1. |
Włoczewski M., Jasiewicz K., Jenczyk P., Gadalińska E.♦, Kulikowski K.♦, Zhang Y.♦, Li R.♦, Jarząbek D. M., AlCoCrFeNiTi0.2 High-Entropy Alloy Under Plasma Nitriding: Complex Microstructure Transformation, Mechanical and Tribological Enhancement,
METALLURGICAL AND MATERIALS TRANSACTIONS A-PHYSICAL METALLURGY AND MATERIALS SCIENCE, ISSN: 1073-5623, DOI: 10.1007/s11661-025-07752-1, pp.1-17, 2025 Abstract: In this study, the AlCoCrFeNiTi0.2 high-entropy alloy (HEA) was plasma nitrided to investigate the microstructure and mechanical properties of high-entropy nitrides formed in the surface layer of the bulk sample. XRD measurements revealed a BCC → FCC crystal structure transformation, with the σ phase disappearing and hexagonal aluminum nitride emerging. Further experimental studies on the nitrided samples, including SEM, EDS, and EBSD, uncovered element segregation into multiple FCC phases with similar lattice constants, such as the NaCl-type (AlCrCoFeNiTi0.2)N high-entropy nitride. These observations align with theoretical analysis based on KKR-CPA calculations. Additionally, plasma nitriding induced high surface porosity; however, micropillar compression testing combined with nanoindentation revealed localized areas with significant hardness. A substantial reduction in the coefficient of friction was also observed. These findings not only provide deeper insights into the nitriding process of complex alloys, like dual-phase HEAs, but also hold promise for further exploration in the manufacturing of super-hard surfaces with high-entropy nitrides, enhancing mechanical properties for applications in harsh environments. Affiliations:
Włoczewski M. | - | IPPT PAN | Jasiewicz K. | - | IPPT PAN | Jenczyk P. | - | IPPT PAN | Gadalińska E. | - | Institute of Aviation (PL) | Kulikowski K. | - | other affiliation | Zhang Y. | - | University of Notre Dame (US) | Li R. | - | other affiliation | Jarząbek D. M. | - | IPPT PAN |
| 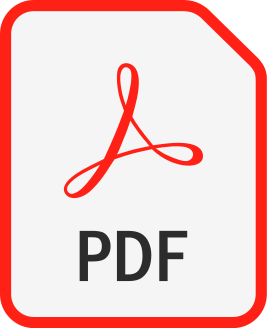 |
2. |
Brachaczek A., Tokpatayeva R.♦, Olek J.♦, Jarząbek D.M., Piotrowski P.♦, Jenczyk P., Jóźwiak-Niedźwiedzka D., Impact of formate based deicing agents on ASR products: Microstructural, chemical and mechanical characteristics,
CONSTRUCTION AND BUILDING MATERIALS, ISSN: 0950-0618, DOI: 10.1016/j.conbuildmat.2025.140729, Vol.471, No.140729, pp.1-12, 2025 Abstract: This study investigates the effects of formate-based deicing agents, specifically potassium formate (HCOOK) and sodium formate (HCOONa), on alkali-silica reaction (ASR) in concrete. By adapting ASTM C1260 standards, mortar bars were subjected to deicing solutions of varying concentrations to evaluate their influence on mortar expansion and ASR product characteristics. Results revealed that high concentrations of formate solutions significantly accelerated ASR, inducing expansions comparable to or greater than those caused by sodium hydroxide, while sodium chloride showed minimal expansion effects. Microstructural and chemical analyses demonstrated that ASR gels formed in formate solutions were predominantly amorphous, with different chemical composition depending on the deicer type. Pore solution analysis indicated a strong correlation between alkali ion concentration and mortar expansion. Furthermore, mechanical testing of ASR products revealed that gels formed in potassium formate exhibited higher hardness and elastic modulus compared to those formed in sodium formate. These findings enhance understanding of the detrimental effects of formate-based deicing agents on ASR and provide a foundation for developing mitigation strategies to preserve concrete infrastructure. Keywords: Alkali-silica reaction,Concrete microstructure,Expansion,Nanoindentation,Deicing agents,Pore solution analysis Affiliations:
Brachaczek A. | - | IPPT PAN | Tokpatayeva R. | - | other affiliation | Olek J. | - | Purdue University (US) | Jarząbek D.M. | - | IPPT PAN | Piotrowski P. | - | other affiliation | Jenczyk P. | - | IPPT PAN | Jóźwiak-Niedźwiedzka D. | - | IPPT PAN |
| 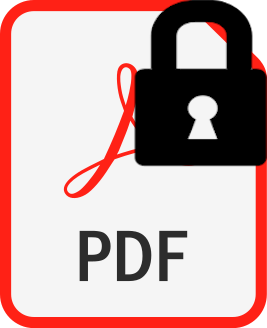 |
3. |
Jenczyk P., Michałowski M.♦, Warcholiński B.♦, Milczarek M., Gilewicz A.♦, Tribology of ZrC Coatings and Spherical Tips Acquired with Extraordinarily Stiff, Metal Atomic Force Microscopy Probes,
