1. |
Kopeć M., Przygucka D.♦, Sitek R.♦, Jóźwiak S.♦, Orientation-dependent low-cycle fatigue and grain boundary evolution in DMLS-fabricated Haynes 282 superalloy,
Manufacturing Letters, ISSN: 2213-8463, DOI: 10.1016/j.mfglet.2025.06.206, Vol.45, pp.1-8, 2025 Streszczenie: This study investigates the effect of build orientation on the fatigue performance of Haynes 282 alloy manufactured via Direct Metal Laser Sintering at 0°, 45°, and 90°. Fatigue tests revealed superior service life for 0° and 45° orientations, attributed to equiaxed grains and high-angle grain boundaries identified by EBSD. Vertical builds exhibited columnar grains and reduced fatigue resistance. This work provides the first systematic correlation between grain boundary character and low-cycle fatigue behavior in DMLS-manufactured Haynes 282, expanding current understanding beyond Inconel-based systems and offering insights for orientation-based design optimization in critical high-temperature applications Słowa kluczowe: Nickel alloys, Fatigue, Additive manufacturing, Direct metal laser sintering (DMLS) Afiliacje autorów:
Kopeć M. | - | IPPT PAN | Przygucka D. | - | inna afiliacja | Sitek R. | - | Politechnika Warszawska (PL) | Jóźwiak S. | - | Military University of Technology (PL) |
| 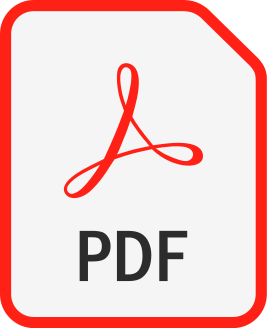 | 140p. |
2. |
Kopeć M., Przygucka D.♦, Mierzejewska I., Sitek R.♦, Kowalewski Z.L., Jóźwiak S.♦, Effect of printing orientation on microstructure and fatigue behaviour of additively manufactured Haynes 282,
JOURNAL OF ALLOYS AND COMPOUNDS, ISSN: 0925-8388, DOI: 10.1016/j.jallcom.2025.181777, No.181777, pp.1-16, 2025 Streszczenie: In this study, Haynes 282 alloy bars were fabricated using Direct Metal Laser Sintering (DMLS) in three build orientations: 0°, 45°, and 90°. The process was conducted under an argon protective atmosphere with an energy density of 104 J/mm³, a laser power of 100 W, and a scanning speed of 800 mm/s. The additively manufactured (AM) specimens underwent fatigue testing at stress amplitudes ranging from ±550 MPa to ±800 MPa. Specimens printed at 0° and 45° showed significantly improved mechanical performance, indicating these orientations are more favorable. Notably, the AM specimens demonstrated extended service life at stress amplitudes below 700 MPa, highlighting the potential of DMLS for producing durable Haynes 282 components. Słowa kluczowe: Haynes 282,nickel alloys,fatigue,additive manufacturing,Direct Metal Laser Sintering (DMLS) Afiliacje autorów:
Kopeć M. | - | IPPT PAN | Przygucka D. | - | inna afiliacja | Mierzejewska I. | - | IPPT PAN | Sitek R. | - | Politechnika Warszawska (PL) | Kowalewski Z.L. | - | IPPT PAN | Jóźwiak S. | - | Military University of Technology (PL) |
| 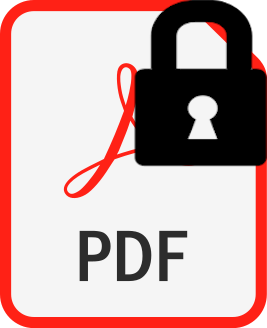 | 100p. |
3. |
Kopeć M., Liu X.♦, Gorniewicz D.♦, Modrzejewski P.♦, Zasada D.♦, Jóźwiak S.♦, Janiszewski J.♦, Kowalewski Z.L., Mechanical response of 6061-T6 aluminium alloy subjected to dynamic testing at low temperature: Experiment and modelling,
