1. |
Dera W., Konopacka H., Jarząbek D., Development of a novel nickel-based metal force microsensor using bottom-up approach,
Precision Engineering, ISSN: 1873-2372, DOI: 10.1016/j.precisioneng.2025.05.003, pp.251-261, 2025 Abstract: The advancement of force microsensors has shifted towards alternative fabrication methods offering enhanced flexibility, cost efficiency, and adaptability. Traditional silicon-based sensors face limitations such as mechanical fragility, thermal expansion mismatches, and high fabrication costs, necessitating alternative approaches. This study explores a bottom-up fabrication approach using electro-galvanic deposition to develop nickel-based capacitive force microsensors. Unlike conventional methods, electro-galvanic deposition enables precise control over material thickness and microstructure, allowing for the fabrication of robust, metal-based sensors with superior toughness and mechanical reliability. Nickel, chosen for its high tensile strength, corrosion resistance, and adaptability to high temperatures, is well-suited for demanding applications. The fabrication process involves UV maskless lithography for mold patterning, followed by electro-galvanic deposition in a modified Watt's bath with saccharin additives to control grain structure. This enables fine-tuning of nickel's mechanical properties, enhancing hardness and ductility. The capacitive comb sensor structure, integrated with a high-resolution capacitance-to-digital converter, enables precise force measurements with a linear response and high sensitivity. Experimental validation included mechanical testing, calibration, and stability analysis under controlled loading conditions. Results confirmed a strong linear force-capacitance relationship (R2 = 0.9898) and excellent long-term stability, with minimal capacitance drift under sustained load.
Keywords: Nickel-based sensor, Bottom-up process for sensor fabrication, Electro-galvanic deposition, Capacitance stability, Silicon sensor limitations, Industrial sensor applications, Sensor durability, Displacement-force calibration Affiliations:
Dera W. | - | IPPT PAN | Konopacka H. | - | IPPT PAN | Jarząbek D. | - | IPPT PAN |
| 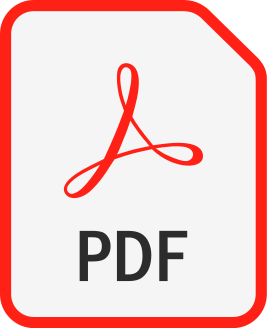 |
2. |
Włoczewski M., Jasiewicz K., Jenczyk P., Gadalińska E.♦, Kulikowski K.♦, Zhang Y.♦, Li R.♦, Jarząbek D. M., AlCoCrFeNiTi0.2 High-Entropy Alloy Under Plasma Nitriding: Complex Microstructure Transformation, Mechanical and Tribological Enhancement,
METALLURGICAL AND MATERIALS TRANSACTIONS A-PHYSICAL METALLURGY AND MATERIALS SCIENCE, ISSN: 1073-5623, DOI: 10.1007/s11661-025-07752-1, pp.1-17, 2025 Abstract: In this study, the AlCoCrFeNiTi0.2 high-entropy alloy (HEA) was plasma nitrided to investigate the microstructure and mechanical properties of high-entropy nitrides formed in the surface layer of the bulk sample. XRD measurements revealed a BCC → FCC crystal structure transformation, with the σ phase disappearing and hexagonal aluminum nitride emerging. Further experimental studies on the nitrided samples, including SEM, EDS, and EBSD, uncovered element segregation into multiple FCC phases with similar lattice constants, such as the NaCl-type (AlCrCoFeNiTi0.2)N high-entropy nitride. These observations align with theoretical analysis based on KKR-CPA calculations. Additionally, plasma nitriding induced high surface porosity; however, micropillar compression testing combined with nanoindentation revealed localized areas with significant hardness. A substantial reduction in the coefficient of friction was also observed. These findings not only provide deeper insights into the nitriding process of complex alloys, like dual-phase HEAs, but also hold promise for further exploration in the manufacturing of super-hard surfaces with high-entropy nitrides, enhancing mechanical properties for applications in harsh environments. Affiliations:
Włoczewski M. | - | IPPT PAN | Jasiewicz K. | - | IPPT PAN | Jenczyk P. | - | IPPT PAN | Gadalińska E. | - | Institute of Aviation (PL) | Kulikowski K. | - | other affiliation | Zhang Y. | - | University of Notre Dame (US) | Li R. | - | other affiliation | Jarząbek D. M. | - | IPPT PAN |
| 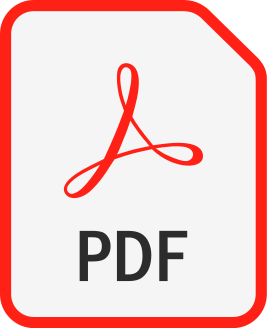 |
3. |
Brachaczek A., Tokpatayeva R.♦, Olek J.♦, Jarząbek D.M., Piotrowski P.♦, Jenczyk P., Jóźwiak-Niedźwiedzka D., Impact of formate based deicing agents on ASR products: Microstructural, chemical and mechanical characteristics,
CONSTRUCTION AND BUILDING MATERIALS, ISSN: 0950-0618, DOI: 10.1016/j.conbuildmat.2025.140729, Vol.471, No.140729, pp.1-12, 2025 Abstract: This study investigates the effects of formate-based deicing agents, specifically potassium formate (HCOOK) and sodium formate (HCOONa), on alkali-silica reaction (ASR) in concrete. By adapting ASTM C1260 standards, mortar bars were subjected to deicing solutions of varying concentrations to evaluate their influence on mortar expansion and ASR product characteristics. Results revealed that high concentrations of formate solutions significantly accelerated ASR, inducing expansions comparable to or greater than those caused by sodium hydroxide, while sodium chloride showed minimal expansion effects. Microstructural and chemical analyses demonstrated that ASR gels formed in formate solutions were predominantly amorphous, with different chemical composition depending on the deicer type. Pore solution analysis indicated a strong correlation between alkali ion concentration and mortar expansion. Furthermore, mechanical testing of ASR products revealed that gels formed in potassium formate exhibited higher hardness and elastic modulus compared to those formed in sodium formate. These findings enhance understanding of the detrimental effects of formate-based deicing agents on ASR and provide a foundation for developing mitigation strategies to preserve concrete infrastructure. Keywords: Alkali-silica reaction,Concrete microstructure,Expansion,Nanoindentation,Deicing agents,Pore solution analysis Affiliations:
Brachaczek A. | - | IPPT PAN | Tokpatayeva R. | - | other affiliation | Olek J. | - | Purdue University (US) | Jarząbek D.M. | - | IPPT PAN | Piotrowski P. | - | other affiliation | Jenczyk P. | - | IPPT PAN | Jóźwiak-Niedźwiedzka D. | - | IPPT PAN |
| 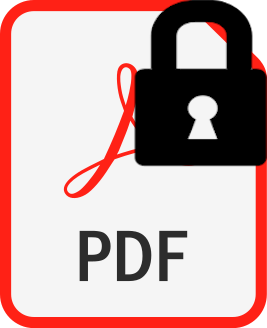 |
4. |
Jarząbek D. M., Włoczewski M.♦, Milczarek M., Jenczyk P., Takesue N.♦, Golasiński K.♦, Pieczyska E. A., Deformation Mechanisms of (100) and (110) Single-Crystal BCC Gum Metal Studied by Nanoindentation and Micropillar Compression,
METALLURGICAL AND MATERIALS TRANSACTIONS A-PHYSICAL METALLURGY AND MATERIALS SCIENCE, ISSN: 1073-5623, DOI: 10.1007/s11661-024-07605-3, pp.1-11, 2024 Abstract: In this paper, small-scale testing techniques—nanoindentation and micropillar compression—were used to investigate the deformation mechanisms, size effects, and strain rate sensitivity of (100) and (110) single-crystal Gum Metal at the micro/nanoscale. It was observed that the (100) orientation exhibits a significant size effect, resulting in hardness values ranging from 1 to 5 GPa. Conversely, for the (110) orientation, this effect was weaker. Furthermore, the yield strength obtained from the micropillar compression tests was approximately 740 MPa for the (100) orientation and 650 MPa for the (110) orientation. The observed deformations were consistent with the established features of the deformation behavior of body-centered cubic (bcc) alloys: significant strain rate sensitivity with no depth dependence, pile-up patterns comparable to those reported in the literature, and shear along the {112}<111> slip directions. However, the investigated material also exhibited Gum Metal-like high ductility, a relatively low modulus of elasticity, and high yield strength, which distinguishes it from classic bcc alloys. Affiliations:
Jarząbek D. M. | - | IPPT PAN | Włoczewski M. | - | other affiliation | Milczarek M. | - | IPPT PAN | Jenczyk P. | - | IPPT PAN | Takesue N. | - | Fukuoka University (JP) | Golasiński K. | - | other affiliation | Pieczyska E. A. | - | IPPT PAN |
| 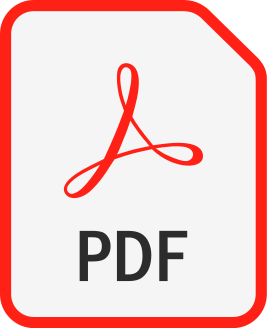 |
5. |
Jóźwiak-Niedźwiedzka D., Jaskulski R.♦, Dziedzic K., Brachaczek A., Jarząbek D.♦, Initial Characteristics of Alkali–Silica Reaction Products in Mortar Containing Low-Purity Calcined Clay,
Materials, ISSN: 1996-1944, DOI: 10.3390/ma17102207, Vol.17, No.10, pp.1-15, 2024 Abstract: An alkali–silica reaction (ASR) is a chemical process that leads to the formation of an expansive gel, potentially causing durability issues in concrete structures. This article investigates the properties and behaviour of ASR products in mortar with the addition of low-purity calcined clay as an additional material. This study includes an evaluation of the expansion and microstructural characteristics of the mortar, as well as an analysis of the formation and behaviour of ASR products with different contents of calcined clay. Expansion tests of the mortar beam specimens were conducted according to ASTM C1567, and a detailed microscopic analysis of the reaction products was performed. Additionally, their mechanical properties were determined using nanoindentation. This study reveals that with an increasing calcined clay content, the amount of the crystalline form of the ASR gel decreases, while the nanohardness increases. The Young’s modulus of the amorphous ASR products ranged from 5 to 12 GPa, while the nanohardness ranged from 0.41 to 0.67 GPa. The obtained results contribute to a better understanding of how the incorporation of low-purity calcined clay influences the ASR in mortar, providing valuable insights into developing sustainable and durable building materials for the construction industry. Keywords: alkali–silica reaction, ASR products, calcined clay, mortar, expansion Affiliations:
Jóźwiak-Niedźwiedzka D. | - | IPPT PAN | Jaskulski R. | - | other affiliation | Dziedzic K. | - | IPPT PAN | Brachaczek A. | - | IPPT PAN | Jarząbek D. | - | other affiliation |
| 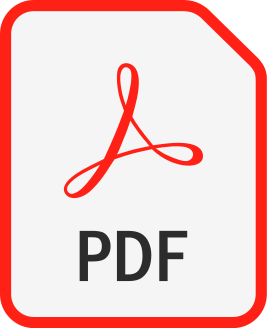 |
6. |
Nosewicz S., Jenczyk P., Romelczyk-Baishya B.♦, Bazarnik P.♦, Jarząbek D.M., Majchrowicz K.♦, Pakieła Z.♦, Kowiorski K.♦, Chmielewski M.♦, The influence of spark plasma sintering on multiscale mechanical properties of nickel-based composite materials,
MATERIALS SCIENCE AND ENGINEERING A-STRUCTURAL MATERIALS PROPERTIES MICROSTRUCTURE AND PROCESSING, ISSN: 0921-5093, DOI: 10.1016/j.msea.2023.146001, Vol.891, pp.146001, 2024 Abstract: The paper presents a comprehensive investigation of the influence of the main process parameters of spark plasma sintering on the mechanical and microstructural properties of nickel-silicon carbide composites at various scales. Microstructure analysis performed by scanning and transmission electron microscopy revealed a significant interfacial reaction between nickel and silicon carbide due to the decomposition of silicon carbide. The chemical interaction of the matrix and reinforcement results in the formation of a multicomponent interphase zone formed by silicides (Ni31Si12 or/and Ni3Si) and graphite precipitates. Furthermore, several