolerance. Eddy current signal variations correlated with microstructural changes, enabling detection of damage otherwise invisible to traditional methods. These findings establish ECT as a precise, non-destructive approach for monitoring aluminide coatings in critical applications. Keywords: Nickel alloys, Aluminide coating, Non-destructive testing, Eddy current testing Affiliations:
Tytko G. | - | other affiliation | Adamczyk-Habrajska M. | - | other affiliation | Linke Y. | - | Warsaw University of Technology (PL) | Liu Z. | - | other affiliation | Kopeć M. | - | IPPT PAN |
| 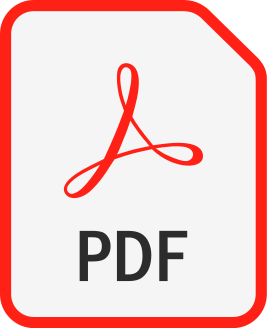 |
3. |
Macek W.♦, Sitek R.♦, Podulka P.♦, Lesiuk G.♦, Zhu S.♦, Liu X.♦, Kopeć M., Fractography of Haynes 282 alloy manufactured by DMLS after tensile and HCF,
Journal of Constructional Steel Research, ISSN: 1873-5983, DOI: 10.1016/j.jcsr.2025.109623, Vol.232, No.109623, pp.1-12, 2025 Abstract: In this paper, the fracture surface topography of additively manufactured Haynes 282 alloy subjected to tensile and high-cycle fatigue loading was investigated. Haynes 282 alloy bars were printed in three different directions relative to the base plate (0°, 45°, and 90°) via Direct Metal Laser Sintering (DMLS) under an argon protective atmosphere. The specimens were subjected to monotonic tensile loading and fatigue testing under load control using full tension and compression cyclic loading (R = −1) in the range of stress amplitude from ±550 MPa to ±800 MPa. The entire surface topography was evaluated by using a 3D non-contact confocal technique and post-failure specimens after a fatigue test performed at three stress amplitudes, ±650 MPa, ±700 MPa and ±750 MPa. Such an attempt was proposed to analyse the fatigue response of AM Haynes 282 in the region near its yield strength. It was found that the printing orientation and the stress amplitude have a strong impact on service life and fracture surface characteristics. Finally, a surface topography parameter involving the mass density of furrows, root-mean-square height, and fractal dimension was successfully combined with the stress amplitude to estimate the fatigue life. The findings offer a novel approach to fatigue life prediction based on post-failure surface analysis, providing valuable insights for industrial applications and forensic engineering. Keywords: Nickel alloys,Fatigue,Additive manufacturing,Direct Metal Laser Sintering (DMLS),Fracture,Surface topography Affiliations:
Macek W. | - | other affiliation | Sitek R. | - | Warsaw University of Technology (PL) | Podulka P. | - | other affiliation | Lesiuk G. | - | other affiliation | Zhu S. | - | other affiliation | Liu X. | - | Imperial College London (GB) | Kopeć M. | - | IPPT PAN |
| 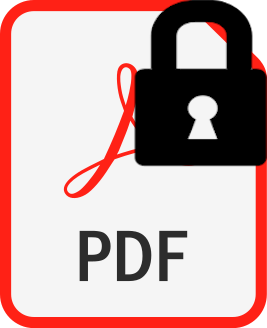 |
4. |
Kopeć M., Przygucka D.♦, Mierzejewska I., Sitek R.♦, Kowalewski Z. L., Jóźwiak S.♦, Effect of printing orientation on microstructure and fatigue behaviour of additively manufactured Haynes 282,
JOURNAL OF ALLOYS AND COMPOUNDS, ISSN: 0925-8388, No.181777, pp.1-16, 2025 Abstract: In this study, Haynes 282 alloy bars were fabricated using Direct Metal Laser Sintering (DMLS) in three build orientations: 0°, 45°, and 90°. The process was conducted under an argon protective atmosphere with an energy density of 104 J/mm³, a laser power of 100 W, and a scanning speed of 800 mm/s. The additively manufactured (AM) specimens underwent fatigue testing at stress amplitudes ranging from ±550 MPa to ±800 MPa. Specimens printed at 0° and 45° showed significantly improved mechanical performance, indicating these orientations are more favorable. Notably, the AM specimens demonstrated extended service life at stress amplitudes below 700 MPa, highlighting the potential of DMLS for producing durable Haynes 282 components. Keywords: Haynes 282,nickel alloys,fatigue,additive manufacturing,Direct Metal Laser Sintering (DMLS) Affiliations:
Kopeć M. | - | IPPT PAN | Przygucka D. | - | other affiliation | Mierzejewska I. | - | IPPT PAN | Sitek R. | - | Warsaw University of Technology (PL) | Kowalewski Z. L. | - | IPPT PAN | Jóźwiak S. | - | Military University of Technology (PL) |
| 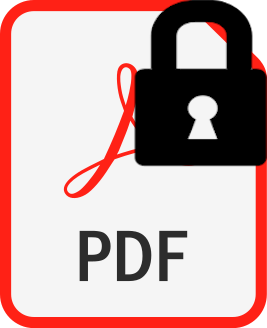 |
5. |
Tytko G.♦, Adamczyk-Habrajska M.♦, Linke Y.♦, Pengpeng S.♦, Kopeć M., Eddy Current Method in Non-Magnetic Aluminide Coating Thickness Assessment,
JOURNAL OF NONDESTRUCTIVE EVALUATION, ISSN: 0195-9298, DOI: 10.1007/s10921-025-01211-y, Vol.44, No.65, pp.1-11, 2025 Abstract: This study investigates the use of eddy current testing (ECT) as a non-destructive technique to evaluate the thickness and structural variations of non-magnetic aluminide coatings on MAR-M247 nickel-based superalloy. Coatings with thicknesses of 20 μm and 40 μm were applied to substrates exhibiting fine, coarse, and columnar grain structures. Using sensors of different geometries, impedance measurements were performed within a frequency range of 11.5 MHz to 12.5 MHz. Results demonstrated the designed sensor’s superior sensitivity, with the highest values of absolute resistance difference significantly exceeding the threshold for reliable distinction due to coating thicknesses or grain structures. The study highlights the impact of eddy current penetration depth and edge effects on the measurement accuracy, emphasizing the need for optimized sensor design and frequency selection. Findings confirm the efficacy of ECT in differentiating coatings of varying thicknesses and substrate structures, offering a reliable tool for quality control in high-temperature applications. Keywords: Aluminide coating, Eddy current testing, Non-destructive testing, Nickel alloys Affiliations:
Tytko G. | - | other affiliation | Adamczyk-Habrajska M. | - | other affiliation | Linke Y. | - | Warsaw University of Technology (PL) | Pengpeng S. | - | other affiliation | Kopeć M. | - | IPPT PAN |
| 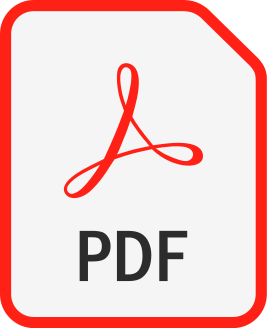 |
6. |
Kopeć M., Gunputh U.♦, Williams G.♦, Wojcieck M.♦, Kowalewski Z., Wood P.♦, On the Cover: Fatigue Damage Evolution in SS316L Produced by Powder Bed Fusion in Different Orientations with Reused Powder Feedstock,
EXPERIMENTAL MECHANICS, ISSN: 0014-4851, DOI: 10.1007/s11340-025-01179-w, pp.1-1, 2025, EDITORIAL Abstract: Background Metal Laser Powder Bed Fusion Melting (LPBF-M) is considered economically viable and environmentally
sustainable because of the possibility of reusing the residual powder feedstock leftover in the build chamber after a part
build is completed. There is however limited information on the fatigue damage development of LPBF-M samples made
from reused feedstock.
Objective In this paper, the stainless steel 316 L (SS316L) powder feedstock was examined and characterised after 25
reuses, following which the fatigue damage development of material samples made from the reused powder was assessed.
Methods The suitability of the powder to LPBF-M technology was evaluated by microstructural observations and measurements of Hall flow, apparent and tapped density as well as Carr’s Index and Hausner ratio. LPBF-M bar samples in three
build orientations (Z – vertical, XY – horizontal, ZX – 45° from the build plate) were built for fatigue testing. They were
then subjected to fatigue testing under load control using full tension and compression cyclic loading and stress asymmetry
coefficient equal to -1 in the range of stress amplitude from ± 300 MPa to ± 500 MPa.
Results Samples made from reused powder (25 times) in the LPBF-M process exhibited similar fatigue performance to fresh
unused powder although a lower ductility for vertical samples was observed during tensile testing. Printing in horizontal
(XY) and diagonal (ZX) directions, with reused powder, improved the service life of the SS316L alloy in comparison to
the vertical (Z).
Conclusions Over the 25 reuses of the powder feedstock there was no measurable difference in the flowability between the
fresh (Hall Flow: 21.4 s/50 g) and reused powder (Hall Flow: 20.6 s/50 g). This confirms a uniform and stable powder feeding
process during LPBF-M for both fresh and reused powder. The analysis of fatigue damage parameter, D, concluded cyclic
plasticity and ratcheting to be the main mechanism of damage. Keywords: SS316L ,Stainless steel,Fatigue,Additive manufacturing,Laser Powder Bed Fusion Melting (LPBF-M) Affiliations:
Kopeć M. | - | IPPT PAN | Gunputh U. | - | other affiliation | Williams G. | - | University of Derby (GB) | Wojcieck M. | - | other affiliation | Kowalewski Z. | - | IPPT PAN | Wood P. | - | University of Derby (GB) |
| 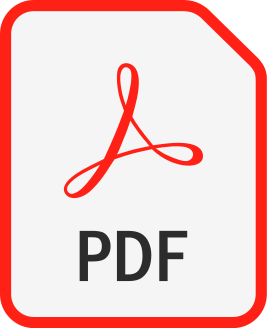 |
7. |
Szczęsny G.♦, Kopeć M., Kowalewski Z. L., Toxicity, Irritation, and Allergy of Metal Implants: Historical Perspective and Modern Solutions,
Coatings, ISSN: 2079-6412, DOI: 10.3390/coatings15030361, Vol.15, No.361, pp.1-32, 2025 Abstract: The widespread adoption of metal implants in orthopaedics and dentistry has revolutionized medical treatments, but concerns remain regarding their biocompatibility, toxicity, and immunogenicity. This study conducts a comprehensive literature review of traditional biomaterials used in orthopaedic surgery and traumatology, with a particular focus on their historical development and biological interactions. Research articles were gathered from PubMed andWeb of Science databases using keyword combinations such as “toxicity, irritation, allergy, biomaterials, corrosion, implants, orthopaedic surgery, biocompatible materials, steel, alloys, material properties, applications, implantology, and surface modification”. An initial pool of 400 articles was screened by independent reviewers based on predefined inclusion and exclusion criteria, resulting in 160 relevant articles covering research from 1950 to 2025. This paper explores the electrochemical processes of metals like iron, titanium, aluminium, cobalt, molybdenum, nickel, and chromium post-implantation, which cause ion release and wear debris formation. These metal ions interact with biological molecules, triggering localized irritation, inflammatory responses, and immune-mediated hypersensitivity. Unlike existing reviews, this paper highlights how metal–protein interactions can form antigenic complexes, contributing to delayed hypersensitivity and complications such as peri-implant osteolysis and implant failure. While titanium is traditionally considered bioinert, emerging evidence suggests that under certain conditions, even inert metals can induce adverse biological effects. Furthermore, this review emphasizes the role of oxidative stress, illustrating how metal ion release and systemic toxicity contribute to long-term health risks. It also uncovers the underappreciated genotoxic and cytotoxic effects of metal ions on cellular metabolism, shedding light on potential long-term repercussions. By integrating a rigorous methodological approach with an in-depth exploration of metal-induced biological responses, this paper offers a more nuanced perspective on the complex interplay between metal implants and human biology, advancing the discourse on implant safety and material innovation. Keywords: orthopaedic implants, toxicity, metals, biomaterials Affiliations:
Szczęsny G. | - | Medical University of Warsaw (PL) | Kopeć M. | - | IPPT PAN | Kowalewski Z. L. | - | IPPT PAN |
| 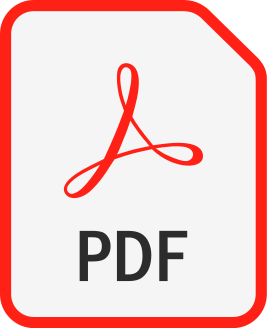 |
8. |
Kamiński J.♦, Adamczyk-Cieślak B.♦, Kopeć M., Kosiński A.♦, Sitek R.♦, Cover Picture: Materials and Corrosion. 3/2025: Effects of Reduction-Oxidation Cycles on the Structure, Heat and Corrosion Resistance of Haynes 282 Nickel Alloy Manufactured by using Powder Bed Fusion- Laser Beam Method,
materials and corrosion, ISSN: 0947-5117, DOI: 10.1002/maco.202570031, pp.1-1, 2025, EDITORIAL Keywords: corrosion, DMLS, haynes 282, nickel superalloy, hydrogen , oxidation Affiliations:
Kamiński J. | - | other affiliation | Adamczyk-Cieślak B. | - | other affiliation | Kopeć M. | - | IPPT PAN | Kosiński A. | - | other affiliation | Sitek R. | - | Warsaw University of Technology (PL) |
| 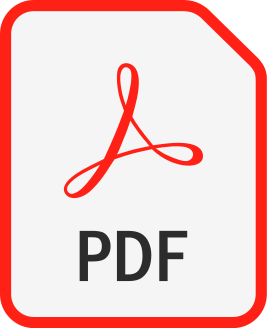 |
9. |
Sitek R.♦, Bochenek K., Maj P.♦, Marczak M.♦, Żaba K.♦, Kopeć M., Kaczmarczyk G.♦, Kamiński J.♦, Hot-Pressing of Ti-Al-N Multiphase Composite: Microstructure and Properties,
Applied Sciences, ISSN: 2076-3417, DOI: 10.3390/app15031341, Vol.15, No.1341, pp.1-15, 2025 Abstract: This study focuses on the development and characterization of a bulk Ti-Al-N
multiphase composite enriched with BN addition and sintered through hot pressing. The
research aimed to create a material with optimized mechanical and corrosion-resistant
properties suitable for demanding industrial applications. The composite was synthesized using a powder metallurgy approach with a mixture of AlN, TiN, and BN powders, processed under a high temperature and pressure. Comprehensive analyses, including microstructural evaluation, hardness testing, X-ray tomography, and electrochemical corrosion assessments, were conducted. The results confirmed the formation of a multiphase microstructure consisting of TiN, Ti₂AlN and Ti₃AlN phases. The microstructure was uniform with minimal porosity, achieving a hardness within the range of 500–540 HV2. Electrochemical tests revealed the formation of a passive oxide layer that provided moderate corrosion resistance in chloride-rich environment. However, localized pitting corrosion was observed under extreme conditions. The study highlights the potential of a BN admixture to enhance mechanical and corrosion-resistant properties and suggests directions for further optimization in sintering processes and material formulations. Keywords: AlN-TiN(BN) composite,hot-pressing,μCT,corrosion resistance Affiliations:
Sitek R. | - | Warsaw University of Technology (PL) | Bochenek K. | - | IPPT PAN | Maj P. | - | Warsaw University of Technology (PL) | Marczak M. | - | other affiliation | Żaba K. | - | other affiliation | Kopeć M. | - | IPPT PAN | Kaczmarczyk G. | - | other affiliation | Kamiński J. | - | other affiliation |
| 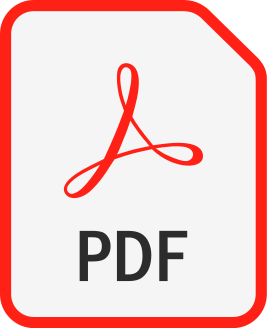 |
10. |
Kukla D., Kowalewski Z., Kopeć M., Assessment of microstructural changes in S235 steel after cold rolling using eddy current testing,
JOURNAL OF THEORETICAL AND APPLIED MECHANICS, ISSN: 1429-2955, pp.1-6, 2025 Abstract: This study investigates the eddy current testing (ECT) technique to assess microstructural changes in S235 low carbon steel after cold rolling. Specimens of varying thicknesses (12 mm, 8 mm, and 6mm) were analyzed to evaluate the impact of deformation on such properties as dislocation density, grain texture, and hardness. Metallographic studies using light microscopy were performed, supplemented by dislocation density measurements via transmission electron microscopy (TEM). The ECT results demonstrated that microstructural changes, particularly cold-work hardening and grain elongation, significantly influenced the phase angle of impedance. Lower penetration depths were more sensitive to surface changes, highlighting the capacity of ECT for detecting nearsurface deformation. This work establishes a robust, non-destructive methodology for characterizing manufacturing-induced microstructural changes in heat-resistant steels, with applications in quality control and material performance evaluation Keywords: cold rolling, eddy current, microstructure Affiliations:
Kukla D. | - | IPPT PAN | Kowalewski Z. | - | IPPT PAN | Kopeć M. | - | IPPT PAN |
| 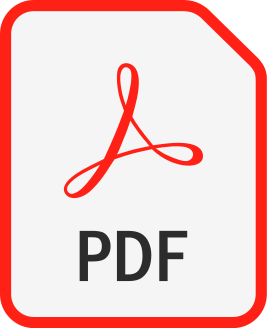 |
11. |
Dubey Ved P., Kopeć M., Kowalewski Z., Experimental identification of CP-Cu yield surface and its evolution due to complex loading pre-deformation,
JOURNAL OF THEORETICAL AND APPLIED MECHANICS, ISSN: 1429-2955, pp.1-14, 2025 Abstract: This study examines the yield surface evolution of technical copper (CP-Cu) under complex loading, focusing on monotonic tension and combined tension with cyclic torsion. Using biaxial testing, initial and pre-deformed yield surfaces were analysed. Results indicate kinematic hardening with tensile pre-strain, while cyclic torsion induces anisotropic hardening at lower amplitudes (±0.1 %) and softening at higher amplitudes (±0.2 %). Strain amplitude significantly impacts material response, while frequency has a minor effect Keywords: copper,pre-deformation,yield Surface,biaxial Affiliations:
Dubey Ved P. | - | IPPT PAN | Kopeć M. | - | IPPT PAN | Kowalewski Z. | - | IPPT PAN |
| 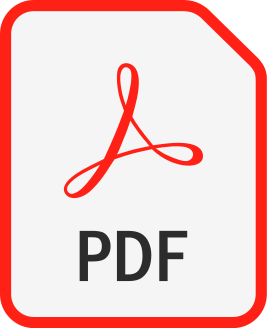 |
12. |
Kopeć M., Digital image correlation in monitoring of fatigue damage development of MAR-M247 with aluminide coating,
JOURNAL OF THEORETICAL AND APPLIED MECHANICS, ISSN: 1429-2955, pp.1-6, 2025 Abstract: This study investigates the fatigue damage development in MAR-M247, a nickel-based superalloy with aluminide coating, using the digital image correlation (DIC) technique. The alloy’s microstructures, including fine, coarse, and columnar grains, were analyzed to understand their influence on fatigue crack initiation and propagation. Fatigue tests were conducted at room temperature under controlled force, with strain evolution monitored through non-contact full-field DIC measurements. Results revealed that fine-grained MAR-M247 exhibited superior fatigue resistance due to uniform strain distribution, while coarse-grained and columnar structures showed pronounced strain localization and earlier crack initiation. The application of aluminide coatings did not significantly affect strain distribution across the different microstructures but highlighted complex interactions between coating and grain structure under cyclic loading. These findings provide critical insights into optimizing the performance of MAR-M247 for high-stress applications Keywords: fatigue, coatings, nickel alloys, digital image correlation Affiliations:
| 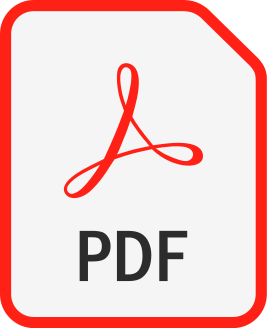 |
13. |
Kukla D., Kondej A.♦, Jończyk S.♦, Lasota P.♦, Tabin J., Schob D.♦, Roszak R.♦, Kawałko J.♦, Zagórski A.♦, Kopeć M., Eddy current methodology in the non-direct measurement of martensite during plastic deformation of SS316L,
Open Engineering , ISSN: 2391-5439, Vol.15(1), No.20250118, pp.1-9, 2025 Abstract: This study examines the use of various eddy current induction techniques to evaluate the stability of austenite in SS316L steel subjected to plastic deformation. This deformation, which occurs locally in austenitic steel structures under operational loads, leads to a martensitic transformation. This transformation affects both the mechanical and magnetic properties of the steel. The martensitic phase content, being ferromagnetic, can be quantitatively assessed using a ferritoscope and other magnetic induction methods. The research explores techniques based on the analysis of impedance signal changes obtained using the NORTEC defetoscope and the WIROTEST device developed by the author’s team. By examining the phase angle, ET signal amplitude, and resonance frequency changes in the eddy current excitation system, the study aims to quantitatively assess the martensitic phase content in samples subjected to plastic deformation. These results were verified through comparison with data from a ferritoscope and X-ray diffraction analysis. Additionally, the eddy current technique facilitates surface screening of the specimen, making it possible to identify cracks and locate the martensitic transformation front in areas of stress concentration. Keywords: eddy current, martensitic transformation, additive manufacturing, stainless steel, non-destructive testing, WIROTEST device Affiliations:
Kukla D. | - | IPPT PAN | Kondej A. | - | other affiliation | Jończyk S. | - | other affiliation | Lasota P. | - | other affiliation | Tabin J. | - | IPPT PAN | Schob D. | - | other affiliation | Roszak R. | - | other affiliation | Kawałko J. | - | other affiliation | Zagórski A. | - | Warsaw University of Technology (PL) | Kopeć M. | - | IPPT PAN |
| 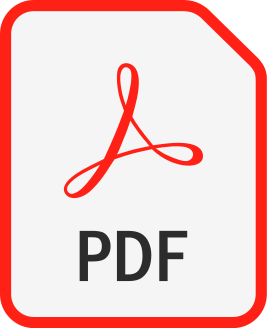 |
14. |
Kopeć M., Kukla D., Kowalewski Z., Assessment of aluminide coating integrity by using acoustic emission,
JOURNAL OF THEORETICAL AND APPLIED MECHANICS, ISSN: 1429-2955, DOI: 10.15632/jtam-pl/203353 , pp.1-6, 2025 Abstract: Coatings are essential for protecting high-temperature components in aerospace and power generation industries. This study evaluates the integrity of aluminide coatings on MAR-M247, a nickelbased superalloy, under uniaxial tensile loading using acoustic emission (AE). Aluminide coatings, deposited via chemical vapor deposition (CVD), provide oxidation and corrosion resistance but are prone to damage under operational stresses. AE monitoring, a nondestructive evaluation method, detects transient elastic waves associated with damage events such as crack initiation and delamination. By analyzing AE signal characteristics like amplitude and energy, this research identifies acoustic signatures indicative of coating degradation. The findings highlight AE’s potential for real-time damage assessment, enabling early detection and predictive maintenance strategies in high-temperature applications. Keywords: coatings,acoustic emission,nickel alloys,non destructive testing Affiliations:
Kopeć M. | - | IPPT PAN | Kukla D. | - | IPPT PAN | Kowalewski Z. | - | IPPT PAN |
| 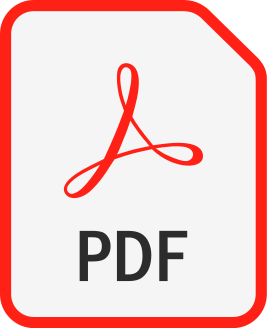 |
15. |
Podulka P.♦, Macek W.♦, Zima B.♦, Kopeć M., Ricardo B.♦, Achtelik H.♦, Fracture surface topography measurements analysis of low-alloyed corrosion resistant steel after bending-torsion fatigue tests,
Precision Engineering, ISSN: 1873-2372, DOI: 10.1016/j.precisioneng.2024.07.002, pp.1-34, 2024 Abstract: In this paper, an assessment of a topography measurement method for fracture surfaces of 10HNAP steel after bending-torsion fatigue tests was performed. Surface roughness was measured by using a non-contact Focus Variation Microscopy (FVM) technique in which the non-measured points (NMPs) and outliers (spikes) were removed by the application of general methods. The results revealed, that the optical measurement method introduced variations in the high-frequency errors, considered as noise within the selected bandwidth. Therefore, the minimization of the high-frequency noise (HFN) was proposed based on an extensive examination of ISO 25178 roughness parameters. Additionally, a general S-filter was applied, as recommended by international standards and commercial software. It was used to identify and remove noise from the measured data after pre-processing. Consequently, levelling and eliminating of NMPs and spikes was successfully performed. Subsequently, the results obtained by using various filters were compared to further assess the impact of different filtration bandwidths. Finally, the proposed procedure was validated by implementing different general functions, such as autocorrelation (ACF), power spectral densities (PSD), and texture direction (TD). It was concluded, that coupled characteristics, including profile and areal measurements, should be studied simultaneously since they are necessary to analyze the fracture surfaces comprehensively. Keywords: bending-torsion fatigue ,surface topography ,roughness ,non-measured points ,outliers ,high-frequency noise,measurement errors Affiliations:
Podulka P. | - | other affiliation | Macek W. | - | other affiliation | Zima B. | - | other affiliation | Kopeć M. | - | IPPT PAN | Ricardo B. | - | other affiliation | Achtelik H. | - | other affiliation |
| 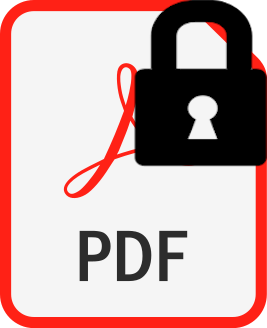 |
16. |
Kopeć M., Brodecki A., Kowalewski Z.L., Quantitative digital image correlation approach for the monitoring of fatigue damage development in 10CrMo9-10 steel in the as-received state and after extended service,
MEASUREMENT, ISSN: 0263-2241, DOI: 10.1016/j.measurement.2024.114926, Vol.234, No.114926, pp.1-9, 2024 Abstract: In this paper, the quantitative Digital Image Correlation (DIC) approach was used to study the long-time degradation of two different states of 10CrMo9-10 (10H2M) power engineering steel. The specimens subjected to cyclic loading (R = 0) were monitored by using the DIC technique. The data obtained from DIC measurements were presented in form of strain distributions for specified, independent points within the strain gauge of specimens. Furthermore, the strain profiles were extracted for the particular stages of fatigue damage development (FDD). The presented methodology provides a different approach of DIC application, in which, the data could be treated more quantitative than qualitative. Keywords: Power engineering steel, Fatigue, Damage Affiliations:
Kopeć M. | - | IPPT PAN | Brodecki A. | - | IPPT PAN | Kowalewski Z.L. | - | IPPT PAN |
| 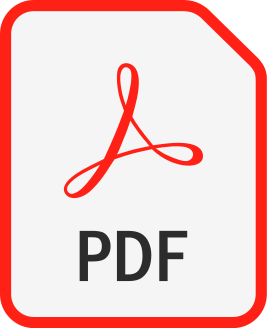 |
17. |
Liu X.♦, Jin S.♦, Ming M.♦, Fan C.♦, Liu H.♦, Politis D.J.♦, Kopeć M., A high throughput in-situ measurement of heat transfer in successive non-isothermal forming of sheet alloys,
Journal of Manufacturing Processes, ISSN: 1526-6125, DOI: 10.1016/j.jmapro.2024.08.048, Vol.129, pp.77-91, 2024 Abstract: The measurement and control of the heat transfer of sheet alloys in successive non-isothermal forming cycles is crucial to achieve the desired post-form properties and microstructure, which could not as of yet be realized by using traditional test facilities. In the present research, a novel heat transfer measurement facility was designed to generate and subsequently measure the in-situ heat transfer from a sheet alloy to multi-mediums such as forming tools, air, lubricant and coating. More importantly, the facility was able to use a single sheet alloy sample to perform successive non-isothermal forming cycles, and subsequently obtain high throughput experimental results including the temperature evolution, cooling rate, mechanical properties and microstructures of the alloy. The high throughput in-situ heat transfer measurement facility identified that the cooling rate of AA7075 was 152 °C/s and the mechanical strength was over 530 MPa in the 1st forming cycle. However, it decreased to less than the critical value of 100 °C/s in the successive 10th forming cycle, leading to a low mechanical strength of only 487 MPa. The identified variations that occur in the successive non-isothermal forming cycles would improve the consistency and accuracy of part performance in large-scale manufacturing. Keywords: High throughput in-situ measurement,Heat transfer,Successive non-isothermal forming,Sheet alloys,Microstructure Affiliations:
Liu X. | - | Imperial College London (GB) | Jin S. | - | other affiliation | Ming M. | - | other affiliation | Fan C. | - | other affiliation | Liu H. | - | Imperial College London (GB) | Politis D.J. | - | Imperial College London (GB) | Kopeć M. | - | IPPT PAN |
| 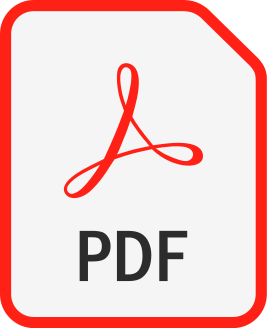 |
18. |
Kopeć M., Dubey Ved P., Pawlik M.♦, Wood P.♦, Kowalewski Z.L., Experimental identification of yield surface for additively manufactured stainless steel 316L under tension–compression-torsion conditions considering its printing orientation,
Manufacturing Letters, ISSN: 2213-8463, DOI: 10.1016/j.mfglet.2024.07.003, Vol.41, pp.28-32, 2024 Abstract: Stainless steel 316L tubes and bars were additively manufactured (AM) by using the Laser Powder Bed Fusion Melting (LPBF-M) method in three orientations. As-built specimens were then machined and the initial yield surface was determined for three printing orientations based on the yield stress definition for 0.005 % plastic offset strain. The as-received, wrought material was additionally tested using the same tension–compression-torsion conditions to compare the mechanical behaviour of AM and wrought SS316L. The sizes of yield surfaces elaborated for LPBF-M specimens increased along the tensile and compressive directions and shrunk when torsion was applied, as compared to the as-received specimen. Keywords: Stainless steel ,Yield surface ,Additive manufacturing Affiliations:
Kopeć M. | - | IPPT PAN | Dubey Ved P. | - | IPPT PAN | Pawlik M. | - | other affiliation | Wood P. | - | University of Derby (GB) | Kowalewski Z.L. | - | IPPT PAN |
| 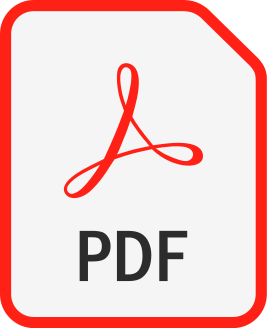 |
19. |
Kopeć M., Digital image correlation approach for low-cycle fatigue life monitoring of 13HMF power engineering steel,
Optics and Lasers in Engineering, ISSN: 0143-8166, DOI: https://doi.org/10.1016/j.optlaseng.2024.108448, Vol.181, No.108448, pp.1-10, 2024 Abstract: In this paper, strain evolution of 13HMF power engineering steel was analysed during force-controlled low cycle fatigue (LCF). The material performance under cyclic loading was monitored by using Digital Image Correlation (DIC) technique for different values of stress amplitude exceeding the yield strength of the material significantly. Data collected from DIC was compared to the extensometer ones to confirm the effectiveness of the proposed approach. Finally, the cloud data reflecting the fatigue performance of 13HMF was generated in the form of strain-stress amplitude - service life distribution map. Keywords: Fatigue,Mechanical properties,Strain analysis Affiliations:
| 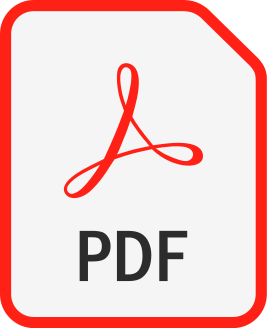 |
20. |
Macek W.♦, Kopeć M., Laska A.♦, Kowalewski Z. L., Entire fracture surface topography parameters for fatigue life assessment of 10H2M steel,
Journal of Constructional Steel Research, ISSN: 1873-5983, DOI: 10.1016/j.jcsr.2024.108890, Vol.221, No.108890, pp.1-11, 2024 Abstract: In this paper, the entire fracture surface approach was used to assess an effect of 280,000 h of exploitation under internal pressure of 2.9 MPa and high temperature of 540 °C on the fatigue response of 10H2M (10CrMo9–10) power engineering steel. The mechanical testing was carried out on the hourglass specimens produced from the as-received, unused pipeline and the same material after long-time exploitation. The uniaxial tensile tests were performed to establish the stress amplitude for subsequent force controlled, fatigue testing in the range from ±250 MPa to ±400 MPa under the frequency of 20 Hz. Since the exploited 10H2M steel was characterized by significantly lower mechanical properties, different damage mechanisms responsible for specimen failure were revealed through fracture surface analysis. The fracture surface topography evaluation was performed with a 3D non-contact measuring system. It was found, that the exploitation state has a strong impact on the fatigue life and fracture characteristics since the significant drop in lifespan of about 300 %–400 % was found for the material after prolonged service. Finally, the proposed surface topography parameter was related to the stress amplitude in order to estimate the fatigue life for the steel in question. Keywords: fatigue , 10H2M steel , Mechanical properties , Surface topography Affiliations:
Macek W. | - | other affiliation | Kopeć M. | - | IPPT PAN | Laska A. | - | other affiliation | Kowalewski Z. L. | - | IPPT PAN |
| 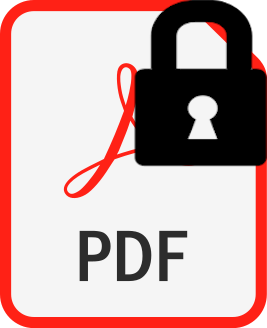 |
21. |
Kopeć M., The analysis of strain response for as-received and exploited 10H2M power engineering steel subjected to low cycle fatigue in plastic regime,
International Journal of Pressure Vessels and Piping, ISSN: 0308-0161, DOI: 10.1016/j.ijpvp.2023.105110, Vol.207, No.105110, pp.1-6, 2024 Abstract: Thermal shocks occurred during power plant station shutdowns result in notable changes in material microstructure and affect its mechanical behaviour significantly. High temperature gradients as well as internal pressure changes in pipes are also responsible for external and internal stress introduction. Such stress may also exceed the yield strength of the material resulting in its deformation. Thus, in this work, the comparative studies on 10H2M power engineering steel in the as-received and exploited state (280 000h at 540 °C under internal pressure of 1.8 MPa) subjected to low cycle fatigue in the plastic regime were performed. The strain response of both states of steel was monitored for three different values of stress amplitude exceeding the yield strength of the material. The significant differences in strain response were found for both states of steel when subjected to the same stress amplitude Keywords: Fatigue,10H2M steel,Mechanical properties,Strain analysis Affiliations:
| 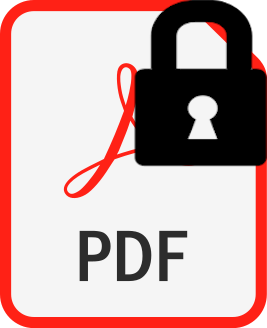 |
22. |
Kopeć M., Liu X.♦, Gorniewicz D.♦, Modrzejewski P.♦, Zasada D.♦, Jóźwiak S.♦, Janiszewski J.♦, Kowalewski Z.L., Mechanical response of 6061-T6 aluminium alloy subjected to dynamic testing at low temperature: Experiment and modelling,
INTERNATIONAL JOURNAL OF IMPACT ENGINEERING, ISSN: 0734-743X, DOI: 10.1016/j.ijimpeng.2023.104843, Vol.185, No.104843, pp.1-10, 2024 Abstract: The aim of this research was to investigate an effect of low temperature on the mechanical properties and mi-crostructure of 6061-T6 aluminium alloy (AA6061-T6) subjected to dynamic loading. The specimens were subjected to dynamic compression at a low temperature of −80°C in a range of strain rates from 1.25 × 10 3 1/s to 3.4 × 10 3 1/s to compare their mechanical responses. The deformation mechanisms were analysed through EBSD observations during which dynamic recovery, was found as the dominant one. Furthermore, microstruc-tural analysis indicated that deformation under high strain rate conditions and temperature of-80°C enables to keep the constant initial grain size of the material after the loading applied. The material behaviour was modelled using mechanism-based viscoplastic constitutive equations. Furthermore, an accuracy of the developed model was validated by comparing it to experimental data. The set of constitutive equations proposed has been successful in modelling the stress-strain behaviour of the material for the range of strain rates and temperatures encountered in aluminium-forming processes under low-temperature conditions. Keywords: Split Hopkinson pressure bar (SHPB),Low temperature,AA6061-T6,Microstructure Affiliations:
Kopeć M. | - | IPPT PAN | Liu X. | - | Imperial College London (GB) | Gorniewicz D. | - | Military University of Technology (PL) | Modrzejewski P. | - | other affiliation | Zasada D. | - | other affiliation | Jóźwiak S. | - | Military University of Technology (PL) | Janiszewski J. | - | Military University of Technology (PL) | Kowalewski Z.L. | - | IPPT PAN |
| 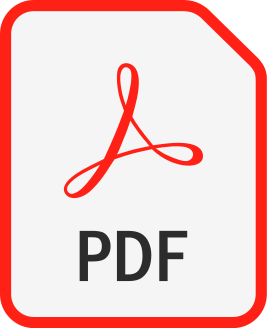 |
23. |
Kamiński J.♦, Adamczyk-Cieślak B.♦, Kopeć M., Kosiński A.♦, Sitek R.♦, Effects of Reduction-Oxidation Cycles on the Structure, Heat and Corrosion Resistance of Haynes 282 Nickel Alloy Manufactured by Using Powder Bed Fusion-Laser Beam Method,
materials and corrosion, ISSN: 0947-5117, DOI: 10.1002/maco.202414477, pp.1-14, 2024 Abstract: The study investigated the effect of the oxidation–reduction cycles on the structure and corrosion resistance of the Haynes 282 nickel superalloy at ambient and elevated temperatures. The comparative studies were performed on specimens produced by the Powder Bed Fusion-Laser Beam (PBF-LB) process and those in the as-received state. The microstructure of the PBF-LB specimens was studied using optical and scanning electron microscopy, whereas the chemical composition of the scale formed after isothermal oxidation in an air atmosphere at 750°C was analysed using energy-dispersive X-ray spectroscopy and X-ray Photoelectron Spectroscopy. The phase composition of the formed scale was determined by X-ray diffraction. Laboratory-induced hydrogen atmosphere was adopted through cathodic charging. A comparison of corrosion resistance was carried out on two types of Haynes 282 specimens, before and after the oxidation and cathodic charging processes. It was found that PBF-LB process could be effectively used to manufacture Haynes 282 nickel superalloy with low porosity and a fine crystalline microstructure. The low-porous, fine-crystalline microstructure of the tested specimens produced by the PBF-LB technique exhibited good resistance to electrochemical corrosion, slightly lower than wrought Haynes 282 nickel superalloy specimens. Keywords: corrosion, DMLS, haynes 282 nickel superalloy, hydrogen, oxidation Affiliations:
Kamiński J. | - | other affiliation | Adamczyk-Cieślak B. | - | other affiliation | Kopeć M. | - | IPPT PAN | Kosiński A. | - | other affiliation | Sitek R. | - | Warsaw University of Technology (PL) |
| 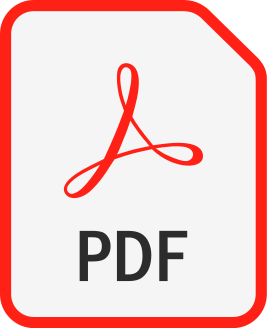 |
24. |
Tytko G.♦, Adamczyk-Habrajska M.♦, Luo Y.♦, Kopeć M., Eddy Current Testing in the Quantitive Assessment of Degradation State in MAR247 Nickel Superalloy with Aluminide Coatings,
JOURNAL OF NONDESTRUCTIVE EVALUATION, ISSN: 0195-9298, DOI: 10.1007/s10921-024-01129-x, Vol.43, No.112, pp.1-10, 2024 Abstract: In this paper, the effectiveness of the eddy current methodology for crack detection in MAR 247 nickel-based superalloy with aluminide coatings subjected to cyclic loading was investigated. The specimens were subjected to force-controlled fatigue tests under zero mean level, constant stress amplitude from 300 MPa to 600 MPa and a frequency of 20 Hz. During the fatigue, a particular level of damage was introduced into the material leading to the formation of microcracks. Subsequently, a new design of probe with a pot core was developed to limit magnetic flux leakage and directed it towards the surface under examination. The suitability of the new methodology was further confirmed as the specimens containing defects were successfully identified. The changes in probe resistance values registered for damaged specimens ranged approximately from 8 to 14%. Keywords: Nickel alloys, Aluminide coating, Non-destructive testing, Eddy current testing Affiliations:
Tytko G. | - | other affiliation | Adamczyk-Habrajska M. | - | other affiliation | Luo Y. | - | other affiliation | Kopeć M. | - | IPPT PAN |
| 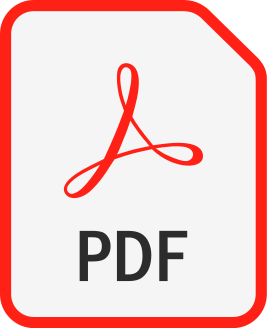 |
25. |
Kopeć M., Gunputh U.♦, Williams G.♦, Macek W.♦, Kowalewski Z.L., Wood P.♦, Fatigue Damage Evolution in SS316L Produced by Powder Bed Fusion in Different Orientations with Reused Powder Feedstock,
EXPERIMENTAL MECHANICS, ISSN: 0014-4851, DOI: 10.1007/s11340-024-01118-1, pp.1-16, 2024 Abstract: Background
Metal Laser Powder Bed Fusion Melting (LPBF-M) is considered economically viable and environmentally sustainable because of the possibility of reusing the residual powder feedstock leftover in the build chamber after a part build is completed. There is however limited information on the fatigue damage development of LPBF-M samples made from reused feedstock.
Objective
In this paper, the stainless steel 316 L (SS316L) powder feedstock was examined and characterised after 25 reuses, following which the fatigue damage development of material samples made from the reused powder was assessed.
Methods
The suitability of the powder to LPBF-M technology was evaluated by microstructural observations and measurements of Hall flow, apparent and tapped density as well as Carr’s Index and Hausner ratio. LPBF-M bar samples in three build orientations (Z – vertical, XY – horizontal, ZX – 45° from the build plate) were built for fatigue testing. They were then subjected to fatigue testing under load control using full tension and compression cyclic loading and stress asymmetry coefficient equal to -1 in the range of stress amplitude from ± 300 MPa to ± 500 MPa.
Results
Samples made from reused powder (25 times) in the LPBF-M process exhibited similar fatigue performance to fresh unused powder although a lower ductility for vertical samples was observed during tensile testing. Printing in horizontal (XY) and diagonal (ZX) directions, with reused powder, improved the service life of the SS316L alloy in comparison to the vertical (Z).
Conclusions
Over the 25 reuses of the powder feedstock there was no measurable difference in the flowability between the fresh (Hall Flow: 21.4 s/50 g) and reused powder (Hall Flow: 20.6 s/50 g). This confirms a uniform and stable powder feeding process during LPBF-M for both fresh and reused powder. The analysis of fatigue damage parameter, D, concluded cyclic plasticity and ratcheting to be the main mechanism of damage. Keywords: SS316L ,Stainless steel,Fatigue ,Additive manufacturing,Laser Powder Bed Fusion Melting (LPBF-M) Affiliations:
Kopeć M. | - | IPPT PAN | Gunputh U. | - | other affiliation | Williams G. | - | University of Derby (GB) | Macek W. | - | other affiliation | Kowalewski Z.L. | - | IPPT PAN | Wood P. | - | University of Derby (GB) |
| 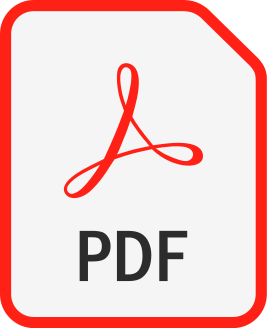 |
26. |
Kopeć M., Mierzejewska I., Gorniewicz D.♦, Sitek R.♦, Jóźwiak S.♦, High-temperature oxidation behaviour of additively manufactured and wrought HAYNES 282,
JOURNAL OF MATERIALS SCIENCE, ISSN: 0022-2461, DOI: 10.1007/s10853-024-10207-4, pp.1-19, 2024 Abstract: Direct Metal Laser Sintered Haynes 282 specimens as well as wrought ones were subjected to high-temperature exposure at 1000 °C for 100h in air to compare their oxidation behaviour. The specimens were removed from the furnace after 1h, 5h, 25h, 50h and 100h to reveal and study oxidation mechanisms through morphological and cross-sectional examination by using scanning electron microscopy with energy dispersive spectroscopy attachment and X-ray diffraction. Microstructural studies revealed that the oxidation kinetics, determined by changes in thickness scale and depth of aluminium diffusion zone, were mainly driven by the formation of Cr2O3 for the wrought material, and TiO2 for DMLS one. The wrought material was characterized by the oxidation rate equal to 0.96 and followed the logarithmic law. On the other hand, DMLS-manufactured Haynes 282 exhibited oxidation rate of 0.90 and follows the linear law for the thickness scale considerations. However, when the depth of aluminium diffusion was investigated, it had an oxidation rate of 0.87 and followed cubic law. Affiliations:
Kopeć M. | - | IPPT PAN | Mierzejewska I. | - | IPPT PAN | Gorniewicz D. | - | Military University of Technology (PL) | Sitek R. | - | Warsaw University of Technology (PL) | Jóźwiak S. | - | Military University of Technology (PL) |
| 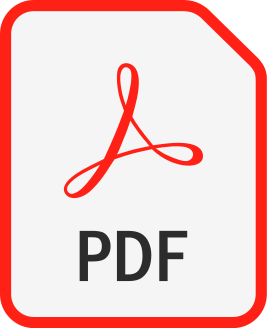 |
27. |
Kopeć M., Effect of Aluminide Coating Thickness on High-Temperature Fatigue Response of MAR-M247 Nickel-Based Superalloy,
Coatings, ISSN: 2079-6412, DOI: 10.3390/coatings14081072, Vol.14(8), No.1072, pp.1-12, 2024 Abstract: In this paper, 20 µm and 40 µm thick aluminide coatings were deposited on MAR-M247 nickel-based superalloy through the chemical vapor deposition (CVD) process in a hydrogen protective atmosphere for 4 h and 12 h, respectively, at a temperature of 1040 °C and an internal pressure of 150 mbar. The effect of aluminide coating thickness on the high-temperature performance of the MAR-M247 nickel-based superalloy was examined during a fatigue test at 900 °C. After high-temperature testing, the specimens were subjected to fractographic analysis to reveal the damage mechanisms. No significant effect of coating thickness was found since the material exhibited a similar service life throughout the fatigue test when subjected to the same stress amplitude. One should stress that the coating remained well adhered after specimen fracture, confirming its effectiveness in protecting the material against high-temperature oxidation. Keywords: fatigue, aluminide coatings, nickel alloys , high-temperature performance Affiliations:
| 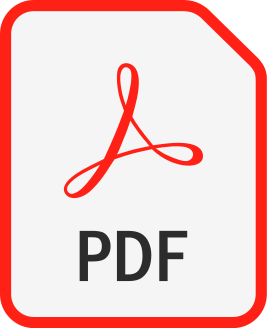 |
28. |
Kopeć M., Recent Advances in the Deposition of Aluminide Coatings on Nickel-Based Superalloys: A Synthetic Review (2019–2023),
Coatings, ISSN: 2079-6412, DOI: 10.3390/coatings14050630, Vol.14, No.630, pp.1-15, 2024 Abstract: Thermal barrier coatings (TBCs) are widely used to improve the oxidation resistance and high-temperature performance of nickel-based superalloys operating in aggressive environments. Among the TBCs, aluminide coatings (ACs) are commonly utilized to protect the structural parts of jet engines against high-temperature oxidation and corrosion. They can be deposited by differ-ent techniques, including pack cementation (PC), slurry aluminizing or chemical vapor deposition (CVD). Although the mentioned deposition techniques have been known for years, the constant developments in materials sciences and processing stimulates progress in terms of ACs. There-fore, this review paper aims to summarize recent advances in the AC field that have been report-ed between 2019 and 2023. The review focuses on recent advances involving improved corrosion resistance in salty environments as well as against high temperatures ranging between 1000 °C and 1200 °C under both continuous isothermal high-temperature exposure for up to 1000 h and cyclic oxidation resulting from AC application. Additionally, the beneficial effects of enhanced mechanical properties, including hardness, fatigue performance and wear, are discussed. Keywords: high-temperature corrosion, aggressive environment, coating deposition Affiliations:
| 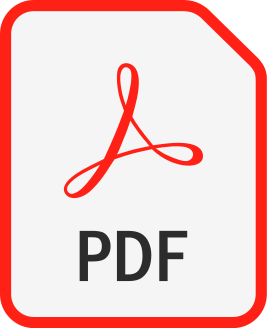 |
29. |
Kopeć M., Gunputh U.♦, Macek W.♦, Kowalewski Z.L., Wood P.♦, Orientation effects on the fracture behaviour of additively manufactured stainless steel 316L subjected to high cyclic fatigue,
Theoretical and Applied Fracture Mechanics, ISSN: 0167-8442, DOI: 10.1016/j.tafmec.2024.104287, pp.1-20, 2024 Abstract: In this paper, stainless steel 316L (SS316L) bars were additively manufactured (AM) in three orientations (Z – vertical, XY – horizontal, ZX45 – midway between vertical and horizontal) by using the Laser Powder Bed Fusion Melting (LPBF-M) method. The AM specimens were subjected to load control fatigue testing under full tension and compression (R = -1) at stress amplitudes ±350, ±400 and ±450 MPa. The XY and ZX45 printing orientations were found to significantly improve service life. Although similar strain response was found for each orientation when the same stress amplitude was applied, slightly different fracture mechanisms were identified during the post-mortem surface observations. Keywords: SS316L,stainless steel,fatigue,additive manufacturing,Laser Powder Bed Fusion Melting (LPBF-M) Affiliations:
Kopeć M. | - | IPPT PAN | Gunputh U. | - | other affiliation | Macek W. | - | other affiliation | Kowalewski Z.L. | - | IPPT PAN | Wood P. | - | University of Derby (GB) |
| 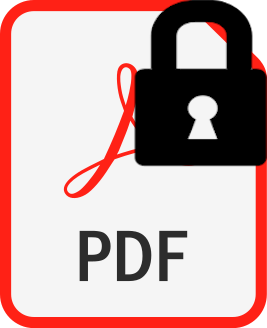 |
30. |
Kopeć M., Kukla D., Wyszkowski M., Kowalewski Z.L., High temperature fatigue testing of turbine blades,
FATIGUE OF AIRCRAFT STRUCTURES, ISSN: 2300-7591, DOI: 10.2478/fas-2023-0002, Vol.15, pp.22-27, 2024 Abstract: This paper evaluates the efficacy of a patented grip for high-temperature fatigue testing by establishing the S-N curve for full-scale nickel-based turbine blades under simulated environmental conditions. Initially, a bending test assessed the stress-displacement characteristics of the component. This was followed by a series of fatigue tests at 950°C, using cyclic bending with force amplitudes from 5.2 kN to 6.6 kN and a constant frequency of 10 Hz. The setup, integrating the grip into a standard testing machine,
proved effective for high-temperature tests and successfully determined the service life of full-scale components. Keywords: fatigue,high temperature,turbine blade,full-scale fatigue test Affiliations:
Kopeć M. | - | IPPT PAN | Kukla D. | - | IPPT PAN | Wyszkowski M. | - | IPPT PAN | Kowalewski Z.L. | - | IPPT PAN |
| 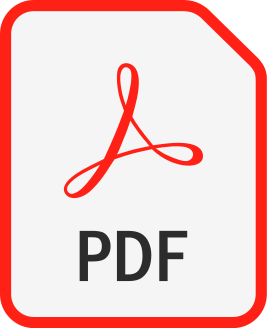 |
31. |
Kopeć M., What Makes for a “Good” Supervisor?,
Academia, Magazyn Polskiej Akademii Nauk, ISSN: 1733-8662, DOI: 10.24425/academiaPAS.2024.152923, Vol.4, No.80, pp.17-19, 2024 Abstract: A newly admitted doctoral student is often simply thrown in at the deep end, facing a whole new environment, unfamiliar faces, and a multitude of challenges. More often than not, they
feel ill-equipped and insufficiently supported by their
supervisor – the person who is ostensibly their closest
ally. This, in turn, affects the overall experience and
success of their academic path. But is this primarily
due to a flawed system, the supervisor’s attitude, or
perhaps the student’s own approach? The truth likely
