1. |
Haponova O., Tarelnyk V.♦, Tarelnyk N.♦, Laponog G.♦, Investigation of Aluminum Electrospark Alloyed Coatings on Steels,
METALLURGICAL AND MATERIALS TRANSACTIONS A-PHYSICAL METALLURGY AND MATERIALS SCIENCE, ISSN: 1073-5623, DOI: 10.1007/s11661-025-07908-z, Vol.56, pp.4204-4229, 2025 Streszczenie: The paper presents a study of the structure-phase state of aluminised coatings obtained by the electrospark alloying (ESA) method. The influence of the discharge energy and the productivity of the treatment process on the thickness of the hardened layer, its microhardness, continuity and surface roughness of C20 and C40 steels has been studied. It is shown that the structure of ESA coatings consists of a white layer, a diffusion zone and a substrate metal. Increasing the discharge energy during ESA leads to a change in the chemical and phase composition of the layer. With a 2-fold decrease in ESA productivity, the thickness of the “white” layer increases to 75 to 110 µm, its microhardness to 7450 MPa; the continuity of the coating tends to 100 pct. With a 4-fold decrease in ESA productivity, the thickness of the ‘white’ layer also increases, but not intensively, to 60 µm at Wp = 4.6 J and then does not change; at the same time, the surface roughness Ra increases to 8.1 to 9.0 µm and the continuity is 95 pct. A 4-fold decrease in process productivity contributes to the deterioration of coating quality parameters and an increase in roughness. The study of the influence of the energy parameters of ESA, as well as the alloying time (‘productivity’) of the process, is important for the improvement of hardening technology. The paper proposes a mathematical model for predicting the coating parameters taking into account the processing time of a given plane to be alloyed, i.e., the labour intensity of the ESA process (the value of the inverse productivity). The equations of the mathematical model and methods for determining the constants of the equations for predicting the parameters of the alloyed layer have been obtained. An algorithm has been developed and the adequacy of the mathematical model has been verified, which allows the prediction of the main technological parameters of ESA in order to obtain a coating with the specified quality indicators. Afiliacje autorów:
Haponova O. | - | IPPT PAN | Tarelnyk V. | - | Sumy National Agrarian University (UA) | Tarelnyk N. | - | Sumy National Agrarian University (UA) | Laponog G. | - | inna afiliacja |
| 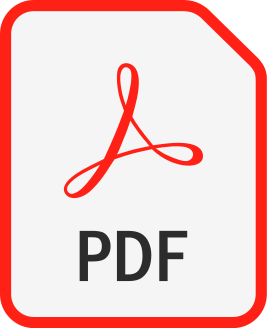 | 200p. |
2. |
Haponova O., Tarelnyk V.♦, Mościcki T., Tarelnyk N.♦, Hybrid Surface Treatment Technologies Based on the Electrospark Alloying Method: A Review,
Coatings, ISSN: 2079-6412, Vol.15, No.6, pp.1-26, 2025 Streszczenie: Technologies for functional coatings are evolving rapidly, with electrospark alloying (ESA) emerging as a promising method for surface modification due to its efficiency and localized impact. This review analyzes the fundamental principles of ESA and the effects of process parameters on coating characteristics and highlights its advantages and limitations. Particular attention is given to hybrid ESA-based technologies, including combinations with laser treatment, plastic deformation, vapor deposition, and polymer-metal overlays. These hybrid methods significantly improve coating quality by enhancing hardness, adhesion, and structural integrity and reducing roughness and defects. However, the multi-parameter nature of these processes presents optimization challenges. This review identifies knowledge gaps related to process reproducibility, control of microstructure formation, and long-term performance under service conditions. Recent breakthroughs in combining ESA with high-energy surface treatments are discussed. Future research should focus on systematic parameter optimization, in situ diagnostics, and predictive modeling to enable the design of application-specific hybrid coatings. Słowa kluczowe: electrospark alloying, hybrid technologies, surface plastic deformation, laser treatment, vapor phase deposition, metal–polymer material, coating, structure, properties, roughness, coating quality, sustainable development goals Afiliacje autorów:
Haponova O. | - | IPPT PAN | Tarelnyk V. | - | Sumy National Agrarian University (UA) | Mościcki T. | - | IPPT PAN | Tarelnyk N. | - | Sumy National Agrarian University (UA) |
| 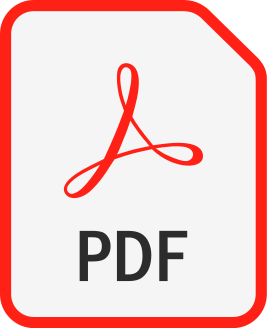 | 100p. |
3. |
Tarelnyk V.♦, Haponova O., Tarelnyk N.♦, Konoplianchenko Y.♦, Sulphurizing of Metal Surfaces by Electrospark-Discharge Alloying. Pt. 2: Tribological Properties of Electrospark Depositing Sulphur-Containing Coating,
Uspekhi Fiziki Metallov, ISSN: 1608-1021, Vol.26, No.2, pp.111-222, 2025 Streszczenie: The essence and technological characteristics of the electrospark alloying (ESA) process, its advantages and disadvantages have been considered in order to use it to improve the tribological properties of bronze and steel parts. A generalization of the available data and results in the literature concerned with the ESA process has been made. Based on the published data, a comparative analysis of various methods for forming combined electrospark coatings (CESC) on bronzes, which include sulphur, the influence of the mode parameters and the compositions of the CESC on the microstructure, mechanical and tribological properties are represented. The methods for practical application in production have been proposed. The methods for forming the self-lubricating electrospark coatings containing molybdenum disulphide on steel substrates have been investigated. There have been represented physical and mechanical characteristics of the coatings, which had been obtained using different strategies, as well as there has been disclosed the nature of their changes depending on the technological parameters of the ESA modes and the types of the starting materials for the anode and cathode, and on the compositions of the environment wherein the ESA process takes place. There have been given the summarized data on the tribological properties of the coatings, which had been obtained on some steel grades using different electrode materials and modes of operation. As demonstrated, the ESA method can be successfully used to reduce the coefficient of friction and to increase the wear resistance of bronze and steel surfaces. There have been specified the proposed electrode materials and ESA process parameters for modifying the surfaces made of some bronzes and steels. Słowa kluczowe: technology, electrospark alloying, coating, microstructure, tribotechnical properties Afiliacje autorów:
Tarelnyk V. | - | Sumy National Agrarian University (UA) | Haponova O. | - | IPPT PAN | Tarelnyk N. | - | Sumy National Agrarian University (UA) | Konoplianchenko Y. | - | inna afiliacja |
| | 70p. |
4. |
Tarelnyk V.♦, Haponova O., Tarelnyk N.♦, Konoplianchenko Y.♦, Sulphurizing of Metal Surfaces by Electrospark-Discharge Alloying. Pt. 1: Structural–Phase State of Sulphur-Containing Coatings on Constructional Steels,