INTERNATIONAL JOURNAL OF IMPACT ENGINEERING, ISSN: 0734-743X, DOI: 10.1016/j.ijimpeng.2023.104843, Vol.185, No.104843, pp.1-10, 2024 Streszczenie: The aim of this research was to investigate an effect of low temperature on the mechanical properties and mi-crostructure of 6061-T6 aluminium alloy (AA6061-T6) subjected to dynamic loading. The specimens were subjected to dynamic compression at a low temperature of −80°C in a range of strain rates from 1.25 × 10 3 1/s to 3.4 × 10 3 1/s to compare their mechanical responses. The deformation mechanisms were analysed through EBSD observations during which dynamic recovery, was found as the dominant one. Furthermore, microstruc-tural analysis indicated that deformation under high strain rate conditions and temperature of-80°C enables to keep the constant initial grain size of the material after the loading applied. The material behaviour was modelled using mechanism-based viscoplastic constitutive equations. Furthermore, an accuracy of the developed model was validated by comparing it to experimental data. The set of constitutive equations proposed has been successful in modelling the stress-strain behaviour of the material for the range of strain rates and temperatures encountered in aluminium-forming processes under low-temperature conditions. Słowa kluczowe: Split Hopkinson pressure bar (SHPB),Low temperature,AA6061-T6,Microstructure Afiliacje autorów:
Kopeć M. | - | IPPT PAN | Liu X. | - | Imperial College London (GB) | Gorniewicz D. | - | Military University of Technology (PL) | Modrzejewski P. | - | inna afiliacja | Zasada D. | - | inna afiliacja | Jóźwiak S. | - | Military University of Technology (PL) | Janiszewski J. | - | Military University of Technology (PL) | Kowalewski Z.L. | - | IPPT PAN |
| 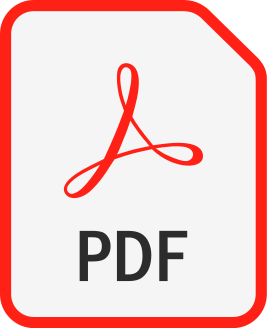 | 140p. |
4. |
Kopeć M., Mierzejewska I., Gorniewicz D.♦, Sitek R.♦, Jóźwiak S.♦, High-temperature oxidation behaviour of additively manufactured and wrought HAYNES 282,
JOURNAL OF MATERIALS SCIENCE, ISSN: 0022-2461, DOI: 10.1007/s10853-024-10207-4, pp.1-19, 2024 Streszczenie: Direct Metal Laser Sintered Haynes 282 specimens as well as wrought ones were subjected to high-temperature exposure at 1000 °C for 100h in air to compare their oxidation behaviour. The specimens were removed from the furnace after 1h, 5h, 25h, 50h and 100h to reveal and study oxidation mechanisms through morphological and cross-sectional examination by using scanning electron microscopy with energy dispersive spectroscopy attachment and X-ray diffraction. Microstructural studies revealed that the oxidation kinetics, determined by changes in thickness scale and depth of aluminium diffusion zone, were mainly driven by the formation of Cr2O3 for the wrought material, and TiO2 for DMLS one. The wrought material was characterized by the oxidation rate equal to 0.96 and followed the logarithmic law. On the other hand, DMLS-manufactured Haynes 282 exhibited oxidation rate of 0.90 and follows the linear law for the thickness scale considerations. However, when the depth of aluminium diffusion was investigated, it had an oxidation rate of 0.87 and followed cubic law. Afiliacje autorów:
Kopeć M. | - | IPPT PAN | Mierzejewska I. | - | IPPT PAN | Gorniewicz D. | - | Military University of Technology (PL) | Sitek R. | - | Politechnika Warszawska (PL) | Jóźwiak S. | - | Military University of Technology (PL) |
| 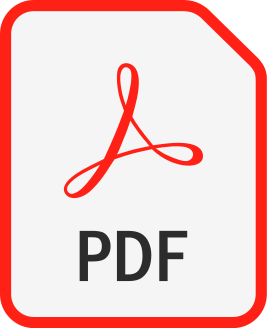 | 100p. |
5. |
Kopeć M., Gorniewicz D.♦, Jóźwiak S.♦, Janiszewski J.♦, Kowalewski Z.L., Microstructural evolution of 6061 aluminium alloy subjected to static and dynamic compression at low temperature,
