1. |
Broniszewska-Wojdat P., Pawłowski P., Anodizing of cast and additively manufactured AlSi10Mg alloy,
ICASS, 6th International Conference on Applied Surface Science, 2024-06-17/06-20, Wuzhen (CN), pp.1-1, 2024 | 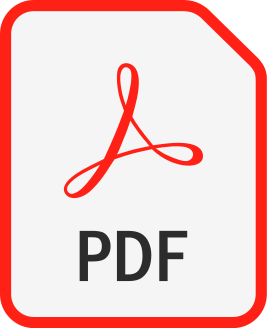 |
2. |
Broniszewska-Wojdat P., Pawłowski P., Comparison of oxide layers manufactured by Plasma Electrolytic Oxidation on the AlSi10Mg alloy manufactured by casting and 3d printing,
PSE 2024, 19th International Conference on Plasma Surface Engineering, 2024-09-02/09-05, Erfurt (DE), pp.1-1, 2024 Abstract: Additive manufacturing, widely called 3d printing, allows to create new quality of metal products. A microstructure of 3d printed AlSi10Mg alloy can be described as an eutectic area surrounded by Si-network. Eutectic, fine-grain microstructure improves durability of material in comparison to cast, dendritic aluminium alloys. The presence of Si particles is challenging for electrochemical surface treatments, for instance to anodizing. In this study, Plasma Electrolytic Oxidation (PEO) – the most environmentally-friendly kind of anodizing – was performed on the cast AlSi10Mg and on the 3d printed AlSi10Mg specimens. Keywords: 3d printing, Laser Powder Bed Fusion Process,Plasma Electrolytic Oxidation, aluminium Affiliations:
Broniszewska-Wojdat P. | - | IPPT PAN | Pawłowski P. | - | IPPT PAN |
| 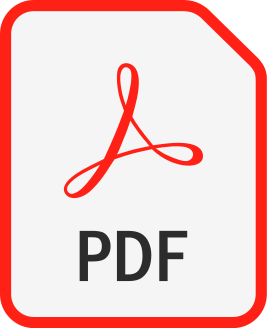 |
3. |
Broniszewska-Wojdat P., Pawłowski P., Microstructure impact of additively manufactured and cast Al-Si alloy on the chosen properties of PEO oxide coatings,
NTEM 1, Spring School for Young Researchers, New Trends in Experimental Mechanics, 2024-05-13/05-17, Zakopane (PL), pp.38-38, 2024 | 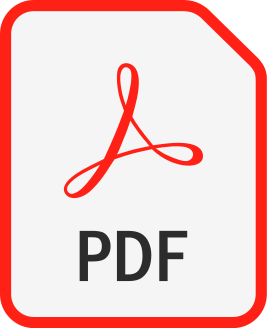 |
4. |
Broniszewska P., Pawłowski P., Plasma Electrolytic Oxidation of additively manufactured AlSi10Mg alloy,
PLATHINIUM 2023, PLASMA THIN FILM INTERNATIONAL UNION MEETING, 2023-09-11/09-15, Antibes, French Riviera (FR), pp.184-184, 2023 Abstract: Plasma Electrolytic Oxidation (PEO) is the most advanced of the anodizing methods. In comparison to traditional anodizing PEO provides coatings with higher wear- and corrosion- resistance and hardness. Moreover, PEO is carried out in an alkalic bath, instead of strong acids, which makes this method more environmentally friendly. PEO is an excellent surface treatment for light metals, like magnesium or aluminium. More often light metals are produced by additive technologies (3d printing). The microstructure of additively manufactured alloys strongly differs from casting alloys. Characteristic melting pools are observed. AlSi10Mg alloy presents eutectic structure surrounded by Si-net. The microstructure is strongly connected to laser paths. Fine-grain microstructure results in higher strength than cast alloy. In this study, traditional anodizing, hard anodizing (HA) and PEO were carried out on AlSi10Mg manufactured by Direct Metal Laser Sintering (DMLS). Moreover, PEO was also performed on cast AlSi10Mg alloy. Thin, conversion coatings were obtained (thickness under 10 μm). A microstructure of oxide coatings was observed. Scratch resistance was tested and allowed to describe the films' adhesion. PEO coatings are vastly porous and include more SiO2 oxides than traditional and HA coatings. SiO2 oxides are more difficult to obtain as silicon has higher resistance than aluminium. Moreover, PEO guarantees more phase-mixed surface microstructure, including amorphous, ceramic phases, which cannot be formed in low-voltage processes. In comparison to traditional and HA oxide coatings, PEO coatings exhibit better adhesion and scratch resistance. Traditional anodizing and hard anodizing on additively manufactured AlSi10Mg provide the critical load LC1 at which coating begins to be broken of 8.5N and 10N respectively. A similar LC1 value can be obtained for PEO performed on cast alloy (7.8N), while in the case of additively manufactured AlSi10Mg this LC1 is increased four times to 42.1N. Keywords: Additive manufacturing, Plasma Electrolytic Oxidation, Aluminium alloys AlSi10Mg Affiliations:
Broniszewska P. | - | IPPT PAN | Pawłowski P. | - | IPPT PAN |
| 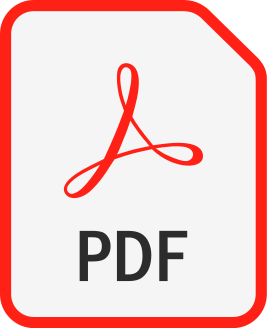 |
5. |
Broniszewska P., Anodic Oxidation of AlSi10Mg Alloy Manufactured by DMLS,
AMM, ADDITIVE MANUFACTURING MEETING 2019, 2019-09-18/09-19, Wrocław (PL), pp.38, 2019 Abstract: Direct Metal Laser Sintering is a powder bed fusion process, which allows direct production of elements with complex shapes and very good mechanical properties. However, regardless of manufacturing technology elimination of some materials’ weaknesses is definitely tough to eliminate. These weaknesses might be excluded by surface engineering.This poster presents results of producing oxidized films on AlSi10Mg alloy manufactured by Direct Metal Laser Sintering using EOSM280 system equipped with 400W Yb fiber laser and standard EOS AlSi10Mg powder. AlSi10Mg is a near-eutectic die casting alloy which is applied to automotive and aviation industries. The density of printed samples was under 99%. We used 3 different methods of oxidation: traditional electrochemical oxidation, electrochemical oxidation in lower temperature (hard anodizing) and plasma electrochemical oxidation. Processes lasted 20 or 25 minutes. Traditional and hard anodizing was carried out in H2SO4 with the voltage in the range of 18.5-32.5 V. Plasma oxidation was carried out in 2 g/l KOH + 4 g/l Na2SiO3 and the applied voltage was between 190 and 225 V. Metallography, SEM and EDS proved that we received Al2O3 oxides on the AlSi10Mg surfaces. All produced films were thin (2-5 um), providing slightly increased microhardness and roughness of the surface. Roughness depends especially on electric current parameters applied in the oxidation process. Therefore the structure of layers manufactured by plasma electrochemical oxidation was more irregular and porous. All films had high adhesion which was confirmed by scratch tests. Keywords: DMLS, electrochemical oxidation, anodizing, aluminum alloy, AlSi10Mg Affiliations:
Broniszewska P. | - | IPPT PAN |
| 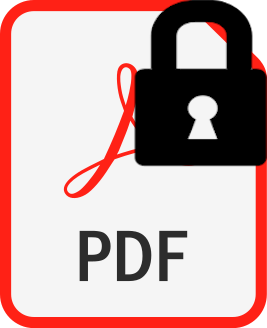 |