lies somewhere in between. Affiliations:
| 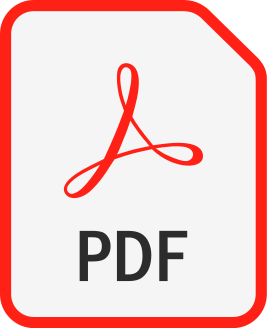 |
32. |
Kopeć M., Kurs na promotora,
Academia, Magazyn Polskiej Akademii Nauk, ISSN: 1733-8662, DOI: 10.24425/academiaPAN.2024.152814, Vol.4, No.80, pp.17-19, 2024 Abstract: Świeżo upieczony student studiów doktoranckich często jest wrzucany na głęboką wodę-
– nowe środowisko, nowi ludzie, masa wyzwań i trudności. Niejednokrotnie ma on wrażenie, że brakuje mu odpowiednich umiejętności i wsparcia ze strony
promotora, co bezpośrednio wpływa na jakość procesu naukowego. Czy to jednak głównie kwestia wadliwego systemu, postawy promotora, czy może podejścia samego studenta? Szczerze mówiąc, problem
leży zapewne pośrodku. Affiliations:
| 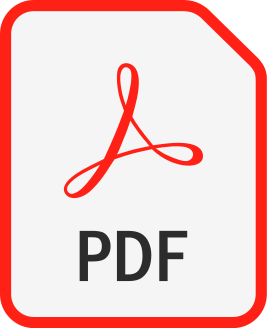 |
33. |
Dubey Ved P., Kopeć M., Łazińska M.♦, Kowalewski Z.L., Yield surface identification of CP-Ti and its evolution reflecting pre-deformation under complex loading,
International Journal of Plasticity, ISSN: 0749-6419, DOI: 10.1016/j.ijplas.2023.103677, Vol.167, pp.1-21, 2023 Abstract: Uniaxial testing methods to characterize materials provide only limited data that is insufficient to fully understand all aspects of their behaviour, such as initial texture or anisotropy. Therefore, this research aims to conduct complex stress loading experiments to understand the physical mechanism accountable for plastic deformation caused by monotonic tension and tension assisted by proportional cyclic torsion in the CP-Ti (Commercially Pure Titanium). The yield surface approach was applied to assess the variation of mechanical properties in the as-received and predeformed material. It was found, that such monotonic tension associated with cyclic torsion caused a significant decrease of the tensile stress. The initial yield surface obtained for the asreceived material exhibits anisotropic behaviour, whereas, the sizes of subsequent yield surface reflecting pre-deformation were reduced in all directions with exception of the tension direction. Keywords: yield surface,pre-deformation,plastic anisotropy,cycle loading,tubular specimen Affiliations:
Dubey Ved P. | - | IPPT PAN | Kopeć M. | - | IPPT PAN | Łazińska M. | - | Military University of Technology (PL) | Kowalewski Z.L. | - | IPPT PAN |
| 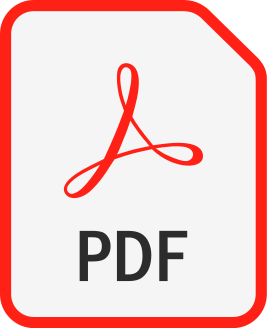 |
34. |
Chang S.♦, Wang K.♦, Wang B.♦, Kopeć M., Li Z.♦, Wang L.♦, Liu G.♦, Effects of rapid heating on non-equilibrium microstructure evolution and strengthening mechanisms of titanium alloy,
MATERIALS SCIENCE AND ENGINEERING A-STRUCTURAL MATERIALS PROPERTIES MICROSTRUCTURE AND PROCESSING, ISSN: 0921-5093, DOI: 10.1016/j.msea.2023.145337, No.145337, pp.1-33, 2023 Abstract: In this paper, the effects of heating parameters, including temperature ranging from 900 ℃ to 1000 ℃, heating rates ranging from 2 ℃∙s-1 to 100 ℃∙s-1, and 120 s soaking on the non-equilibrium microstructure evolution of Ti-6Al-4V alloy were studied. Microstructures after heating were characterized to reveal the mechanism of non-equilibrium phase transformation. Uniaxial tensile tests at room temperature were carried out to evaluate the effects of non-equilibrium microstructure on the mechanical properties. Results show that higher heating rate and lower temperature lead to lower β phase volume fraction and finer β grains. A transition region with element gradient forms in the αp grain near the αp/β phase boundary and transfers into β phase gradually during the heating. Rapid heating could confine the movement of the transition region, and therefore reduce the α→β transition and growth of the β phase. When the Ti-6Al-4V alloy was heated to 1000 ℃ at a rate of 50 ℃/s and then quenched immediately, the tensile strength was improved by 19.5% and reached up to 1263.0 MPa with the elongation only decreasing from 13.6% to 9.6% compared with the initial material. The main strengthening mechanism is that the rapid heating in the single-phase region avoids the rapid growth of the β phase, which leads to fully fine martensite formation after water quenching. Keywords: Rapid heating,Non-equilibrium microstructure,Mechanical properties,Strengthening mechanisms Affiliations:
Chang S. | - | Harbin Institiute of Technology (CN) | Wang K. | - | Imperial College London (GB) | Wang B. | - | other affiliation | Kopeć M. | - | IPPT PAN | Li Z. | - | other affiliation | Wang L. | - | Imperial College London (GB) | Liu G. | - | Harbin Institiute of Technology (CN) |
| 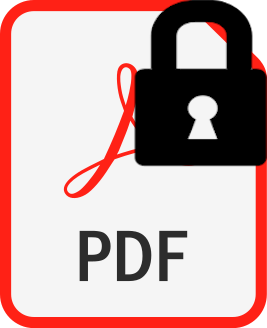 |
35. |
Kopeć M., Politis D.♦, Advances in Sheet Metal Forming Processes of Lightweight Alloys,
Materials, ISSN: 1996-1944, DOI: 10.3390/ma16093293, Vol.16, No.3293, pp.1-4, 2023, EDITORIAL Abstract: With the continuously growing need for more fuel-efficient and sustainable vehicles, the characterization and modeling of metal-forming processes have been indispensable in the development of new products. In the automotive and aviation sector, low-strength structural components are commonly produced from aluminum alloys, and higher-strength structural components are made from ultra-high-strength steels (UHSSs) and titanium alloys. The main issue experienced during the hot forming of complex-shaped components from difficult-to-form alloys is that they are time-, energy-, and cost-intensive. The aircraft industry currently uses methods such as superplastic forming (SPF), superplastic forming with diffusion bonding (SPF-DB), hot stretch forming, hot gas-pressure forming, and isothermal hot forming. Moreover, novel techniques have been developed to produce complex-shaped structural components including solution heat treatment, forming and in-die quenching (HFQ), quick-plastic forming, hot stamping using rapid heating, and fast light alloy stamping technology (FAST). Affiliations:
Kopeć M. | - | IPPT PAN | Politis D. | - | Imperial College London (GB) |
| 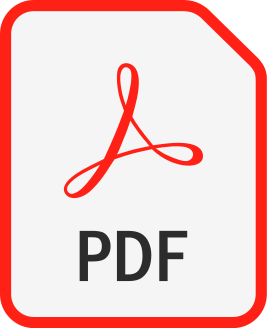 |
36. |
Kopeć M., Brodecki A., Kowalewski Z.L., Fatigue damage development in 10CrMo9-10 steel for power plant pipes in as-received state and after 280,000 h of exploitation,
ARCHIVES OF CIVIL AND MECHANICAL ENGINEERING, ISSN: 1644-9665, DOI: 10.1007/s43452-023-00637-3, Vol.23, No.98, pp.1-10, 2023 Abstract: This paper discusses an effect of 280,000 h of exploitation under internal pressure of 2.9 MPa and high temperature of 540 °C on the mechanical properties of 10CrMo9-10 (10H2M) power engineering steel. The mechanical response of the specimens obtained from two pipes: a new in the as-received state and exploited for a long period was assessed through the uniaxial tensile tests and subsequent fatigue tests. The long-term, high-temperature exposure of 10H2M steel resulted in the deterioration of its mechanical properties and was quantitatively described as a function of the fatigue damage measure, φ, and the fatigue damage parameter D. Finally, the proposed methodology of power exponent approximation with both damage sensitive parameters (φ, D) enabled for successful determination of the 10H2M steel fatigue life. Keywords: Fatigue,Damage development,10H2M steel,High-temperature aging Affiliations:
Kopeć M. | - | IPPT PAN | Brodecki A. | - | IPPT PAN | Kowalewski Z.L. | - | IPPT PAN |
| 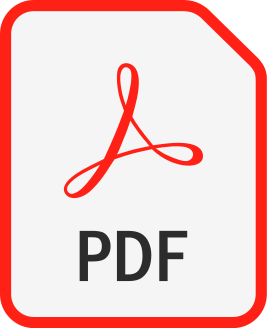 |
37. |
Brodecki A., Kopeć M., Kowalewski Z., Monitoring of fatigue damage development in as-received and exploited 10CrMo9-10 power engineering steel supported by Digital Image Correlation,
International Journal of Pressure Vessels and Piping, ISSN: 0308-0161, DOI: 10.1016/j.ijpvp.2023.104889, Vol.202, No.104889, pp.1-9, 2023 Abstract: This research aimed to compare the effect of long-time degradation of two different states of 10CrMo9-10 (10H2M) power engineering steel by using different experimental and analytical approaches. The specimens machined from the as-received steel and the same material after exploitation for 280 000 h at the temperature of 540 ◦C and the internal pressure of 2.9 MPa were subjected to fatigue loading that was simultaneously monitored by using the Digital Image Correlation (DIC) technique. The effect of long-time degradation on the mechanical response of 10H2M steel was studied through fractographic observations and was finally described as a function of the fatigue damage measure, φ, and the fatigue damage parameter D. Keywords: Fatigue development, Damage, 10H2M steel, Digital image correlation (DIC) Affiliations:
Brodecki A. | - | IPPT PAN | Kopeć M. | - | IPPT PAN | Kowalewski Z. | - | IPPT PAN |
| 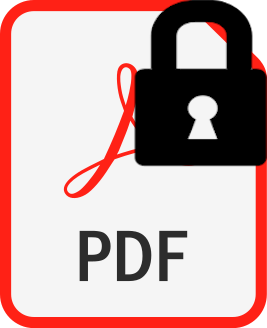 |
38. |
Szczęsny G.♦, Kopec M., Łukaszewicz A.♦, Kowalewski Z.L., Identification of the damage mechanism in orthopaedic implant. Case study including the biomechanical analysis,
INTERNATIONAL JOURNAL OF DAMAGE MECHANICS, ISSN: 1056-7895, DOI: 10.1177/10567895231215553, pp.1-12, 2023 Abstract: Implant breaking destabilizing the fracture may be caused by its structural defect, inappropriate use, or massive overloads. We present the patient, who broke the plate stabilizing comminuted clavicular fracture at the sixth postoperative week due to the, primarily reported, simple loading of the limb that should not exceeded admissible limits. Macroscopic examination excluded its manufacturing defect of an explant, but revealed areas of fatigue fractures, as well as anterior and inferior bending of its edges. Mechanical analysis proved sufficient material durability. Those findings clearly showed that the plate broke in consequence of repetitive overloads exceeding its durability. Patient, when acquitted with those results, confessed that the plate broke, while fishing. Moreover, he reported an episode of alcohol overuse that could contribute to implant failure bringing the risk of additional injury. Biomechanical analysis confirmed that mechanical loads throwing the spinner exceed values adequate for plate breaking. Thus, the real circumstances of the complication seem to be unveiled pointing out to facts that some patients disobey postoperative recommendations to avoid overloading of stabilized extremity, thus participating actively in this type of complications, that they dissemble the real circumstances of the complications, and that they may exhibit risky and irrational behavior. Basing on the presented case we concluded that in some cases plaster cast immobilization supporting stabilized fracture may be beneficial precluding banned activities and preventing from secondary injuries reducing the risk of postoperative complications. Keywords: clavicle fracture, implant failure, mechanical overloads, postoperative recommendations disobey, insubordinate patient Affiliations:
Szczęsny G. | - | Medical University of Warsaw (PL) | Kopec M. | - | IPPT PAN | Łukaszewicz A. | - | other affiliation | Kowalewski Z.L. | - | IPPT PAN |
| 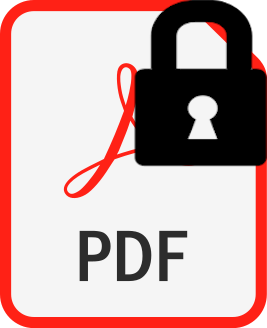 |
39. |
Łukaszewicz A.♦, Kopeć M., Szczęsny G.♦, Kowalewski Z.L., Characteristics of orthopaedic implants damage and mechanisms of its initiation,
INTERNATIONAL JOURNAL OF DAMAGE MECHANICS, ISSN: 1056-7895, DOI: 10.1177/10567895231212329, pp.1-19, 2023 Abstract: Implant fractures complicate orthopaedic procedures requiring secondary surgeries. However, it is not exactly known when the damage initiation starts and which factors predispose them to the highest degree. Thus, the aim of the study was to characterize changes observed in orthopaedic implants after their removal from the bone. Particular efforts were made to determine, which of them occur during the process of its production, installation, usage and removal. Such identification enabled to specify the role of lesions emerging during each period and their role in the implant’s deformation or fracture. The paper was focused on implants dedicated to the stabilization of the femur fractures since the bone transfers the highest loads. External surface and geometric features of eight representative implants were observed under standard and stereoscopic cameras, as well as under light and scanning electron microscopes. Macroscopic analysis of the investigated implants exhibited a number of defects in the form of scratches, abrasions, deformations and chipping. The wear degree of each implant was different and strictly depended on how it was implanted in the patient’s body, as well as on how the patient exploited it through his mobility. Four different sources of implant integrity changes were identified: manufacturingrelated changes, implant application-related changes, daily life-related changes and implant removalrelated changes. Keywords: Orthopaedic implants, implant’s destruction, intramedullary nail, bone plate, surface analysis, wear Affiliations:
Łukaszewicz A. | - | other affiliation | Kopeć M. | - | IPPT PAN | Szczęsny G. | - | Medical University of Warsaw (PL) | Kowalewski Z.L. | - | IPPT PAN |
| 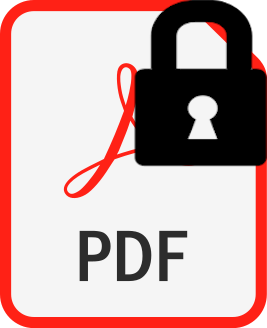 |
40. |
Kopeć M., Liu X.♦, Kukla D., Sitek R.♦, Kowalewski Z.L., Effect of printing direction on fatigue response and damage development in additive manufactured Haynes 282 nickel superalloy,
INTERNATIONAL JOURNAL OF DAMAGE MECHANICS, ISSN: 1056-7895, DOI: 10.1177/10567895231204951, pp.1-15, 2023 Abstract: In this paper, three different directions of 0°, 45° and 90° were used to manufacture the Haynes 282 alloy bars by using the Direct Metal Laser Sintering (DMLS) method. The additively manufactured specimens as well as these of the wrought Haynes 282 were subsequently subjected to comparative fatigue tests in the range of stress amplitude from ±400 MPa to ±800 MPa. The AM process enhanced the fatigue response of the nickel-based alloy in question by 200 MPa. Furthermore, it was found, that the printing direction does not affect the fatigue response of additively manufactured specimens significantly as minor differences in service life were observed for the entire stress amplitude range adopted. Finally, fatigue damage measure φ and fatigue damage parameter D approaches were used to reveal the dynamics of damage development and to monitor damage development due to fatigue. Keywords: Haynes 282, nickel alloys, fatigue, additive manufacturing, Direct Metal Laser Sintering (DMLS) Affiliations:
Kopeć M. | - | IPPT PAN | Liu X. | - | Imperial College London (GB) | Kukla D. | - | IPPT PAN | Sitek R. | - | Warsaw University of Technology (PL) | Kowalewski Z.L. | - | IPPT PAN |
| 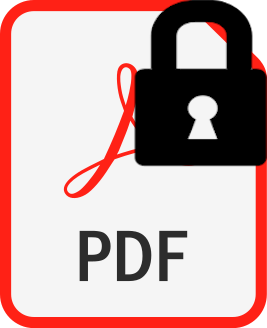 |
41. |
Kopeć M., Gorniewicz D.♦, Jóźwiak S.♦, Janiszewski J.♦, Kowalewski Z.L., Microstructural evolution of 6061 aluminium alloy subjected to static and dynamic compression at low temperature,
MRS Communications, ISSN: 2159-6867, DOI: 10.1557/s43579-023-00439-x, pp.1-8, 2023 Abstract: In this research, an effect of low temperature on the mechanical properties and microstructure of 6061-T6 aluminium alloy (AA6061-T6) subjected to static and dynamic loading was investigated systematically. The specimens were subjected to compression at the temperature of − 80°C in a range of strain rates from 0.001 to 0.1 1/s under static conditions, and from 1250 to 3400 1/s under dynamic conditions to compare their mechanical responses. The deformation mechanisms were discussed based on EBSD analysis. It was found, that under both testing conditions, dynamic recovery was the dominant mechanism responsible for material deformation. Affiliations:
Kopeć M. | - | IPPT PAN | Gorniewicz D. | - | Military University of Technology (PL) | Jóźwiak S. | - | Military University of Technology (PL) | Janiszewski J. | - | Military University of Technology (PL) | Kowalewski Z.L. | - | IPPT PAN |
| 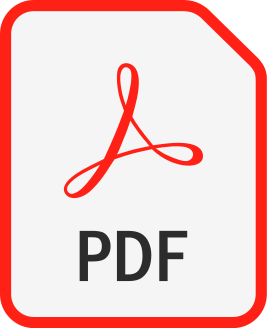 |
42. |
Macek W.♦, Branco R.♦, Podulka P.♦, Kopeć M., Zhu S.♦, Costa J.♦, A brief note on entire fracture surface topography parameters for 18Ni300 maraging steel produced by LB-PBF after LCF,
