1. |
Rabcuka J.♦, Smethurst P. A.♦, Dammert K.♦, Saker J.♦, Aran G.♦, Walsh G. M.♦, Tan J. C. G.♦, Codinach M.♦, McTaggart K.♦, Marks D. C.♦, Bakker S. J. L.♦, McMahon A.♦, Di Angelantonio E.♦, Roberts D. J.♦, Błoński S., Korczyk P.M., Shirakami A.♦, Cardigan R.♦, Swietach P.♦, Assessing the kinetics of oxygen-unloading from red cells using FlowScore, a flow-cytometric proxy of the functional quality of blood,
eBioMedicine, ISSN: 2352-3964, DOI: 10.1016/j.ebiom.2024.105498, Vol.111, pp.105498-105498, 2025 Abstract: Background
Metrics evaluating the functional quality of red blood cells (RBCs) must consider their role in oxygen delivery. Whereas oxygen-carrying capacity is routinely reported using haemoglobin assays, the rate of oxygen exchange is not measured, yet also important for tissue oxygenation. Since oxygen-unloading depends on the diffusion pathlength inside RBCs, cell geometry offers a plausible surrogate.
Methods
We related the time-constant of oxygen-unloading (τ), measured using single-cell oxygen saturation imaging, with flow-cytometric variables recorded on a haematology analyser. Experiments compared freshly-drawn RBCs with stored RBCs, wherein metabolic run-down and spherical remodelling hinder oxygen unloading.
Findings
Multivariable regression related τ to a ratio of side- and forward-scatter, referred to herein as FlowScore. FlowScore was able to distinguish, with sensitivity and specificity >80%, freshly drawn blood from blood that underwent storage-related kinetic attrition in O2-handling. Moreover, FlowScore predicted τ restoration upon biochemical rejuvenation of stored blood. Since RBC geometry and metabolic state are related, variants of FlowScore estimated [ATP] and [2,3-diphosphoglycerate]. The veracity of FlowScore was confirmed by four blood-banking systems (Australia, Canada, England, Spain). Applying FlowScore to data from the COMPARE study revealed a positive association with the time-delay from sample collection to measurement, which was verified experimentally. The LifeLines dataset revealed age, sex, and smoking among factors affecting FlowScore.
Interpretation
We establish FlowScore as a widely-accessible and cost-effective surrogate of RBC oxygen-unloading kinetics. As a metric of a cellular process that is sensitive to storage and disease, we propose FlowScore as an RBC quality marker for blood-banking and haematology. Keywords: Haematology,Erythrocytes,Storage lesion,Assay,Oxygen transport,Transfusion Affiliations:
Rabcuka J. | - | other affiliation | Smethurst P. A. | - | other affiliation | Dammert K. | - | other affiliation | Saker J. | - | other affiliation | Aran G. | - | other affiliation | Walsh G. M. | - | other affiliation | Tan J. C. G. | - | other affiliation | Codinach M. | - | other affiliation | McTaggart K. | - | other affiliation | Marks D. C. | - | other affiliation | Bakker S. J. L. | - | other affiliation | McMahon A. | - | other affiliation | Di Angelantonio E. | - | other affiliation | Roberts D. J. | - | other affiliation | Błoński S. | - | IPPT PAN | Korczyk P.M. | - | IPPT PAN | Shirakami A. | - | other affiliation | Cardigan R. | - | other affiliation | Swietach P. | - | other affiliation |
| 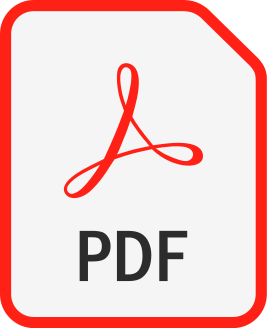 |
2. |
Dumbill R.♦, Rabcuka J.♦, Fallon J.♦, Knight S.♦, Hunter J.♦, Voyce D.♦, Barrett Jacob T.♦, Ellen M.♦, Weissenbacher A.♦, Kurniawan T., Błoński S., Korczyk P.M., Ploeg Rutger J.♦, Coussios C.♦, Friend P.♦, Świętach P.♦, Impaired O2 unloading from stored blood results in diffusion-limited O2 release at tissues: evidence from human kidneys,
Blood, ISSN: 0006-4971, DOI: 10.1182/blood.2023022385, Vol.143, No.8, pp.721-733, 2024 Abstract: The volume of oxygen drawn from systemic capillaries down a partial pressure gradient is determined by the oxygen content of red blood cells (RBCs) and their oxygen-unloading kinetics, although the latter is assumed to be rapid and, therefore, not a meaningful factor. Under this paradigm, oxygen transfer to tissues is perfusion-limited. Consequently, clinical treatments to optimize oxygen delivery aim at improving blood flow and arterial oxygen content, rather than RBC oxygen-handling. Whilst the oxygen-carrying capacity of blood is increased with transfusion, previous studies have shown that stored blood undergoes kinetic attrition of oxygen release, which may compromise overall oxygen delivery to tissues, i.e. transport became diffusion-limited. We sought evidence for diffusion-limited oxygen release in viable human kidneys normothermically perfused with stored blood. In a cohort of kidneys that went on to be transplanted, ex-vivo renal respiration correlated inversely with the time-constant of oxygen-unloading from RBCs used for perfusion. Furthermore, the renal respiratory rate did not correlate with arterial O2 delivery unless this factored the rate of oxygen-release from RBCs, as expected from diffusion-limited transport. In kidneys deemed unsuitable for transplantation, perfusion was alternated between stored and rejuvenated RBCs of the same donation to control oxygen-unloading without intervening ischemia and holding all non-RBC parameters constant. Rejuvenated oxygen-unloading kinetics reversibly improved the kidney's oxygen diffusion capacity and increased cortical oxygen partial pressure by 60%. Thus, oxygen delivery to tissues can become diffusion-limited during perfusion with stored blood, which has implications in scenarios such as ex-vivo organ perfusion, major hemorrhage, and pediatric transfusion. Affiliations:
Dumbill R. | - | other affiliation | Rabcuka J. | - | other affiliation | Fallon J. | - | other affiliation | Knight S. | - | other affiliation | Hunter J. | - | other affiliation | Voyce D. | - | other affiliation | Barrett Jacob T. | - | other affiliation | Ellen M. | - | other affiliation | Weissenbacher A. | - | other affiliation | Kurniawan T. | - | IPPT PAN | Błoński S. | - | IPPT PAN | Korczyk P.M. | - | IPPT PAN | Ploeg Rutger J. | - | other affiliation | Coussios C. | - | other affiliation | Friend P. | - | other affiliation | Świętach P. | - | other affiliation |
| 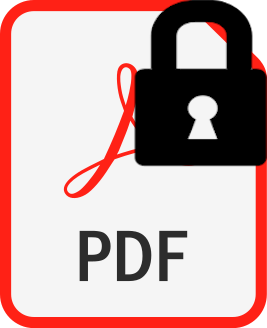 |
3. |
Kurniawan T., Sahebdivani M.♦, Zaremba D., Błoński S., Garstecki P.♦, van Steijn V.♦, Korczyk P.M., Formation of droplets in microfluidic cross-junctions at small capillary numbers: Breakdown of the classical squeezing regime,
Chemical Engineering Journal, ISSN: 1385-8947, DOI: 10.1016/j.cej.2023.145601, Vol.474, pp.14560-14560, 2023 Abstract: Two decades of research on droplet formation in microchannels have led to the widely accepted view that droplets form through the squeezing mechanism when interfacial forces dominate over viscous forces. The initially surprising finding that the volume of the droplets is insensitive to the relative importance of these two forces is nowadays well understood from the constrained deformation of the droplet interface during formation. In this work, we show a lower limit of the squeezing mechanism for droplets produced in microfluidic cross-junctions. Below this limit, in the leaking regime, which was recently discovered for droplets produced in T-junctions, the volume of the produced droplets strongly depends on the relative importance of interfacial and viscous forces, as captured by the capillary number. We reveal a fundamental difference in the mechanisms at play in the leaking regime between T- and cross-junctions. In cross-junctions, the droplet neck elongates substantially, and unlike the case of the T-junction, the magnitude of this elongation depends strongly on the value of the capillary number. This elongation significantly affects the final droplet volume in a low capillary number regime. Generalizing the classical squeezing law by lifting the original assumptions and incorporating both identified mechanisms of leaking through gutters and neck elongation, we derive a model for droplet formation and show that it agrees with our experiments. Keywords: Microfluidics,Cross-junction,Flow-focusing device,Droplet formation,Two-phase flow,Scaling law,Squeezing regime Affiliations:
Kurniawan T. | - | IPPT PAN | Sahebdivani M. | - | other affiliation | Zaremba D. | - | IPPT PAN | Błoński S. | - | IPPT PAN | Garstecki P. | - | Institute of Physical Chemistry, Polish Academy of Sciences (PL) | van Steijn V. | - | Delft University of Technology (NL) | Korczyk P.M. | - | IPPT PAN |
| 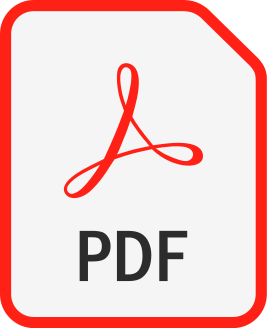 |
4. |
Sønstevold L.♦, Czerkies M.K., Escobedo-Cousin E.♦, Błoński S., Vereshchagina E.♦, Application of Polymethylpentene, an Oxygen Permeable Thermoplastic, for Long-Term on-a-Chip Cell Culture and Organ-on-a-Chip Devices,
Micromachines, ISSN: 2072-666X, DOI: 10.3390/mi14030532, Vol.14, No.3, pp.532-1-18, 2023 Abstract: The applicability of a gas-permeable, thermoplastic material polymethylpentene (PMP) was investigated, experimentally and analytically, for organ-on-a-chip (OoC) and long-term on-a-chip cell cultivation applications. Using a sealed culture chamber device fitted with oxygen sensors, we tested and compared PMP to commonly used glass and polydimethylsiloxane (PDMS). We show that PMP and PDMS have comparable performance for oxygen supply during 4 days culture of epithelial (A549) cells with oxygen concentration stabilizing at 16%, compared with glass control where it decreases to 3%. For the first time, transmission light images of cells growing on PMP were obtained, demonstrating that the optical properties of PMP are suitable for non-fluorescent, live cell imaging. Following the combined transmission light imaging and calcein-AM staining, cell adherence, proliferation, morphology, and viability of A549 cells were shown to be similar on PMP and glass coated with poly-L-lysine. In contrast to PDMS, we demonstrate that a film of PMP as thin as 0.125 mm is compatible with high-resolution confocal microscopy due to its excellent optical properties and mechanical stiffness. PMP was also found to be fully compatible with device sterilization, cell fixation, cell permeabilization and fluorescent staining. We envision this material to extend the range of possible microfluidic applications beyond the current state-of-the-art, due to its beneficial physical properties and suitability for prototyping by different methods. The integrated device and measurement methodology demonstrated in this work are transferrable to other cell-based studies and life-sciences applications. Keywords: polymethylpentene (PMP), cell culture, oxygen control, microfluidic device, organ-on-a-chip Affiliations:
Sønstevold L. | - | other affiliation | Czerkies M.K. | - | IPPT PAN | Escobedo-Cousin E. | - | other affiliation | Błoński S. | - | IPPT PAN | Vereshchagina E. | - | other affiliation |
| 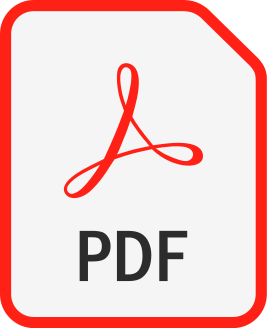 |
5. |
Zaremba D., Błoński S., Korczyk P.M., Concentration on demand – a microfluidic system for precise adjustment of the content of single droplets,
Chemical Engineering Journal, ISSN: 1385-8947, DOI: 10.1016/j.cej.2021.132935, Vol.430, No.3, pp.132935-1-16, 2022 Abstract: We present a novel microfluidic system that produces the required concentration of a reagent in a single droplet or that produces a sequence of droplets with a defined periodic distribution of concentrations. We use digital algorithms that, through a series of simple operations, such as merging and splitting droplets, ensure superior precision, repeatability and flexibility in concentration setting. Unlike Digital microfluidic (DMF) systems based on electrowetting on dielectric (EWOD) commonly used to implement digital algorithms in the droplet world, our approach is based on much more available channel-based microfluidics operated by programmable syringe pumps. Furthermore, the small footprint of our system makes it easy to integrate with other structures of microfluidic networks. Thus, this technique is a comprehensive component that can be built into the microfluidic networks executing laboratory analytical tasks in chemistry or biology to enrich their performance and offer new functionalities. Keywords: droplet-based microfluidics, microfluidic traps, droplet manipulation, concentration tuning, concentration gradient Affiliations:
Zaremba D. | - | IPPT PAN | Błoński S. | - | IPPT PAN | Korczyk P.M. | - | IPPT PAN |
| 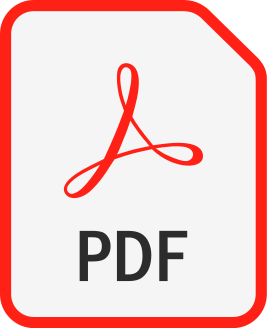 |
6. |
Rabcuka J.♦, Błoński S., Meli A.♦, Sowemimo-Coker S.♦, Zaremba D., Stephenson D.♦, Dzieciatkowska M.♦, Nerguizian D.♦, Cardigan R.♦, Korczyk P.M., Smethurst P.A.♦, D’Alessandro A.♦, Swietach P.♦, Metabolic reprogramming under hypoxic storage preserves faster oxygen unloading from stored red blood cells,
Blood Advances, ISSN: 2473-9529, DOI: 10.1182/bloodadvances.2022007774, Vol.6, No.18, pp.5415-5428, 2022 Abstract: Stored red blood cells (RBCs) incur biochemical and morphological changes, collectively termed the storage lesion. Functionally, the storage lesion manifests as slower oxygen unloading from RBCs, which may compromise the efficacy of transfusions where the clinical imperative is to rapidly boost oxygen delivery to tissues. Recent analysis of large real-world data linked longer storage with increased recipient mortality. Biochemical rejuvenation with a formulation of adenosine, inosine, and pyruvate can restore gas-handling properties, but its implementation is impractical for most clinical scenarios. We tested whether storage under hypoxia, previously shown to slow biochemical degradation, also preserves gas-handling properties of RBCs. A microfluidic chamber, designed to rapidly switch between oxygenated and anoxic superfusates, was used for single-cell oxygen saturation imaging on samples stored for up to 49 days. Aliquots were also analyzed flow cytometrically for side-scatter (a proposed proxy of O2 unloading kinetics), metabolomics, lipidomics, and redox proteomics. For benchmarking, units were biochemically rejuvenated at 4 weeks of standard storage. Hypoxic storage hastened O2 unloading in units stored to 35 days, an effect that correlated with side-scatter but was not linked to posttranslational modifications of hemoglobin. Although hypoxic storage and rejuvenation produced distinct biochemical changes, a subset of metabolites including pyruvate, sedoheptulose 1-phosphate, and 2/3 phospho-d-glycerate, was a common signature that correlated with changes in O2 unloading. Correlations between gas handling and lipidomic changes were modest. Thus, hypoxic storage of RBCs preserves key metabolic pathways and O2 exchange properties, thereby improving the functional quality of blood products and potentially influencing transfusion outcomes. Keywords: hypoxia, Hemanext, erythrocyte, hemoglobin, oxidative stress, microfluidics Affiliations:
Rabcuka J. | - | other affiliation | Błoński S. | - | IPPT PAN | Meli A. | - | other affiliation | Sowemimo-Coker S. | - | other affiliation | Zaremba D. | - | IPPT PAN | Stephenson D. | - | other affiliation | Dzieciatkowska M. | - | other affiliation | Nerguizian D. | - | other affiliation | Cardigan R. | - | other affiliation | Korczyk P.M. | - | IPPT PAN | Smethurst P.A. | - | other affiliation | D’Alessandro A. | - | other affiliation | Swietach P. | - | other affiliation |
| 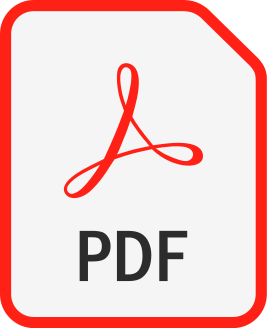 |
7. |
Brun-Cosme-Bruny M.♦, Pernet L.♦, Błoński S., Zaremba D., Fraboulet S.♦, Dolega M.E.♦, Microfluidic system for in vitro epithelial folding and calcium waves induction,
STAR Protocols, ISSN: 2666-1667, DOI: 10.1016/j.xpro.2022.101683, Vol.3, No.4, pp.101683-101683, 2022 Abstract: Epithelial folding is a fundamental process where initially flat monolayers transform into functional 3D structures. This protocol details fabrication steps for a polycarbonate microfluidic platform which enables triggering epithelial folds that recapitulate stereotypical cell shape changes and folding-associated mechanical stresses. We describe the steps for cell seeding to form a monolayer on the chip, and subsequent approach to trigger calcium waves in the epithelial monolayer through local epithelial deformation. Lastly, we outline quantitative analysis steps of the epithelial response. Affiliations:
Brun-Cosme-Bruny M. | - | other affiliation | Pernet L. | - | other affiliation | Błoński S. | - | IPPT PAN | Zaremba D. | - | IPPT PAN | Fraboulet S. | - | other affiliation | Dolega M.E. | - | Université Grenoble Alpes (FR) |
| 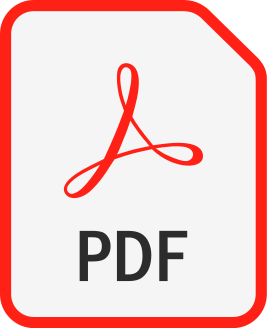 |
8. |
Błoński S., Aureille J.♦, Badawi S.♦, Zaremba D., Pernet L.♦, Grichine A.♦, Fraboulet S.♦, Korczyk P.M., Recho P.♦, Guilluy Ch.♦, Dolega M.E.♦, Direction of epithelial folding defines impact of mechanical forces on epithelial state,
Developmental Cell, ISSN: 1534-5807, DOI: 10.1016/j.devcel.2021.11.008, Vol.56, pp.3222-3234, 2021 Abstract: Cell shape dynamics during development is tightly regulated and coordinated with cell fate determination. Triggered by an interplay between biochemical and mechanical signals, epithelia form complex tissues by undergoing coordinated cell shape changes, but how such spatiotemporal coordination is controlled remains an open question. To dissect biochemical signaling from purely mechanical cues, we developed a microfluidic system that experimentally triggers epithelial folding to recapitulate stereotypic deformations observed in vivo. Using this system, we observe that the apical or basal direction of folding results in strikingly different mechanical states at the fold boundary, where the balance between tissue tension and torque (arising from the imposed curvature) controls the spread of folding-induced calcium waves at a short timescale and induces spatial patterns of gene expression at longer timescales. Our work uncovers that folding-associated gradients of cell shape and their resulting mechanical stresses direct spatially distinct biochemical responses within the monolayer. Keywords: epithelial morphogenesis, epithelial folding, tension, calcium waves, microfluidics, RNAseq Affiliations:
Błoński S. | - | IPPT PAN | Aureille J. | - | other affiliation | Badawi S. | - | other affiliation | Zaremba D. | - | IPPT PAN | Pernet L. | - | other affiliation | Grichine A. | - | other affiliation | Fraboulet S. | - | other affiliation | Korczyk P.M. | - | IPPT PAN | Recho P. | - | other affiliation | Guilluy Ch. | - | other affiliation | Dolega M.E. | - | Université Grenoble Alpes (FR) |
| 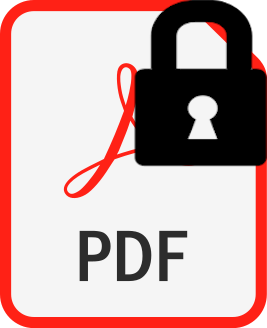 |
9. |
Zaremba D., Błoński S., Korczyk P.M., Integration of capillary–hydrodynamic logic circuitries for built-in control over multiple droplets in microfluidic networks,
LAB ON A CHIP, ISSN: 1473-0197, DOI: 10.1039/D0LC00900H, Vol.21, No.9, pp.1771-1778, 2021 Abstract: Here, we show the successful implementation of advanced sequential logic in droplet microfluidics, whose principles rely on capillary wells establishing stationary states, where droplets can communicate remotely via pressure impulses, influencing each other and switching the device states. All logic operations perform spontaneously due to the utilization of nothing more than capillary–hydrodynamic interactions, inherent for the confined biphasic flow. Our approach offers integration feasibility allowing to encode unprecedentedly long algorithms, e.g., 1000-droplet counting. This work has the potential for the advancement of liquid computers and thereby could participate in the development of the next generation of portable microfluidic systems with embedded control, enabling applications from single-cell analysis and biochemical assays to materials science. Affiliations:
Zaremba D. | - | IPPT PAN | Błoński S. | - | IPPT PAN | Korczyk P.M. | - | IPPT PAN |
| 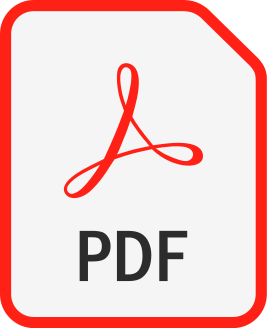 |
10. |
Zalewska-Piątek B.♦, Olszewski M.♦, Lipniacki T., Błoński S., Wieczór M.♦, Bruździak P.♦, Skwarska A.♦, Nowicki B.♦, Nowicki S.♦, Piątek R.♦, A shear stress micromodel of urinary tract infection by the Escherichia coli producing Dr adhesin,
PLoS Pathogens, ISSN: 1553-7366, DOI: 10.1371/journal.ppat.1008247, Vol.16, No.1, pp. e1008247-1-32, 2020 Abstract: In this study, we established a dynamic micromodel of urinary tract infection to analyze the impact of UT-segment-specific urinary outflow on the persistence of E. coli colonization. We found that the adherence of Dr+ E. coli to bladder T24 transitional cells and type IV collagen is maximal at lowest shear stress and is reduced by any increase in flow velocity. The analyzed adherence was effective in the whole spectrum of physiological shear stress and was almost irreversible over the entire range of generated shear force. Once Dr+ E. coli bound to host cells or collagen, they did not detach even in the presence of elevated shear stress or of chloramphenicol, a competitive inhibitor of binding. Investigating the role of epithelial surface architecture, we showed that the presence of budding cells–a model microarchitectural obstacle–promotes colonization of the urinary tract by E. coli. We report a previously undescribed phenomenon of epithelial cell "rolling-shedding" colonization, in which the detached epithelial cells reattach to the underlying cell line through a layer of adherent Dr+ E. coli. This rolling-shedding colonization progressed continuously due to "refilling" induced by the flow-perturbing obstacle. The shear stress of fluid containing free-floating bacteria fueled the rolling, while providing an uninterrupted supply of new bacteria to be trapped by the rolling cell. The progressive rolling allows for transfer of briefly attached bacteria onto the underlying monolayer in a repeating cascading event. Affiliations:
Zalewska-Piątek B. | - | Gdansk University of Technology (PL) | Olszewski M. | - | Gdansk University of Technology (PL) | Lipniacki T. | - | IPPT PAN | Błoński S. | - | IPPT PAN | Wieczór M. | - | Gdansk University of Technology (PL) | Bruździak P. | - | Gdansk University of Technology (PL) | Skwarska A. | - | University of Oxford (GB) | Nowicki B. | - | Nowicki Institute for Woman’s Health Research (US) | Nowicki S. | - | Nowicki Institute for Woman’s Health Research (US) | Piątek R. | - | Gdansk University of Technology (PL) |
| 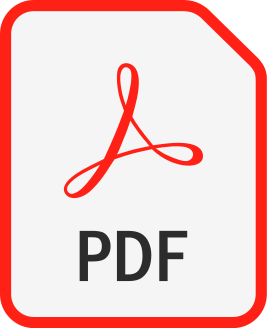 |
11. |
Błoński S., Zaremba D., Jachimek M.♦, Jakiela S.♦, Wacławczyk T.♦, Korczyk P.M., Impact of inertia and channel angles on flow distribution in microfluidic junctions,
MICROFLUIDICS AND NANOFLUIDICS, ISSN: 1613-4982, DOI: 10.1007/s10404-020-2319-6, Vol.24, No.2, pp.14-1-15, 2020 Abstract: In the present paper, we provide evidence of the vital impact of inertia on the flow in microfluidic networks, which is disclosed by the appearance of nonlinear velocity–pressure coupling. The experiments and numerical analysis of microfluidic junctions within the range of moderate Reynolds number (1 < Re < 250) revealed that inertial effects are of high relevance when Re > 10. Thus, our results estimate the applicability limit of the linear relationship between the flow rate and pressure drop in channels, commonly described by the so-called hydraulic resistance. Herein, we show that neglecting the nonlinear in their nature inertial effects can make such linear resistance-based approximation mistaken for the network operating beyond Re < 10. In the course of our research, we investigated the distribution of flows in connections of three channels in two flow modes. In the splitting mode, the flow from a common channel divides between two outputs, while in the merging mode, streams from two channels join together in a common duct. We tested a wide range of junction geometries characterized by parameters such as: (1) the angle between bifurcating channels (45°, 90°, 135° and 180°); (2) angle of the common channel relative to bifurcating channels (varied within the available range); (3) ratio of lengths of bifurcating channels (up to 8). The research revealed that the inertial effects strongly depend on angles between the channels. Additionally, we observed substantial differences between the distributions of flows in the splitting and merging modes in the same geometries, which reflects the non-reversibility of the motion of an inertial fluid. The promising aspect of our research is that for some combinations of both lengths and angles of the channels, the inertial contributions balance each other in such a way that the equations recover their linear character. In such an optimal configuration, the dependence on Reynolds number can be effectively mitigated. Affiliations:
Błoński S. | - | IPPT PAN | Zaremba D. | - | IPPT PAN | Jachimek M. | - | other affiliation | Jakiela S. | - | other affiliation | Wacławczyk T. | - | Wroclaw University of Science and Technology (PL) | Korczyk P.M. | - | IPPT PAN |
| 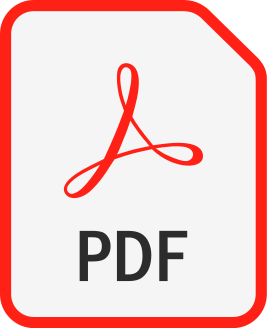 |
12. |
Korczyk P.M., van Steijn V.♦, Błoński S., Zaremba D., Beattie D.A.♦, Garstecki P.♦, Accounting for corner flow unifies the understanding of droplet formation in microfluidic channels,
Nature Communications, ISSN: 2041-1723, DOI: 10.1038/s41467-019-10505-5, Vol.10, No.1, pp.2528-1-9, 2019 Abstract: While shear emulsification is a well understood industrial process, geometrical confinement in microfluidic systems introduces fascinating complexity, so far prohibiting complete understanding of droplet formation. The size of confined droplets is controlled by the ratio between shear and capillary forces when both are of the same order, in a regime known as jetting, while being surprisingly insensitive to this ratio when shear is orders of magnitude smaller than capillary forces, in a regime known as squeezing. Here, we reveal that further reduction of—already negligibly small—shear unexpectedly re-introduces the dependence of droplet size on shear/capillary-force ratio. For the first time we formally account for the flow around forming droplets, to predict and discover experimentally an additional regime—leaking. Our model predicts droplet size and characterizes the transitions from leaking into squeezing and from squeezing into jetting, unifying the description for confined droplet generation, and offering a practical guide for applications. Affiliations:
Korczyk P.M. | - | IPPT PAN | van Steijn V. | - | Delft University of Technology (NL) | Błoński S. | - | IPPT PAN | Zaremba D. | - | IPPT PAN | Beattie D.A. | - | University of South Australia (AU) | Garstecki P. | - | Institute of Physical Chemistry, Polish Academy of Sciences (PL) |
| 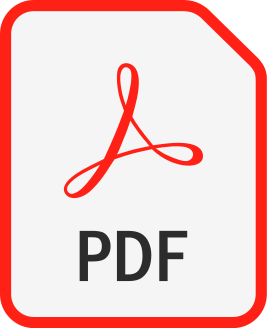 |
13. |
Jetka T.♦, Nienałtowski K.♦, Winarski T., Błoński S., Komorowski M., Information-theoretic analysis of multivariate single-cell signaling responses,
PLOS COMPUTATIONAL BIOLOGY, ISSN: 1553-7358, DOI: 10.1371/journal.pcbi.1007132, Vol.15, No.7, pp.e1007132-1-23, 2019 Abstract: Mathematical methods of information theory appear to provide a useful language to describe how stimuli are encoded in activities of signaling effectors. Exploring the information-theoretic perspective, however, remains conceptually, experimentally and computationally challenging. Specifically, existing computational tools enable efficient analysis of relatively simple systems, usually with one input and output only. Moreover, their robust and readily applicable implementations are missing. Here, we propose a novel algorithm, SLEMI—statistical learning based estimation of mutual information, to analyze signaling systems with high-dimensional outputs and a large number of input values. Our approach is efficient in terms of computational time as well as sample size needed for accurate estimation. Analysis of the NF-κB single—cell signaling responses to TNF-α reveals that NF-κB signaling dynamics improves discrimination of high concentrations of TNF-α with a relatively modest impact on discrimination of low concentrations. Provided R-package allows the approach to be used by computational biologists with only elementary knowledge of information theory. Affiliations:
Jetka T. | - | other affiliation | Nienałtowski K. | - | other affiliation | Winarski T. | - | IPPT PAN | Błoński S. | - | IPPT PAN | Komorowski M. | - | IPPT PAN |
| 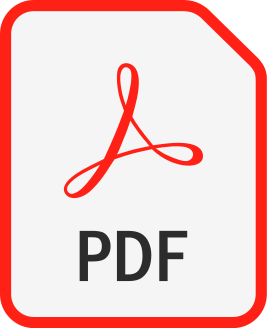 |
14. |
Błoński S., Pręgowska A., Michałek T., Szczepański J., The use of Lempel-Ziv complexity to analyze turbulence and flow randomness based on velocity fluctuations,
BULLETIN OF THE POLISH ACADEMY OF SCIENCES: TECHNICAL SCIENCES, ISSN: 0239-7528, DOI: 10.24425/bpasts.2019.130876, Vol.67, No.5, pp.957-962, 2019 Abstract: One of the mathematical tools to measure the generation rate of new patterns along a sequence of symbols is the Lempel-Ziv complexity (LZ). Under additional assumptions, LZ is an estimator of entropy in the Shannon sense. Since entropy is considered as a measure of randomness, this means that LZ can be treated also as a randomness indicator. In this paper, we used LZ concept to the analysis of different flow regimes in cold flow combustor models. Experimental data for two combustor's configurations motivated by efficient mixing need were considered. Extensive computer analysis was applied to develop a complexity approach to the analysis of velocity fluctuations recorded with hot-wire anemometry and PIV technique. A natural encoding method to address these velocity fluctuations was proposed. It turned out, that with this encoding the complexity values of the sequences are well correlated with the values obtained by means of RMS method (larger/smaller complexity larger/smaller RMS). However, our calculations pointed out the interesting result that most complex, this means most random, behavior does not overlap with the "most turbulent" point determined by the RMS method, but it is located in the point with maximal average velocity. It seems that complexity method can be particularly useful to analyze turbulent and unsteady flow regimes. Moreover, the complexity can also be used to establish other flow characteristics like its ergodicity or mixing. Keywords: turbulence, complexity, entropy, randomness Affiliations:
Błoński S. | - | IPPT PAN | Pręgowska A. | - | IPPT PAN | Michałek T. | - | IPPT PAN | Szczepański J. | - | IPPT PAN |
| 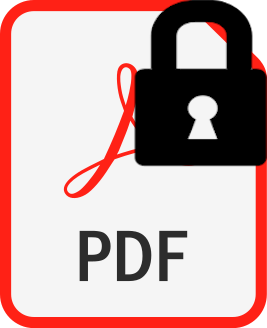 |
15. |
Zaremba D., Błoński S., Marijnissen M.J., Korczyk P.M., Fixing the direction of droplets in a bifurcating microfluidic junction,
MICROFLUIDICS AND NANOFLUIDICS, ISSN: 1613-4982, DOI: 10.1007/s10404-019-2218-x, Vol.23, pp.55-1-18, 2019 Abstract: We present a novel type of microfluidic bifurcating junctions which fixes the droplet's route. Unlike in regular junctions, where a droplet chooses one of two outputs depending on the (often instantaneous) flow distribution, our modifications direct droplets only to one preferred outlet. As we show, this solution works properly regardless of the variations of flow distribution in a wide range of its amplitude. Such modified junctions allow for the encoding of the droplet's traffic in the geometry of the device. We compare in a series of experiments different junctions having channels of uniform square cross section. Our observations revealed that a small, local modification of the junction in the form of an additional shallow slit imposes a significant consequence for the flow of droplets at an entire microfluidic network's scale. Another interesting and helpful feature of these new junctions is that they keep the integrity of long droplets, unlike regular junctions, which tend to split long droplets. Our experimental investigations revealed a complex transformation of the long droplet during its transfer through the modified junction. We show that this transformation resembles the Baker's transform and can be used for the enhancement of mixing inside the droplets. Finally, we show two examples of microfluidic devices where the deterministic character of these modified junctions is utilized to obtain new, non-trivial functionalities. This approach can be used for the engineering of microfluidic devices with embedded procedures replacing active elements like valves or magnetic/electric fields. Keywords: droplet, microfluidics, two-phase, manipulations Affiliations:
Zaremba D. | - | IPPT PAN | Błoński S. | - | IPPT PAN | Marijnissen M.J. | - | IPPT PAN | Korczyk P.M. | - | IPPT PAN |
| 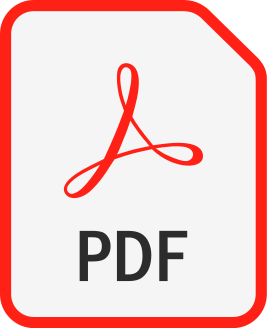 |
16. |
Czerkies M., Korwek Z., Prus W., Kochańczyk M., Jaruszewicz-Błońska J., Tudelska K.♦, Błoński S., Kimmel M.♦, Brasier A.R.♦, Lipniacki T., Cell fate in antiviral response arises in the crosstalk of IRF, NF-κB and JAK/STAT pathways,
Nature Communications, ISSN: 2041-1723, DOI: 10.1038/s41467-017-02640-8, Vol.9, pp.493-1-14, 2018 Abstract: The innate immune system processes pathogen-induced signals into cell fate decisions. How information is turned to decision remains unknown. By combining stochastic mathematical modelling and experimentation, we demonstrate that feedback interactions between the IRF3, NF-κB and STAT pathways lead to switch-like responses to a viral analogue, poly(I:C), in contrast to pulse-like responses to bacterial LPS. Poly(I:C) activates both IRF3 and NF-κB, a requirement for induction of IFNβ expression. Autocrine IFNβ initiates a JAK/STAT-mediated positive-feedback stabilising nuclear IRF3 and NF-κB in first responder cells. Paracrine IFNβ, in turn, sensitises second responder cells through a JAK/STAT-mediated positive feedforward pathway that upregulates the positive-feedback components: RIG-I, PKR and OAS1A. In these sensitised cells, the 'live-or-die' decision phase following poly(I:C) exposure is shorter—they rapidly produce antiviral responses and commit to apoptosis. The interlinked positive feedback and feedforward signalling is key for coordinating cell fate decisions in cellular populations restricting pathogen spread. Keywords: cellular signalling networks, innate immunity, regulatory networks, stochastic modelling Affiliations:
Czerkies M. | - | IPPT PAN | Korwek Z. | - | IPPT PAN | Prus W. | - | IPPT PAN | Kochańczyk M. | - | IPPT PAN | Jaruszewicz-Błońska J. | - | IPPT PAN | Tudelska K. | - | other affiliation | Błoński S. | - | IPPT PAN | Kimmel M. | - | Rice University (US) | Brasier A.R. | - | University of Texas Medical Branch (US) | Lipniacki T. | - | IPPT PAN |
| 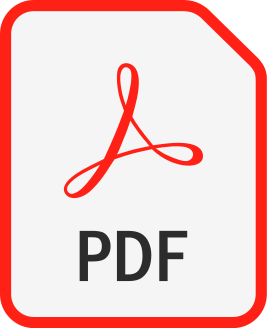 |
17. |
Małolepszy A.♦, Błoński S., Chrzanowska-Giżyńska J., Wojasiński M.♦, Płociński T.♦, Stobiński L.♦, Szymański Z., Fluorescent carbon and graphene oxide nanoparticles synthesized by the laser ablation in liquid,
APPLIED PHYSICS A-MATERIALS SCIENCE AND PROCESSING, ISSN: 0947-8396, DOI: 10.1007/s00339-018-1711-5, Vol.124, pp.282-1-7, 2018 Abstract: The results of synthesis of the fluorescent carbon dots (CDots) from graphite target and reduced graphene oxide (rGO) nanoparticles performed by the nanosecond laser ablation in polyethylene glycol 200 (PEG200) are shown. Two-step laser irradiation (first graphite target, next achieved suspension) revealed a very effective production of CDots. However, the ablation in PEG appeared to be effective with 1064 nm laser pulse in contrast to the ablation with 355 nm laser pulse. In the case of rGO nanoparticles similar laser irradiation procedure was less efficient. In both cases, received nanoparticles exhibited strong, broadband photoluminescence with a maximum dependent on the excitation wavelength. The size distribution for obtained CDots was evaluated using the DLS technique and HRTEM images. The results from both methods show quite good agreement in nanoparticle size estimation although the DLS method slightly overestimates nanoparticle's diameter Affiliations:
Małolepszy A. | - | Warsaw University of Technology (PL) | Błoński S. | - | IPPT PAN | Chrzanowska-Giżyńska J. | - | IPPT PAN | Wojasiński M. | - | Warsaw University of Technology (PL) | Płociński T. | - | Warsaw University of Technology (PL) | Stobiński L. | - | Warsaw University of Technology (PL) | Szymański Z. | - | IPPT PAN |
| 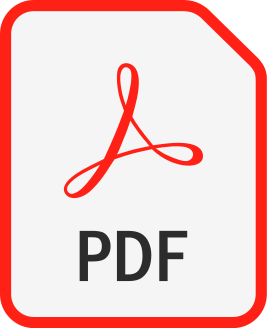 |
18. |
Zaremba D., Błoński S., Jachimek M.♦, Marijnissen M.J., Jakieła S.♦, Korczyk P.M., Investigations of modular microfluidic geometries for passive manipulations on droplets,
BULLETIN OF THE POLISH ACADEMY OF SCIENCES: TECHNICAL SCIENCES, ISSN: 0239-7528, DOI: 10.24425/119068, Vol.66, No.2, pp.139-149, 2018 Abstract: Multiple pipetting is a standard laboratory procedure resulting in the compartmentalisation of a liquid sample. Microfluidics offers techniques which can replace this process by the use of tiny droplets. Passive manipulation on droplets is an interesting and promising approach for the design of microfluidic devices which on one hand are easy-to-use and on the other, execute complex laboratory procedures. We present a comprehensive study of the geometry of microfluidic components which encode different operations on droplets into the structure of the device. The understanding of hydrodynamic interactions between the continuous flow and a droplet travelling through confined space of nontrivial microfluidic geometries is crucial for a rational and efficient design of new generation of modular microfluidic processors with embedded instructions. Keywords: microfluidics, two-phase flows, droplets Affiliations:
Zaremba D. | - | IPPT PAN | Błoński S. | - | IPPT PAN | Jachimek M. | - | other affiliation | Marijnissen M.J. | - | IPPT PAN | Jakieła S. | - | Institute of Physical Chemistry, Polish Academy of Sciences (PL) | Korczyk P.M. | - | IPPT PAN |
| 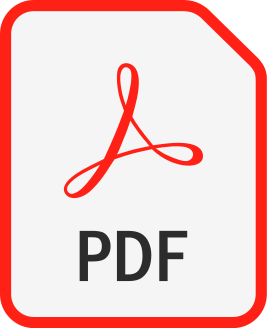 |
19. |
Tudelska K.♦, Markiewicz J., Kochańczyk M., Czerkies M., Prus W., Korwek Z., Abdi A.♦, Błoński S., Kaźmierczak B., Lipniacki T., Information processing in the NF-κB pathway,
Scientific Reports, ISSN: 2045-2322, DOI: 10.1038/s41598-017-16166-y, Vol.7, pp.15926-1-14, 2017 Abstract: The NF-κB pathway is known to transmit merely 1 bit of information about stimulus level. We combined experimentation with mathematical modeling to elucidate how information about TNF concentration is turned into a binary decision. Using Kolmogorov-Smirnov distance, we quantified the cell's ability to discern 8 TNF concentrations at each step of the NF-κB pathway, to find that input discernibility decreases as signal propagates along the pathway. Discernibility of low TNF concentrations is restricted by noise at the TNF receptor level, whereas discernibility of high TNF concentrations it is restricted by saturation/depletion of downstream signaling components. Consequently, signal discernibility is highest between 0.03 and 1 ng/ml TNF. Simultaneous exposure to TNF or LPS and a translation inhibitor, cycloheximide, leads to prolonged NF-κB activation and a marked increase of transcript levels of NF-κB inhibitors, IκBα and A20. The impact of cycloheximide becomes apparent after the first peak of nuclear NF-κB translocation, meaning that the NF-κB network not only relays 1 bit of information to coordinate the all-or-nothing expression of early genes, but also over a longer time course integrates information about other stimuli. The NF-κB system should be thus perceived as a feedback-controlled decision-making module rather than a simple information transmission channel. Keywords: cellular signaling networks, innate immunity, stress signaling Affiliations:
Tudelska K. | - | other affiliation | Markiewicz J. | - | IPPT PAN | Kochańczyk M. | - | IPPT PAN | Czerkies M. | - | IPPT PAN | Prus W. | - | IPPT PAN | Korwek Z. | - | IPPT PAN | Abdi A. | - | New Jersey Institute of Technology (US) | Błoński S. | - | IPPT PAN | Kaźmierczak B. | - | IPPT PAN | Lipniacki T. | - | IPPT PAN |
| 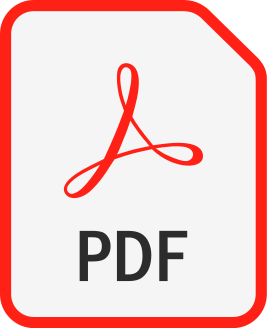 |
20. |
Jarecki L., Błoński S., Zachara A., Modeling of Pneumatic Melt Drawing of Poly‑L‑lactide Fibers in the Laval Nozzle,