Advanced Engineering Materials, ISSN: 1438-1656, DOI: 10.1002/adem.202500243, No.2500243, pp.1-11, 2025 Abstract: Friction and wear are among the most crucial limiting factors for micro-electro-mechanical systems reliability. In this article, it introduces a novel approach to microtribological research by developing ultrastiff atomic force microscopy (AFM) probes capable of applying millinewton-range normal loads. This innovation enables friction measurements in operational ranges relevant to microbearings, overcoming limitations of conventional AFM probes. This article investigates the tribological performance of zirconium carbide (ZrC) coatings, fabricated via physical vapor deposition sputtering, in combination with various microspherical counterfaces. Its findings reveal that ZrC coatings with high carbon content exhibit coefficient of friction as low as 0.08 when paired with borosilicate glass. Additionally, it provides insights into wear behavior, advancing the selection of tribo-pairs for next-generation microbearings. Affiliations:
Jenczyk P. | - | IPPT PAN | Michałowski M. | - | Warsaw University of Technology (PL) | Warcholiński B. | - | other affiliation | Milczarek M. | - | IPPT PAN | Gilewicz A. | - | other affiliation |
| 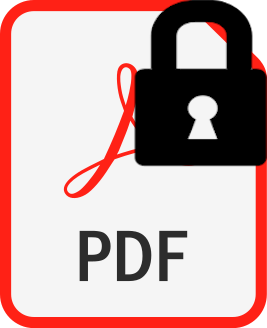 |
4. |
Jarząbek D. M., Włoczewski M.♦, Milczarek M., Jenczyk P., Takesue N.♦, Golasiński K.♦, Pieczyska E. A., Deformation Mechanisms of (100) and (110) Single-Crystal BCC Gum Metal Studied by Nanoindentation and Micropillar Compression,
METALLURGICAL AND MATERIALS TRANSACTIONS A-PHYSICAL METALLURGY AND MATERIALS SCIENCE, ISSN: 1073-5623, DOI: 10.1007/s11661-024-07605-3, pp.1-11, 2024 Abstract: In this paper, small-scale testing techniques—nanoindentation and micropillar compression—were used to investigate the deformation mechanisms, size effects, and strain rate sensitivity of (100) and (110) single-crystal Gum Metal at the micro/nanoscale. It was observed that the (100) orientation exhibits a significant size effect, resulting in hardness values ranging from 1 to 5 GPa. Conversely, for the (110) orientation, this effect was weaker. Furthermore, the yield strength obtained from the micropillar compression tests was approximately 740 MPa for the (100) orientation and 650 MPa for the (110) orientation. The observed deformations were consistent with the established features of the deformation behavior of body-centered cubic (bcc) alloys: significant strain rate sensitivity with no depth dependence, pile-up patterns comparable to those reported in the literature, and shear along the {112}<111> slip directions. However, the investigated material also exhibited Gum Metal-like high ductility, a relatively low modulus of elasticity, and high yield strength, which distinguishes it from classic bcc alloys. Affiliations:
Jarząbek D. M. | - | IPPT PAN | Włoczewski M. | - | other affiliation | Milczarek M. | - | IPPT PAN | Jenczyk P. | - | IPPT PAN | Takesue N. | - | Fukuoka University (JP) | Golasiński K. | - | other affiliation | Pieczyska E. A. | - | IPPT PAN |
| 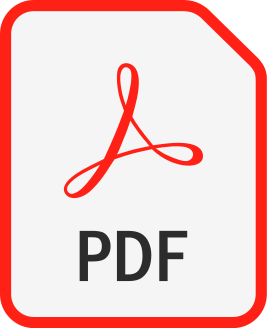 |
5. |
Nosewicz S., Jenczyk P., Romelczyk-Baishya B.♦, Bazarnik P.♦, Jarząbek D.M., Majchrowicz K.♦, Pakieła Z.♦, Kowiorski K.♦, Chmielewski M.♦, The influence of spark plasma sintering on multiscale mechanical properties of nickel-based composite materials,
MATERIALS SCIENCE AND ENGINEERING A-STRUCTURAL MATERIALS PROPERTIES MICROSTRUCTURE AND PROCESSING, ISSN: 0921-5093, DOI: 10.1016/j.msea.2023.146001, Vol.891, pp.146001, 2024 Abstract: The paper presents a comprehensive investigation of the influence of the main process parameters of spark plasma sintering on the mechanical and microstructural properties of nickel-silicon carbide composites at various scales. Microstructure analysis performed by scanning and transmission electron microscopy revealed a significant interfacial reaction between nickel and silicon carbide due to the decomposition of silicon carbide. The chemical interaction of the matrix and reinforcement results in the formation of a multicomponent interphase zone formed by silicides (Ni31Si12 or/and Ni3Si) and graphite precipitates. Furthermore, several types of structure defects were observed (mainly nano/micropores at the phase boundaries). These significantly influenced the mechanical response of nickel-silicon carbide composites at different levels. At the macroscopic scale, uniaxial tensile tests confirmed that applying a 1000 oC sintering temperature ensured that the manufactured composite was characterised by satisfactory tensile strength, however, with a considerable reduction of material elongation compared to pure nickel. Moreover, the fractography study allowed us to identify a significant difference in the damage mode for certain nickel-silicon carbide samples. Secondly, the interface of the nickel matrix and silicate interphase was tested by bending with microcantilevers to evaluate its deformation behaviour, strength, and fracture characteristics. It was confirmed that a diffusive kind of interface, such as Ni-NiSi, demonstrates unexpected bonding properties with a relatively large range of plastic deformation. Finally, the nanoindentation of three main components of the nickel-silicon carbide composite was executed to evaluate the evolution of nanohardness, Young’s modulus, and elastic recovery due to the application of various spark plasma sintering conditions. Keywords: nickel-based composite,silicon carbide,spark plasma sintering,multiscale characterization,mechanical properties,nanoindentation,bending of microcantilevers Affiliations:
Nosewicz S. | - | IPPT PAN | Jenczyk P. | - | IPPT PAN | Romelczyk-Baishya B. | - | Warsaw University of Technology (PL) | Bazarnik P. | - | Warsaw University of Technology (PL) | Jarząbek D.M. | - | IPPT PAN | Majchrowicz K. | - | other affiliation | Pakieła Z. | - | Warsaw University of Technology (PL) | Kowiorski K. | - | other affiliation | Chmielewski M. | - | Institute of Electronic Materials Technology (PL) |
| 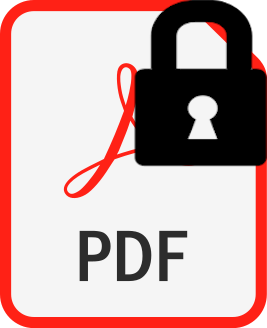 |
6. |
Ciurans-Oset M.♦, Flasar P.♦, Jenczyk P., Jarząbek D. M., Mouzon J.♦, Akhtar F.♦, Role of the microstructure and the residual strains on the mechanical properties of cast tungsten carbide produced by different methods,
Journal of Materials Research and Technology, ISSN: 2238-7854, DOI: 10.1016/j.jmrt.2024.04.067, Vol.30, pp.3640-3649, 2024 Abstract: Cast tungsten carbide (CTC) is a biphasic, pearlitic-like structure composed of WC lamellae in a matrix of W2C. Besides excellent flowability, spherical CTC powders exhibit superior hardness and wear resistance. Nevertheless, the available literature generally fails to explain the physical mechanisms behind such a phenomenon. In the present work, the microstructure and the mechanical properties of the novel centrifugally-atomized spherical CTC have been extensively investigated. This material exhibited an extremely fine microstructure, with WC lamellae of 27–29 nm in thickness and bulk lattice strains of 1.0–1.4 %, resulting in a microindentation hardness of 31.4 ± 1.6 GPa. The results of this study clearly show that centrifugally-atomized CTC is mechanically superior to both spheroidized CTC and conventional cast-and-crushed CTC. In addition, the effect of a series of heat treatments on the bulk fracture toughness and the fatigue life of entire CTC particles was also investigated. The reduction of residual stresses in the bulk of particles upon annealing dramatically increased the indentation fracture toughness, whereas the bulk microindentation hardness remained essentially unaffected. Regarding the fatigue life of entire particles under uniaxial cyclic compressive loading, local phase transformation phenomena at the surface of the particles upon heat treatment were concluded to play the most critical role. Indeed, the cumulative fatigue damage was minimized in surface-carburized CTC powders, where compressive stresses were induced at the outermost surface. Keywords: Cast tungsten carbide, Microindentation hardness, X-ray diffraction, Lattice microstrains, Dislocation density, Compression Affiliations:
Ciurans-Oset M. | - | other affiliation | Flasar P. | - | other affiliation | Jenczyk P. | - | IPPT PAN | Jarząbek D. M. | - | IPPT PAN | Mouzon J. | - | other affiliation | Akhtar F. | - | Luleå University of Technology (SE) |
| 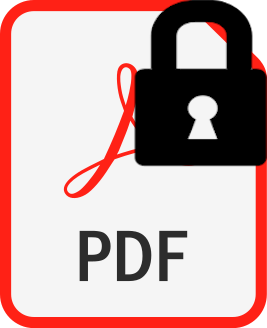 |
7. |
Milczarek M., Jarząbek D., Jenczyk P., Bochenek K., Filipiak M.♦, Novel paradigm in AFM probe fabrication: Broadened range of stiffness, materials, and tip shapes,
TRIBOLOGY INTERNATIONAL, ISSN: 0301-679X, DOI: 10.1016/j.triboint.2023.108308, Vol.180, No.108308, pp.1-12, 2023 Abstract: Atomic force microscopes could be used in wide range of nanotribology experiments but probes available on the market are only made of silicon or silicon nitride with a stiffness in the range of 0.01–100 N/m, which significantly limits the possible research. We strive to solve this problem by designing all-metal probes. The proposed fabrication method is characterised by the use of a copper substrate and electrodeposition in a mould prepared by indentation and photolithography. Prototype probes fabricated with this method were made of nickel with a stiffness of 20 N/m and 2800 N/m and were used for topography and friction measurements. Both the method and all-metal probes showed flexibility and great potential, especially in the field of nano/microtribology. Keywords: Atomic force microscopy, Microfabrication, Cantilever, Metal probe, Friction, Nanotribology Affiliations:
Milczarek M. | - | IPPT PAN | Jarząbek D. | - | IPPT PAN | Jenczyk P. | - | IPPT PAN | Bochenek K. | - | IPPT PAN | Filipiak M. | - | other affiliation |
| 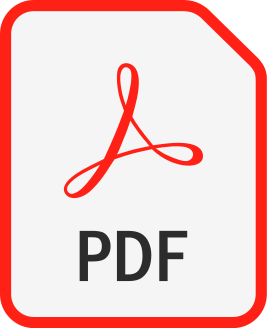 |
8. |
Wilczewski S.♦, Skórczewska K.♦, Tomaszewska J.♦, Osial M., Dąbrowska A.♦, Nikiforow K.♦, Jenczyk P., Grzywacz H., Graphene Modification by Curcuminoids as an Effective Method to Improve the Dispersion and Stability of PVC/Graphene Nanocomposites,
Molecules, ISSN: 1420-3049, DOI: 10.3390/molecules28083383, Vol.28, No.8, pp.1-25, 2023 Keywords: graphene, curcuminoids, poly(vinyl chloride), nanocomposites stability, polymer films Affiliations:
Wilczewski S. | - | other affiliation | Skórczewska K. | - | other affiliation | Tomaszewska J. | - | other affiliation | Osial M. | - | IPPT PAN | Dąbrowska A. | - | University of Warsaw (PL) | Nikiforow K. | - | other affiliation | Jenczyk P. | - | IPPT PAN | Grzywacz H. | - | IPPT PAN |
| 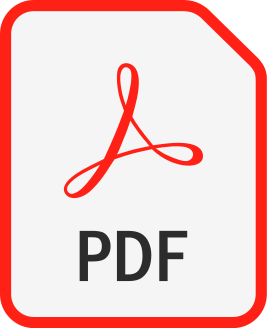 |
9. |
Abramowicz M.♦, Osial M., Urbańska W.♦, Walicki M.♦, Wilczewski S., Pręgowska A., Skórczewska K.♦, Jenczyk P., Warczak M.♦, Pisarek M.♦, Giersig M., Upcycling of Acid-Leaching Solutions from Li-Ion Battery Waste Treatment through the Facile Synthesis of Magnetorheological Fluid,
Molecules, ISSN: 1420-3049, DOI: 10.3390/molecules28062558, Vol.28, No.6, pp.2558-1-2558-16, 2023 Abstract: The rapidly growing production and usage of lithium-ion batteries (LIBs) dramatically raises the number of harmful wastes. Consequently, the LIBs waste management processes, taking into account reliability, efficiency, and sustainability criteria, became a hot issue in the context of environmental protection as well as the scarcity of metal resources. In this paper, we propose for the first time a functional material—a magnetorheological fluid (MRF) from the LIBs-based liquid waste containing heavy metal ions. At first, the spent battery waste powder was treated with acid-leaching, where the post-treatment acid-leaching solution (ALS) contained heavy metal ions including cobalt. Then, ALS was used during wet co-precipitation to obtain cobalt-doped superparamagnetic iron oxide nanoparticles (SPIONs) and as an effect, the harmful liquid waste was purified from cobalt. The obtained nanoparticles were characterized with SEM, TEM, XPS, and magnetometry. Subsequently, superparamagnetic nanoparticles sized 15 nm average in diameter and magnetization saturation of about 91 emu g−1 doped with Co were used to prepare the MRF that increases the viscosity by about 300% in the presence of the 100 mT magnetic fields. We propose a facile and cost-effective way to utilize harmful ALS waste and use them in the preparation of superparamagnetic particles to be used in the magnetorheological fluid. This work describes for the first time the second life of the battery waste in the MRF and a facile way to remove the harmful ingredients from the solutions obtained after the acid leaching of LIBs as an effective end-of-life option for hydrometallurgical waste utilization. Keywords: environment protection SPION, battery waste, toxic waste management, direct recycling, sustainability, circular economy, critical raw materials Affiliations:
Abramowicz M. | - | University of Warsaw (PL) | Osial M. | - | IPPT PAN | Urbańska W. | - | Wroclaw University of Science and Technology (PL) | Walicki M. | - | other affiliation | Wilczewski S. | - | IPPT PAN | Pręgowska A. | - | IPPT PAN | Skórczewska K. | - | other affiliation | Jenczyk P. | - | IPPT PAN | Warczak M. | - | Institute of Physical Chemistry, Polish Academy of Sciences (PL) | Pisarek M. | - | Institute of Physical Chemistry, Polish Academy of Sciences (PL) | Giersig M. | - | IPPT PAN |
| 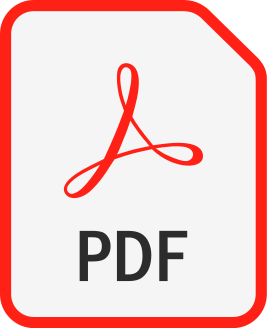 |
10. |
Manecka-Padaż A., Jenczyk P., Pęcherski R., Nykiel A.♦, Experimental investigation of Euler’s elastica: in-situ SEM nanowire post-buckling,
BULLETIN OF THE POLISH ACADEMY OF SCIENCES: TECHNICAL SCIENCES, ISSN: 0239-7528, DOI: 10.24425/bpasts.2022.143648, Vol.70(6), No.e143648, pp.1-6, 2023 Abstract: An in-situ nanoindenter with a flat tip was employed to conduct buckling tests of a single nanowire with simultaneous SEM imaging. A series of SEM images allowed us to calculate deflection. The deflection was confronted with the mathematical model of elastica. The post-buckling behaviour of nanowires is conducted in the framework of the nonlinear elasticity theory. Results show the significant effect of geometrical parameters on the stability of buckled nanowires. Keywords: post-buckling, nanowire, nanomechanics Affiliations:
Manecka-Padaż A. | - | IPPT PAN | Jenczyk P. | - | IPPT PAN | Pęcherski R. | - | IPPT PAN | Nykiel A. | - | other affiliation |
| 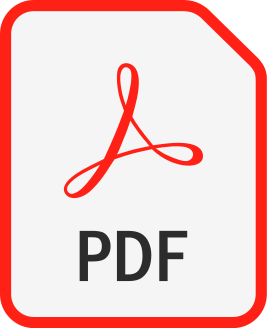 |
11. |
Wilczewski S.♦, Skórczewska K.♦, Tomaszewska J.♦, Lewandowski K.♦, Studziński W.♦, Osial M., Jenczyk P., Grzywacz H., Domańska A.♦, Curcuma longa L. Rhizome Extract as a Poly(vinyl chloride)/Graphene Nanocomposite Green Modifier,
Molecules, ISSN: 1420-3049, DOI: 10.3390/molecules27228081, Vol.27, No.8081, pp.1-18, 2022 Abstract: In this work, a method to increase the dispersion of graphene (GN) in the matrix of rigid
poly(vinyl chloride) (PVC) by using a natural plant extract from Curcuma longa L. (CE) is proposed. Currently, despite the increasing number of reports on the improvement of GN dispersion in PVC blends, still there is a need to find environmentally friendly and economical dispersion stabilizers. We proposed a stabilizer that can be easily obtained from a plant offering thermal stability and high effectiveness. PVC/GN nanocomposites stabilized with the proposed extract were investigated by SEM, AFM (structure), TGA, and Congo red test (thermal properties). Additionally, static and dynamic mechanical properties and electrical resistivity were measured. The use of CE as a graphene dispersant improved its dispersion in the PVC matrix, influenced tensile properties, increased the storage modulus and glass transition temperature, and extended the thermal stability time of nanocomposites. In this work, a CE extract is proposed as an efficient eco-friendly additive for the production of nanocomposites with an improved homogeneity of a nanofiller in the matrix and promising characteristics.
Keywords: nanocomposites,graphene,poly(vinyl chloride),curcuma extract Affiliations:
Wilczewski S. | - | other affiliation | Skórczewska K. | - | other affiliation | Tomaszewska J. | - | other affiliation | Lewandowski K. | - | other affiliation | Studziński W. | - | other affiliation | Osial M. | - | IPPT PAN | Jenczyk P. | - | IPPT PAN | Grzywacz H. | - | IPPT PAN | Domańska A. | - | other affiliation |
| 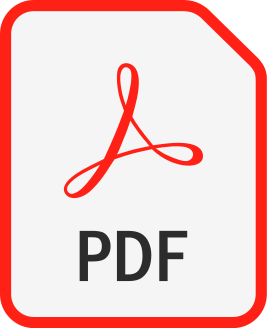 |
12. |
Jenczyk P., Jarząbek D.M., Lu Z.♦, Gadalińska E.♦, Levintant-Zayonts N., Zhang Y.♦, Unexpected crystallographic structure, phase transformation, and hardening behavior in the AlCoCrFeNiTi0.2 high-entropy alloy after high-dose nitrogen ion implantation,
Materials & Design, ISSN: 0264-1275, DOI: 10.1016/j.matdes.2022.110568, Vol.216, pp.110568-1-11, 2022 Abstract: Harsh environments, such as nuclear power plants, require the development of materials with stable properties when exposed to radiation/bombardment conditions. In this work, a bulk high-entropy alloy (HEA) was implanted with nitrogen ions accelerated at 50 kV to induce and study crystal structural defects. X-ray powder diffraction (XRD) showed that the studies HEA consisted of two phases—σ and body-centered cubic (BCC)—and underwent the σ to BCC phase transformation due to ion bombardment. Unexpectedly, XRD peaks of implanted samples could not be assigned to any known simple nitride, a finding that suggests the creation of new high- or medium-entropy ceramics. Studies of the mechanical and tribological properties with the use of nanoindentation and scratch tests revealed a hardening of both phases of the implanted surface and higher wear resistance. There were also surprising increases in the hardness-to-Young’s modulus ratio and elastic recovery for both phases. The results are promising not only for the nuclear applications, but also for space applications, mechanical engineering, and tribology. Keywords: high-entropy alloys, high-entropy ceramics, ion implantation, irradiation, phase transformation Affiliations:
Jenczyk P. | - | IPPT PAN | Jarząbek D.M. | - | IPPT PAN | Lu Z. | - | University of Science and Technology Beijing (CN) | Gadalińska E. | - | Institute of Aviation (PL) | Levintant-Zayonts N. | - | IPPT PAN | Zhang Y. | - | University of Science and Technology Beijing (CN) |
| 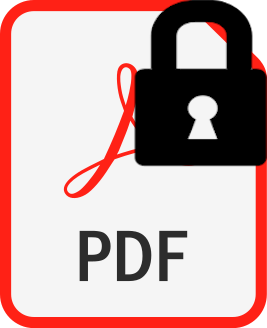 |
13. |
Grzywacz H., Jenczyk P., Milczarek M., Michałowski M.♦, Jarząbek D.M., Burger model as the best option for modeling of viscoelastic behavior of resists for nanoimprint lithography,