Engineering Failure Analysis, ISSN: 1350-6307, DOI: 10.1016/j.engfailanal.2023.107541, No.107541, pp.1-27, 2023 Abstract: The concept of entire fracture surface investigation is helpful in explaining fatigue phenomena. In this paper, this method has been applied for 18Ni300 maraging steel using a 3D measurement system. Before post-mortem analysis, the specimens produced by laser beam powder bed fusion (LB-PBF) were tested under low-cycle fatigue (LCF) for eight strain amplitudes in the interval 0.3% to 1.0%. The attention was placed on the relationship between the fatigue features, represented by the strain level and the fatigue life as well as the fracture surface topography evaluated in the form of areal, volume and fractal dimension parameters. It was found that fatigue life predictions calculated using the core material volume Vmc, obtained with the entire fracture surface method were within a scatter band with factors of ±1.5. The present results can be useful for the analysis of damaged structural elements exposed to LCF, especially for materials produced by additive manufacturing (AM). The outcomes of this brief note are important for the development of other fractographic methods and validation of fatigue life evaluation procedures. Keywords: 18Ni300 steel,laser beam powder bed fusion,low-cycle fatigue,surface metrology,entire fracture surface method,fractography,fractal dimension Affiliations:
Macek W. | - | other affiliation | Branco R. | - | other affiliation | Podulka P. | - | other affiliation | Kopeć M. | - | IPPT PAN | Zhu S. | - | other affiliation | Costa J. | - | other affiliation |
| 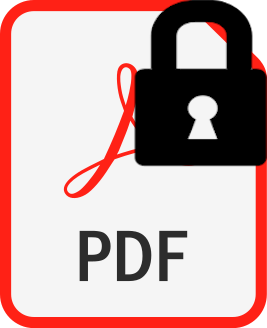 |
43. |
Kopeć M., Compression and Fatigue Testing of High‑Strength Thin Metal Sheets by Using an Anti-Buckling Device,
EXPERIMENTAL MECHANICS, ISSN: 0014-4851, DOI: 10.1007/s11340-023-00969-4, pp.1-11, 2023 Abstract: Background: The modelling of the sheet metal forming operations requires accurate and precise data of the material plastic be-haviour along non-proportional strain paths. However, the buckling phenomenon severely limits the compressive strain range that could be used to deform thin metal sheets. Objective: The main aim of this paper was to propose an effective device, that ena-bles to determine of accurate stress-strain characteristics of thin metal sheet specimens subjected to axial deformation without buckling and with a special emphasis on friction correction. Methods: In this paper, an anti-buckling fixture was proposed to as-sess the deformation characteristics of X10CrMoVNb9-1 (P91) power engineering steel, and DP500 and DP980 dual-phase steels, under compression loading. The fixture enables monitoring of the friction between the specimen and supporting blocks during the test, and thus the precise stress response of the material could be determined. Results: The effectiveness of the fixture was evalu-ated under tension-compression cyclic loading and during the compression tests in which high-strength thin metal sheets were successfully deformed up to 10% without specimen buckling. Furthermore, the successful determination of a friction force varia-tion between supporting blocks and the specimen during tests enabled to determine an actual force acting on the specimen. Con-clusions: The proposed testing fixture was successfully assessed during the compression and cyclic tension-compression of high-strength thin metal sheets as no buckling was observed. Its advantage lies in adapting to change its length with specimen elongation or shrinkage during a test. The friction force generated from a movement of both parts of the device could be effec-tively monitored by the special strain gauge system during testing and thus its impact on the stress-strain characteristics could be successfully eliminated. Keywords: buckling, fatigue, compression, mechanical testing, thin sheets Affiliations:
| 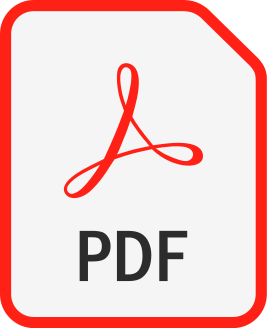 |
44. |
Barwińska I., Kopeć M., Kukla D., Senderowski C.♦, Kowalewski Z.L., Thermal Barrier Coatings for High-Temperature Performance of Nickel-Based Superalloys: A Synthetic Review,
Coatings, ISSN: 2079-6412, DOI: 10.3390/coatings13040769, Vol.13, No.4, pp.1-21, 2023 Abstract: With the rising demands of industry to increase the working temperature of gas turbine blades and internal combustion engines, thermal barrier coatings (TBC) were found to be an effective way to further enhance the lifetime of aero components through the improvement of mechanical properties and oxidation-resistance. Thus, this paper aims to review coating technologies with special emphasis on plasma-sprayed thermal barrier coatings (PS), and those produced by physical vapor deposition (PVD) and chemical vapor deposition (CVD) methods. Each technology was assessed in terms of its effectiveness to enhance the mechanical response and oxidation resistance of nickel-based parts working at high temperature. The effect of coating technology on mechanical strength, hardness, fatigue and creep of nickel alloys was discussed to reveal the potential candidates for future applications in aggressive environments Keywords: high temperature corrosion, fatigue, creep, aggressive environment, turbine blade Affiliations:
Barwińska I. | - | IPPT PAN | Kopeć M. | - | IPPT PAN | Kukla D. | - | IPPT PAN | Senderowski C. | - | other affiliation | Kowalewski Z.L. | - | IPPT PAN |
| 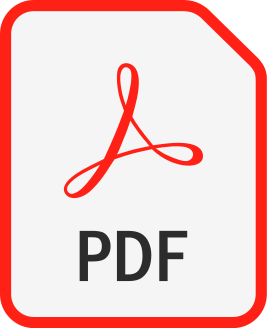 |
45. |
Barwińska I., Kopeć M., Kukla D., Łazińska M.♦, Sitek R.♦, Kowalewski Z., Effect of Aluminizing on the Fatigue and High-Temperature Corrosion Resistance of Inconel 740 Nickel Alloy,
The Journal of The Minerals, ISSN: 1047-4838, DOI: 10.1007/s11837-022-05662-w, Vol.75, No.2, pp.1-13, 2023 Abstract: The fatigue response and high-temperature corrosion resistance of Inconel 740 nickel alloy in its as-received state, and the same material with aluminized surface layer, were investigated. The aluminized layer was applied by using the chemical vapor deposition process with the participation of AlCl3 vapors under a hydrogen protective atmosphere at a temperature of 1040°C for 8 h and internal pressure of 150 hPa. The microstructure of the aluminized layer was characterized through scanning electron microscopy and x-ray energy dispersive spectroscopy analysis. It was found that Inconel 740 with an aluminized surface exhibited an improved hardness and fatigue response of 100 MPa in the whole range of stress amplitudes from 350 MPa to 650 MPa. Additionally, the application of the aluminization process enhanced service life as well as the corrosion resistance of the alloy in question and effectively protected it against high-temperature corrosion. Affiliations:
Barwińska I. | - | IPPT PAN | Kopeć M. | - | IPPT PAN | Kukla D. | - | IPPT PAN | Łazińska M. | - | Military University of Technology (PL) | Sitek R. | - | Warsaw University of Technology (PL) | Kowalewski Z. | - | IPPT PAN |
| 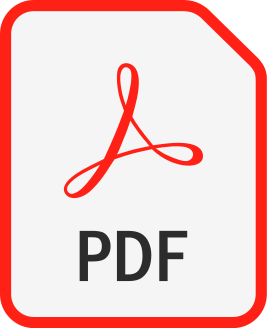 |
46. |
Kopeć M., Fatigue Damage Development in 14MoV6-3 Steel for Power Plant Pipes Monitored by Digital Image Correlation,
Acta Mechanica Solida Sinica, ISSN: 0894-9166, DOI: 10.1007/s10338-023-00387-y, pp.1-13, 2023 Abstract: In this paper, fatigue damage development of 14MoV6-3 (13HMF) power engineering steel was studied through different experimental and analytical approaches. The specimens machined from the as-received pipe were subjected to fatigue loading and simultaneously monitored using the digital image correlation (DIC) technique. The damage development was analysed through microstructural observations of fracture surfaces and further described as a function of the fatigue damage parameter D and the fatigue damage measure φ. The combination of such parameters’ evolution with the number of cycles to failure and the DIC technique enables a determination of separate stages of damage development. It was found that dynamics of damage could be effectively exposed within the first 100 cycles. Keywords: Fatigue development, Damage, 13HMF steel, Digital image correlation (DIC) Affiliations:
| 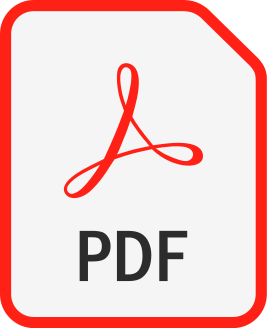 |
47. |
Kopeć M., Garbacz G.♦, Brodecki A., Kowalewski Z.L., Metric entropy and digital image correlation in deformation dynamics analysis of fibre glass reinforced composite under uniaxial tension,
MEASUREMENT, ISSN: 0263-2241, DOI: 10.1016/j.measurement.2022.112196, Vol.205, No.112196, pp.1-6, 2022 Abstract: This paper proposes a combined method for the mechanical properties assessment of composite materials based on the analysis of the internal dynamics of raw data from uniaxial tensile tests. Determination of the Kolmogorov-Sinai (K-S) metric entropy from the recorded data enables to find the tensile strength of materials. The correctness of the methodology proposed was verified by the full filed DIC measurements. Therefore, the main aim of this research was to apply independent measurement tools in the analysis of the non-linear dynamics supported by their mutual validation. The experimental program carried out on the glass fibre-based thermoplastic Elium acrylic composite and E752 Carbon Fiber Reinforced Epoxy (CFRE) composite confirmed the high suitability of the presented methodology in ultimate tensile stress identification, and thus, its great applicability potential in many aspects of the contemporary engineering. Keywords: Digital image correlation (DIC), Kolmogorov-Sinai metric entropy, Mechanical properties, Glass fibre composites Affiliations:
Kopeć M. | - | IPPT PAN | Garbacz G. | - | other affiliation | Brodecki A. | - | IPPT PAN | Kowalewski Z.L. | - | IPPT PAN |
| 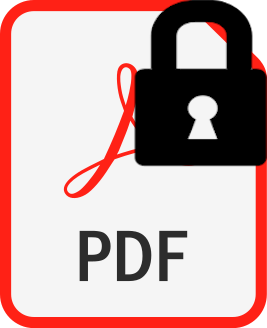 |
48. |
Kopeć M., Kowalewski Z.L., Deformation of thin metal and composite sheets by using anti-buckling fixture for large deformation under tension–compression cyclic loading,
Thin-Walled Structures, ISSN: 0263-8231, DOI: 10.1016/j.tws.2022.109886, Vol.180, pp.109886-1-5, 2022 Abstract: In this paper, an anti-buckling fixture was proposed to assess the deformation characteristics of DP500 and DP980 dual-phase steels, and AZ31B magnesium composite under tension–compression cyclic loading. The advantage of the device lies in the possibility of monitoring friction between the specimen and supporting blocks during the test. In consequence, it allows to avoid an error during stress determination. The full cyclic loading capacity for each material can be executed at the displacement amplitude within the range ±2.5 mm which corresponds to the maximum strain amplitude of ±0.2 for the specimen with the gauge length of 21.5 mm. It is concluded, that the technique proposed is promising since the thin sheet material can be tested under tension–compression in a wide range of deformation without the buckling effect. Furthermore, useful data for modelling cyclic deformation behaviour for shell structures can be obtained. Keywords: buckling, cyclic loading, fixture, thin sheets, metal forming Affiliations:
Kopeć M. | - | IPPT PAN | Kowalewski Z.L. | - | IPPT PAN |
| 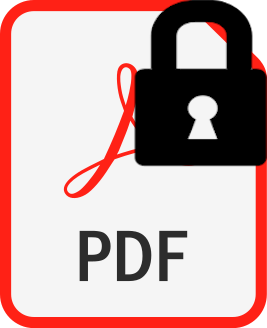 |
49. |
Liu X.♦, Di B.♦, Yu X.♦, Liu H.♦, Dhawan S.♦, Politis D.J.♦, Kopeć M., Wang L.♦, Development of a Formability Prediction Model for Aluminium Sandwich Panels with Polymer Core,
Materials, ISSN: 1996-1944, DOI: 10.3390/ma15124140, Vol.15, No.12, pp.4140-1-12, 2022 Abstract: In the present work, the compatibility relationship on the failure criteria between aluminium and polymer was established, and a mechanics-based model for a three-layered sandwich panel was developed based on the M-K model to predict its Forming Limit Diagram (FLD). A case study for a sandwich panel consisting of face layers from AA5754 aluminium alloy and a core layer from polyvinylidene difluoride (PVDF) was subsequently conducted, suggesting that the loading path of aluminium was linear and independent of the punch radius, while the risk for failure of PVDF increased with a decreasing radius and an increasing strain ratio. Therefore, the developed formability model would be conducive to the safety evaluation on the plastic forming and critical failure of composite sandwich panels. Keywords: formability, M-K model, failure criteria, composite sandwich panel Affiliations:
Liu X. | - | Imperial College London (GB) | Di B. | - | Imperial College London (GB) | Yu X. | - | Imperial College London (GB) | Liu H. | - | Imperial College London (GB) | Dhawan S. | - | Imperial College London (GB) | Politis D.J. | - | Imperial College London (GB) | Kopeć M. | - | IPPT PAN | Wang L. | - | Imperial College London (GB) |
| 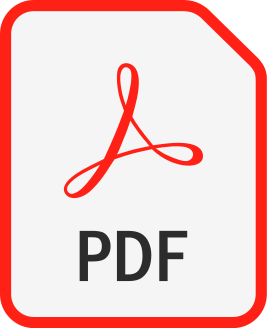 |
50. |
Szczęsny G.♦, Kopeć M., Politis D.J.♦, Kowalewski Z.L., Łazarski A.♦, Szolc T., A review on biomaterials for orthopaedic surgery and traumatology: from past to present,
Materials, ISSN: 1996-1944, DOI: 10.3390/ma15103622, Vol.15, No.10, pp.3622-1-20, 2022 Abstract: The principal features essential for the success of an orthopaedic implant are its shape, dimensional accuracy, and adequate mechanical properties. Unlike other manufactured products, chemical stability and toxicity are of increased importance due to the need for biocompatibility over an implants life which could span several years. Thus, the combination of mechanical and biological properties determines the clinical usefulness of biomaterials in orthopaedic and musculoskeletal trauma surgery. Materials commonly used for these applications include stainless steel, cobalt-chromium and titanium alloys, ceramics, polyethylene, and poly(methyl methacrylate) (PMMA) bone cement. This study reviews the properties of commonly used materials and the advantages and disadvantages of each, with special emphasis on the sensitivity, toxicity, irritancy, and possible mutagenic and teratogenic capabilities. In addition, the production and final finishing processes of implants are discussed. Finally, potential directions for future implant development are discussed, with an emphasis on developing advanced personalised implants, according to a patient’s stature and physical requirements. Keywords: orthopaedic surgical procedures, biomaterials, implants, biocompatible materials, alloys, ceramic, polyethylene Affiliations:
Szczęsny G. | - | Medical University of Warsaw (PL) | Kopeć M. | - | IPPT PAN | Politis D.J. | - | Imperial College London (GB) | Kowalewski Z.L. | - | IPPT PAN | Łazarski A. | - | Medical University of Warsaw (PL) | Szolc T. | - | IPPT PAN |
| 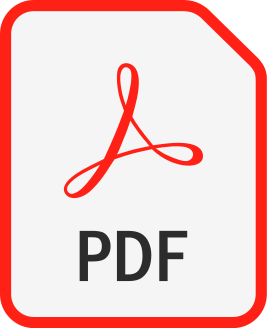 |
51. |
Kopeć M., Gorniewicz D.♦, Kukla D., Barwińska I., Jóźwiak S.♦, Sitek R.♦, Kowalewski Z.L., Effect of plasma nitriding process on the fatigue and high temperature corrosion resistance of Inconel 740H nickel alloy,
ARCHIVES OF CIVIL AND MECHANICAL ENGINEERING, ISSN: 1644-9665, DOI: 10.1007/s43452-022-00381-0, pp.57-1-15, 2022 Abstract: The paper presents a comparison of microhardness, fatigue and high temperature corrosion of Inconel 740H nickel alloy in its as-received state and the same material with nitrided surface layers. The nitrided layers were produced using traditional glow discharge nitriding (specimens nitriding on the cathode potential) and an active screen (specimens nitriding at the plasma potential). A microstructure of the layers was characterized through the scanning electron microscopy, X-ray energy dispersive spectroscopy and X-ray diffraction analysis. Mechanical properties of the nitrided Inconel 740H alloy were examined using microhardness measurements and standard fatigue tests. It was found that Inconel 740H with a nitrided surface exhibited an improved fatigue response of 50 MPa in the whole range of stress amplitudes from 350 to 650 MPa and almost 325% increase of hardness for plasma modified surface and 250% for cathode modified surface. Additionally, the application of cathode nitriding enhanced the corrosion resistance of the alloy in question and effectively protected it against a high temperature oxidation. Keywords: nitriding, nickel alloys, coatings, fatigue, corrosion Affiliations:
Kopeć M. | - | IPPT PAN | Gorniewicz D. | - | Military University of Technology (PL) | Kukla D. | - | IPPT PAN | Barwińska I. | - | IPPT PAN | Jóźwiak S. | - | Military University of Technology (PL) | Sitek R. | - | Warsaw University of Technology (PL) | Kowalewski Z.L. | - | IPPT PAN |
