1. |
Barwińska I., Kopeć M., Kukla D., Senderowski C.♦, Kowalewski Z.L., Thermal Barrier Coatings for High-Temperature Performance of Nickel-Based Superalloys: A Synthetic Review,
Coatings, ISSN: 2079-6412, DOI: 10.3390/coatings13040769, Vol.13, No.4, pp.1-21, 2023 Abstract: With the rising demands of industry to increase the working temperature of gas turbine blades and internal combustion engines, thermal barrier coatings (TBC) were found to be an effective way to further enhance the lifetime of aero components through the improvement of mechanical properties and oxidation-resistance. Thus, this paper aims to review coating technologies with special emphasis on plasma-sprayed thermal barrier coatings (PS), and those produced by physical vapor deposition (PVD) and chemical vapor deposition (CVD) methods. Each technology was assessed in terms of its effectiveness to enhance the mechanical response and oxidation resistance of nickel-based parts working at high temperature. The effect of coating technology on mechanical strength, hardness, fatigue and creep of nickel alloys was discussed to reveal the potential candidates for future applications in aggressive environments Keywords: high temperature corrosion, fatigue, creep, aggressive environment, turbine blade Affiliations:
Barwińska I. | - | IPPT PAN | Kopeć M. | - | IPPT PAN | Kukla D. | - | IPPT PAN | Senderowski C. | - | other affiliation | Kowalewski Z.L. | - | IPPT PAN |
| 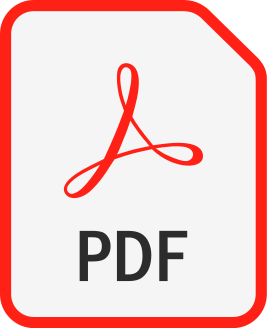 |
2. |
Senderowski C.♦, Panas A.J.♦, Fikus B.♦, Zasada D.♦, Kopeć M., Korytchenko K.V.♦, Effects of heat and momentum gain differentiation during gas detonation spraying of FeAl powder particles into the water,
Materials, ISSN: 1996-1944, DOI: 10.3390/ma14237443, Vol.14, No.23, pp.7443-1-18, 2021 Abstract: In this paper, dynamic interactions between the FeAl particles and the gaseous detonation stream during supersonic D-gun spraying (DGS) conditions into the water are discussed in detail. Analytical and numerical models for the prediction of momentum and complex heat exchange, that includes radiative effects of heat transfer between the FeAl particle and the D-gun barrel wall and phase transformations due to melting and evaporation of the FeAl phase, are analyzed. Phase transformations identified during the DGS process impose the limit of FeAl grain size, which is required to maintain a solid state of aggregation during a collision with the substrate material. The identification of the characteristic time values for particle acceleration in the supersonic gas detonation flux, their convective heating and heat diffusion enable to assess the aggregation state of FeAl particles sprayed into water under certain DGS conditions Keywords: D-gun spraying, FeAl intermetallic powder, gas detonation flux, heat transfer, two-phase metallization stream, particle thermal history Affiliations:
Senderowski C. | - | other affiliation | Panas A.J. | - | other affiliation | Fikus B. | - | other affiliation | Zasada D. | - | other affiliation | Kopeć M. | - | IPPT PAN | Korytchenko K.V. | - | other affiliation |
| 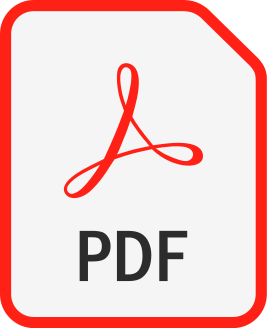 |
3. |
Kukla D., Kopeć M., Wang K.♦, Senderowski C.♦, Kowalewski Z.L., Nondestructive methodology for identification of local discontinuities in aluminide layer-coated Mar 247 during its fatigue performance,
Materials, ISSN: 1996-1944, DOI: 10.3390/ma14143824, Vol.14, No.14, pp.3824-1-13, 2021 Abstract: In this paper, the fatigue performance of the aluminide layer-coated and as-received MAR 247 nickel superalloy with three different initial microstructures (fine grain, coarse grain and column-structured grain) was monitored using nondestructive, eddy current methods. The aluminide layers of 20 and 40 µm were obtained through the chemical vapor deposition (CVD) process in the hydrogen protective atmosphere for 8 and 12 h at the temperature of 1040 °C and internal pressure of 150 mbar. A microstructure of MAR 247 nickel superalloy and the coating were characterized using light optical microscopy (LOM), scanning electron microscopy (SEM) and X-ray energy dispersive spectroscopy (EDS). It was found that fatigue performance was mainly driven by the initial microstructure of MAR 247 nickel superalloy and the thickness of the aluminide layer. Furthermore, the elaborated methodology allowed in situ eddy current measurements that enabled us to localize the area with potential crack initiation and its propagation during 60,000 loading cycles. Keywords: chemical vapor deposition, nickel alloys, aluminide coatings, fatigue, eddy current Affiliations:
Kukla D. | - | IPPT PAN | Kopeć M. | - | IPPT PAN | Wang K. | - | Imperial College London (GB) | Senderowski C. | - | other affiliation | Kowalewski Z.L. | - | IPPT PAN |
| 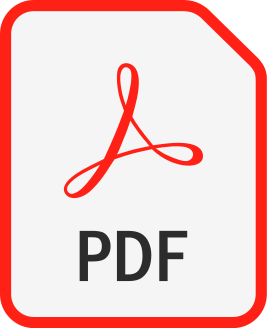 |
4. |
Kopeć M., Kukla D., Yuan X.♦, Rejmer W.♦, Kowalewski Z.L., Senderowski C.♦, Aluminide thermal barrier coating for high temperature performance of MAR 247 nickel based superalloy,
Coatings, ISSN: 2079-6412, DOI: 10.3390/coatings11010048, Vol.11, No.1, pp.48-1-12, 2021 Abstract: In this paper, mechanical properties of the as-received and aluminide layer coated MAR 247 nickel based superalloy were examined through creep and fatigue tests. The aluminide layer of 20 µm was obtained through the chemical vapor deposition (CVD) process in the hydrogen protective atmosphere for 8 h at the temperature of 1040 °C and internal pressure of 150 mbar. A microstructure of the layer was characterized using the scanning electron microscopy (SEM) and X-ray Energy Dispersive Spectroscopy (EDS). It was found that aluminide coating improve the high temperature fatigue performance of MAR247 nickel based superalloy at 900 °C significantly. The coated MAR 247 nickel based superalloy was characterized by the stress amplitude response ranging from 350 MPa to 520 MPa, which is twice as large as that for the uncoated alloy. Keywords: chemical vapor deposition, nickel alloys, aluminide coatings, high temperature fatigue, creep Affiliations:
Kopeć M. | - | IPPT PAN | Kukla D. | - | IPPT PAN | Yuan X. | - | Imperial College London (GB) | Rejmer W. | - | other affiliation | Kowalewski Z.L. | - | IPPT PAN | Senderowski C. | - | other affiliation |
| 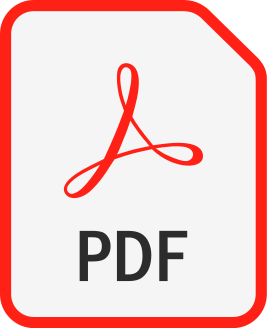 |
5. |
Kukla D., Kopeć M., Kowalewski Z.L., Politis D.J.♦, Jóźwiak S.♦, Senderowski C.♦, Thermal barrier stability and wear behavior of CVD deposited aluminide coatings for MAR 247 nickel superalloy,
Materials, ISSN: 1996-1944, DOI: 10.3390/ma13173863, Vol.13, No.17, pp.3863-1-11, 2020 Abstract: In this paper, aluminide coatings of various thicknesses and microstructural uniformity obtained using chemical vapor deposition (CVD) were studied in detail. The optimized CVD process parameters of 1040 °C for 12 h in a protective hydrogen atmosphere enabled the production of high density and porosity-free aluminide coatings. These coatings were characterized by beneficial mechanical features including thermal stability, wear resistance and good adhesion strength to MAR 247 nickel superalloy substrate. The microstructure of the coating was characterized through scanning electron microscopy (SEM), X-ray energy dispersive spectroscopy (EDS) and X-ray diffraction (XRD) analysis. Mechanical properties and wear resistance of aluminide coatings were examined using microhardness, scratch test and standardized wear tests, respectively. Intermetallic phases from the Ni-Al system at specific thicknesses (20-30 µm), and the chemical and phase composition were successfully evaluated at optimized CVD process parameters. The optimization of the CVD process was verified to offer high performance coating properties including improved heat, adhesion and abrasion resistance. Keywords: chemical vapor deposition, nickel alloys, coatings, X-ray analysis Affiliations:
Kukla D. | - | IPPT PAN | Kopeć M. | - | IPPT PAN | Kowalewski Z.L. | - | IPPT PAN | Politis D.J. | - | Imperial College London (GB) | Jóźwiak S. | - | Military University of Technology (PL) | Senderowski C. | - | other affiliation |
| 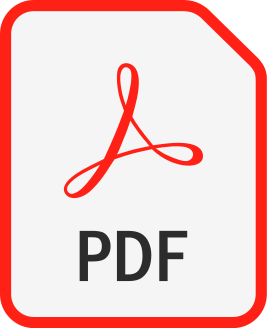 |