Materials, ISSN: 1996-1944, DOI: 10.3390/ma14216639, Vol.14, No.21, pp.6639-1-12, 2021 Abstract: In this study, Atomic Force Microscopy-based nanoindentation (AFM-NI) with diamond-like carbon (DLC) coated tip was used to analyze the mechanical response of poly(methyl methacrylate) (PMMA) thin films (thicknesses: 235 and 513 nm) on a silicon substrate. Then, Oliver and Pharr (OP) model was used to calculate hardness and Young’s modulus, while three different Static Linear Solid models were used to fit the creep curve and measure creep compliance, Young’s modulus, and viscosity. Values were compared with each other, and the best-suited method was suggested. The impact of four temperatures below the glass transition temperature and varied indentation depth on the mechanical properties has been analyzed. The results show high sensitivity on experiment parameters and there is a clear difference between thin and thick film. According to the requirements in the nanoimprint lithography (NIL), the ratio of hardness at demolding temperature to viscosity at molding temperature was introduced as a simple parameter for prediction of resist suitability for NIL. Finally, thinner PMMA film was tentatively attributed as more suitable for NIL. Keywords: PMMA, atomic force microscopy-based nanoindentation, Young’s modulus, hardness, viscosity, Burger creep model, nanoimprint lithography Affiliations:
Grzywacz H. | - | IPPT PAN | Jenczyk P. | - | IPPT PAN | Milczarek M. | - | IPPT PAN | Michałowski M. | - | Warsaw University of Technology (PL) | Jarząbek D.M. | - | IPPT PAN |
| 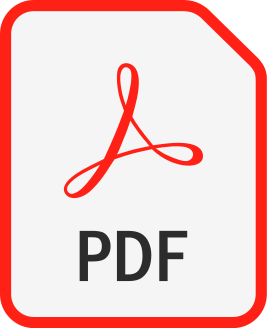 |
14. |
Psiuk R., Milczarek M., Jenczyk P., Denis P., Jarząbek D., Bazarnik P.♦, Pisarek M.♦, Mościcki T., Improved mechanical properties of W-Zr-B coatings deposited by hybrid RF magnetron – PLD method,
APPLIED SURFACE SCIENCE, ISSN: 0169-4332, DOI: 10.1016/j.apsusc.2021.151239, Vol.570, pp.151239-1-11, 2021 Abstract: In this work, novel W-Zr-B coatings were developed by a hybrid process combining pulsed laser deposited ZrB2 and radio frequency magnetron sputtered W2B5. The influence of the laser power density on the structure and mechanical properties of the deposited films was studied. Addition of zirconium causes a change in the structure of the deposited films from columnar to mainly amorphous. The nanoindentation tests and compression of nanopillars showed that doped W-Zr-B layers are still super-hard and incompressible in comparison to WB2 films without doping, but they change their behaviour from brittle to ductile. Films obtained with a fluence of 1.06 J/cm2 are superhard (H = 40 ± 4 GPa) and incompressible (12 ± 1 GPa), but possess a relatively low Young’s modulus (E = 330 ± 32 GPa) and a high elastic recovery (We = 0.9). Further increase in the fluence causes films to consist of deeply embedded fragments of laser ablated ZrB2 target in the deposited layer. Taking into account that the particles are made of ZrB2 which possess extraordinary thermal properties, and the matrix is made of W-Zr-B, a super-hard material, such a composite can also be interesting for industrial applications. Keywords: superhard tungsten borides, hybrid magnetron sputtering – pulsed laser deposition, nanopillar compression Affiliations:
Psiuk R. | - | IPPT PAN | Milczarek M. | - | IPPT PAN | Jenczyk P. | - | IPPT PAN | Denis P. | - | IPPT PAN | Jarząbek D. | - | IPPT PAN | Bazarnik P. | - | Warsaw University of Technology (PL) | Pisarek M. | - | Institute of Physical Chemistry, Polish Academy of Sciences (PL) | Mościcki T. | - | IPPT PAN |
| 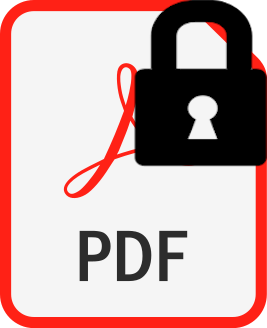 |
15. |
Nosewicz S., Bazarnik P.♦, Clozel M.♦, Kurpaska Ł.♦, Jenczyk P., Jarząbek D., Chmielewski M.♦, Romelczyk-Baishya B.♦, Lewandowska M.♦, Pakieła Z.♦, Huang Y.♦, Langdon T.G.♦, A multiscale experimental analysis of mechanical properties and deformation behavior of sintered copper–silicon carbide composites enhanced by high-pressure torsion,
ARCHIVES OF CIVIL AND MECHANICAL ENGINEERING, ISSN: 1644-9665, DOI: 10.1007/s43452-021-00286-4, Vol.21, pp.131-1-19, 2021 Abstract: Experiments were conducted to investigate, within the framework of a multiscale approach, the mechanical enhancement, deformation and damage behavior of copper–silicon carbide composites (Cu–SiC) fabricated by spark plasma sintering (SPS) and the combination of SPS with high-pressure torsion (HPT). The mechanical properties of the metal–matrix composites were determined at three different length scales corresponding to the macroscopic, micro- and nanoscale. Small punch testing was employed to evaluate the strength of composites at the macroscopic scale. Detailed analysis of microstructure evolution related to SPS and HPT, sample deformation and failure of fractured specimens was conducted using scanning and transmission electron microscopy. A microstructural study revealed changes in the damage behavior for samples processed by HPT and an explanation for this