| 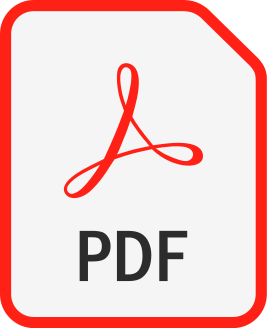 |
52. |
Kopeć M., The stress and strain distribution in X10CrMoVNb9-1 power engineering steel after long time degradation studied by the ESPI system,
BULLETIN OF THE POLISH ACADEMY OF SCIENCES: TECHNICAL SCIENCES, ISSN: 0239-7528, DOI: 10.24425/bpasts.2022.141181, Vol.70, No.2, pp.1-7, 2022 Abstract: Maintenance of assets and equipment in power plants is essential for their safety and is required to help the plant stay active. In this paper, the specimens manufactured from the pipe of X10CrMoVNb9-1 (P91) power engineering steel in the as-received state and after operating for 80 000 h at internal pressure of 8.4 MPa and temperature of 540ºC were subjected to tests using electronic speckle pattern interferometry (ESPI) under static loading up to 2.5 kN. Such a procedure enables assessment of strain and stress distribution maps to compare the material integrity in the as-received state and after exploitation in its elastic range. The conducted measurements showed no effect of long time operation on the mechanical response of P91 steel under the power installations conditions since the field strain distributions for each type of specimen were found to be similar. Keywords: damage, P91 steel, electronic speckle pattern interferometry (ESPI), optical measurements Affiliations:
| 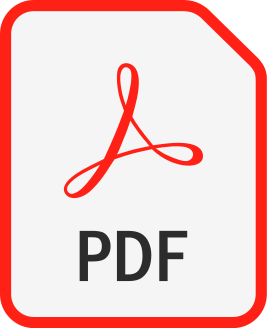 |
53. |
Kukla D., Kopeć M., Gradzik A.♦, Identification and characterization of the grinding burns by eddy current method,
Open Engineering , ISSN: 2391-5439, DOI: 10.1515/eng-2022-0382, Vol.12, pp.1-5, 2022 Abstract: This work presents an attempt to identify local
changes in materials caused by local grinding burnings
by using the eddy current (EC) method. The locally heattreated AISI 9310 steel specimen was prepared by using a
laser surfacing process to imitate three different grinding burns. These burn marks were characterized in terms of changes in microstructure and hardness on the surface and cross-section of the specimen. On such a basis, the depth of the heat-affected zone caused by the grinding tool was examined. Subsequently, the specimen was subjected to the EC measurements for the quantitative description of the signal from each of the defects by using a commercial NORTEC 600D flaw detector working in specimen Q5 scanning mode and with a pencil probe. The changes in the amplitude and the phase angle of the signal from three defects indicate the possibility to identify burns along with their quantitative description and subsequent estimation of their depth. The differences in the phase angle value, related to the local changes in the stress state, serve as an effective indicator of the specimen overheating degree in the area of the EC induction Keywords: eddy current,non-destructive testing,hardness,heat-treatment Affiliations:
Kukla D. | - | IPPT PAN | Kopeć M. | - | IPPT PAN | Gradzik A. | - | Rzeszów University of Technology (PL) |
| 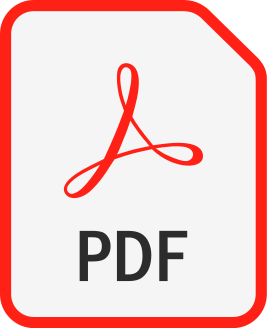 |
54. |
Szczęsny G.♦, Kopeć M., Szolc T., Kowalewski Z.L., Małdyk P.♦, Deformation of the Titanium Plate Stabilizing the Lateral Ankle Fracture Due to Its Overloading in Case of the Young, Obese Patient: Case Report Including the Biomechanical Analysis,
Diagnostics, ISSN: 2075-4418, DOI: 10.3390/diagnostics12061479, Vol.12, No.6, pp.1479-1-10, 2022 Abstract: The number of overweight and obese patients in developed countries is gradually increasing. It was reported that 1287 (64%) out of 2007 adults operated on in 2017 had a body mass index (BMI) greater than 25 kg/m2, and 26.4% even greater than 30, while the BMI of the most obese patient was as high as 57.6 kg/m2. Such distressing statistics raised an issue related to the inadequate durability of implants used for the fixation of bone fractures. Implants for the lower-extremity fractures may not be durable enough to fit the requirements of overweight and obese patients. This case report presents the history of a 23-year-old obese male with a BMI of 38.7, who bent the angularly stabile titanium plate stabilizing his broken lateral ankle and torn distal tibiofibular syndesmosis. Biomechanical analysis showed that the maximal static bending moment registered during one-leg standing was equal to 1.55 Nm. This value was circa one-third of the maximally admissible bending moment for this particular plate (5.34 Nm) that could be transmitted without its plastic deformation. Since dynamic forces exceed static ones several (3–12) times during typical activities, such as walking, climbing the stairs, running, and jumping, unpredictable forces may occur and increase the risk of loosening, bending, and even breaking implants. None of these situations should have occurred for the typical patient’s body mass of 75 kg, or even for the analyzed mass of the young patient (120 kg) who tried to avoid excessive loading during his daily routine. Subsequent implant bending and destabilization of the fracture shows that for the significantly high and still growing number of obese patients, a very strict physical regime should be recommended to prevent overabundant dynamic loads. On the other hand, the geometry of implants dedicated to these patients should be reconsidered. Keywords: ankle injuries surgery, bone plate, obesity, postoperative complications, implant failure Affiliations:
Szczęsny G. | - | Medical University of Warsaw (PL) | Kopeć M. | - | IPPT PAN | Szolc T. | - | IPPT PAN | Kowalewski Z.L. | - | IPPT PAN | Małdyk P. | - | Medical University of Warsaw (PL) |
| 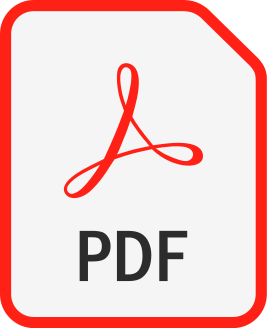 |
55. |
Kopeć M., Kukla D., Kowalewski Z.L., Assessment of fatigue life of aluminized, coarse-grained MAR247 alloy supported by full-field espi measurements,
JOURNAL OF THEORETICAL AND APPLIED MECHANICS, ISSN: 1429-2955, DOI: 10.15632/jtam-pl/153041, Vol.60, No.4, pp.619-623, 2022 Abstract: In this paper, fatigue performance of an aluminide layer coated, coarse-grained MAR247 nickel superalloy was monitored by using the full-field Electronic Speckle Pattern Interferometry (ESPI) method in the range of stress amplitude from 350MPa to 650MPa. It was found, that the ESPI method enables precise monitoring of the fatigue behaviour of coated MAR247 specimens since the area of potential failure was accurately indicated within the initial stage of fatigue damage development. Keywords: fatigue development, damage, nickel alloys, electronic speckle pattern interferometry Affiliations:
Kopeć M. | - | IPPT PAN | Kukla D. | - | IPPT PAN | Kowalewski Z.L. | - | IPPT PAN |
| 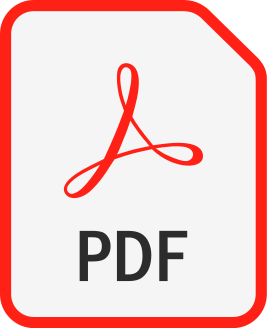 |
56. |
Barwińska I., Kopeć M., Łazińska M.♦, Brodecki A., Durejko T.♦, Kowalewski Z.L., Three Point Bending of Laser Engineered Net Shaping (LENS) Repaired Inconel 625,
Physical Science Forum, ISSN: 2673-9984, DOI: 10.3390/psf2022004001, Vol.4, No.1, pp.1-7, 2022 Abstract: In this paper, the LENS technique with optimized parameters was applied to investigate the feasibility of Inconel 625 repair process. The process was performed on the substrate material heated to 300 ◦C at laser power of 550 W. Subsequently, the specimens were subjected to microhardness and three-point bending tests to assess the effectiveness of the repair system. The results showed that the mechanical properties of the Inconel 625 specimens repaired by using the LENS system were similar or even better than those of the substrate material. Keywords: LENS technology, Inconel alloys, repair process, additive manufacturing Affiliations:
Barwińska I. | - | IPPT PAN | Kopeć M. | - | IPPT PAN | Łazińska M. | - | Military University of Technology (PL) | Brodecki A. | - | IPPT PAN | Durejko T. | - | Military University of Technology (PL) | Kowalewski Z.L. | - | IPPT PAN |
| 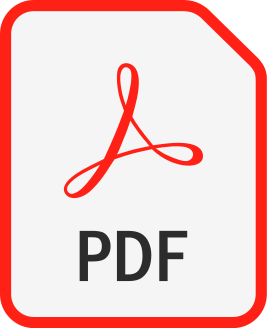 |
57. |
Senderowski C.♦, Panas A.J.♦, Fikus B.♦, Zasada D.♦, Kopeć M., Korytchenko K.V.♦, Effects of heat and momentum gain differentiation during gas detonation spraying of FeAl powder particles into the water,
Materials, ISSN: 1996-1944, DOI: 10.3390/ma14237443, Vol.14, No.23, pp.7443-1-18, 2021 Abstract: In this paper, dynamic interactions between the FeAl particles and the gaseous detonation stream during supersonic D-gun spraying (DGS) conditions into the water are discussed in detail. Analytical and numerical models for the prediction of momentum and complex heat exchange, that includes radiative effects of heat transfer between the FeAl particle and the D-gun barrel wall and phase transformations due to melting and evaporation of the FeAl phase, are analyzed. Phase transformations identified during the DGS process impose the limit of FeAl grain size, which is required to maintain a solid state of aggregation during a collision with the substrate material. The identification of the characteristic time values for particle acceleration in the supersonic gas detonation flux, their convective heating and heat diffusion enable to assess the aggregation state of FeAl particles sprayed into water under certain DGS conditions Keywords: D-gun spraying, FeAl intermetallic powder, gas detonation flux, heat transfer, two-phase metallization stream, particle thermal history Affiliations:
Senderowski C. | - | other affiliation | Panas A.J. | - | other affiliation | Fikus B. | - | other affiliation | Zasada D. | - | other affiliation | Kopeć M. | - | IPPT PAN | Korytchenko K.V. | - | other affiliation |
| 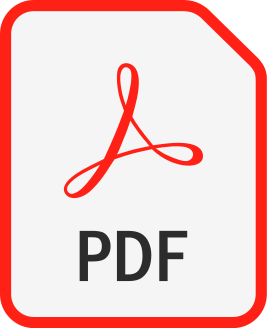 |
58. |
Barwińska I., Kopeć M., Łazińska M.♦, Brodecki A., Durejko T.♦, Kowalewski Z.L., Suitability of laser engineered net shaping technology for Inconel 625 based parts repair process,
Materials, ISSN: 1996-1944, DOI: 10.3390/ma14237302, Vol.14, No.23, pp.7302-1-14, 2021 Abstract: In this paper, the Inconel 625 laser clads characterized by microstructural homogeneity due to the application of the Laser Engineered Net Shaping (LENS, Optomec, Albuquerque, NM, USA) technology were studied in detail. The optimized LENS process parameters (laser power of 550 W, powder flow rate of 19.9 g/min, and heating of the substrate to 300 °C) enabled to deposit defect-free laser cladding. Additionally, the laser clad was applied in at least three layers on the repairing place. The deposited laser clads were characterized by slightly higher mechanical properties in comparison to the Inconel 625 substrate material. Microscopic observations and X-ray Tomography (XRT, Nikon Corporation, Tokyo, Japan) confirmed, that the substrate and cladding interface zone exhibited a defect-free structure. Mechanical properties and flexural strength of the laser cladding were examined using microhardness and three-point bending tests. It was concluded, that the LENS technology could be successfully applied for the repair since a similar strain distribution was found after Digital Image Correlation measurements during three-point bending tests. Keywords: LENS technology, Inconel alloys, repair process, additive manufacturing Affiliations:
Barwińska I. | - | IPPT PAN | Kopeć M. | - | IPPT PAN | Łazińska M. | - | Military University of Technology (PL) | Brodecki A. | - | IPPT PAN | Durejko T. | - | Military University of Technology (PL) | Kowalewski Z.L. | - | IPPT PAN |
| 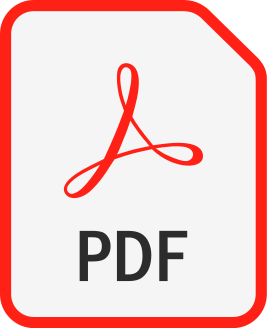 |
59. |
Kopeć M., Brodecki A., Kukla D., Kowalewski Z.L., Suitability of DIC and ESPI optical methods for monitoring fatigue damage development in X10CrMoVNb9-1 power engineering steel,
ARCHIVES OF CIVIL AND MECHANICAL ENGINEERING, ISSN: 1644-9665, DOI: 10.1007/s43452-021-00316-1, Vol.21, pp.167-1-13, 2021 Abstract: The aim of this research was to compare the effectiveness of two different optical measurement techniques (digital image correlation—DIC and electronic speckle pattern interferometry—ESPI) during fatigue damage development monitoring in X10CrMoVNb9-1 (P91) power engineering steel for pipes. The specimens machined from the as-received pipe were subjected to fatigue loadings and monitored simultaneously using DIC and ESPI techniques. It was found that DIC technique, although characterised by lower resolution, was more effective than ESPI. DIC allows to monitor the fatigue behaviour of steel specimens and accurately indicate the area of potential failure even within the initial stage of fatigue damage development. Keywords: fatigue development, damage, P91 steel, digital image correlation (DIC), electronic speckle pattern interferometry (ESPI) Affiliations:
Kopeć M. | - | IPPT PAN | Brodecki A. | - | IPPT PAN | Kukla D. | - | IPPT PAN | Kowalewski Z.L. | - | IPPT PAN |
| 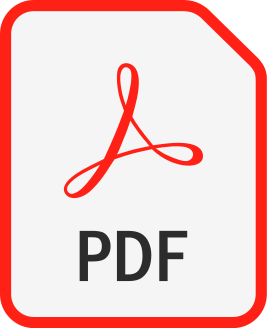 |
60. |
Gorniewicz D.♦, Przygucki H.♦, Kopeć M., Karczewski K.♦, Jóźwiak S.♦, TiCoCrFeMn (BCC + C14) high-entropy alloy multiphase structure analysis based on the theory of molecular orbitals,
Materials, ISSN: 1996-1944, DOI: 10.3390/ma14185285, Vol.14, No.18, pp.5285-1-16, 2021 Abstract: High-entropy alloys (HEA) are a group of modern, perspective materials that have been intensively developed in recent years due to their superior properties and potential applications in many fields. The complexity of their chemical composition and the further interactions of main elements significantly inhibit the prediction of phases that may form during material processing. Thus, at the design stage of HEA fabrication, the molecular orbitals theory was proposed. In this method, the connection of the average strength of covalent bonding between the alloying elements (Bo parameter) and the average energy level of the d-orbital (parameter Md) enables for a preliminary assessment of the phase structure and the type of lattice for individual components in the formed alloy. The designed TiCoCrFeMn alloy was produced by the powder metallurgy method, preceded by mechanical alloying of the initial elementary powders and at the temperature of 1050 °C for 60 s. An ultra-fine-grained structured alloy was homogenized at 1000 °C for 1000 h. The X-ray diffraction and scanning electron microscopy analysis confirmed the correctness of the methodology proposed as the assumed phase structure consisted of the body-centered cubic (BCC) solid solution and the C14 Laves phase was obtained. Keywords: HEA, solid solution, laves phase, U-FAST sintering Affiliations:
Gorniewicz D. | - | Military University of Technology (PL) | Przygucki H. | - | other affiliation | Kopeć M. | - | IPPT PAN | Karczewski K. | - | Military University of Technology (PL) | Jóźwiak S. | - | Military University of Technology (PL) |
| 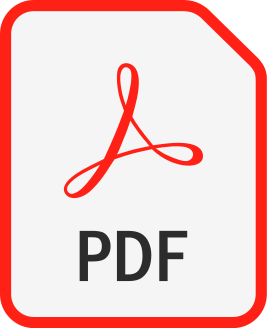 |
61. |
Kukla D., Kopeć M., Wang K.♦, Senderowski C.♦, Kowalewski Z.L., Nondestructive methodology for identification of local discontinuities in aluminide layer-coated Mar 247 during its fatigue performance,
Materials, ISSN: 1996-1944, DOI: 10.3390/ma14143824, Vol.14, No.14, pp.3824-1-13, 2021 Abstract: In this paper, the fatigue performance of the aluminide layer-coated and as-received MAR 247 nickel superalloy with three different initial microstructures (fine grain, coarse grain and column-structured grain) was monitored using nondestructive, eddy current methods. The aluminide layers of 20 and 40 µm were obtained through the chemical vapor deposition (CVD) process in the hydrogen protective atmosphere for 8 and 12 h at the temperature of 1040 °C and internal pressure of 150 mbar. A microstructure of MAR 247 nickel superalloy and the coating were characterized using light optical microscopy (LOM), scanning electron microscopy (SEM) and X-ray energy dispersive spectroscopy (EDS). It was found that fatigue performance was mainly driven by the initial microstructure of MAR 247 nickel superalloy and the thickness of the aluminide layer. Furthermore, the elaborated methodology allowed in situ eddy current measurements that enabled us to localize the area with potential crack initiation and its propagation during 60,000 loading cycles. Keywords: chemical vapor deposition, nickel alloys, aluminide coatings, fatigue, eddy current Affiliations:
Kukla D. | - | IPPT PAN | Kopeć M. | - | IPPT PAN | Wang K. | - | Imperial College London (GB) | Senderowski C. | - | other affiliation | Kowalewski Z.L. | - | IPPT PAN |
| 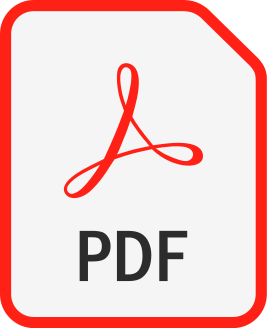 |
62. |
Kopeć M., Brodecki A., Szczęsny G.♦, Kowalewski Z.L., Microstructural analysis of fractured orthopedic implants,
Materials, ISSN: 1996-1944, DOI: 10.3390/ma14092209, Vol.14, No.9, pp.2209-1-17, 2021 Abstract: In this paper, fracture behavior of four types of implants with different geometries (pure titanium locking plate, pure titanium femoral implant, Ti-6Al-4V titanium alloy pelvic implant, X2CrNiMo18 14-3 steel femoral implant) was studied in detail. Each implant fractured in the human body. The scanning electron microscopy (SEM) was used to determine the potential cause of implants fracture. It was found that the implants fracture mainly occurred in consequence of mechanical overloads resulting from repetitive, prohibited excessive limb loads or singular, un-intendent, secondary injures. Among many possible loading types, the implants were subjected to an excessive fatigue loads with additional interactions caused by screws that were mounted in their threaded holes. The results of this work enable to conclude that the design of orthopedic implants is not fully sufficient to transduce mechanical loads acting over them due to an increasing weight of treated patients and much higher their physical activity. Keywords: medical fixation devices, orthopedic prostheses and implants, titanium, titanium alloy, stainless steel, microscopic fracture analysis Affiliations:
Kopeć M. | - | IPPT PAN | Brodecki A. | - | IPPT PAN | Szczęsny G. | - | Medical University of Warsaw (PL) | Kowalewski Z.L. | - | IPPT PAN |
| 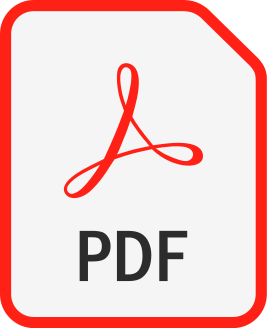 |
63. |
Kukla D., Kopeć M., Sitek R.♦, Olejnik A.♦, Kachel S.♦, Kiszkowiak Ł.♦, A novel method for high temperature fatigue testing of nickel superalloy turbine blades with additional NDT diagnostics,
Materials, ISSN: 1996-1944, DOI: 10.3390/ma14061392, Vol.14, No.6, pp.1392-1-17, 2021 Abstract: In this paper, a novel method for high temperature fatigue strength assessment of nickel superalloy turbine blades after operation at different times (303 and 473 h) was presented. The studies included destructive testing (fatigue testing at temperature 950 °C under cyclic bending load), non-destructive testing (Fluorescent Penetrant Inspection and Eddy Current method), and finite element modelling. High temperature fatigue tests were performed within load range from 5200 to 6600 N using a special self-designed blade grip attached to the conventional testing machine. The experimental results were compared with the finite element model generated from the ANSYS software. It was found that failure of turbine blades occurred in the area with the highest stress concertation, which was accurately predicted by the finite element (FE) model. Keywords: nickel superalloys, high temperature fatigue, finite element (FE) modelling, eddy current Affiliations:
Kukla D. | - | IPPT PAN | Kopeć M. | - | IPPT PAN | Sitek R. | - | Warsaw University of Technology (PL) | Olejnik A. | - | other affiliation | Kachel S. | - | other affiliation | Kiszkowiak Ł. | - | other affiliation |
| 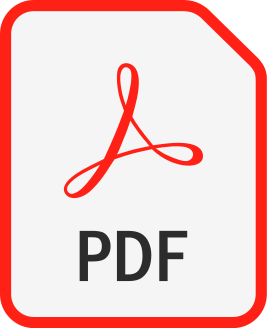 |
64. |
Kopeć M., Kukla D., Brodecki A., Kowalewski Z.L., Effect of high temperature exposure on the fatigue damage development of X10CrMoVNb9-1 steel for power plant pipes,
International Journal of Pressure Vessels and Piping, ISSN: 0308-0161, DOI: 10.1016/j.ijpvp.2020.104282, Vol.189, pp.104282-1-16, 2021 Abstract: The aim of this research was to compare the effect of 80 000 h exploitation time in high temperature on mechanical properties and microstructure of X10CrMoVNb9-1 (P91) power engineering steel for pipes. The specimens obtained from two pipes: new, as-received and after exploitation were subjected to fatigue loadings to compare their mechanical responses. Additionally, the uniaxial tensile tests on both types of P91 steel were performed. The microstructure evolution before and after deformation was monitored using optical and scanning electron microscopy. The time intensive, high temperature exposure of P91 power engineering steel led to significant phase transformation and subsequent deterioration of mechanical properties and was further described as a function of the fatigue damage measure, φ, and the fatigue damage parameter D. Further proposed methodology of power exponent approximation of the fatigue damage measure, φ, and fatigue damage parameter D, allowed to successfully determine the fatigue life of P91 steel. Keywords: fatigue development, damage, P91 steel, microstructure Affiliations:
Kopeć M. | - | IPPT PAN | Kukla D. | - | IPPT PAN | Brodecki A. | - | IPPT PAN | Kowalewski Z.L. | - | IPPT PAN |
| 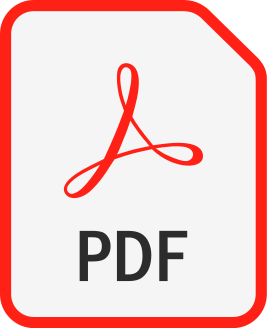 |
65. |
Kopeć M., Kukla D., Yuan X.♦, Rejmer W.♦, Kowalewski Z.L., Senderowski C.♦, Aluminide thermal barrier coating for high temperature performance of MAR 247 nickel based superalloy,
Coatings, ISSN: 2079-6412, DOI: 10.3390/coatings11010048, Vol.11, No.1, pp.48-1-12, 2021 Abstract: In this paper, mechanical properties of the as-received and aluminide layer coated MAR 247 nickel based superalloy were examined through creep and fatigue tests. The aluminide layer of 20 µm was obtained through the chemical vapor deposition (CVD) process in the hydrogen protective atmosphere for 8 h at the temperature of 1040 °C and internal pressure of 150 mbar. A microstructure of the layer was characterized using the scanning electron microscopy (SEM) and X-ray Energy Dispersive Spectroscopy (EDS). It was found that aluminide coating improve the high temperature fatigue performance of MAR247 nickel based superalloy at 900 °C significantly. The coated MAR 247 nickel based superalloy was characterized by the stress amplitude response ranging from 350 MPa to 520 MPa, which is twice as large as that for the uncoated alloy. Keywords: chemical vapor deposition, nickel alloys, aluminide coatings, high temperature fatigue, creep Affiliations:
Kopeć M. | - | IPPT PAN | Kukla D. | - | IPPT PAN | Yuan X. | - | Imperial College London (GB) | Rejmer W. | - | other affiliation | Kowalewski Z.L. | - | IPPT PAN | Senderowski C. | - | other affiliation |
| 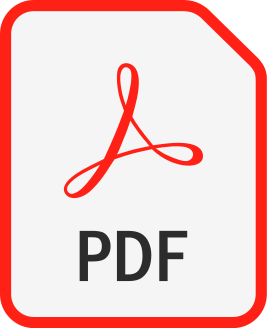 |
66. |
Kopeć M., Jóźwiak S.♦, Kowalewski Z.L., Fe-Al based composite reinforced with ultra-fine Al2O3 oxides for high temperature applications,
JOURNAL OF THEORETICAL AND APPLIED MECHANICS, ISSN: 1429-2955, DOI: 10.15632/jtam-pl/138322, Vol.59, No.3, pp.509-513, 2021 Abstract: In this paper, an Fe-Al based composite reinforced with ultra-fine Al2O3 oxides was obtained through sintering of aluminium, iron and mullite ceramic powders using self-propagated high temperature synthesis (SHS). The powder mixture with a 50%wt. content of the ceramic reinforcement was cold pressed and subsequently subjected to the sintering process in vacuum at 1200◦C for 25 minutes under external loading of 25 kN. The complex microstructure of the Fe-Al matrix reinforced with ultra-fine Al2O3 oxides was found to be desired in high temperature applications since only 3% of the relative weight gain was observed after 100 hours of annealing at 900◦C. Keywords: cermet composites, reaction synthesis, powder methods, electron microscopy Affiliations:
Kopeć M. | - | IPPT PAN | Jóźwiak S. | - | Military University of Technology (PL) | Kowalewski Z.L. | - | IPPT PAN |
| 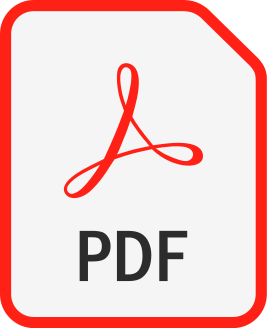 |
67. |
Kukla D., Kopeć M., Kowalewski Z.L., Politis D.J.♦, Jóźwiak S.♦, Senderowski C.♦, Thermal barrier stability and wear behavior of CVD deposited aluminide coatings for MAR 247 nickel superalloy,
Materials, ISSN: 1996-1944, DOI: 10.3390/ma13173863, Vol.13, No.17, pp.3863-1-11, 2020 Abstract: In this paper, aluminide coatings of various thicknesses and microstructural uniformity obtained using chemical vapor deposition (CVD) were studied in detail. The optimized CVD process parameters of 1040 °C for 12 h in a protective hydrogen atmosphere enabled the production of high density and porosity-free aluminide coatings. These coatings were characterized by beneficial mechanical features including thermal stability, wear resistance and good adhesion strength to MAR 247 nickel superalloy substrate. The microstructure of the coating was characterized through scanning electron microscopy (SEM), X-ray energy dispersive spectroscopy (EDS) and X-ray diffraction (XRD) analysis. Mechanical properties and wear resistance of aluminide coatings were examined using microhardness, scratch test and standardized wear tests, respectively. Intermetallic phases from the Ni-Al system at specific thicknesses (20-30 µm), and the chemical and phase composition were successfully evaluated at optimized CVD process parameters. The optimization of the CVD process was verified to offer high performance coating properties including improved heat, adhesion and abrasion resistance. Keywords: chemical vapor deposition, nickel alloys, coatings, X-ray analysis Affiliations:
Kukla D. | - | IPPT PAN | Kopeć M. | - | IPPT PAN | Kowalewski Z.L. | - | IPPT PAN | Politis D.J. | - | Imperial College London (GB) | Jóźwiak S. | - | Military University of Technology (PL) | Senderowski C. | - | other affiliation |
| 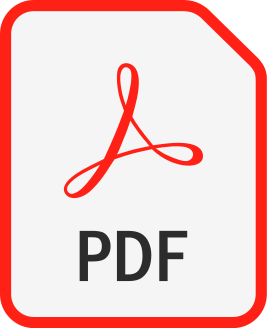 |
68. |
Wang K.♦, Kopeć M., Chang S.♦, Qu B.♦, Liu J.♦, Politis D.J.♦, Wang L.♦, Liu G.♦, Enhanced formability and forming efficiency for two-phase titanium alloys by fast light alloys stamping technology (FAST),
Materials & Design, ISSN: 0264-1275, DOI: 10.1016/j.matdes.2020.108948, pp.1-25, 2020 Abstract: During hot stamping of titanium alloys, insufficient forming temperatures result in limited material formability, whereas temperatures approaching the β phase transus also result in reduced formability due to phase transformation, grain coarsening and oxidation during the long-time heating. To solve this problem, Fast light Alloys Stamping Technology (FAST) is proposed in this paper, where fast heating is employed. Effects of heating parameters on the formability and post-form strength were studied by tensile tests. Forming of a wing stiffener was performed to validate this new process. Results show that microstructure of TC4 alloy after fast heating was in nonequilibrium state, which could enhance ductility significantly compared with the equilibrium state. When TC4 alloy was first heated to 950 °C with heating rate of 100 °C/s and then cooled to 700 °C, the elongation at 700 °C was more than 3 times that of a slow heating rate with soaking. Nano-scaled martensite with high dislocation density transformed from β phase was observed under fast heating condition. A complex shaped wing stiffener was successfully formed from TC4 titanium alloy in less than 70 s including heating, transfer and forming, and the post-form strength was almost the same with the initial blank. Keywords: titanium alloys, fast heating, hot stamping, formability, post-form strength Affiliations:
Wang K. | - | Imperial College London (GB) | Kopeć M. | - | IPPT PAN | Chang S. | - | Harbin Institiute of Technology (CN) | Qu B. | - | Harbin Institiute of Technology (CN) | Liu J. | - | Imperial College London (GB) | Politis D.J. | - | Imperial College London (GB) | Wang L. | - | Imperial College London (GB) | Liu G. | - | Harbin Institiute of Technology (CN) |
| 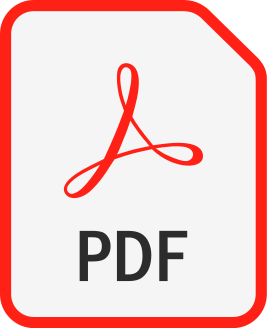 |
69. |
Kopeć M., Jóźwiak S.♦, Kowalewski Z.L., A novel microstructural evolution model for growth of ultra-fine Al2O3 oxides from SiO2 silica ceramic decomposition during self-propagated high-temperature synthesis,
Materials, ISSN: 1996-1944, DOI: 10.3390/ma13122821, Vol.13, No.12, pp.2821-1-11, 2020 Abstract: In this paper, experimental verification of the microstructural evolution model during sintering of aluminum, iron and particulate mullite ceramic powders using self-propagated high-temperature synthesis (SHS) was performed. The powder mixture with 20% wt. content of reinforcing ceramic was investigated throughout this research. The mixed powders were cold pressed and sintered in a vacuum at 1030 °C. The SHS reaction between sintered feed powders resulted in a rapid temperature increase from the heat generated. The temperature increase led to the melting of an aluminum-based metallic liquid. The metallic liquid infiltrated the porous SiO2 ceramics. Silicon atoms were transited into the intermetallic iron-aluminum matrix. Subsequently, a ternary matrix from the Fe-Al-Si system was formed, and synthesis of the oxygen and aluminum occurred. Synthesis of both these elements resulted in formation of new, fine Al2O3 precipitates in the volume of matrix. The proposed microstructural evolution model for growth of ultra-fine Al2O3 oxides from SiO2 silica ceramic decomposition during SHS was successfully verified through scanning electron microscopy (SEM), X-ray energy-dispersive spectroscopy (EDS) analysis and X-ray diffraction (XRD). Keywords: intermetallics, powder methods, electron microscopy, X-ray analysis Affiliations:
Kopeć M. | - | IPPT PAN | Jóźwiak S. | - | Military University of Technology (PL) | Kowalewski Z.L. | - | IPPT PAN |
| 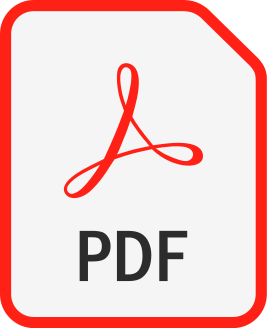 |
70. |
Ranachowski Z., Ranachowski P., Dębowski T., Brodecki A., Kopeć M., Roskosz M.♦, Fryczowski K.♦, Szymków M.♦, Krawczyk E.♦, Schabowicz K.♦, Mechanical and non-destructive testing of plasterboards subjected to a hydration process,
Materials, ISSN: 1996-1944, DOI: 10.3390/ma13102405, Vol.13, No.10, pp.2405-1-18, 2020 Abstract: The aim of this study was to investigate the effect of plasterboards' humidity absorption on their performance. Specimens' hydration procedure consisted of consecutive immersing in water and subsequent drying at room temperature. Such a procedure was performed to increase the content of moisture within the material volume. The microstructural observations of five different plasterboard types were performed through optical and scanning electron microscopy. The deterioration of their properties was evaluated by using a three-point bending test and a subsequent ultrasonic (ultrasound testing (UT)) longitudinal wave velocity measurement. Depending on the material porosity, a loss of UT wave velocity from 6% to 35% and a considerable decrease in material strength from 70% to 80% were observed. Four types of approximated formulae were proposed to describe the dependence of UT wave velocity on board moisture content. It was found that the proposed UT method could be successfully used for the on-site monitoring of plasterboards' hydration processes. Keywords: plasterboards, moisture content, hydration processes, mechanical properties, ultrasound measurements Affiliations:
Ranachowski Z. | - | IPPT PAN | Ranachowski P. | - | IPPT PAN | Dębowski T. | - | IPPT PAN | Brodecki A. | - | IPPT PAN | Kopeć M. | - | IPPT PAN | Roskosz M. | - | AGH University of Science and Technology (PL) | Fryczowski K. | - | Silesian University of Technology (PL) | Szymków M. | - | other affiliation | Krawczyk E. | - | other affiliation | Schabowicz K. | - | Wroclaw University of Science and Technology (PL) |
| 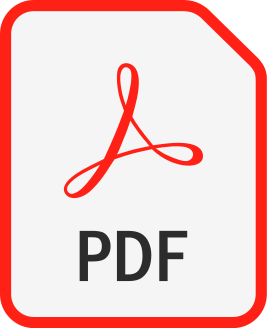 |
71. |
Liu X.♦, Kopeć M., Fakir O.♦, Qu H.♦, Wang Y.♦, Wang L.♦, Li Z.♦, Characterisation of the interfacial heat transfer coefficient in hot stamping of titanium alloys,