Uspekhi Fiziki Metallov, ISSN: 1608-1021, Vol.26, No.1, pp.146-200, 2025 Streszczenie: The methods of surface sulphur saturation of metal surfaces to provide them with special tribotechnical properties are reviewed and analysed. The main attention is focused on technologies based on the method of electrospark alloying (ESA). As shown, the process of sulphur saturation can be realised by using a special sulphur-containing saturating technical substance (STS). The methods of forming sulphided, sulphocarburized, sulphoaluminized, Al–C–S, and sulphomolybdenum coatings on steels using STS by ESA are considered. The results of sulphur distribution in the surface layer during ESA sulphurizing with a metal electrode using STS are presented. As shown, the sulphur concentration on the surface is of about 0.53–0.60% that gradually decreases deeper into the substrate. The topography of the treated surface and its structure after sulphocarburized of steel surfaces with a graphite electrode using STS containing sulphur are investigated. As found, the coating consists of several layers: a ‘soft’ layer saturated with sulphur, a hardened layer saturated with carbon, and the substrate metal. The thickness, microhardness, and continuity of the coating increase with the discharge energy. The qualitative parameters of sulphoaluminized coatings obtained by the ESA method with an aluminium electrode using STS are analysed. The microstructures reveal three zones: a near-surface, non-continuous loose layer with sulphur enrichment, 10–100-µm thick, and microhardness of 1368–2073 MPa; a ‘white’ hardened layer containing aluminium, 20–40 µm-thick, and microhardness of 4094–5157 MPa; a diffusion zone; and a substrate material. The sulphoaluminized-coatings’ phase composition depends on the ESA energy parameters. Intermetallics FeAl and FeAl2 are formed in the surface layer. The structural–phase state and properties of sulphomolybdenum coatings obtained by the ESA method with a molybdenum electrode using STS are discussed. The near-surface loose layer saturated with sulphur contains up to 8% of molybdenum disulphide formed due to ESA. Beneath this layer is a hardened layer saturated with molybdenum and having a microhardness of 10596–10731 MPa. It is proposed to use sulphurizing methods based on ESA using STS as cheap and effective methods of surface modification of friction surfaces to reduce seizure and friction coefficient. Słowa kluczowe: sulphurizing, electrospark alloying, coating, microstructure, tribotechnical properties Afiliacje autorów:
Tarelnyk V. | - | Sumy National Agrarian University (UA) | Haponova O. | - | IPPT PAN | Tarelnyk N. | - | Sumy National Agrarian University (UA) | Konoplianchenko Y. | - | inna afiliacja |
| 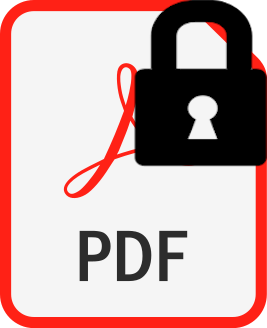 | 70p. |
5. |
Tarelnyk V.♦, Haponova O., Tarelnyk N.♦, Dumanchuk M.♦, Maifat M.♦, Gerasimenko V.♦, Mikulina M.♦, Polyvanyi A.♦, Ohrimenko V.♦, Semernya O.♦, Vasylenko M.♦, Kozin V.♦, Surface Properties of HighStrength Cast Iron Parts with Wear-Resistant Composite Coatings Synthesized by Electrospark Alloying Method. Pt. 1. Specific Aspects of Mass Transfer; Geometric, Topographic, and Mechanical Characteristic Features of Strengthened Surfaces,
Metallofizika i Noveishie Tekhnologii, ISSN: 1024-1809, Vol.47, No.4, pp.427-451, 2025 | 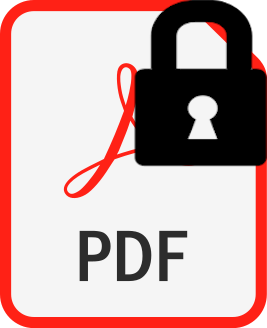 | 40p. |
6. |
Tarelnyk V.♦, Haponova O., Tarelnyk N.♦, Rogovskii I.♦, IMPROVEMENT OF SURFACE LAYER QUALITY PARAMETERS OF STEEL PARTS AFTER NITROСARBURUZING BY ELECTROSPARK ALLOYING METHOD
Part 1 FEATURES OF THE STRUCTURAL STATE AND TOPOGRAPHY OF STEEL SURFACES AFTER NITROCARBURIZING,
Problems of Atomic Science and Technology, ISSN: 1562-6016, Vol.156, No.2, pp.131-137, 2025 Streszczenie: The paper analyses modern methods for improving the surface quality of steel parts of nuclear power plant pumps. The aim of the work was to improve the technology of nitrocarburisation by the method of electrospark alloying (ESA) by studying the effect of the ESA process performance on the quality parameters of the formed surfaces. As a result of the studies, the dependence of the quality parameters of the surfaces of steel parts during nitrocarburizing by the ESA method on the energy parameters of the equipment (discharge energy Wp) and the technological parameters of the process (productivity Q) was established. Experimental studies have shown that as Wp increases, the thickness of the hardened layer, its microhardness and continuity, and surface roughness grow. As Q decreases, the thickness, microhardness and continuity of the hardened layer rise, while the roughness remains practically unchanged. The proposed technology can be recommended for implementation in manufacturing Afiliacje autorów:
Tarelnyk V. | - | Sumy National Agrarian University (UA) | Haponova O. | - | IPPT PAN | Tarelnyk N. | - | Sumy National Agrarian University (UA) | Rogovskii I. | - | inna afiliacja |
| 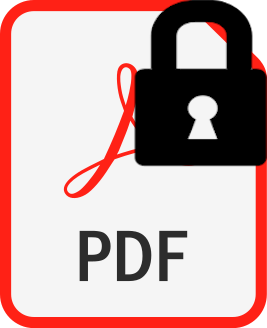 | 20p. |
7. |
Haponova O., Tarelnyk V.♦, Mościcki T. P., Tarelnyk N.♦, Investigating the effect of electrospark alloying parameters on structure formation of modified nitrogen coatings,
BULLETIN OF THE POLISH ACADEMY OF SCIENCES: TECHNICAL SCIENCES, ISSN: 0239-7528, DOI: 10.24425/bpasts.2024.150802, Vol.72, No.5, pp.1-8, 2024 Streszczenie: The quality parameters of surface layers synthesised using electrospark alloying (ESA) technology were analysed in this paper. The main focus was on the influence of equipment energy parameters on structure formation, specifically the effect of discharge energy and productivity. Microstructural analysis of the modified surface of C40 steel after nitriding by ESA using a paste containing nitrogen compounds injected into the interelectrode gap was conducted. The layer structure for all studied ESA parameters includes three areas: the upper “white layer”, the diffusion zone below it, and the substrate. The roughness of the surface is Ra ∼ 0.9 μm at low discharge energy Wp = 0.13 J and Ra ∼ 6 μm at Wp = 3.4 J. The microhardness, continuity, and surface roughness of the layers varied with Wp. The influence of ESA productivity on the structure was studied. The thickness of the hardened layer and the diffusion zone, as well as the microhardness and continuity, are affected by reduced productivity. For the same discharge energy, the thickness of the hardened layer increases by 10-18% with a decrease in productivity compared to the classical mode. Słowa kluczowe: electrospark alloying, discharge energy, productivity, coating, structure Afiliacje autorów:
Haponova O. | - | IPPT PAN | Tarelnyk V. | - | Sumy National Agrarian University (UA) | Mościcki T. P. | - | IPPT PAN | Tarelnyk N. | - | Sumy National Agrarian University (UA) |
| 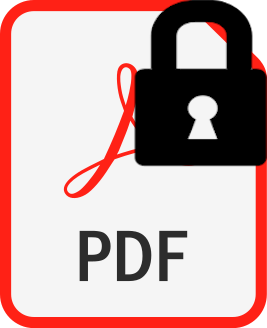 | 100p. |
8. |
Haponova O., Tarelnyk V.♦, Mościcki T. P., Tarelnyk N.♦, Półrolniczak J.♦, Myslyvchenko O.♦, Adamczyk-Cieślak B.♦, Sulej-Chojnacka J.♦, Investigation of the Structure and Properties of MoS2 Coatings Obtained by Electrospark Alloying,