MRS Communications, ISSN: 2159-6867, DOI: 10.1557/s43579-023-00439-x, pp.1-8, 2023 Streszczenie: In this research, an effect of low temperature on the mechanical properties and microstructure of 6061-T6 aluminium alloy (AA6061-T6) subjected to static and dynamic loading was investigated systematically. The specimens were subjected to compression at the temperature of − 80°C in a range of strain rates from 0.001 to 0.1 1/s under static conditions, and from 1250 to 3400 1/s under dynamic conditions to compare their mechanical responses. The deformation mechanisms were discussed based on EBSD analysis. It was found, that under both testing conditions, dynamic recovery was the dominant mechanism responsible for material deformation. Afiliacje autorów:
Kopeć M. | - | IPPT PAN | Gorniewicz D. | - | Military University of Technology (PL) | Jóźwiak S. | - | Military University of Technology (PL) | Janiszewski J. | - | Military University of Technology (PL) | Kowalewski Z.L. | - | IPPT PAN |
| 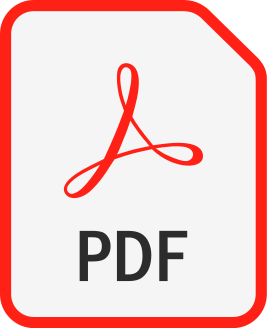 | 100p. |
6. |
Kopeć M., Gorniewicz D.♦, Kukla D., Barwińska I., Jóźwiak S.♦, Sitek R.♦, Kowalewski Z.L., Effect of plasma nitriding process on the fatigue and high temperature corrosion resistance of Inconel 740H nickel alloy,
ARCHIVES OF CIVIL AND MECHANICAL ENGINEERING, ISSN: 1644-9665, DOI: 10.1007/s43452-022-00381-0, pp.57-1-15, 2022 Streszczenie: The paper presents a comparison of microhardness, fatigue and high temperature corrosion of Inconel 740H nickel alloy in its as-received state and the same material with nitrided surface layers. The nitrided layers were produced using traditional glow discharge nitriding (specimens nitriding on the cathode potential) and an active screen (specimens nitriding at the plasma potential). A microstructure of the layers was characterized through the scanning electron microscopy, X-ray energy dispersive spectroscopy and X-ray diffraction analysis. Mechanical properties of the nitrided Inconel 740H alloy were examined using microhardness measurements and standard fatigue tests. It was found that Inconel 740H with a nitrided surface exhibited an improved fatigue response of 50 MPa in the whole range of stress amplitudes from 350 to 650 MPa and almost 325% increase of hardness for plasma modified surface and 250% for cathode modified surface. Additionally, the application of cathode nitriding enhanced the corrosion resistance of the alloy in question and effectively protected it against a high temperature oxidation. Słowa kluczowe: nitriding, nickel alloys, coatings, fatigue, corrosion Afiliacje autorów:
Kopeć M. | - | IPPT PAN | Gorniewicz D. | - | Military University of Technology (PL) | Kukla D. | - | IPPT PAN | Barwińska I. | - | IPPT PAN | Jóźwiak S. | - | Military University of Technology (PL) | Sitek R. | - | Politechnika Warszawska (PL) | Kowalewski Z.L. | - | IPPT PAN |
| 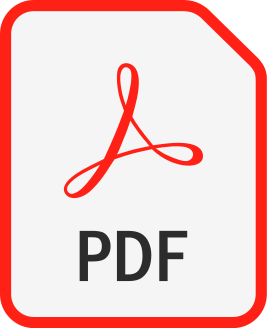 | 140p. |
7. |
Gorniewicz D.♦, Przygucki H.♦, Kopeć M., Karczewski K.♦, Jóźwiak S.♦, TiCoCrFeMn (BCC + C14) high-entropy alloy multiphase structure analysis based on the theory of molecular orbitals,