Industrial and Engineering Chemistry Research, ISSN: 0888-5885, DOI: 10.1021/acs.iecr.5b02375, Vol.54, pp.10796-10810, 2015 Abstract: An air-drawing model of poly-l-lactide melt under a supersonic air jet in the Laval nozzle is presented. The aerodynamic fields are computed using the k–ω model. The pneumatic process is considered based on the mathematical model of melt spinning in single-, thin-filament approximation. Simultaneous acceleration of the air and the melt within the nozzle leads to fast attenuation of the filament. Air velocity dominates velocity of the filament and results in continual air-drawing on the entire spinning line. Oriented crystallization and nonlinear viscoelasticity effects under fast uniaxial elongation of the polymer melt are considered. The filament velocity at the collector increases significantly with increasing air compression, from the values typical for high-speed melt spinning up to values by two folds higher. The increase in filament velocity is limited by the effects of online oriented crystallization at higher air compressions. Influence of the inlet air compression, melt extrusion temperature and weight-average molecular weight on the axial profiles of the melt spinning functions is discussed, as well as on the development of amorphous orientation and online oriented crystallization. Keywords: Laval nozzle, Pneumatic melt spinning, Super-thin fibers, Oriented crystallization, Computer simulation, Polylactides Affiliations:
Jarecki L. | - | IPPT PAN | Błoński S. | - | IPPT PAN | Zachara A. | - | IPPT PAN |
| 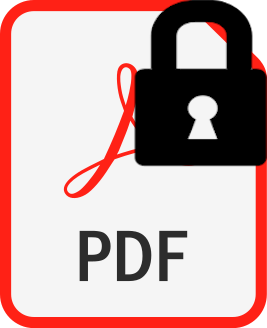 |
21. |
Blim A., Jarecki L., Błoński S., Modeling of pneumatic melt drawing of polypropylene super-thin fibers in the Laval nozzle,
BULLETIN OF THE POLISH ACADEMY OF SCIENCES: TECHNICAL SCIENCES, ISSN: 0239-7528, DOI: 10.2478/bpasts-2014-0005, Vol.62, No.1, pp.43-54, 2014 Abstract: Melt spinning of the fibers by supersonic air jet in the Laval nozzle is a novel, efficient and energy saving method of formation of super-thin fibers. In the process, polymer melt is extruded from a row of orifices and fast drawn by the pneumatic forces. In the modelling, air velocity, temperature and pressure distributions are computed from the k-! aerodynamic model. Computations of the polymer air-drawing dynamics are based on the mathematical model of melt spinning in a single-, thin-filament approximation and Phan-Thien/Tanner non-linear viscoelasticity of the polymer melt. Axial profiles of the polymer velocity, temperature, tensile stress and rheological extra-pressure are computed. Influence of the Laval nozzle geometry, initial air compression, an initial melt temperature, a polymer mass output and the diameter of the melt extrusion die is discussed. The role of the polymer molecular weight, melt viscosity and relaxation time is considered. Example computations show the influence of important processing and material parameters. In the supersonic process, a high negative internal extra-pressure is predicted in the polymer melt under high elongation rates which may lead to cavitation and longitudinal burst splitting of the filament into a high number of sub-filaments. A hypothetical number of sub-filaments at the splitting is estimated from an energetic criterion. The diameter of the sub-filaments may reach the range of nano-fibers. A substantial influence of the Laval nozzle geometry is also predicted. Keywords: air-drawing, Laval nozzle, pneumatic melt spinning, superthin fibers Affiliations:
Blim A. | - | IPPT PAN | Jarecki L. | - | IPPT PAN | Błoński S. | - | IPPT PAN |
| 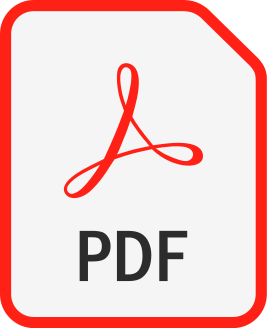 |
22. |
Węgrzyn J.♦, Samborski A.♦, Reissig L.♦, Korczyk P.M., Błoński S., Garstecki P.♦, Microfluidic architectures for efficient generation of chemistry gradations in droplets,
MICROFLUIDICS AND NANOFLUIDICS, ISSN: 1613-4982, DOI: 10.1007/s10404-012-1042-3, Vol.14, No.1, pp.235-245, 2013 Abstract: We demonstrate a strategy for construction of high-throughput microfluidic systems generating gradations of chemistry in micro-droplets. The productivity of the systems that we propose is limited only by the maximum rate of the droplet formation, and does not need to be limited by the rate of mixing. Multilayer polycarbonate chips transform two miscible input streams A and B into N streams of droplets, containing mixtures [A]i, [B]i. Exemplary devices generate linear ([B]i ∝ i) and logarithmic gradations (ln[B]i ∝ i). We also analyze the use of the same strategy for the generation of concentration gradation in the streams of droplets comprising mixtures of liquids of different viscosities. The devices preserve the required distribution of compositions, while allowing the volume of the droplets to be tuned over almost two orders of magnitude (i.e. between 3 and 80 nL). Keywords: Microfluidics, Generation of gradients, Droplet, Viscosity Affiliations:
Węgrzyn J. | - | other affiliation | Samborski A. | - | other affiliation | Reissig L. | - | Nagoya University (JP) | Korczyk P.M. | - | IPPT PAN | Błoński S. | - | IPPT PAN | Garstecki P. | - | Institute of Physical Chemistry, Polish Academy of Sciences (PL) |
| 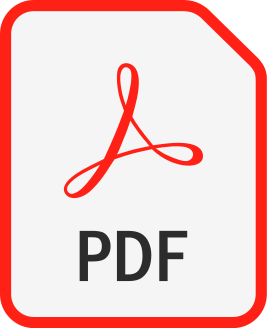 |
23. |
Jarecki L., Błoński S., Blim A., Zachara A., Modeling of pneumatic melt spinning processes,
JOURNAL OF APPLIED POLYMER SCIENCE, ISSN: 0021-8995, DOI: 10.1002/app.36575, Vol.125, No.6, pp.4402-4415, 2012 Abstract: Computer simulation of the pneumatic processes of fiber formation from the polymer melts is discussed. The dynamics of air-drawing of thin polymer streams in supersonic air jets formed in the Laval nozzle is presented versus the melt blowing process. In the Laval nozzle process, the air flow takes place with high Reynolds number and the k–omega model is used which considers kinetic energy of the air flow and the specific dissipation rate of the kinetic energy. For melt blowing, the air fields are simulated with the use of the k–epsilon turbulent model. The air velocity, temperature, and pressure distributions along the centerline of the air jets are considered in the modeling of both pneumatic processes. The air fields are predetermined at the absence of the polymer streams for several air compression values in the Laval nozzle inlet and several initial air velocities in the melt blowing process. Each polymer stream in a usual configuration of a single row of the filaments in the process is considered as non-interacting aerodynamically with other streams, and the air jet is assumed to be undisturbed by the polymer streams. Airdrawing of the polymer filaments is simulated as controlled by the distribution of air velocity, temperature, and pressure on the air jet centerline with the use of a stationary model of melt spinning in a single-, thin-filament approximation. Effects of non-linear viscoelasticity of the polymer melt subjected to fast uniaxial elongation are accounted for in the modeling. Strong influence of the air jet velocity, the melt viscosity which controls response of the polymer melt on the air-drawing forces, and the dieto-collector distance has been predicted. Influence of initial air temperature, geometry of the air die, initial velocity and temperature of the melt, extrusion orifice diameter can be also predicted from the model. The example computations concern air-drawing of isotactic polypropylene with the use of the Laval nozzle are compared with the predictions for the melt blowing process. Keywords: computer modeling, fibers, melt blowing, supersonic melt spinning, polypropylene Affiliations:
Jarecki L. | - | IPPT PAN | Błoński S. | - | IPPT PAN | Blim A. | - | IPPT PAN | Zachara A. | - | IPPT PAN |
| 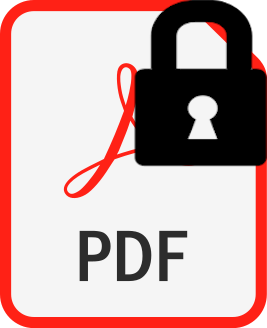 |
24. |
Szumbarski J.♦, Błoński S., Destabilization of laminar flow in a rectangular channel by transversely-oriented wall corrugation,