Coatings, ISSN: 2079-6412, DOI: 10.3390/coatings14050563, Vol.14, No.563, pp.1-15, 2024 Streszczenie: Electrospark coatings alloyed with MoS2 have been studied. The coatings were obtained by the following two strategies: the first consisted of pre-applying molybdenum disulfide to the treated surface and alloying with a molybdenum electrode (Mo + MoS2 coating); the second consisted of applying a paste with a sulfur content of 33.3% to the treated surface and alloying with a molybdenum electrode (Mo + S coating). The structure, phase composition, and tribological properties of the coatings were investigated. The coatings have a complex structure consisting of an upper soft layer, a hardened white layer, a diffusion zone, and a substrate. Element analysis and cross-sectional hardness changes indicated that element diffusion occurred at the coating/substrate interface. The phase composition of the coatings is represented by BCC and FCC solid solutions on Fe, and MoS2 is also detected. In Mo + S coatings, the molybdenum disulfide on the surface is about 8%; in Mo + MoS2 coatings, it is 27%–46%. The obtained coatings show very good tribological properties compared to molybdenum ESA coatings. The frictional forces and coefficients are reduced by a factor of 10 and 40, depending on the test conditions. Słowa kluczowe: electrospark alloying, coating, structure, molybdenum disulfide, tribological properties, energy conservation Afiliacje autorów:
Haponova O. | - | IPPT PAN | Tarelnyk V. | - | Sumy National Agrarian University (UA) | Mościcki T. P. | - | IPPT PAN | Tarelnyk N. | - | Sumy National Agrarian University (UA) | Półrolniczak J. | - | inna afiliacja | Myslyvchenko O. | - | I. M. Frantsevich Institute for Problems in Materials (UA) | Adamczyk-Cieślak B. | - | inna afiliacja | Sulej-Chojnacka J. | - | inna afiliacja |
| 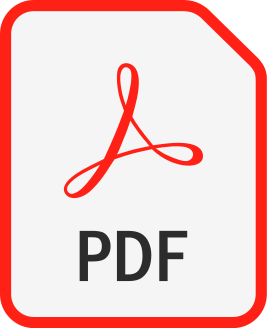 | 100p. |
9. |
Haponova O.♦, Tarelnyk N.♦, Improvement of the Quality Parameters of the Surface Layers of Steel Parts after Alitization by the Electrospark-Alloying Method. Pt 3. Mathematical Model of Forecasting the Quality Parameters of Coatings Taking into Account the Performance of Surface Treatment,
Metallofizika i Noveishie Tekhnologii, ISSN: 1024-1809, DOI: 10.15407/mfint.46.08.0771, Vol.46, No.8, pp.771-795, 2024 | 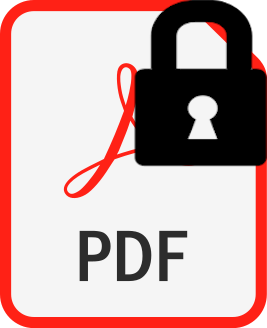 | 40p. |
10. |
Haponova O.♦, Tarelnyk V.♦, Zhylenko T.♦, Tarelnyk N.♦, Vasilenko O.♦, Pavlovskyi S.♦, Improvement of the Quality Parameters of the Surface Layers of Steel Parts after Aluminizing by Electrospark Alloying. Pt. 2. Results of the Influence of the Productivity of Aluminizing by Electrospark Alloying on the Structural State of Steel Surfaces,
Metallofizika i Noveishie Tekhnologii, ISSN: 1024-1809, DOI: 10.15407/mfint.46.04.0313, Vol.46, No.4, pp.313-324, 2024 Streszczenie: In the article, investigation is carried out at the second stage of aluminizing, when a consistent substance containing aluminium powder (the first option) or graphite powder and aluminium powder (the second option) is applied to the surface that has undergone aluminizing at the first stage, before further electrospark alloying with an aluminium electrode, and, regardless of the drying of the consistent substance, the aluminizing process is carried out at a discharge energy of 0.52–2.6 J and a productivity of 1.0–2.0 cm2/min, while the discharge energy and productivity are chosen such that the surface roughness decreases by ≅ 3–4 times. At the second stage aluminizing for both options, when using a consistent substance that contains aluminium powder or aluminium powder and graphite powder, the microhardness of the ‘white layer’ and the diffusion zone are increased (to a greater degree when graphite is present in the consistent substance), the surface roughness is decreased, and the integrity of the coating is of 100%. Before practical implementation, it is recommended to carry out the aluminizing process according to the first option at the discharge energy Wp = 4.6–6.8 J, using a consistent substance containing aluminium powder and graphite powder at the second stage. Słowa kluczowe: electrospark alloying,aluminizing,productivity,surface layer,quality,structure,roughness,microhardness,thickness of the white layer,coating continuity Afiliacje autorów:
Haponova O. | - | inna afiliacja | Tarelnyk V. | - | inna afiliacja | Zhylenko T. | - | inna afiliacja | Tarelnyk N. | - | inna afiliacja | Vasilenko O. | - | inna afiliacja | Pavlovskyi S. | - | inna afiliacja |
| 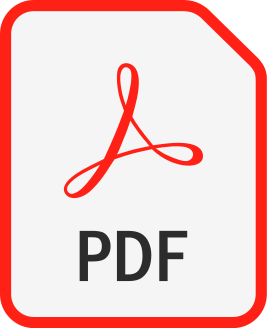 | 40p. |
11. |
Haponova O., Tarelnyk V.♦, Tarelnyk N.♦, Kurp P.♦, The Formation of C-S Coatings by Electrospark Alloying with the Use Special Process Media,
Solid State Phenomena, ISSN: 1662-9779, DOI: 10.4028/p-5KfyZQ, Vol.355, pp.85-93, 2024 Streszczenie: The paper presents an analysis of technologies for improving the quality parameters of the surface layers of parts, which were carried out by the method of electrospark alloying (ESA) and by additional saturation of surfaces with alloying elements from special process media (STM). The technology of sulfocementation was considered. Metallographic and hardness tests after sulfocementation by ESA showed that the treated surface consists of layers: "soft", hardened and base metal. As the discharge energy increases, the thickness, microhardness and integrity of the coating increase. The presence of sulfur in STM promotes the sulfidation process. It is shown that sulfur accumulates on the surface of the metal at a depth of up to 30 μm. This zone is characterized by reduced microhardness. A strengthened layer is formed under this layer, it has an increased carbon content and high microhardness. Słowa kluczowe: electro-spark alloying, special technological environment, coating, sulfocementation, microstructure, microhardness Afiliacje autorów:
Haponova O. | - | IPPT PAN | Tarelnyk V. | - | Sumy National Agrarian University (UA) | Tarelnyk N. | - | Sumy National Agrarian University (UA) | Kurp P. | - | Kielce University of Technology (PL) |
| 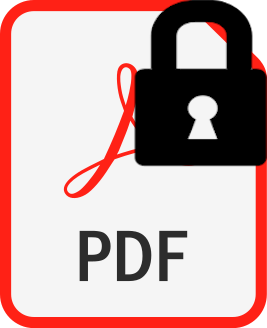 |
12. |
Haponova O.♦, Tarelnyk V.♦, Tarelnyk N.♦, Myslyvchenko M.♦, Nanostructuring of Metallic Surfaces by Electrospark Alloying Method,
The Journal of The Minerals, ISSN: 1047-4838, DOI: 10.1007/s11837-023-05940-1, pp.1-13, 2023 Streszczenie: A new method of nanostructuring of the surface by electrospark alloying method (ESA) using special processing media (SPM) with carbon nanotubes is proposed. The influence on the ESA regimes and the composition of the SPM on the microstructure and hardness of the coatings has been considered. While processing the Armco iron, with an increase in the discharge energy, the thickness and continuity of the coating increase. In the microstructures, the nanoscale phases of 40 nm to 1300 nm are detected, and they are evenly distributed in the coatings. Adding nanotubes helps to increase the continuity, thickness and hardness. Because of the ESA process, coatings with a uniform distribution of molybdenum are formed. Carbon, apparently in the form of the carbon nanotubes, is concentrated on the surfaces of the samples being processed, regardless of the discharge energy during the ESA process. The use of the proposed ESA method has a positive effect on the quality parameters of the coating. Afiliacje autorów:
Haponova O. | - | inna afiliacja | Tarelnyk V. | - | Sumy National Agrarian University (UA) | Tarelnyk N. | - | Sumy National Agrarian University (UA) | Myslyvchenko M. | - | I. M. Frantsevich Institute for Problems in Materials (UA) |
| 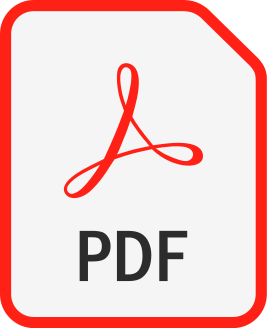 | 100p. |
13. |
Tarelnyk V.♦, Haponova O.♦, Tarelnyk N.♦, Myslyvchenko O.♦, Aluminizing of Metal Surfaces by Electric-Spark Alloying,