behavior was provided by mechanical testing performed at the micro- and nanoscale. The strength of copper samples and the metal–ceramic interface was determined by microtensile testing and the hardness of each composite component, corresponding to the metal matrix, metal–ceramic interface, and ceramic reinforcement, was measured using nano-indentation. The results confirm the advantageous effect of large plastic deformation on the mechanical properties of Cu–SiC composites and demonstrate the impact on these separate components on the deformation and damage type. Keywords: copper–silicon carbide composite, high-pressure torsion, metal–matrix composites, multiscale analysis, nano-indentation, small punch test Affiliations:
Nosewicz S. | - | IPPT PAN | Bazarnik P. | - | Warsaw University of Technology (PL) | Clozel M. | - | National Centre for Nuclear Research (PL) | Kurpaska Ł. | - | National Centre for Nuclear Research (PL) | Jenczyk P. | - | IPPT PAN | Jarząbek D. | - | IPPT PAN | Chmielewski M. | - | Institute of Electronic Materials Technology (PL) | Romelczyk-Baishya B. | - | Warsaw University of Technology (PL) | Lewandowska M. | - | other affiliation | Pakieła Z. | - | Warsaw University of Technology (PL) | Huang Y. | - | Bournemouth University (GB) | Langdon T.G. | - | University of Southampton (GB) |
| 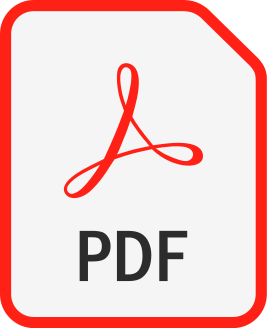 |
16. |
Jenczyk P., Grzywacz H., Milczarek M., Jarząbek D.M.♦, Mechanical and tribological properties of co-electrodeposited particulate-reinforced metal matrix composites: a critical review with interfacial aspects,
Materials, ISSN: 1996-1944, DOI: 10.3390/ma14123181, Vol.14, No.12, pp.3181-1-36, 2021 Abstract: Particulate-reinforced metal matrix composites (PRMMCs) with excellent tribo-mechanical properties are important engineering materials and have attracted constant scientific interest over the years. Among the various fabrication methods used, co-electrodeposition (CED) is valued due to its efficiency, accuracy, and affordability. However, the way this easy-to-perform process is carried out is inconsistent, with researchers using different methods for volume fraction measurement and tribo-mechanical testing, as well as failing to carry out proper interface characterization. The main contribution of this work lies in its determination of the gaps in the tribo-mechanical research of CED PRMMCs. For mechanical properties, hardness is described with respect to measurement methods, models, and experiments concerning CED PRMMCs. The tribology of such composites is described, taking into account the reinforcement volume fraction, size, and composite fabrication route (direct/pulsed current). Interfacial aspects are discussed using experimental direct strength measurements. Each part includes a critical overview, and future prospects are anticipated. This review paper provides an overview of the tribo-mechanical parameters of Ni-based co-electrodeposited particulate-reinforced metal matrix composite coatings with an interfacial viewpoint and a focus on hardness, wear, and friction behavior. Keywords: experimental mechanics, tribology, co-electrodeposited composites Affiliations:
Jenczyk P. | - | IPPT PAN | Grzywacz H. | - | IPPT PAN | Milczarek M. | - | IPPT PAN | Jarząbek D.M. | - | other affiliation |
| 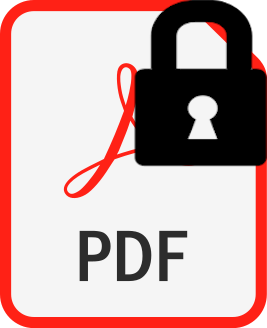 |
17. |
Grzywacz H.♦, Milczarek M., Jenczyk P., Dera W., Michałowski M.♦, Jarząbek D.M.♦, Quantitative measurement of nanofriction between PMMA thin films and various AFM probes,
MEASUREMENT, ISSN: 0263-2241, DOI: 10.1016/j.measurement.2020.108267, Vol.168, pp.108267-1-13, 2020 Abstract: This study reports the quantitative, precise and accurate results of nanoscale friction measurements with the use of an Atomic Force Microscope calibrated with a precise nanoforce sensor. For this purpose, three samples of spin-coated thin Polymethylmethacrylate (PMMA) films were prepared with the following thicknesses: 235, 343, and 513 nm. Three different AFM probes were used for the friction measurements: with diamond-like carbon (DLC) tip with a small (15 nm) or big (2 µm) tip radius, and a reference silicon tip with a small (8 nm) radius. The results show that in all of the studied cases, the coefficient of friction strongly depends on the applied load, being much higher for a lower load. Furthermore, a strong relation of the friction force on the cantilever's geometry, the scanning velocity, and the film thickness was observed. Keywords: lateral force microscopy, friction, thin PMMA films, atomic force microscope, DLC coatings, adhesion Affiliations:
Grzywacz H. | - | other affiliation | Milczarek M. | - | IPPT PAN | Jenczyk P. | - | IPPT PAN | Dera W. | - | IPPT PAN | Michałowski M. | - | Warsaw University of Technology (PL) | Jarząbek D.M. | - | other affiliation |
| 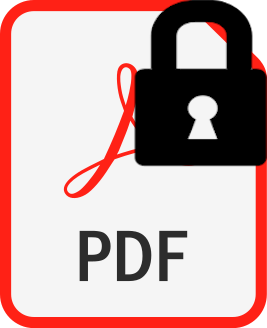 |
18. |
Alvi S.♦, Jarząbek D.M., Kohan M.G.♦, Hedman D.♦, Jenczyk P., Natile M.M.♦, Vomiero A.♦, Akhtar F.♦, Synthesis and mechanical characterization of a CuMoTaWV high-entropy film by magnetron sputtering,
ACS Applied Materials and Interfaces, ISSN: 1944-8244, DOI: 10.1021/acsami.0c02156, Vol.12, No.18, pp.21070-21079, 2020 Abstract: Development of high-entropy alloy (HEA) films is a promising and cost-effective way to incorporate these materials of superior properties in harsh environments. In this work, a refractory high-entropy alloy (RHEA) film of equimolar CuMoTaWV was deposited on silicon and 304 stainless-steel substrates using DC-magnetron sputtering. A sputtering target was developed by partial sintering of an equimolar powder mixture of Cu, Mo, Ta, W, and V using spark plasma sintering. The target was used to sputter a nanocrystalline RHEA film with a thickness of ~900 nm and an average grain size of 18 nm. X-ray diffraction of the film revealed a body-centered cubic solid solution with preferred orientation in the (110) directional plane. The nanocrystalline nature of the RHEA film resulted in a hardness of 19 ± 2.3 GPa and an elastic modulus of 259 ± 19.2 GPa. A high compressive strength of 10 ± 0.8 GPa was obtained in nanopillar compression due to solid solution hardening and grain boundary strengthening. The adhesion between the RHEA film and 304 stainless-steel substrates was increased on annealing. For the wear test against the E52100 alloy steel (Grade 25, 700-880 HV) at 1 N load, the RHEA film showed an average coefficient of friction (COF) and wear rate of 0.25 (RT) and 1.5 (300 °C), and 6.4 × 10^–6 mm^3/N m (RT) and 2.5 × 10^–5 mm^3/N m (300 °C), respectively. The COF was found to be 2 times lower at RT and wear rate 10^2 times lower at RT and 300 °C than those of 304 stainless steel. This study may lead to the processing of high-entropy alloy films for large-scale industrial applications. Keywords: high-entropy alloys, magnetron sputtering, spark plasma sintering, mechanical properties, wear Affiliations:
Alvi S. | - | Luleå University of Technology (SE) | Jarząbek D.M. | - | IPPT PAN | Kohan M.G. | - | Luleå University of Technology (SE) | Hedman D. | - | Luleå University of Technology (SE) | Jenczyk P. | - | IPPT PAN | Natile M.M. | - | other affiliation | Vomiero A. | - | Luleå University of Technology (SE) | Akhtar F. | - | Luleå University of Technology (SE) |
| 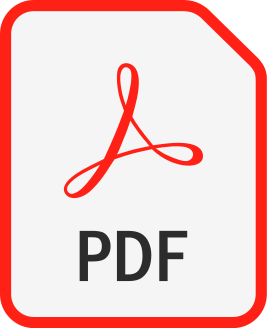 |
19. |
Jenczyk P., Gawrońska M.♦, Dera W., Chrzanowska-Giżyńska J., Denis P., Jarząbek D.M., Application of SiC particles coated with a protective Ni layer for production of Ni/SiC co-electrodeposited composite coatings with enhanced tribological properties,
CERAMICS INTERNATIONAL, ISSN: 0272-8842, DOI: 10.1016/j.ceramint.2019.08.063, Vol.45, No.17B, pp.23540-23547, 2019 Abstract: In this paper, the mechanical properties of composites consisting of electroplated Ni and co-electrodeposited SiC particles, coated with a thin protective layer of Ni, were studied. The protective layer was on the SiC particles prior to adding them to the electrolyte bath. It was demonstrated that due to the application of the protective layer it was possible to decrease sliding friction force, and improve the wear resistance, of the composite coatings in comparison with standard electroplated composite coatings made of Ni and co-electrodeposited pure SiC particles. Coating SiC particles with Ni was achieved by means of a PVD process. The main advantage of this step is avoiding oxidation of the surface of the particles during the contact with an electrolyte. Particles protected from oxidation lead to stronger interfacial bonding between the matrix and the reinforcement. Furthermore, better bonding protects the SiC particles from being extracted from the matrix by a counter-probe during friction and wear tests. The influence of the particle's concentration is studied. A smaller friction force and constant wear rate was observed. Keywords: wear, friction, interfacial bonding strength, metal matrix composites, silicon carbide, electrodeposited nickel Affiliations:
Jenczyk P. | - | IPPT PAN | Gawrońska M. | - | Warsaw University of Technology (PL) | Dera W. | - | IPPT PAN | Chrzanowska-Giżyńska J. | - | IPPT PAN | Denis P. | - | IPPT PAN | Jarząbek D.M. | - | IPPT PAN |
| 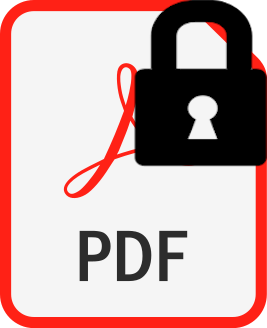 |