1. |
Sadowski T.♦, Postek E., Pietras D.♦, Guhathakurta J.♦, Kruszka L.♦, Grążka M.♦, Data-based micromechanical modelling of the dynamic response of interpenetrated composites,
ICCS27 - 27th International Conference on Composite Structures, 2024-09-03/09-06, Ravenna (IT), No.1014, pp.130-130, 2024 | 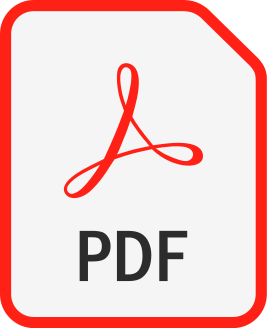 |
2. |
Postek E., Pietras D.♦, Guhathakurta J.♦, Kruszka L.♦, Grążka M.♦, Sadowski T.♦, Experimental testing and numerical modelling of impacts in interpenetrated composite,
ICCSE3, 3rd International Conference on Computations for Science and Engineering, 2023-08-20/08-23, Neapol (IT), pp.19-20, 2023 Streszczenie:
The interpenetrating composites consist of a scaffold and metallic matrix, which fills it being introduced under pressure. The scaffold is usually crushable. In our case, the SiC material stands for the skeleton, while the AlSi12 alloy is the matrix. Both materials are crushable. The SiC phase is brittle throughout the loading process, but the AlSi12 alloy is brittle during the elastic phase; then, its behaviour becomes viscous-plastic. The presentation concerns the experimental testing and simulations of the impact and fragmentation of metal matrix composite - AlSi12/SiC. The numerical model of the internal structure is created based on CT scanning. The microstructure of the composite is complex and consists of a metallic phase (85%), ceramic SiC skeleton, porosity, and a system of not perfect interfaces. The impacts are realized in the following few scenarios. The exemplary scenario is realized by imposing the initial conditions on the sample that hits a hard elastic barrier. The second one corresponds to SHPB experiments. The last one is the hitting of an elastic impactor against the sample. The influence of the impact velocities and material parameters of the phases on the failure modes is observed. Previously, analyses of the modes of loading application on the micromechanical failure of metal matrix composite were analysed in [1, 2]. An analysis of the empty SiC scaffolds is presented in [3]. The proposed finite element model of the AlSi12/SiC composite behaviour describing gradual degradation under impact loading was tested for different scenarios of hitting. In all cases, the growth of damage in the composite is very realistic. These results lead to the conclusion the proposed finite element model is very effective.
Acknowledgement: The results presented in this paper were obtained within the framework of research grant No. 2019/33/B/ST8/01263 financed by the National Science Centre, Poland. The numerical analyses were done in the ICM UW in Warsaw and in CI TASK in Gdańsk, Poland.
References:
[1] Postek, E. and Sadowski, T. Distributed microcracking process of WC/Co cermet under dynamic impulse compressive loading. Compos. Struct. (2018) 194: 494-508.
[2] Postek, E. and Sadowski, T. Qualitative comparison of dynamic compressive pressure load and impact of WC/Co composite. Int. J. Refract. Hard. Met. (2018) 77: 68-81.
[3] Postek, E., Sadowski, T. and Bieniaś, J. Simulation of impact and fragmentation of SiC skeleton, Phys. Letters (2021) 24:578-587.
Słowa kluczowe: Cermets, Interpenetration, Impact, Viscoplasticity, Peridynamics Afiliacje autorów:
Postek E. | - | IPPT PAN | Pietras D. | - | Lublin University of Technology (PL) | Guhathakurta J. | - | CT-LAB Stuttgart (DE) | Kruszka L. | - | Military University of Technology (PL) | Grążka M. | - | Military University of Technology (PL) | Sadowski T. | - | Lublin University of Technology (PL) |
| 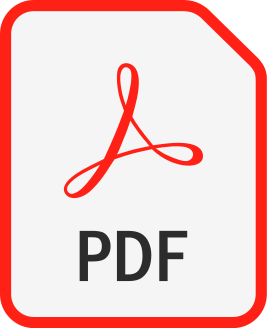 |
3. |
Postek E., Sadowski T.♦, Kruszka L.♦, Grążka M.♦, Guhathakurta J.♦, Fikus B.♦, Numerical modelling and experimental observation of ballistic penetration process in two-phase metal/ceramic composites,
ESMC 2022, 11th European Solid Mechanics Conference, 2022-07-04/07-08, Galway (IE), pp.1, 2022 Streszczenie: Ceramic two-phases composites are used in such industries as the armaments industry, aviation, automotive, nuclear power, and space exploration. In several areas, they stand as the source of technological progress. The material is often subjected to extreme loads, such as variable dynamic loads and high temperatures. The paper presents experimental investigations of ballistic impact on ceramic /metal composites. The internal structure of the novel material consists of ceramic foam made of SiC and filled with Al alloy. The experiment was performed using the ballistic stand and spherical impactor of diameter 5 mm and mass 0.5 g. The impactor hit the sample of diameter 30 mm and thickness 4 mm with a velocity of 600 m/s. Fig. 1 presents crater after impact and defragmented sample. The numerical analysis of the fragmentation process was performed using the finite element method. The internal structure of the composite was assessed using micro-CT selecting both phases, i.e., ceramic foam and AL alloy. The phases are joined by a continuous very small thickness interface. The numerical calculations allow for the description of the whole degradation process of the analysed interpenetrating composite up to the final failure by fragmentation and confirm the novel applicability of the material as a protective layer against the high-velocity impact. Acknowledgement The work has been performed under the research grants 2019/33/B/ST8/01263, National Science Centre, Poland. The analyses were done in the ICM UW in Warsaw and in CI TASK in Gdańsk, Poland. References [1] T. Ohji and M. Singh, Engineered Ceramics: Current Status and Future Prospects: Wiley, 2015. Słowa kluczowe: two-phase metal/ceramic composites, penetration experiments, numerical modelling Afiliacje autorów:
Postek E. | - | IPPT PAN | Sadowski T. | - | Lublin University of Technology (PL) | Kruszka L. | - | Military University of Technology (PL) | Grążka M. | - | Military University of Technology (PL) | Guhathakurta J. | - | CT-LAB Stuttgart (DE) | Fikus B. | - | inna afiliacja |
| 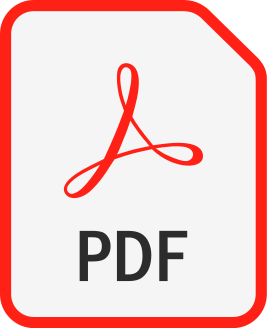 |