Uspekhi Fiziki Metallov, ISSN: 1608-1021, DOI: 10.15407/ufm.24.02.282, Vol.24, No.2, pp.282-318, 2023 Streszczenie: The analysis of the influence of the parameters of electrospark alloying with an aluminium electrode on the quality (roughness, microstructure of the coating, its continuity, phase composition, and microhardness) of the aluminized layer is presented. The effect of finishing methods after aluminizing is evaluated. The heat resistance of the obtained coatings is studied. Metallographic analysis shows that the coating consists of three sections: a ‘white’ layer, a diffusion zone, and the base metal. With an increase in the discharge energy, such quality parameters of the surface layer as thickness, microhardness of both a ‘white’ layer and a transition zone, and roughness are increased. The continuity of a ‘white’ layer at the discharge energy Wp = 0.52 J is low (of 50–60%); with a subsequent increase in the discharge energy, it increases and, at Wp = 6.8 J, it is of 100%. An increase in the discharge energy during electric-spark alloying (ESA) leads to a change in the chemical and phase compositions of the layer: at low discharge energies, a layer is formed, consisting mainly of α-Fe and aluminium oxides. As Wp increases, the layer consists of iron and aluminium intermetallic compounds, as well as free aluminium, that is confirmed by the data of local x-ray microanalysis. For practical application, it is possible to recommend the process of aluminizing by the ESA method, using the modes (discharge energy in the range of 4.6–6.8 J and productivity of 2.0–3.0 cm2/min). Such process provides the formation of a ‘white’ layer with a thickness of 70–130 µm, microhardness of 5000–7500 MPa, roughness (Ra) of 6–9 µm, and continuity of 95–100%. In order to increase the thickness of the aluminized layer, it is recommended to preliminarily apply grease containing aluminium powder to the steel surface and, without waiting for it to dry, carry out ESA with an aluminium electrode. In this case, the coating continuity is of 100%, the layer thickness is of up to 200 µm, and the microhardness is of 4500 MPa. The paper presents the results of study of the quality parameters of multicomponent aluminium-containing coatings of Al–S, Al–C–S, and Al–C–B systems. Replacing the aluminium electrode with graphite one leads to a decrease in the thickness and continuity of a ‘white’ layer, respectively, to 50 µm and 30%. In turn, the microhardness on the surface increases to 9000 MPa. The addition of 0.7 boron to the consistency substance leads to an increase in the thickness and continuity of a ‘white’ layer, respectively, up to 60 µm and 70%. The microhardness on the surface rises to 12000 MPa. In order to reduce the roughness of the surface layer and to obtain continuous coatings, it is recommended to carry out ESA with an aluminium electrode, but at lower modes. Słowa kluczowe: electrospark alloying, coating, aluminizing, microhardness, continuity, roughness, structure, x-ray diffraction analysis, x-ray spectral analysis Afiliacje autorów:
Tarelnyk V. | - | Sumy National Agrarian University (UA) | Haponova O. | - | inna afiliacja | Tarelnyk N. | - | Sumy National Agrarian University (UA) | Myslyvchenko O. | - | I. M. Frantsevich Institute for Problems in Materials (UA) |
| 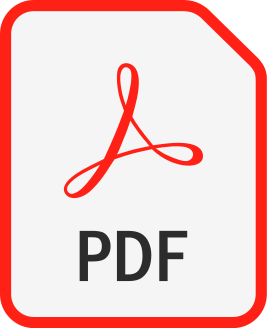 | 70p. |
14. |
Kurp P.♦, Danielewski H.♦, Szwed B.♦, Borkowski K.♦, Zrak A.♦, Haponova O.♦, Discussion about Metal Expansion Joints Manufacturing Technology of Preventing Thermal Deformation Pipelines Intended for the Fluids Transport,
Communications - Scientific Letters of the University of Žilina, ISSN: 1335-4205, DOI: 10.26552/com.C.2023.030, Vol.25, No.2, pp.111-117, 2023 Streszczenie: In this paper, the authors discuss the method of deformations compensation (resulting from the impact of variable temperatures and pressure) in pipelines intended for fluids transport (liquids and gases). Classical methods of compensation through the so-called "natural compensation" and using special devices called expansion joints. In this paper authors present research work on a new type of the metal expansion joints, called bellow-lens expansion joints. The mechanically assisted laser forming method, which was used to manufacture the bellow-lens expansion joints, was presented. The method uses CO2 laser radiation to heat the element from which the expansion joint will be made and the proprietary system consists of an actuator and swivel handle. Słowa kluczowe: metal expansion joints, laser forming, pipelines compensating, pipelines thermal deformation Afiliacje autorów:
Kurp P. | - | Kielce University of Technology (PL) | Danielewski H. | - | inna afiliacja | Szwed B. | - | inna afiliacja | Borkowski K. | - | inna afiliacja | Zrak A. | - | inna afiliacja | Haponova O. | - | inna afiliacja |
| 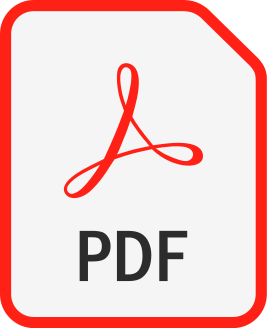 | 70p. |
15. |
Haponova O.♦, Tarelnyk V.♦, Zhylenko T.♦, Tarelnyk N.♦, Sarzhanov O.♦, Melnyk V.♦, Vlasovets V.♦, Pavlovskyy S.♦, Okhrimenko V.♦, Tkachenko A.♦, Improvement of Quality Parameters of Surface Layers of Steel Parts after Aluminizing by Electrospark Alloying. Pt. 1. Features of the Structural State of Steel Surfaces after Aluminizing,
Metallofizika i Noveishie Tekhnologii, ISSN: 1024-1809, DOI: 10.15407/mfint.45.12.1449, Vol.45, No.12, pp.1449-1472, 2023 Streszczenie: The structure formation and properties of the surface layers of steel parts after alloying by traditional technologies and the method of electrospark alloying (ESA) is analysed in the article. As a result of the study of the productivity of the ESA process by aluminium electrode-tool, which is one of the important parameters of the ESA technology, reserves are revealed for improving the quality of the surface layers of steel parts during aluminizing. Two options for reducing productivity in relation to the traditional are studied: the first one, when productivity is reduced by ≅ 2 times; the second one, when performance is reduced by ≅ 4 times. As established, in the first variant, when the discharge energy increases from 0.52 to 6.8 J, at the first stage of aluminizing of steel 20 and steel 40, the thickness of the ‘white’ layer from 20 to 75 and from 25 to 110 μm, respectively; the thickness of the diffusion zone increases from 35 to 120 and from 40 to 140 μm, respectively; the microhardness of the ‘white layer’ increases from 2200 to 7400 and from 2400 to 7450 MPa, respectively; the surface roughness Ra increases from 1.1 to 9.0 and from 1.0 to 8.1 μm, respectively, and the continuity increases from 80 to 100% starting with Wp = 4.6 J and from 60 to 100% at Wp = 6.8 J. In the second variant, when the discharge energy increases from 0.52 to 6.8 J, at the first stage of processing steel 20 and steel 40, the thickness of the ‘white’ layer increases for steel 20 from 25 to 60 μm at Wp = 4.6 J, and then it doesn’t change for steel 40 from 30 to 100 μm; the thickness of the diffusion zone increases from 45 to 130, respectively; the microhardness of the ‘white layer’ increases from 2250 to 7300 and from 2450 to 7300 MPa, respectively; the surface roughness Ra increases from 1.3 to 9.0 and from 1.6 to 8.1 μm, respectively, and the continuity for both steel 20 and steel 40 at Wp = 0.52 J is of 95% and further increases to 100%. Słowa kluczowe: electrospark alloying, aluminizing, productivity, surface layer, structure, roughness, microhardness, thickness of the white layer, coating continuity Afiliacje autorów:
Haponova O. | - | inna afiliacja | Tarelnyk V. | - | inna afiliacja | Zhylenko T. | - | inna afiliacja | Tarelnyk N. | - | inna afiliacja | Sarzhanov O. | - | inna afiliacja | Melnyk V. | - | inna afiliacja | Vlasovets V. | - | inna afiliacja | Pavlovskyy S. | - | inna afiliacja | Okhrimenko V. | - | inna afiliacja | Tkachenko A. | - | inna afiliacja |
| 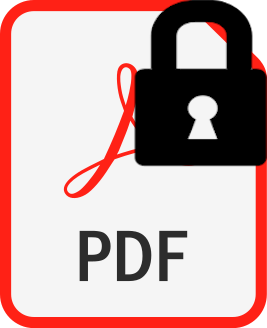 | 40p. |
16. |
Tarelnyk V.♦, Haponova O.♦, Tarelnyk N.♦, Konoplianchenko Y.♦, Bondarev S.♦, Radionov O.♦, Mayfat M.♦, Okhrimenko A.♦, Dumanchuk M.♦, Sirovitskiy K.♦, The Surfaces Properties of Steel Parts with Wear-Resistant Coatings of the 1М and 90% ВК6 + 10% 1M Composition Applied by the Method of Electrospark Alloying with the Use of Special Technological Environments. Pt. 2. Wear Resistance, Topographic and Mechanical Properties,
Metallofizika i Noveishie Tekhnologii, ISSN: 1024-1809, DOI: 10.15407/mfint.45.06.0773, Vol.45, No.6, pp.773-794, 2023 Streszczenie: In the article, as a result of comparative tests, it is established that steel samples with a coating applying the electrospark alloying method (ESA) with a BK6 hard-alloy electrode with the use of a special technological environment (STE) with a composition of 0.5%Si + 0.5%B + 2%Cr + 7%Ni + 90% vaseline, the wear of which after 24 hours of testing is of 221 mg that is 122% less than that for samples without coating and 15% and 31% for samples with coatings applying the nichrome-electrodes’ wire X20H80 using STE composition of 0.5%Si + 0.5%B + 59%BK6 + 40% vaseline and STE composition of 5%Si + 5%B + 90% vaseline, respectively, and by 22% and 47% less than with coatings applying the electrodes made by the method of powder metallurgy (PM), the composition of which is of 90%BK6 + 10%1M and 1M, respectively. For P6M5 steel, better resistance against hydroabrasive wear is possessed by samples with a coating applying the ESA method with an electrode made of hard alloy BK6 using STE composition of 0.5%Si + 0.5%B + 2%Cr + 7%Ni + 90% vaseline, the wear of which after 24 hours of testing is of 188 mg that is 43% less than in samples without coating and by 6% and 15% in samples with a coating applying the ESA method with an electrode made of nichrome wire of the composition X20H80 using STE composition of 0.5%Si + 0.5%B + 59%BK6 + 40% vaseline and STE composition of 5%Si + 5%B + 90% vaseline, and by 24% and 27% less than with coatings applying the electrodes produced by the PM method with a composition of 90%BK6 + 10%1M and 1M, respectively. In ESA with electrodes-tools made both by the PM method and by the new technology of wire X20H80 and hard alloy BK6 and STE, parts made of steel 45 and steel P6M5 have a decrease in the strength limit and yield limit, respectively, and both the relative elongation and the relative narrowing increase. With further abrasive-free ultrasonic finishing (AFUF), both the strength limit and the yield strength increase, and both the relative elongation and the relative narrowing decrease. For practical implementation, wear-resistant coatings formed according to the new technology, using tool electrodes made of X20H80 wire and hard alloy BK6 and STE in two stages with the following AFUF are proposed, the growth of the strength limit and the yield limit of which increase for steel 45 and steel P6M5 by 4.9% and 4.6% and 3.5% and 2.7%, respectively, and relative elongation and relative contraction decrease by 1.7% and 1.3% and 2.0% and 1.7%, respectively. At the same time, the surface roughness is Ra = 1.1 μm, and the integrity is of 100% Słowa kluczowe: electrospark alloying, electrode tool, coating, white layer, microhardness, roughness, integrity Afiliacje autorów:
Tarelnyk V. | - | inna afiliacja | Haponova O. | - | inna afiliacja | Tarelnyk N. | - | inna afiliacja | Konoplianchenko Y. | - | inna afiliacja | Bondarev S. | - | inna afiliacja | Radionov O. | - | inna afiliacja | Mayfat M. | - | inna afiliacja | Okhrimenko A. | - | inna afiliacja | Dumanchuk M. | - | inna afiliacja | Sirovitskiy K. | - | inna afiliacja |
| 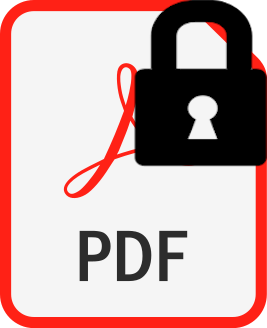 | 40p. |
17. |
Tarelnyk V.♦, Haponova O.♦, Melnyk V.♦, Tarelnyk N.♦, Zubko V.♦, Vlasovets V.♦, Konopliachenko V.♦, Bondarev S.♦, Radionov O.♦, Mayfat M.♦, Okhrimenko V.♦, Tkachenko A.♦, The Surfaces Properties of Steel Parts with Wear-Resistant Coatings of the 1M and 90% BK6 + 10% 1M Composition Applied by the Method of Electrospark Alloying with the Use of Special Technological Environments. Pt. 1. The Strengthened-Surfaces’ Structural State Features,
Metallofizika i Noveishie Tekhnologii, ISSN: 1024-1809, DOI: 10.15407/mfint.45.05.0663, Vol.45, No.5, pp.663-686, 2023 Streszczenie: The article describes a new method of forming the protective coatings of steel parts operating under conditions of abrasive wear both in general mechanical engineering, the composition of which is of 90% ВК6 + 10% 1М, and in industries, where there may be radiation exposure and the composition of 1М (70% Ni, 20% Cr, 5% Si, 5% B), by applying them by the method of electrospark alloying (ESA) with compact electrodes-tools made of nichrome wire X20Н80 and ВК6 hard alloy and using special technological media (STM), which include the necessary alloying elements. As a result of these research, it is established that the surface layers of the 45 and Р6M5 steels after applying wear-resistant coatings have a structure that consists of three areas: the ‘white layer’, the transition zone below, and the base metal. When the discharge energy (Wp) increases from 0.52 to 2.6 J, the thicknesses of the ‘white layer’ and the transition zone, their microhardness and surface roughness increase, but the integrity of the applied coating decreases. The highest microhardness of 9750-12800 and 14250-14600 MPa corresponds to the coating formed on steel 45 and Р6M5, respectively, during ESA by means of both the compact electrodes-tools made of hard alloy ВК6 and the STM with the composition of 0.5% Si + 0.5% B + 2% Cr + 7% Ni + 90% Vaseline. Słowa kluczowe: electrospark alloying, electrode tool, coating, white layer, microhardness, roughness, continuity Afiliacje autorów:
Tarelnyk V. | - | inna afiliacja | Haponova O. | - | inna afiliacja | Melnyk V. | - | inna afiliacja | Tarelnyk N. | - | inna afiliacja | Zubko V. | - | inna afiliacja | Vlasovets V. | - | inna afiliacja | Konopliachenko V. | - | inna afiliacja | Bondarev S. | - | inna afiliacja | Radionov O. | - | inna afiliacja | Mayfat M. | - | inna afiliacja | Okhrimenko V. | - | inna afiliacja | Tkachenko A. | - | inna afiliacja |
| 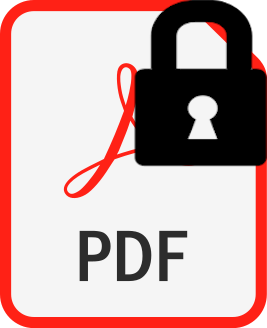 | 40p. |
18. |
Myslyvchenko O.♦, Lytvyn R.♦, Grinkevich K.♦, Zgalat-Lozynskyy O.♦, Tkachenko I.♦, Bloschanevich O.♦, Ivanchenko S.♦, Novichenko V.♦, Haponova O.♦, Laser Processing of High-Entropy VNb2TaCrMoWTi0.3B0.6 Alloy Coatings for Wear Reduction in Dry Friction with Different Counterfaces,