International Communications in Heat and Mass Transfer, ISSN: 0735-1933, DOI: 10.1016/j.icheatmasstransfer.2020.104535, Vol.113, pp.104535-1-14, 2020 Abstract: The interfacial heat transfer coefficient (IHTC) for titanium alloys is an important parameter in non-isothermal hot stamping processes to determine the temperature field as well as temperature-dependent material behaviours that consequently affect the post-form properties of the formed components. However, the IHTC for titanium alloys in hot stamping processes has seldom been studied before. In the present research, the effects of contact pressure, lubricant, surface roughness, tooling material and initial blank temperature on the IHTC for the titanium alloy Ti-6Al-4V were studied and modelled to characterise the IHTC values under various hot stamping conditions as well as identify the functional mechanisms affecting the IHTC. Furthermore, the results of hot stamping of Ti-6Al4V wing stiffener components were used to verify the simulation results of the temperature field of the formed component with an error of less than 5%. Keywords: interfacial heat transfer coefficient (IHTC), Ti-6Al-4V, hot stamping, experimental validation Affiliations:
Liu X. | - | Imperial College London (GB) | Kopeć M. | - | IPPT PAN | Fakir O. | - | other affiliation | Qu H. | - | AVIC Manufacturing Technology Institute (CN) | Wang Y. | - | Beijing Aeronautical Manufacturing Technology Research Institute (CN) | Wang L. | - | Imperial College London (GB) | Li Z. | - | AVIC Manufacturing Technology Institute (CN) |
| 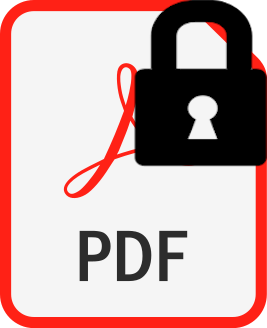 |
72. |
Ranachowski Z., Ranachowski P., Brodecki A., Kopeć M., Kúdela Jr S.♦, Quasi-static and dynamic testing of carbon fiber reinforced magnesium composites,
ARCHIVES OF METALLURGY AND MATERIALS, ISSN: 1733-3490, DOI: 10.24425/amm.2020.132836, Vol.65, No.2, pp.893-899, 2020 Abstract: Two types of composites, consisting of pure magnesium matrix reinforced with two commercially used carbon fibers, were systematically studied in this paper. The composites fabricated by the pressure infiltration method, were subjected to quasistatic and dynamic compression tests. Morphology of fiber strands was observed using scanning electron microscope (SEM). The application of carbon fibre reinforcement led to the stiffening of tested materials, resulting in the limitation of the possible compression to approx. 2.5%. The performed tests revealed the remarkable difference in compression strength of investigated compositions. The cause of that effect was that GRANOC fiber reinforced composite exhibited insufficient bond quality between the brittle fibers and the ductile matrix. T300 reinforced composite presented good connection between reinforcement and matrix resulting in increased mechanical properties. Investigated composites demonstrated higher mechanical strength during deformation at high strain rates. Microscopic observations also proved that the latter fibers with regular shape and dense packaging within the filaments are proper reinforcement when designing the lightweight composite material. Keywords: Mg matrix composite, compressive properties, carbon fiber, Split-Hopkinson pressure bar Affiliations:
Ranachowski Z. | - | IPPT PAN | Ranachowski P. | - | IPPT PAN | Brodecki A. | - | IPPT PAN | Kopeć M. | - | IPPT PAN | Kúdela Jr S. | - | Institute of Materials and Machine Mechanics, Slovak Academy of Sciences (SK) |
| 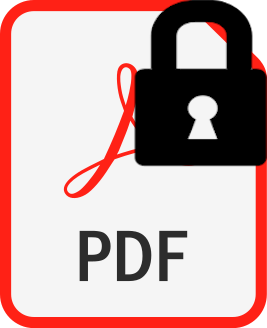 |
73. |
Levintant-Zayonts N., Starzyński G., Kopeć M., Kucharski S., Characterization of NiTi SMA in its unusual behaviour in wear tests,
TRIBOLOGY INTERNATIONAL, ISSN: 0301-679X, DOI: 10.1016/j.triboint.2019.05.005, Vol.137, pp.313-323, 2019 Abstract: The manuscript presents experimental investigations of an unusual behaviour of shape memory alloys (NiTi) having different characteristic temperatures in wear test. The studies are focused on the different wear mechanism at varying loads and sliding times and include a description of the phenomena accompanying the wear process. The ball-on-plate reciprocating sliding wear tests were conducted on NiTi shape memory alloys against a sapphire ball. We show that the wear resistance of NiTi is affected by its specific stress-strain characteristic. The understanding of the tribological behaviour of NiTi, a knowledge of the course of wear and an examination of its mechanisms can enable an effective prevention of the destruction of devices components and prolong their safe working life. Keywords: wear behaviour of NiTi SMA, friction coefficient, superelasticity, shape memory effect Affiliations:
Levintant-Zayonts N. | - | IPPT PAN | Starzyński G. | - | IPPT PAN | Kopeć M. | - | IPPT PAN | Kucharski S. | - | IPPT PAN |
| 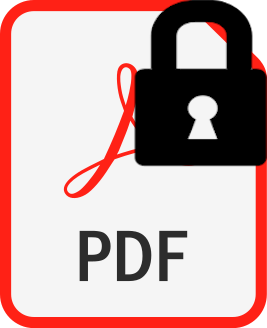 |
74. |
Li Z.♦, Qu H.♦, Chen F.♦, Wang Y.♦, Tan Z.♦, Kopeć M., Wang K.♦, Zheng K.♦, Deformation behavior and microstructural evolution during hot stamping of TA15 sheets: experimentation and modelling,
Materials, ISSN: 1996-1944, DOI: 10.3390/ma12020223, Vol.12, No.2, pp.223-1-14, 2019 Abstract: Near-α titanium alloys have extensive applications in high temperature structural components of aircrafts. To manufacture complex-shaped titanium alloy panel parts with desired microstructure and good properties, an innovative low-cost hot stamping process for titanium alloy was studied in this paper. Firstly, a series of hot tensile tests and Scanning Electron Microscope (SEM) observations were performed to investigate hot deformation characteristics and identify typical microstructural evolutions. The optimal forming temperature range is determined to be from 750 °C to 900 °C for hot stamping of TA15. In addition, a unified mechanisms-based material model for TA15 titanium alloy based on the softening mechanisms of recrystallization and damage was established, which enables to precisely predict stress-strain behaviors and potentially to be implemented into Finite Element (FE) simulations for designing the reasonable processing window of structural parts for the aerospace industry. Keywords: TA15, hot stamping, phase evolution, deformation, modelling Affiliations:
Li Z. | - | AVIC Manufacturing Technology Institute (CN) | Qu H. | - | AVIC Manufacturing Technology Institute (CN) | Chen F. | - | AVIC Manufacturing Technology Institute (CN) | Wang Y. | - | Beijing Aeronautical Manufacturing Technology Research Institute (CN) | Tan Z. | - | Imperial College London (GB) | Kopeć M. | - | IPPT PAN | Wang K. | - | Imperial College London (GB) | Zheng K. | - | Imperial College London (GB) |
| 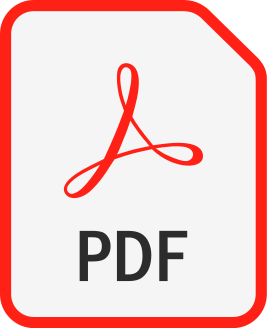 |
75. |
Jozwik P.♦, Kopeć M., Polkowski W.♦, Bojar Z.♦, Dynamic deformation tests of Ni3Al based intermetallic alloy by using the split Hopkinson pressure bar technique,
Journal of Mining and Metallurgy, Section B: Metallurgy, ISSN: 1450-5339, DOI: 10.2298/JMMB181113014J, Vol.55, No.1, pp.129-134, 2019 Abstract: In this work, the Ni3Al-based intermetallic alloy was subjected to room temperature dynamic plastic deformation tests by using a split Hopkinson pressure bar technique. The dynamic compression processes were carried out at strain rates in the range of ε=(1.9×10^2 ÷ 1×10^4 s^-1). A strong impact of applied deformation conditions on microstructure and mechanical properties evolution in the examined Ni3Al intermetallic, was documented. Generally, very high maximum compressive stress values were obtained, reaching 5500 MPa for the sample deformed at the highest strain rate (i.e. ε=1×10^4 s^-1). The results of performed SEM/EBSD evaluation point towards an occurrence of dynamic recovery and recrystallization phenomena in Ni3Al samples deformed at high strain rates. Keywords: Ni3Al-based alloy, split Hopkinson pressure bar, SEM/EBSD analysis Affiliations:
Jozwik P. | - | Military University of Technology (PL) | Kopeć M. | - | IPPT PAN | Polkowski W. | - | Foundry Research Institute (PL) | Bojar Z. | - | Military University of Technology (PL) |
| 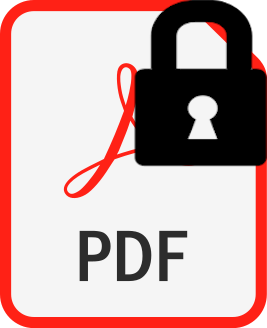 |
76. |
Kopeć M., Wang K.♦, Politis D.J.♦, Wang Y.♦, Wang L.♦, Lin J.♦, Formability and microstructure evolution mechanisms of Ti6Al4V alloy during a novel hot stamping process,
MATERIALS SCIENCE AND ENGINEERING A-STRUCTURAL MATERIALS PROPERTIES MICROSTRUCTURE AND PROCESSING, ISSN: 0921-5093, DOI: 10.1016/j.msea.2018.02.038, Vol.719, pp.72-81, 2018 Abstract: A novel hot stamping process for Ti6Al4V alloy using cold forming tools and a hot blank was presented in this paper. The formability of the material was studied through uniaxial tensile tests at temperatures ranging from 600 to 900 °C and strain rates ranging from 0.1 to 5 s-1. An elongation ranging from 30% to 60% could be achieved at temperatures ranging from 750 to 900°C respectively. The main microstructure evolution mechanisms varied with the deformation temperature, including recovery, phase transformation and recrystallization. The hardness of the material after deformation first decreased with the temperature due to recovery, and subsequently increased mainly due to the phase transformation. During the hot stamping tests, qualified parts could be formed successfully at heating temperatures ranging from 750 to 850°C. The forming failed at lower temperatures due to the limited ductility of the material. At temperatures higher than 900°C, extensive phase transformation of α to β occurred during the heating. During the transfer and forming, the temperature dropped significantly which led to the formation of transformed β, reduction of the formability and subsequent failure. The post-form hardness distribution demonstrated the same tendency as that after uniaxial tensile tests. Keywords: titanium alloys, Ti6Al4V, hot stamping, microstructure Affiliations:
Kopeć M. | - | IPPT PAN | Wang K. | - | Imperial College London (GB) | Politis D.J. | - | Imperial College London (GB) | Wang Y. | - | Beijing Aeronautical Manufacturing Technology Research Institute (CN) | Wang L. | - | Imperial College London (GB) | Lin J. | - | Imperial College London (GB) |
| 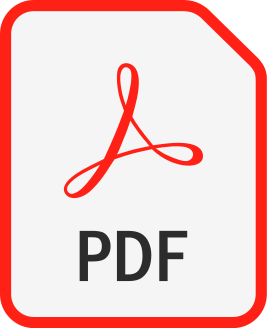 |
77. |
Kopeć M., Wang K.♦, Wang Y.♦, Wang L.♦, Lin J.♦, Feasibility study of a novel hot stamping process for Ti6Al4V alloy,
MATEC Web of Conferences, ISSN: 2261-236X, DOI: 10.1051/matecconf/201819008001, Vol.190, pp.1-5, 2018 Abstract: To investigate the feasibility of a novel hot stamping process for the Ti6Al4V titanium alloy using low temperature forming tools, mechanical properties of the material were studied using hot tensile tests at a temperature range of 600 - 900°C with a constant strain rate of 1s-1. Hot stamping tests were carried out to verify the feasibility of this technology and identify the forming window for the material. Results show that when the deformation temperature was lower than 700°C, the amount of elongation was less than 20%, and it also had little change with the temperature. However, when the temperature was higher than 700°C, a good ductility of the material can be achieved. During the forming tests, parts failed at lower temperatures (600°C) due to the limited formability and also failed at higher temperatures (950°C) due to the phase transformation. The post-form hardness firstly decreased with the temperature increasing due to recovery and then increased due to the phase transformation. Qualified parts were formed successfully between temperatures of 750 - 850°C, which indicates that this new technology has a great potential in forming titanium alloys sheet components. Keywords: titanium, hot stamping, metal forming Affiliations:
Kopeć M. | - | IPPT PAN | Wang K. | - | Imperial College London (GB) | Wang Y. | - | Beijing Aeronautical Manufacturing Technology Research Institute (CN) | Wang L. | - | Imperial College London (GB) | Lin J. | - | Imperial College London (GB) |
| 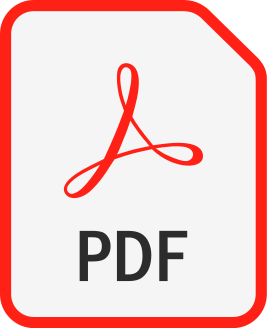 |
78. |
Kukla D., Grzywna P., Kopeć M., Kowalewski Z.L., Assessment of hardened layer thickness for 40HNMA steel using eddy current method,
INŻYNIERIA MATERIAŁOWA, ISSN: 0208-6247, DOI: 10.15199/28.2016.5.10, Vol.213, No.5, pp.263-266, 2016 Abstract: Materials and semi-manufactured products for aviation equipment are usually subjected to increasingly rigorous demands for the quality control. In many cases, like hardened or carburized wheels or rollers assembled in the gear motors, the control procedures enforce necessity of the selective testing of details coming from production lines using destructive techniques. The main aim of diagnostic investigations carrying out on series of final products is to assess qualitatively and quantitatively the layers obtained due to carburizing and induction hardening. Unfortunately, such processes increase the fabrication costs significantly, especially in the case of complex manufacturing technology applied and small-lot production as well. In order to reduce them the attempts for application of non-destructive testing methods are taken for evaluation of either the layers quality or the products subjected to surface treatments. This paper presents the eddy currents method used for the thickness evaluation of the carburized and induction-hardened layers on the basis of the impedance signal variation. The signal was obtained as a result of the so-called ‘lift off’ effect. A methodology for the quantitative thickness evaluation of the carburized and induction-hardened layers has been elaborated under a range of technological parameters. The measurements ranges were defined in the framework of which an identification of the hardened layer was possible using the commercial defectoscope and reference specimens of the fixed thickness. Tests were carried out on specimens made of the ASM6414 steel and subjected subsequently to carburization and induction hardening. The impedance parameters were measured for selected values of frequency. The results were verified on the basis of metallographic investigations as well as the microhardness measurements captured in the form of profiles taken from specimens’ cross-sections of different layer thickness. Keywords: eddy current, hardening, carburizing, layers, non-destructive technique Affiliations:
Kukla D. | - | IPPT PAN | Grzywna P. | - | IPPT PAN | Kopeć M. | - | IPPT PAN | Kowalewski Z.L. | - | IPPT PAN |
| 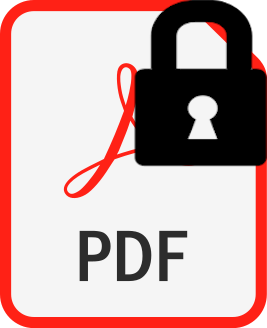 |
79. |
Kopeć M., Grzywna P., Kukla D., Kowalewski Z.L., Evaluation of the fatigue damage development using ESPI method,
INŻYNIERIA MATERIAŁOWA, ISSN: 0208-6247, DOI: 10.15199/28.2016.4.9, Vol.212, No.4, pp.201-205, 2016 Abstract: Fatigue damage process developing in structural materials under long-term cyclic loading is still an unsolved problem of modern engineering. Attempts to assess a degree of materials degradation under fatigue conditions on the basis of changes in the areas of local strain concentration determined by optical methods can be treated as the promising contemporary research direction of majority of scientific centres in the world. In most cases, fatigue damage has a local character and it is based on damage development leading to generation of cracks appearing around structural defects or geometrical notches. An identification of these areas and their subsequent monitoring requires a full-field displacement measurements performed on the objects surfaces. It seems that modern contemporary optical methods for displacement components measuring on the surfaces of structural elements or tested specimens are suitable for such purpose. Digital Image Correlation (DIC) and Electronic Speckle Pattern Interferometry (ESPI) are nowadays the most widely used testing methods in this area. Both of them enable capturing of displacement and strain components distributions. This paper presents an attempt to use the ESPI method for fatigue damage evaluation and its monitoring on specimens made of the aluminide coated nickel super-alloys. Flat specimens were subjected to cyclic loading. The fatigue tests were interrupted several times in order to perform a static loading during which the optical measurements were carried out. An analysis of the results captured by the ESPI system allowed indication of places of the greatest stress concentration and demonstration of the damage development process as a function of the increasing number of cycles. Keywords: fatigue, damage, super-alloy, Electronic Speckle Pattern Interferometry Affiliations:
Kopeć M. | - | IPPT PAN | Grzywna P. | - | IPPT PAN | Kukla D. | - | IPPT PAN | Kowalewski Z.L. | - | IPPT PAN |
| 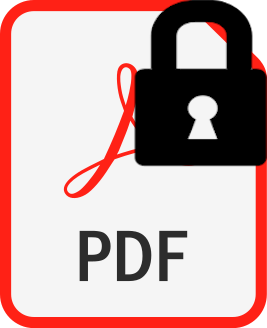 |