1. |
Kalita D.♦, Mulewska K.♦, Jóźwik I.♦, Zaborowska A.♦, Gawęda M.♦, Chromiński W.♦, Bochenek K., Rogal Ł.♦, Metastable β-Phase Ti–Nb Alloys Fabricated by Powder Metallurgy: Effect of Nb on Superelasticity and Deformation Behavior,
METALLURGICAL AND MATERIALS TRANSACTIONS A-PHYSICAL METALLURGY AND MATERIALS SCIENCE, ISSN: 1073-5623, DOI: 10.1007/s11661-023-07285-5, pp.1-17, 2024 Streszczenie: This study investigates the effect of Nb concentration on the mechanical properties, superelasticity, as well as deformation behavior of metastable β-phase Ti–Nb alloys produced via powder metallurgy. The alloys were fabricated through mechanical alloying, followed by consolidation using hot pressing. The resulting microstructure comprises fine β-phase grains with TiC carbide precipitates at the grain boundaries. The study reveals non-linear variations in the values of yield strength for the manufactured materials, which were attributed to the occurrence of various deformation mechanisms activated during the loading. It was found that the mechanisms change with the increasing concentration of Nb in the manner: stress-induced martensitic transformation, twinning, slip. However, all these mechanisms were activated at a reduced concentration of Nb compared to the materials obtained by casting technology previously reported in the literature. This is most probably associated with the elevated oxygen content, which affects the stability of the parent β-phase. The study revealed that superelasticity in Ti–Nb-based alloys prepared using powder metallurgy may be achieved by reducing the content of β-stabilizing elements compared to alloys obtained by conventional technologies. In this study, the Ti–14Nb (at. pct) alloy exhibited the best superelasticity, whereas conventionally fabricated Ti–Nb alloys displayed superelasticity at an Nb concentration of approximately 26 at. pct. The developed material exhibited a non-conventional, one-stage yielding behavior, resulting in a superelastic response at significantly higher stresses compared to conventionally fabricated Ti–Nb alloys. Afiliacje autorów:
Kalita D. | - | inna afiliacja | Mulewska K. | - | National Centre for Nuclear Research (PL) | Jóźwik I. | - | Institute of Electronic Materials Technology (PL) | Zaborowska A. | - | inna afiliacja | Gawęda M. | - | inna afiliacja | Chromiński W. | - | inna afiliacja | Bochenek K. | - | IPPT PAN | Rogal Ł. | - | Institute of Metallurgy and Materials Science, Polish Academy of Sciences (PL) |
| 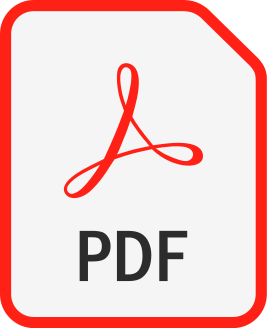 | 200p. |
2. |
Nosewicz S., Jurczak G., Chromiński W.♦, Rojek J., Kaszyca K.♦, Chmielewski M.♦, Combined EBSD and Computer-Assisted Quantitative Analysis of the Impact of Spark Plasma Sintering Parameters on the Structure of Porous Materials,
METALLURGICAL AND MATERIALS TRANSACTIONS A-PHYSICAL METALLURGY AND MATERIALS SCIENCE, ISSN: 1073-5623, DOI: 10.1007/s11661-022-06821-z, Vol.53, pp.4101-4125, 2022 Streszczenie: The paper presents the experimental, numerical, and theoretical investigation of the microstructure of nickel aluminide samples manufactured by spark plasma sintering using electron backscatter diffraction and computer assisted software. The aim of the work was to reveal the evolution of the microscopic and macroscopic parameters related to the microstructure of the material and its dependence on the applied sintering parameters—temperature and pressure. The studied porous samples with different relative density were extracted from various planes and then tested by electron backscatter diffraction to evaluate the crystallographic orientation in every spot of the investigated area. On this foundation, the grain structure of the samples was determined and carefully described in terms of the grain size, shape and boundary contact features. Several parameters reflecting the grain morphology were introduced. The application of the electric current resulting in high temperature and the additional external loading leads to the significant changes in the structure of the porous sample, such as the occurrence of lattice reorientation resulting in grain growth, increase in the grain neighbours, or the evolution of grain ellipticity, circularity, grain boundary length, and fraction. Furthermore, the numerical simulation of heat conduction via a finite element framework was performed in order to analyse the connectivity of the structures. The numerical results related to the thermal properties at the micro- and macroscopic scale—local heat fluxes, deviation angles, and effective thermal conductivity—were evaluated and studied in the context of the microstructural porosity. Finally, the effective thermal conductivity of two-dimensional EBSD maps was compared with those obtained from finite element simulations of three-dimensional micro-CT structures. The relationship between the 2D and 3D results was derived by using the analytical Landauer model. Afiliacje autorów:
Nosewicz S. | - | IPPT PAN | Jurczak G. | - | IPPT PAN | Chromiński W. | - | inna afiliacja | Rojek J. | - | IPPT PAN | Kaszyca K. | - | Lukasiewicz Institute of Microelectronics and Photonics (PL) | Chmielewski M. | - | Institute of Electronic Materials Technology (PL) |
| 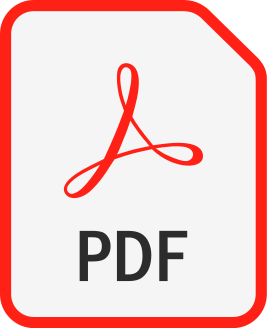 | 200p. |