Powder Metallurgy and Metal Ceramics, ISSN: 1068-1302, DOI: 10.1007/s11106-023-00397-y, Vol.62, No.5-6, pp.339-349, 2023 Streszczenie: The microstructure, phase composition, and microhardness of the cast high-entropy VNb2TaCrMoW alloy with the addition of titanium diboride were studied. The initial VNb2TaCrMoW alloy consisted of two bcc solid solutions, slightly differing in lattice parameters (a = 0.3139 nm and 0.3200 nm). The addition of boron as titanium diboride and repeated remelting led to a bcc solid solution with a larger lattice parameter (a = 0.3217 nm) and a boride with W3.5Fe2.5B4 structure (a = 0.6054 nm and c = 0.3256 nm). The bcc solid solution was the first to crystallize, and the boride was part of the eutectic grains and precipitated from the last melt portions, forming a closed network. The resulting alloy was applied to a carbon steel substrate as a coating using electrospark deposition employing an Elitron-24A installation with varying electrical pulse energy. Higher pulse energy during coating deposition increased the layer thickness and surface roughness but did not influence the phase composition. The microstructure of the coatings was more uniform compared to the cast alloys, and X-ray diffraction showed that the coatings contained bcc solid solutions, Fe7W6 intermetallic compound, and a small amount of TaO2 oxide. The coatings had a hardness of about 10 GPa and were 11–15 μm and 16–20 μm thick at discharge energies of 0.52 and 1.1 J, respectively. A comparative analysis of the phase composition, hardness, and microstructure of the cast alloy and associated coatings was carried out. The coatings deposited at a discharge energy of 0.52 J were subjected to laser processing. Laser processing of the coatings resulted in a thermally affected zone, while the surface layer hardness hardly changed. The wear resistance of the coatings deposited at a discharge energy of 0.52 J was analyzed. Wear resistance testing was conducted for three counterface materials (VK6, Al2O3, and Si3N4) in quasistatic and dynamic loading modes. Laser processing of the electrospark coatings changed the wear mechanism and significantly increased the wear resistance regardless of the counterface material and loading mode. Słowa kluczowe: high-entropy boride, electrospark deposition, solid solution, wear resistance, microstructure, X-ray diffraction Afiliacje autorów:
Myslyvchenko O. | - | inna afiliacja | Lytvyn R. | - | inna afiliacja | Grinkevich K. | - | inna afiliacja | Zgalat-Lozynskyy O. | - | inna afiliacja | Tkachenko I. | - | inna afiliacja | Bloschanevich O. | - | inna afiliacja | Ivanchenko S. | - | inna afiliacja | Novichenko V. | - | inna afiliacja | Haponova O. | - | inna afiliacja |
| 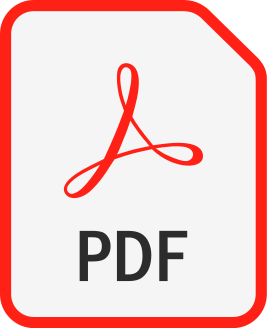 | 20p. |
19. |
Haponova O.♦, Tarelnyk Viacheslav B.♦, Antoszewski B.♦, Radek N.♦, Tarelnyk Nataliia V.♦, Kurp P.♦, Myslyvchenko Oleksandr M.♦, Hoffman J., Technological Features for Controlling Steel Part Quality Parameters by the Method of Electrospark Alloying Using Carburezer Containing Nitrogen—Carbon Components,
Materials, ISSN: 1996-1944, DOI: 10.3390/ma15176085, Vol.15, No.6085, pp.1-14, 2022 Streszczenie: A new method of surface modification based on the method of electrospark alloying (ESA) using carburizer containing nitrogen—carbon components for producing coatings is considered. New processes have been proposed that include the step of applying saturating media in the form of paste-like nitrogenous and nitrogenous-carbon components, respectively, onto the surface without waiting for those media to dry, conducting the ESA process with the use of a steel electrode-tool, as well as with a graphite electrode-tool. Before applying the saturating media, an aluminium layer is applied onto the surface with the use of the ESA method at a discharge energy of Wp = 0.13–6.80 J. A saturating medium in the form of a paste was applied to the surfaces of specimens of steel C22 and steel C40. During nitriding, nitrocarburizing and carburization by ESA (CESA) processes, with an increase in the discharge energy (Wp), the thickness, micro hardness and continuity of the “white layer” coatings, as well as the magnitude of the surface roughness, increase due to saturation of the steel surface with nitrogen and/or carbon, high cooling rates, formation of non-equilibrium structures, formation of special phases, etc. In the course of nitriding, nitrocarburizing and CESA processing of steels C22 and C40, preliminary processing with the use of the ESA method by aluminum increases the thickness, microhardness and continuity of the “white layer”, while the roughness changes insignificantly. Analysis of the phase composition indicates that the presence of the aluminum sublayer leads to the formation of the aluminum-containing phases, resulting in a significant increase in the hardness and, in addition, in an increase in the thickness and quality of the surface layers. The proposed methods can be used to strengthen the surface layers of the critical parts and their elements for compressor and pumping equipment Słowa kluczowe: electrospark alloying,coatings,roughness,structure,microhardness,continuity,X-ray diffraction analysis,nitriding,nitrocarburizing,carburization Afiliacje autorów:
Haponova O. | - | inna afiliacja | Tarelnyk Viacheslav B. | - | Sumy National Agrarian University (UA) | Antoszewski B. | - | Kielce University of Technology (PL) | Radek N. | - | inna afiliacja | Tarelnyk Nataliia V. | - | Sumy National Agrarian University (UA) | Kurp P. | - | Kielce University of Technology (PL) | Myslyvchenko Oleksandr M. | - | I. M. Frantsevich Institute for Problems in Materials (UA) | Hoffman J. | - | IPPT PAN |
| 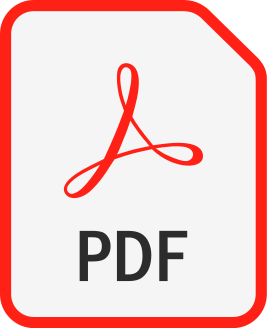 | 140p. |
20. |
Berladir K.♦, Zhyhylii D.♦, Haponova O.♦, Krmela J.♦, Krmelová V.♦, Artyukhov A.♦, Modeling of Polymer Composite Materials Chaotically Reinforced with Spherical and Cylindrical Inclusions,
Polymers, ISSN: 2073-4360, DOI: 10.3390/polym14102087, Vol.14(10), No.2087, pp.1-16, 2022 Streszczenie: The technical and economic efficiency of new PCMs depends on the ability to predict their performance. The problem of predicting the properties of PCMs can be solved by computer simulation by the finite element method. In this work, an experimental determination of the physical and mechanical properties of PTFE PCMs depending on the concentration of fibrous and dispersed filler was carried out. A finite element model in ANSYS APDL was built to simulate the strength and load-bearing capacity of the material with the analysis of damage accumulation. Verification of the developed computer model to predict the mechanical properties of composite materials was performed by comparing the results obtained during field and model experiments. It was found that the finite element model predicts the strength of chaotically reinforced spherical inclusions of composite materials. This is due to the smoothness of the filler surfaces and the lack of filler dissection in the model. Instead, the prediction of the strength of a finite element model of chaotically reinforced cylindrical inclusions of composite materials requires additional analysis. The matrix and the fibrous filler obviously have stress concentrators and are both subject to the difficulties of creating a reliable structural model. Słowa kluczowe: PCMs, polytetrafluoroethylene, carbon fiber, coke, energy efficiency, modeling, strength, solid model, finite element model Afiliacje autorów:
Berladir K. | - | inna afiliacja | Zhyhylii D. | - | inna afiliacja | Haponova O. | - | inna afiliacja | Krmela J. | - | inna afiliacja | Krmelová V. | - | inna afiliacja | Artyukhov A. | - | inna afiliacja |
| 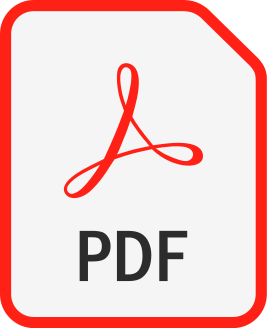 | 100p. |
21. |