ARCHIVES OF MECHANICS, ISSN: 0373-2029, Vol.63, No.4, pp.393-428, 2011 Abstract: Linear stability of the flow through the transversely corrugated channel with flat sidewalls is investigated numerically. Two variants of the wall corrugation are considered: symmetric sinusoidal waviness of the top and bottom walls and onesided corrugation, i.e., one of the walls remains flat. Spectrally accurate Galerkin method formulated in a transformed domain is used for the solution of the main flow and linear stability equations. Unstable normal modes have been identified and their parametric variation has been determined. The results show that for sufficiently large aspect ratios, the influence of the sidewalls is weak and the stability properties resemble those of the spanwise-periodic channel (investigated recently by the first author). It means that an appropriately designed transversal corrugation may be regarded as a promising method for passive enhancement of mixing in laminar regime. Keywords: hydrodynamic stability, wavy channel, wall corrugation, laminar mixing Affiliations:
Szumbarski J. | - | other affiliation | Błoński S. | - | IPPT PAN |
| 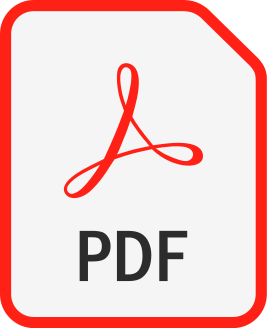 |
25. |
Błoński S., Domagalski P.♦, Dziubiński M.♦, Kowalewski T.A., Hydro-dynamically modified seeding for micro-PIV,
ARCHIVES OF MECHANICS, ISSN: 0373-2029, Vol.63, No.2, pp.163-182, 2011 Abstract: This paper presents numerical and experimental analysis of the hydrodynamic flow focusing in a rectangular microchannel. Aim of the study is to improve performance of the Particle Image Velocimetry (PIV) technique app lied to micro-scale flow analysis. The symmetric flow focusing system of two channels crossed at right angle is investigated. The numerical model is used to analyse the e ffect of Reynolds number on the flow focusing mechanism. In the experiment, the flow foc using is applied to concentrate seeding tracers into a thin sheet at the channel axis. Such a modification removes the out of focus images of the seeding particles, effe ctively improving PIV evaluation of vector fields in microchannel. Based on the exp erimental and numerical results we have found that expected improvement is possible for the flow at Reynolds number less than 10 only. Keywords: selective seeding, flow focusing Affiliations:
Błoński S. | - | IPPT PAN | Domagalski P. | - | other affiliation | Dziubiński M. | - | other affiliation | Kowalewski T.A. | - | IPPT PAN |
| 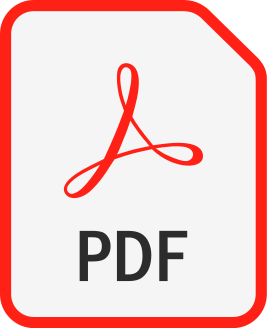 |
26. |
Jarecki L., Błoński S., Zachara A., Blim A., Computer modeling of pneumatic formation of superthin fibres,
COMPUTER METHODS IN MATERIALS SCIENCE / INFORMATYKA W TECHNOLOGII MATERIAŁÓW, ISSN: 1641-8581, Vol.11, No.1, pp.74-80, 2011 Abstract: Dynamics of a novel pneumatic process of superthin fibres formation from polymer melts in supersonic air jets in the Laval nozzle is studied using computer simulation. The approach bases on the mathematical k-w models of air flow in the nozzle and air drawing of polymer filaments in the coaxial air jet. The aerodynamic fields can be considered as undisturbed by presence of a single row of thin polymer filaments and predetermined air conditions are used in the modeling. The air fields are simulated for several values of the air compressions in the nozzle inlet and two nozzle geometries. Driving force of the Laval nozzle process results form air drag forces acting onto the filament surface. Mathematical model of stationary melt spinning in single-, thin-filament approximation is applied with the effects of non-linear viscoelasticity of the polymer melt accounted for. The model allows also to discuss non-linear stress-optical relationship reflecting online molecular orientation, as well as online crystallization of the polymer filament if it occurs. Negative rheological extra-pressure in the air-drawn filament is predicted, as resulting from non-linear viscoelasticity of the polymer melt subjected to high elongation rates. The negative extra-pressure could lead to cavitation and longitudinal burst splitting of each filament into a high number of superthin sub-filaments. A hypothetical mean diameter of the sub-filaments is estimated from an energetic criterion. Example computations of the dynamic profiles of air drawing and discussion concern isotactic polypropylene (iPP) subjected to the Laval nozzle process. Keywords: melt spinning, polymer air drawing, Laval nozzle process, superthin fibres Affiliations:
Jarecki L. | - | IPPT PAN | Błoński S. | - | IPPT PAN | Zachara A. | - | IPPT PAN | Blim A. | - | IPPT PAN |
| 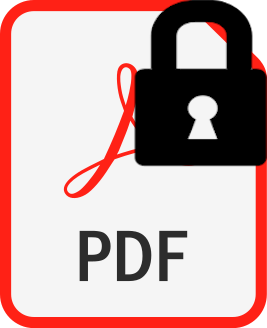 |
27. |
Szumbarski J.♦, Błoński S., Kowalewski T.A., Impact of transversely-oriented wall corrugation on hydraulic resistance of a channel flow,
Archive of Mechanical Engineering, ISSN: 0004-0738, Vol.LVIII, No.4, pp.441-466, 2011 Abstract: The impact of the transversely-oriented sinusoidal wall corrugation on the hydraulic drag is investigated numerically for the flow through the channel of finite width and with flat sidewalls. The numerical method, based on the domain transformation and Chebyshev-Galerkin discretization, is used to investigate the flow resistance of the laminar, parallel and pressure-driven flow. The obtained results are compared to the reference case, i.e., to the flow through the channel with rectangular cross section of the same aspect ratio. Simple explanation of the gain in the volumetric flow rate observed in the flow through spanwise-periodic channel with long-wave transversely-oriented wall corrugation is provided. In the further analysis, pressure drop in the flows with larger Reynolds numbers are studied numerically by means of the finite-volume commercial package Fluent. Preliminary experimental results confirm the predicted tendency. Keywords: Drug reduction, finite volume flow modeling, corrugated walls Affiliations:
Szumbarski J. | - | other affiliation | Błoński S. | - | IPPT PAN | Kowalewski T.A. | - | IPPT PAN |
| 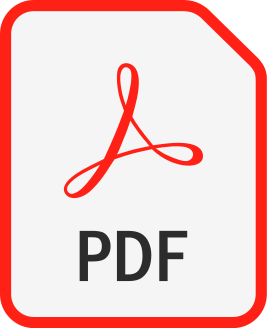 |
28. |
Bretcanu O.♦, Misra S.K.♦, Yunos D.M.♦, Boccaccini A.R.♦, Roy I.♦, Kowalczyk T., Błoński S., Kowalewski T.A., Electrospun nanofibrous biodegradable polyester coatings on Bioglass®-based glass-ceramics for tissue engineering,
MATERIALS CHEMISTRY AND PHYSICS, ISSN: 0254-0584, DOI: 10.1016/j.matchemphys.2009.08.011, Vol.118, pp.420-426, 2009 Abstract: Biodegradable polymeric nanofibrous coatings were obtained by electrospinning different polymers onto sintered 45S5 Bioglass®-based glass-ceramic pellets. The investigated polymers were poly(3-hydroxybutyrate) (P3HB), poly(3-hydroxybutyrate-co-hydroxyvalerate) (PHBV) and a composite of poly(caprolactone) (PCL) and poly(ethylene oxide) (PEO) (PCL–PEO). The fibrous coatings morphology was evaluated by optical microscopy and scanning electron microscopy. The electrospinning process parameters were optimised to obtain reproducible coatings formed by a thin web of polymer nanofibres. In-vitro studies in simulated body fluid (SBF) were performed to investigate the bioactivity and mineralisation of the substrates by inducing the formation of hydroxyapatite (HA) on the nanofiber-coated pellets. HA crystals were detected on all samples after 7 days of immersion in SBF, however the morphology of the HA layer depended on the characteristic fibre diameter, which in turn was a function of the specific polymer-solvent system used. The bioactive and resorbable nanofibrous coatings can be used to tailor the surface topography of bioactive glass-ceramics for applications in tissue engineering scaffolds. Keywords: Electrospinning, Nanofibers, Bioglass®, Polyhydroxyalkanoates, Tissue engineering Affiliations:
Bretcanu O. | - | other affiliation | Misra S.K. | - | other affiliation | Yunos D.M. | - | other affiliation | Boccaccini A.R. | - | Friedrich-Alexander University of Erlangen-Nürnberg (DE) | Roy I. | - | other affiliation | Kowalczyk T. | - | IPPT PAN | Błoński S. | - | IPPT PAN | Kowalewski T.A. | - | IPPT PAN |
| 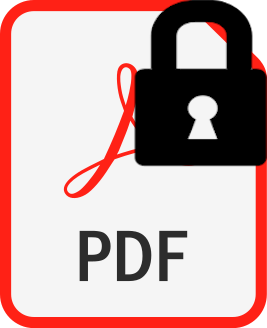 |
29. |
Błoński S., Analiza przejscia laminarno-turbulentnego w mikrokanalach,
Prace IPPT - IFTR Reports, ISSN: 2299-3657, Vol.2, 2009 | |
30. |
Licznar P.♦, Lomotowski J.♦, Błoński S., Ciach G.J.♦, Microprocessor field impactometer calibration: do we measure drops momentum or their kinetic energy?,