Materials, ISSN: 1996-1944, DOI: 10.3390/ma14185285, Vol.14, No.18, pp.5285-1-16, 2021 Streszczenie: High-entropy alloys (HEA) are a group of modern, perspective materials that have been intensively developed in recent years due to their superior properties and potential applications in many fields. The complexity of their chemical composition and the further interactions of main elements significantly inhibit the prediction of phases that may form during material processing. Thus, at the design stage of HEA fabrication, the molecular orbitals theory was proposed. In this method, the connection of the average strength of covalent bonding between the alloying elements (Bo parameter) and the average energy level of the d-orbital (parameter Md) enables for a preliminary assessment of the phase structure and the type of lattice for individual components in the formed alloy. The designed TiCoCrFeMn alloy was produced by the powder metallurgy method, preceded by mechanical alloying of the initial elementary powders and at the temperature of 1050 °C for 60 s. An ultra-fine-grained structured alloy was homogenized at 1000 °C for 1000 h. The X-ray diffraction and scanning electron microscopy analysis confirmed the correctness of the methodology proposed as the assumed phase structure consisted of the body-centered cubic (BCC) solid solution and the C14 Laves phase was obtained. Słowa kluczowe: HEA, solid solution, laves phase, U-FAST sintering Afiliacje autorów:
Gorniewicz D. | - | Military University of Technology (PL) | Przygucki H. | - | inna afiliacja | Kopeć M. | - | IPPT PAN | Karczewski K. | - | Military University of Technology (PL) | Jóźwiak S. | - | Military University of Technology (PL) |
| 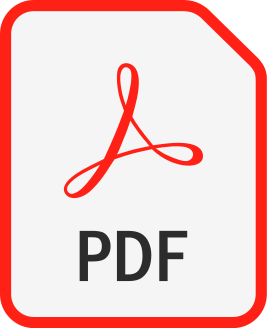 | 140p. |
8. |
Kopeć M., Jóźwiak S.♦, Kowalewski Z.L., Fe-Al based composite reinforced with ultra-fine Al2O3 oxides for high temperature applications,
JOURNAL OF THEORETICAL AND APPLIED MECHANICS, ISSN: 1429-2955, DOI: 10.15632/jtam-pl/138322, Vol.59, No.3, pp.509-513, 2021 Streszczenie: In this paper, an Fe-Al based composite reinforced with ultra-fine Al2O3 oxides was obtained through sintering of aluminium, iron and mullite ceramic powders using self-propagated high temperature synthesis (SHS). The powder mixture with a 50%wt. content of the ceramic reinforcement was cold pressed and subsequently subjected to the sintering process in vacuum at 1200◦C for 25 minutes under external loading of 25 kN. The complex microstructure of the Fe-Al matrix reinforced with ultra-fine Al2O3 oxides was found to be desired in high temperature applications since only 3% of the relative weight gain was observed after 100 hours of annealing at 900◦C. Słowa kluczowe: cermet composites, reaction synthesis, powder methods, electron microscopy Afiliacje autorów:
Kopeć M. | - | IPPT PAN | Jóźwiak S. | - | Military University of Technology (PL) | Kowalewski Z.L. | - | IPPT PAN |
| 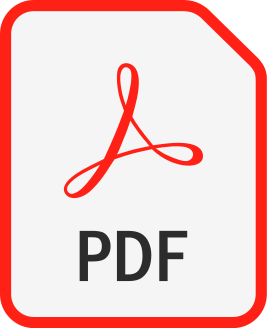 | 40p. |
9. |
Kukla D., Kopeć M., Kowalewski Z.L., Politis D.J.♦, Jóźwiak S.♦, Senderowski C.♦, Thermal barrier stability and wear behavior of CVD deposited aluminide coatings for MAR 247 nickel superalloy,