Tarelnyk V.♦, Haponova O.♦, Konoplianchenko Y.♦, Electric-Spark Alloying of Metal Surfaces with Graphite,
Uspekhi Fiziki Metallov, ISSN: 1608-1021, DOI: 10.15407/ufm.23.01.027, Vol.23, No.1, pp.27-58, 2022 Streszczenie: The article reviews and analyses the current scientific research in the field of surface treatment of metal surfaces with concentrated energy fluxes (CEF) — the electric-spark (in the literature, known also as electrospark) alloying (ESA), which makes it possible to obtain surface structures with unique physical, mechanical and tribological properties at the nanoscale. The ESA method with a graphite electrode (electrospark carburizing — EC) is based on the process of diffusion (saturation of the surface layer of a part with carbon), and it is not accompanied by an increase in the size of the part. In this article, the influence of the EC parameters on the quality of the carburized layer is investigated. The microstructural analysis shows that the three characteristic zones could be distinguished in the structure: the carburized (‘white’) layer, the finely dispersed transition zone with fine grain, and the base metal zone. The analysis of the results of the durometric studies of the coatings is carried out. To achieve the required parameters of dimensional accuracy and roughness of the working surface of the part after the EC process, it is necessary to use the method of non-abrasive ultrasonic finishing (NAUF). In addition, because of applying the NAUF method, the surface roughness is decreased, the tensile stresses are changed to the compressive ones, and the fatigue strength is increased too. In addition, to reduce the roughness of the treated surface, it is proposed to apply the EC technology in stages, reducing the energy of the spark discharge at each subsequent stage. In order to increase the quality of the carburized layer obtained by the EC process, it is proposed to use a graphite powder, which is applied to the treated surface before alloying. The comparative analysis shows that, after the traditional EC process at Wp = 4.6 J, the surface roughness of steel 20 is Ra = 8.3–9.0 μm, and after the proposed technology, Ra = 3.2–4.8 μm. In this case, the continuity of the alloyed layer increases up to 100%; there increases the depth of the diffusion zone of carbon up to 80 μm as well as the microhardness of the ‘white’ layer and its thickness, which increase up to 9932 MPa and up to 230 μm, respectively. The local micro-x-ray spectral analysis of the obtained coatings shows that, at the EC process carried out in a traditional way, the applying Wp = 0.9, 2.6, 4.6 J provides the formation of the surface layers with high-carbon content depths of 70, 100, 120 μm, respectively, and with the use of a graphite powder, they are of 80, 120, 170 μm. While deepening, the amount of carbon is decreasing from 0.72–0.86% to the carbon content in the base metal — 0.17–0.24%. In the near-surface layer formed with the use of the new technology, the pores are filled with free graphite, which could be used as a solid lubricant to improve the operating characteristics of the friction-pairs parts processed thereby Słowa kluczowe: electrospark (electric-spark) alloying, graphite, carburizing, microstructure, quality, wear resistance Afiliacje autorów:
Tarelnyk V. | - | Sumy National Agrarian University (UA) | Haponova O. | - | inna afiliacja | Konoplianchenko Y. | - | inna afiliacja |
| 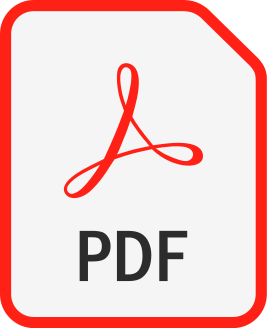 | 70p. |
22. |
Tarelnyk V.♦, Haponova O.♦, Konoplianchenko V.♦, Tarelnyk N.♦, Dumanchuk M.♦, Pirogov V.♦, Voloshko T.♦, Hlushkova D.♦, Development of a System Aimed at Choosing the Most Effective Technology for Improving the Quality of Babbitt Coatings of Sliding Bearings. Pt. 2. Mathematical Model of Wear of Babbitt Coatings. Criteria for Choosing the Technology of Deposition of Babbitt Coatings,
Metallofizika i Noveishie Tekhnologii, ISSN: 1024-1809, DOI: 10.15407/mfint.44.12.1643, Vol.44, No.12, pp.1643-1659, 2022 Streszczenie: In the article, a direct choice system of the most rational technology for applying a babbitt coating on the liners of sliding bearings (SB) is developed, which takes into account both economic and environmental requirements. On the basis of the performed research, a physically substantiated mathematical model of the babbitt-coatings’ wear process (wear equation) is proposed, which allows solving both the direct problem of determining weight and linear wears based on the known work of friction, as well as the inverse problem of finding the necessary work of friction to obtain the required amount of weight or linear wears. With knowing the time to reach a certain amount of wear, it becomes possible to operate the products more rationally, timely assigning the repair time and friction-surface catastrophic-wear preventing. In the course of research, a methodology is developed for determining the constants of the wear equation: activation energy (EA) as well as maximum weight (Δmб.п.н) and linear (Δhб.п.н) wears, which can be used as selection criteria for the most rational technology of applying a babbitt coating. Słowa kluczowe: sliding bearing, babbitt, coating, wear, structure, transition layer, adhesion strength, electrospark alloying, mathematical model Afiliacje autorów:
Tarelnyk V. | - | Sumy National Agrarian University (UA) | Haponova O. | - | inna afiliacja | Konoplianchenko V. | - | inna afiliacja | Tarelnyk N. | - | Sumy National Agrarian University (UA) | Dumanchuk M. | - | inna afiliacja | Pirogov V. | - | inna afiliacja | Voloshko T. | - | inna afiliacja | Hlushkova D. | - | inna afiliacja |
| 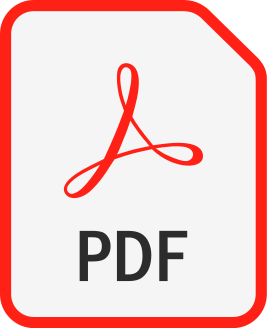 | 40p. |
23. |
Tarelnyk V.♦, Haponova O.♦, Konoplianchenko V.♦, Tarelnyk N.♦, Dumanchuk M.♦, Mikulina M.♦, Pirogov V.♦, Gorovoy S.♦, Medvedchuk N.♦, Development Directed Choice System of the Most Efficient Technology for Improving Sliding Bearings Babbitt Covers Quality. Pt. 1. Peculiarities of Babbitt Coating Technologies,
Metallofizika i Noveishie Tekhnologii, ISSN: 1024-1809, DOI: 10.15407/mfint.44.11.1475, Vol.44, No.11, pp.1475-1493, 2022 Streszczenie: The article substantiates the importance and relevance of increasing problem of the performance and service life of babbitt sliding bearings (SB), which are the rotors supports of a large number of centrifugal pumps, compressors, turbines and other dynamic equipment operating at high operating parameters (speeds, loads and temperatures), as well as in conditions of corrosive, abrasive and other types of working environment’s influence. The analysis of the babbitt SBs production technology and operating conditions showed that the reason for the decrease in their durability are factors that are formed both at the stage of manufacture and during operation. SB failure under normal operating conditions is a consequence of wear various types: cavitation, abrasive wear, damage due to plastic deformations, fatigue damage, etc. The antifriction layer wear resistance depends on the mode of operation and design of the bearing, the physical properties of the connection between the layer and the base, the rigidity of the shaft and the bed under the bearings. As established, the bearing anti-friction layer quality must be evaluated according to the following criteria: adhesion strength of the coating to the base, cohesive strength of the anti-friction