JOURNAL OF ATMOSPHERIC AND OCEANIC TECHNOLOGY, ISSN: 0739-0572, DOI: 10.1175/2007JTECHA938.1, Vol.25, pp.742-753, 2008 Abstract: This study presents the construction and calibration of a low-cost piezoelectric microprocessor impactometer designed for the field measurements of the rainfall kinetic energy (KE) flux. Its precise calibration was performed in laboratory conditions using waterdrops of different sizes and fall velocities. High-speed photography was applied to measure the velocity of each waterdrop. Although the impactometer constructed for this study is not able to measure the momentum of waterdrops, its accuracy for measuring their KE is excellent. It was found that the processing of the piezoelectric signal might determine which physical quantity is measured by different impactometers. It was also found that the distance between the waterdrop impact position and the impactometer center has a significant effect on the sensor output. A scheme to account for this effect is developed in this study, and the calibration curve for field applications of the impactometer is derived. In addition, an example comparison of the concurrent field measurements of KE flux using the impactometer and rainfall rates using a weighing rain gauge is given. Keywords: Rainfall, Dropsize distribution, Kinetic energy Affiliations:
Licznar P. | - | other affiliation | Lomotowski J. | - | other affiliation | Błoński S. | - | IPPT PAN | Ciach G.J. | - | other affiliation |
| 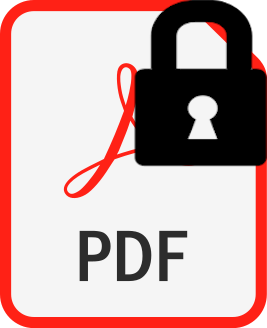 |
31. |
Kowalewski T.A., Błoński S., Korczyk P.M., Eksperymentalna analiza przeplywów w skali mikro i nano,
Wybrane zagadnienia przepływów i wymiany ciepła, Vol.6, pp.127-149, 2008 Keywords: mikroprzepływy, eksperymentalna mechanika płynów Affiliations:
Kowalewski T.A. | - | IPPT PAN | Błoński S. | - | IPPT PAN | Korczyk P.M. | - | IPPT PAN |
| |
32. |
Błoński S., Korczyk P.M., Kowalewski T.A., Analysis of turbulence in a micro-channel emulsifier,
INTERNATIONAL JOURNAL OF THERMAL SCIENCES, ISSN: 1290-0729, DOI: 10.1016/j.ijthermalsci.2007.01.028, Vol.46, pp.1123-1141, 2007 Abstract: Turbulent flow of water in an 1 mm long and 0.4 mm high gap of an emulsifier is investigated experimentally using micro-PIV technique and compared with numerical predictions. The purpose of the investigations is to develop a procedure for well-controlled generation of mono-disperse suspension of micro-droplets. The micro-flow measurements are based on epi-fluorescence illumination and high-speed imaging. The experimental data are compared with the numerical results obtained using direct simulation and turbulent flow model. From the turbulent modelling (k−ε) was found that, the maximum of turbulent energy dissipation rate takes place mainly in the micro-channel gap. However, measured and directly simulated (DNS) velocity fields indicate that flow turbulization is delayed and develops shortly behind the gap. Experimental and numerical results are used to predict droplet dimension of two different oil emulsions. Very low amount of oil-phase fraction in investigated emulsions justifies us to use flow characteristics evaluated for pure water to predict mean diameter of oil droplets. These predictions are validated using experimental data on statistics of droplets size. Keywords: Micro-flow, Micro-PIV, Particle Image Velocimetry, Turbulence, Micro-channel, Emulsion Affiliations:
Błoński S. | - | IPPT PAN | Korczyk P.M. | - | IPPT PAN | Kowalewski T.A. | - | IPPT PAN |
| 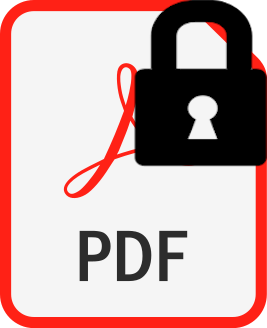 |
33. |
Błoński S., Kowalewski T.A., PIV analysis of turbulent flow in a micro-channel,
JOURNAL OF THEORETICAL AND APPLIED MECHANICS, ISSN: 1429-2955, Vol.45, pp.489-503, 2007 Abstract: Turbulent flow of water in a short 0.4 mm high micro-channel of an emulsifier is investigated experimentally using a micro-PIV technique and compared with numerical predictions. The micro-flow measurements are based on epi-fluorescence illumination and high-speed imaging. Velocity fields obtained from the measurements and direct numerical simulations indicate that flow turbulization is delayed and develops only at the outlet region of the micro-channe Keywords: micro-channel, micro-PIV, turbulence Affiliations:
Błoński S. | - | IPPT PAN | Kowalewski T.A. | - | IPPT PAN |
| 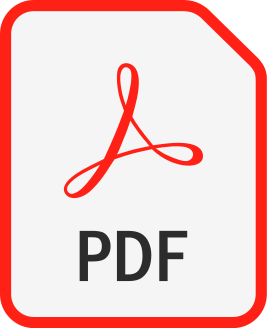 |
34. |
Sielamowicz I.♦, Błoński S., Kowalewski T.A., Digital Particle Image Velocimetry (DPIV) technique in measurements of granular material flows, Part 2 of 3 - converging hoppers,
CHEMICAL ENGINEERING SCIENCE, ISSN: 0009-2509, Vol.61, pp.5307-5317, 2006 Abstract: The flow evolution of an amaranth seed is being investigated in a wedge-shaped model made of Plexiglas. The objective of this paper is to recognise flow patterns in the flowing material, and also to depict evolution of velocity fields, flow field discontinuities, velocity profiles for cross-sections of the model, shear zones and flow streamlines using the digital particle image velocimetry (DPIV) optical technique. It is demonstrated that the DPIV technique used in the experiments enables quantitative analysis of the flow zones geometry. The technique also allows to reveal boundaries between flowing and stagnant zones and to extract velocity profiles at any selected sections of the model. Keywords: Optical technique, DPIV, Granular material flows, Converging hopper, Particle, Plug flow, Shear zones, Discharge flow rate Affiliations:
Sielamowicz I. | - | University of Zielona Góra (PL) | Błoński S. | - | IPPT PAN | Kowalewski T.A. | - | IPPT PAN |
| 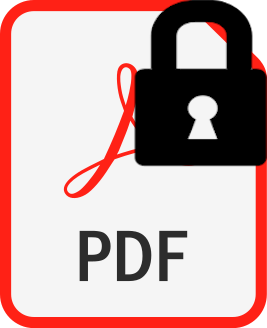 |
35. |
Sielamowicz I.♦, Kowalewski T.A., Błoński S., Optical technique DPIV in measurements of granular material flows, Part 1/3 - plane hoppers,
CHEMICAL ENGINEERING SCIENCE, ISSN: 0009-2509, DOI: 10.1016/j.ces.2004.07.135, Vol.60, pp.589-598, 2005 Abstract: The aim of this paper is to present the evolution of plug flow developing in three densely packed granular materials in the model of a hopper made of Plexiglas. For this purpose, the digital particle image velocimetry (DPIV) technique is applied to analyse the flow field of the granular material. When discharge starts, a plug flow zone in the flowing material expands upward. This zone changes its width reaching the upper surface of the material. The plug flow evolution as a function of time is described using DPIV. This technique yields the velocity profiles of flowing granular materials, velocity magnitude contours, vector fields, velocity distributions on certain levels in the model and traces of the selected particles. The results obtained for the evolution of the vertical velocity, height and width of the plug flow zone as a function of time, measured at the symmetry axis of the model for the amarantus seed are compared to the results obtained by Waters and Drescher. Measurements of the stagnant boundary as a function of time are compared to the results available in the literature Keywords: Optical technique, Experiments, Granular, Materials, Flow, Particle, Plug flow Affiliations:
Sielamowicz I. | - | University of Zielona Góra (PL) | Kowalewski T.A. | - | IPPT PAN | Błoński S. | - | IPPT PAN |
| 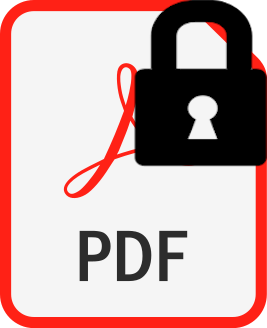 |
36. |
Kowalewski T.A., Błoński S., Barral S., Experiments and modelling of electrospinning process,
BULLETIN OF THE POLISH ACADEMY OF SCIENCES: TECHNICAL SCIENCES, ISSN: 0239-7528, Vol.53, No.4, pp.385-394, 2005 Abstract: Very thin liquid jets can be obtained using electric field, whereas an electrically-driven bending instability occurs that enormously increases the jet path and effectively leads to its thinning by very large ratios, enabling the production of nanometre size fibres. This mechanism, although it was discovered almost one century ago, is not yet fully understood. In the following study, experimental data are collected, with the dual goal of characterizing the electro-spinning of different liquids and evaluating the pertinence of a theoretical model. Keywords: nanofibres, electrospinning, polymer fibres, electrified liquid jet Affiliations:
Kowalewski T.A. | - | IPPT PAN | Błoński S. | - | IPPT PAN | Barral S. | - | IPPT PAN |
| 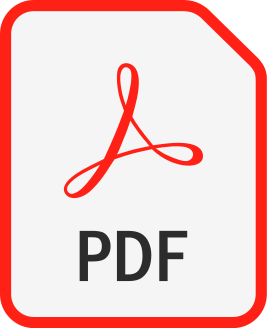 |