Materials, ISSN: 1996-1944, DOI: 10.3390/ma13173863, Vol.13, No.17, pp.3863-1-11, 2020 Streszczenie: In this paper, aluminide coatings of various thicknesses and microstructural uniformity obtained using chemical vapor deposition (CVD) were studied in detail. The optimized CVD process parameters of 1040 °C for 12 h in a protective hydrogen atmosphere enabled the production of high density and porosity-free aluminide coatings. These coatings were characterized by beneficial mechanical features including thermal stability, wear resistance and good adhesion strength to MAR 247 nickel superalloy substrate. The microstructure of the coating was characterized through scanning electron microscopy (SEM), X-ray energy dispersive spectroscopy (EDS) and X-ray diffraction (XRD) analysis. Mechanical properties and wear resistance of aluminide coatings were examined using microhardness, scratch test and standardized wear tests, respectively. Intermetallic phases from the Ni-Al system at specific thicknesses (20-30 µm), and the chemical and phase composition were successfully evaluated at optimized CVD process parameters. The optimization of the CVD process was verified to offer high performance coating properties including improved heat, adhesion and abrasion resistance. Słowa kluczowe: chemical vapor deposition, nickel alloys, coatings, X-ray analysis Afiliacje autorów:
Kukla D. | - | IPPT PAN | Kopeć M. | - | IPPT PAN | Kowalewski Z.L. | - | IPPT PAN | Politis D.J. | - | Imperial College London (GB) | Jóźwiak S. | - | Military University of Technology (PL) | Senderowski C. | - | inna afiliacja |
| 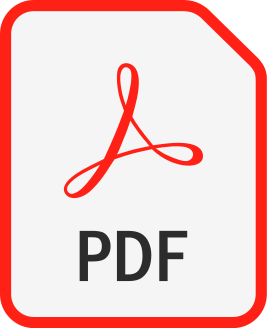 | 140p. |
10. |
Kopeć M., Jóźwiak S.♦, Kowalewski Z.L., A novel microstructural evolution model for growth of ultra-fine Al2O3 oxides from SiO2 silica ceramic decomposition during self-propagated high-temperature synthesis,
Materials, ISSN: 1996-1944, DOI: 10.3390/ma13122821, Vol.13, No.12, pp.2821-1-11, 2020 Streszczenie: In this paper, experimental verification of the microstructural evolution model during sintering of aluminum, iron and particulate mullite ceramic powders using self-propagated high-temperature synthesis (SHS) was performed. The powder mixture with 20% wt. content of reinforcing ceramic was investigated throughout this research. The mixed powders were cold pressed and sintered in a vacuum at 1030 °C. The SHS reaction between sintered feed powders resulted in a rapid temperature increase from the heat generated. The temperature increase led to the melting of an aluminum-based metallic liquid. The metallic liquid infiltrated the porous SiO2 ceramics. Silicon atoms were transited into the intermetallic iron-aluminum matrix. Subsequently, a ternary matrix from the Fe-Al-Si system was formed, and synthesis of the oxygen and aluminum occurred. Synthesis of both these elements resulted in formation of new, fine Al2O3 precipitates in the volume of matrix. The proposed microstructural evolution model for growth of ultra-fine Al2O3 oxides from SiO2 silica ceramic decomposition during SHS was successfully verified through scanning electron microscopy (SEM), X-ray energy-dispersive spectroscopy (EDS) analysis and X-ray diffraction (XRD). Słowa kluczowe: intermetallics, powder methods, electron microscopy, X-ray analysis Afiliacje autorów:
Kopeć M. | - | IPPT PAN | Jóźwiak S. | - | Military University of Technology (PL) | Kowalewski Z.L. | - | IPPT PAN |
| 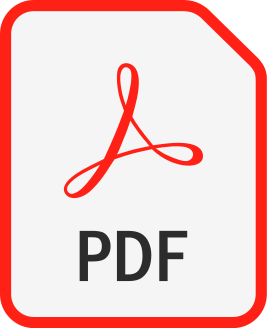 | 140p. |
11. |
Jóźwiak S.♦, Systemy wiedzy w optymalizacji,
Prace IPPT - IFTR Reports, ISSN: 2299-3657, No.3, pp.1-40, 1990 | |