layer, porosity, and homogeneity of the structure. As established, during the production of SBs, the formation by the method of electrospark alloying (ESA) of a copper intermediate layer, firmly bonded with steel substrate, and tin layer (formation of solid substitution solutions) and babbitt provides a stronger (by 35%) of adhesion, compared to traditional technology (steel 20 + babbitt), steel substrate with babbitt, as well as more intensive removal of heat from the friction zone. As determined, a new technology in which all operations are carried out by the ESA method can be a reserve for improving the babbitt coatings formation quality, which significantly affects the durability of the SB. As determined, in order to determine a more rational technology for applying babbitt coatings, it is necessary to develop a physically based mathematical model that relates the wear of a certain amount of babbitt to the frictional work spent on it. Słowa kluczowe: sliding bearing, babbitt, coating, wear, structure, transition layer, adhesion strength, electrospark alloying, mathematical model Afiliacje autorów:
Tarelnyk V. | - | Sumy National Agrarian University (UA) | Haponova O. | - | inna afiliacja | Konoplianchenko V. | - | inna afiliacja | Tarelnyk N. | - | Sumy National Agrarian University (UA) | Dumanchuk M. | - | inna afiliacja | Mikulina M. | - | inna afiliacja | Pirogov V. | - | inna afiliacja | Gorovoy S. | - | inna afiliacja | Medvedchuk N. | - | inna afiliacja |
| 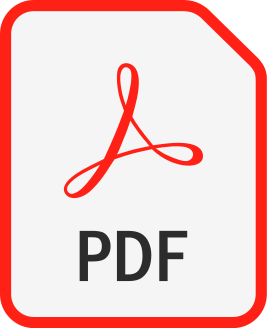 | 40p. |
24. |
Tarelnyk V.♦, Haponova O.♦, Konoplianchenko V.♦, Tarelnyk N.♦, Mikulina M.♦, Gerasimenko V.♦, Vasylenko O.♦, Zubko V.♦, Melnyk V.♦, Properties of Surfaces Parts from X10CrNiTi18-10 Steel Operating in Conditions of Radiation Exposure Retailored by Electrospark Alloying. Pt. 3. X-ray Spectral Analysis of Retailored Coatings,
Metallofizika i Noveishie Tekhnologii, ISSN: 1024-1809, DOI: 10.15407/mfint.44.10.1323, Vol.44, No.10, pp.1323-1333, 2022 Streszczenie: In article we present the results of studies of the local x-ray spectral analysis of coatings formed by the electrospark alloying (ESA) method at the discharge energy Wp = 0.13, 0.52 and 0.9 J by anodes from nickel and stainless steel X10CrNiTi18-10 on the cathode surface from X10CrNiTi18-10 steel. During ESA by stainless steel X10CrNiTi18-10 anode with an increase Wp in characteristic points and from the entire investigated surface of the coating, the quantitative elemental composition is not changed. The analysis of elements distribution over the depth of the formed layer is showed that when using the electrode tool from steel X10CrNiTi18-10 with an increase in Wp, there are a slight decrease in chromium and an increase in nickel and titanium in the surface layer. When steel X10CrNiTi18-10 is replaced by nickel with an increase in Wp, the concentration of nickel on the coating surface decreases from 95.38 to 89.04%. As the recession deepens from the coating surface, the concentration of nickel gradually decreases, respectively, at Wp = 0.13, 0.52 and 0.9 J from 96.29, 90.29 and 89.04% on the surface to 9.0, 10.30 and 9.9% at depth: 120, 165 and 240 μm. At the same time, the concentration of chromium, titanium and iron gradually increases. Słowa kluczowe: electrospark alloying, nickel, steel, x-ray spectral analysis, scan step, topography, spectrum Afiliacje autorów:
Tarelnyk V. | - | Sumy National Agrarian University (UA) | Haponova O. | - | inna afiliacja | Konoplianchenko V. | - | inna afiliacja | Tarelnyk N. | - | Sumy National Agrarian University (UA) | Mikulina M. | - | inna afiliacja | Gerasimenko V. | - | inna afiliacja | Vasylenko O. | - | inna afiliacja | Zubko V. | - | inna afiliacja | Melnyk V. | - | inna afiliacja |
| 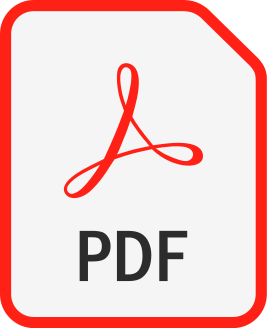 | 40p. |
25. |
Myslyvchenko O.♦, Bondar A.♦, Voblikov V.♦, Tsyganenko N.♦, Silinska T.♦, Haponova O.♦, Solidus Temperatures and Hot Hardness of Ti–Nb–Mo Alloys,
Metallofizika i Noveishie Tekhnologii, ISSN: 1024-1809, DOI: 10.15407/mfint.44.04.0459, Vol.44, No.4, pp.459-469, 2022 Streszczenie: Eight alloys of the Ti–Nb–Mo system are synthesized by the arc remelting method. As shown, they have dendritic microstructures typical of casting. The phase composition and lattice periods of the formed phases are determined. Using the method of differential thermal analysis (DTA), phase transformations in the solid state are investigated, and the temperatures of the onset of melting and crystallization are determined. For alloys, the solidus temperature of which is above 2000°C, together with DTA, the Pirani–Althermum pyrometric method is also used. Based on the experimental data, the temperature dependences of the hardness of the alloys are constructed and the activation energies of deformation of the material under the indenter are calculated. The analysis of the curves of the dependence of the hardness of the alloys is carried out and the temperature of the sharp softening of the material is determined. As shown, that the α→β transition in titanium alloys with an unstable β-phase does not lead to a significant change in hardness. Słowa kluczowe: solidus temperature, hot hardness, high-temperature strength, titanium alloys, crystal structure Afiliacje autorów:
Myslyvchenko O. | - | I. M. Frantsevich Institute for Problems in Materials (UA) | Bondar A. | - | inna afiliacja | Voblikov V. | - | inna afiliacja | Tsyganenko N. | - | inna afiliacja | Silinska T. | - | inna afiliacja | Haponova O. | - | inna afiliacja |
| 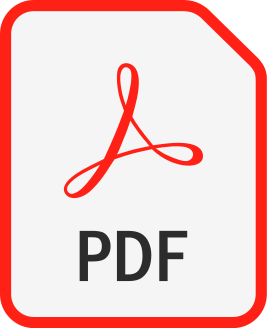 | 40p. |
26. |
Haponova O.♦, Tarelnyk N.♦, Properties of Surfaces Parts from X10CrNiTi18-10 Steel Operating in Conditions of Radiation Exposure Retailored by Electrospark Alloying. Pt. 2. Features of the Structural State of the Retailored Surfaces,
Metallofizika i Noveishie Tekhnologii, ISSN: 1024-1809, DOI: 10.15407/mfint.44.09.1103, Vol.44, No.9, pp.1103-1115, 2022 Streszczenie: In article we present the results of studies of the structural state of coatings formed by the method of electrospark alloying at the discharge energy Wp = 0.13, 0.52 and 0.9 J by anodes from nickel and stainless steel X10CrNiTi18-10 on the cathode surface from X10CrNiTi18-10 steel. Anode materials, such as nickel and X10CrNiTi18-10 steel are recommended as materials, which is advisable to use for restoring the surfaces of parts from X10CrNiTi18-10 steel operating in conditions of radiation exposure. Metallographic analysis of the formed coatings showed that their microstructure consists of 3 zones: 1) ‘white layer’ is the layer that cannot be etched with conventional reagents, 2) transition zone or diffuse zone, 3) base metal. Using nickel and steel X10CrNiTi18-10 with increasing discharge energy, the thickness of the hardened layer, microhardness, continuity and thickness of the white layer, as well as the surface roughness are increased. Replacing the nickel anode with steel X10CrNiTi18-10 surface roughness is increased and the thickness of the hardened layer is decreased. Słowa kluczowe: electrospark alloying, nickel, steel, metallographic analysis, structure, layer thickness, microhardness, roughness, continuity Afiliacje autorów:
Haponova O. | - | inna afiliacja | Tarelnyk N. | - | Sumy National Agrarian University (UA) |
| 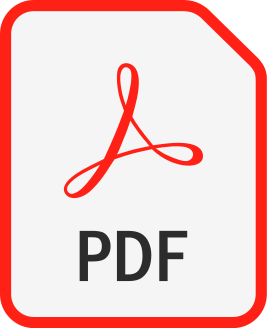 | 40p. |