types of structure defects were observed (mainly nano/micropores at the phase boundaries). These significantly influenced the mechanical response of nickel-silicon carbide composites at different levels. At the macroscopic scale, uniaxial tensile tests confirmed that applying a 1000 oC sintering temperature ensured that the manufactured composite was characterised by satisfactory tensile strength, however, with a considerable reduction of material elongation compared to pure nickel. Moreover, the fractography study allowed us to identify a significant difference in the damage mode for certain nickel-silicon carbide samples. Secondly, the interface of the nickel matrix and silicate interphase was tested by bending with microcantilevers to evaluate its deformation behaviour, strength, and fracture characteristics. It was confirmed that a diffusive kind of interface, such as Ni-NiSi, demonstrates unexpected bonding properties with a relatively large range of plastic deformation. Finally, the nanoindentation of three main components of the nickel-silicon carbide composite was executed to evaluate the evolution of nanohardness, Young’s modulus, and elastic recovery due to the application of various spark plasma sintering conditions. Keywords: nickel-based composite,silicon carbide,spark plasma sintering,multiscale characterization,mechanical properties,nanoindentation,bending of microcantilevers Affiliations:
Nosewicz S. | - | IPPT PAN | Jenczyk P. | - | IPPT PAN | Romelczyk-Baishya B. | - | Warsaw University of Technology (PL) | Bazarnik P. | - | Warsaw University of Technology (PL) | Jarząbek D.M. | - | IPPT PAN | Majchrowicz K. | - | other affiliation | Pakieła Z. | - | Warsaw University of Technology (PL) | Kowiorski K. | - | other affiliation | Chmielewski M. | - | Institute of Electronic Materials Technology (PL) |
| 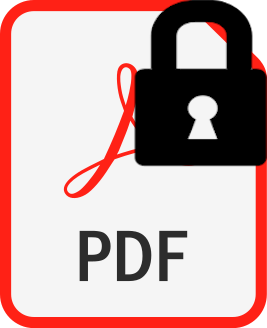 |
7. |
Mościcki T. P., Psiuk R., Jarząbek D. M., Ciemiorek-Bartkowska M.♦, Kulikowski K.♦, Jasiński J.♦, Włoczewski M.♦, Lewandowska-Szumieł M.♦, Effect of titanium and deposition parameters on microstructure and mechanical properties of W-Ti-B thin films deposited by High Power Impulse Magnetron Sputtering,
SURFACE AND COATINGS TECHNOLOGY, ISSN: 0257-8972, DOI: 10.1016/j.surfcoat.2024.130915, Vol.485, No.130915, pp.1-13, 2024 Abstract: Tungsten diboride alloyed with transition metals provides an opportunity to obtain exceptional mechanical, physical, and chemical properties. We report a strategy for designing and synthesizing of superhard and low-compressible ceramic thin films with increased toughness and lowered residual stresses (σ < −0.9 GPa) deposited with high-power impulse magnetron sputtering (HiPIMS) from one target. The addition of 7–12 % titanium promotes additional strengthening mechanisms of the layers in one material, leading to the improvement of wear resistance compared to an alloyed WB2-z yet at even higher hardness 43.8 ± 2.1 GPa and nanoindentation toughness 4.9 ± 0.2 MPa√m. The compression of the micropillar shows that titanium addition changed the type of nanoindentation from cracking along the slip plane to bulging on the top of the pillar and next the crack initiation along column boundaries. The highest adhesion of the layers is obtained for addition of 7 % titanium and in all cases the wear has abrasive character. The controlled use of 200 μs pulses during synthesis with HiPIMS allows for an increase in the deposition rate and maintaining exceptional mechanical properties of the layers even at a substrate temperature of 300 °C. Keywords: Ternary transition metal diboride thin films, Mechanical properties, HiPIMS magnetron sputtering, Wear resistance and adhesion Affiliations:
Mościcki T. P. | - | IPPT PAN | Psiuk R. | - | IPPT PAN | Jarząbek D. M. | - | IPPT PAN | Ciemiorek-Bartkowska M. | - | other affiliation | Kulikowski K. | - | other affiliation | Jasiński J. | - | other affiliation | Włoczewski M. | - | other affiliation | Lewandowska-Szumieł M. | - | other affiliation |
| 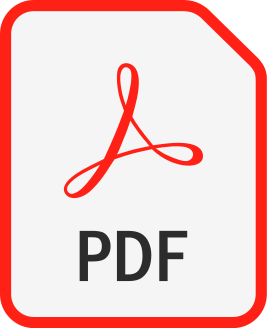 |
8. |
Ciurans-Oset M.♦, Flasar P.♦, Jenczyk P., Jarząbek D. M., Mouzon J.♦, Akhtar F.♦, Role of the microstructure and the residual strains on the mechanical properties of cast tungsten carbide produced by different methods,
Journal of Materials Research and Technology, ISSN: 2238-7854, DOI: 10.1016/j.jmrt.2024.04.067, Vol.30, pp.3640-3649, 2024 Abstract: Cast tungsten carbide (CTC) is a biphasic, pearlitic-like structure composed of WC lamellae in a matrix of W2C. Besides excellent flowability, spherical CTC powders exhibit superior hardness and wear resistance. Nevertheless, the available literature generally fails to explain the physical mechanisms behind such a phenomenon. In the present work, the microstructure and the mechanical properties of the novel centrifugally-atomized spherical CTC have been extensively investigated. This material exhibited an extremely fine microstructure, with WC lamellae of 27–29 nm in thickness and bulk lattice strains of 1.0–1.4 %, resulting in a microindentation hardness of 31.4 ± 1.6 GPa. The results of this study clearly show that centrifugally-atomized CTC is mechanically superior to both spheroidized CTC and conventional cast-and-crushed CTC. In addition, the effect of a series of heat treatments on the bulk fracture toughness and the fatigue life of entire CTC particles was also investigated. The reduction of residual stresses in the bulk of particles upon annealing dramatically increased the indentation fracture toughness, whereas the bulk microindentation hardness remained essentially unaffected. Regarding the fatigue life of entire particles under uniaxial cyclic compressive loading, local phase transformation phenomena at the surface of the particles upon heat treatment were concluded to play the most critical role. Indeed, the cumulative fatigue damage was minimized in surface-carburized CTC powders, where compressive stresses were induced at the outermost surface. Keywords: Cast tungsten carbide, Microindentation hardness, X-ray diffraction, Lattice microstrains, Dislocation density, Compression Affiliations:
Ciurans-Oset M. | - | other affiliation | Flasar P. | - | other affiliation | Jenczyk P. | - | IPPT PAN | Jarząbek D. M. | - | IPPT PAN | Mouzon J. | - | other affiliation | Akhtar F. | - | Luleå University of Technology (SE) |
| 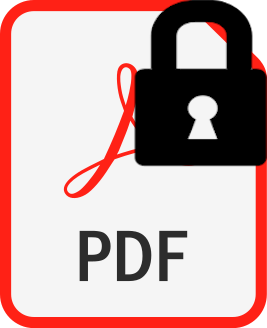 |
9. |
Milczarek M., Jarząbek D., Jenczyk P., Bochenek K., Filipiak M.♦, Novel paradigm in AFM probe fabrication: Broadened range of stiffness, materials, and tip shapes,
TRIBOLOGY INTERNATIONAL, ISSN: 0301-679X, DOI: 10.1016/j.triboint.2023.108308, Vol.180, No.108308, pp.1-12, 2023 Abstract: Atomic force microscopes could be used in wide range of nanotribology experiments but probes available on the market are only made of silicon or silicon nitride with a stiffness in the range of 0.01–100 N/m, which significantly limits the possible research. We strive to solve this problem by designing all-metal probes. The proposed fabrication method is characterised by the use of a copper substrate and electrodeposition in a mould prepared by indentation and photolithography. Prototype probes fabricated with this method were made of nickel with a stiffness of 20 N/m and 2800 N/m and were used for topography and friction measurements. Both the method and all-metal probes showed flexibility and great potential, especially in the field of nano/microtribology. Keywords: Atomic force microscopy, Microfabrication, Cantilever, Metal probe, Friction, Nanotribology Affiliations:
Milczarek M. | - | IPPT PAN | Jarząbek D. | - | IPPT PAN | Jenczyk P. | - | IPPT PAN | Bochenek K. | - | IPPT PAN | Filipiak M. | - | other affiliation |
| 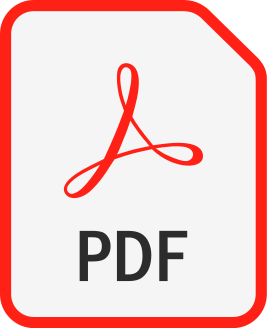 |
10. |
Krajewski M., Kaczmarek A., Tokarczyk M.♦, Lewińska S.♦, Włoczewski M.♦, Bochenek K., Jarząbek D., Mościcki T., Hoffman J., Ślawska-Waniewska A.♦, Laser-Assisted Growth of Fe3O4 Nanoparticle Films on Silicon Substrate in Open Air,
physica status solidi (a), ISSN: 1862-6319, DOI: 10.1002/pssa.202200786, No.2200786, pp.1-5, 2023 Abstract: This work presents a growth of Fe3O4 nanoparticle films on silicon substrate. The iron oxide is deposited applying a pulsed laser deposition technique. The process is performed in open air in the absence and presence of external magnetic field. In fact, the morphologies of the obtained Fe3O4–Si samples are similar. The Fe3O4 nanoparticles are spherical with average diameters of 30 nm and are densely agglomerated on the Si substrate. The Fe3O4–Si material prepared in the absence of magnetic field has revealed more intense signals during X-ray diffraction and Raman measurements. The magnetic investigations indicate that the Fe3O4 nanoparticles are significantly coupled with the Si substrate and do not exhibit superparamagnetic behavior. Moreover, the Verwey transition is 98 K for both investigated Fe3O4–Si samples. Keywords: Fe3O4 nanoparticles,magnetic materials,pulsed laser deposition Affiliations:
Krajewski M. | - | IPPT PAN | Kaczmarek A. | - | IPPT PAN | Tokarczyk M. | - | University of Warsaw (PL) | Lewińska S. | - | Institute of Physics, Polish Academy of Sciences (PL) | Włoczewski M. | - | other affiliation | Bochenek K. | - | IPPT PAN | Jarząbek D. | - | IPPT PAN | Mościcki T. | - | IPPT PAN | Hoffman J. | - | IPPT PAN | Ślawska-Waniewska A. | - | other affiliation |
| 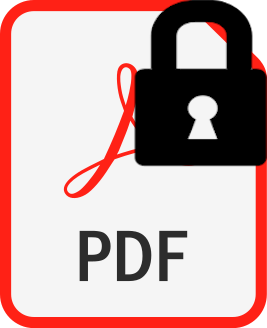 |
11. |
Zakrzewska A., Zargarian S.S., Rinoldi C., Gradys A.D., Jarząbek D.M., Zanoni M.♦, Gualandi C.♦, Lanzi M.♦, Pierini F., Electrospun Poly(vinyl alcohol)-Based Conductive Semi-interpenetrating Polymer Network Fibrous Hydrogel: A Toolbox for Optimal Cross-Linking,
ACS Materials Au, ISSN: 2694-2461, DOI: 10.1021/acsmaterialsau.3c00025, Vol.3, No.5, pp.464-482, 2023 Abstract: Cross-linking of poly(vinyl alcohol) (PVA) creates a three-dimensional network by bonding adjacent polymer chains. The cross-linked structure, upon immersion in water, turns into a hydrogel, which exhibits unique absorption properties due to the presence of hydrophilic groups within the PVA polymer chains and, simultaneously, ceases to be soluble in water. The properties of PVA can be adjusted by chemical modification or blending with other substances, such as polymers, e.g., conductive poly[3-(potassium-5-butanoate)thiophene-2,5-diyl] (P3KBT). In this work, PVA-based conductive semi-interpenetrating polymer networks (semi-IPNs) are successfully fabricated. The systems are obtained as a result of electrospinning of PVA/P3KBT precursor solutions with different polymer concentrations and then cross-linking using “green”, environmentally safe methods. One approach consists of thermal treatment (H), while the second approach combines stabilization with ethanol and heating (E). The comprehensive characterization allows to evaluate the correlation between the cross-linking methods and properties of nanofibrous hydrogels. While both methods are successful, the cross-linking density is higher in the thermally cross-linked samples, resulting in lower conductivity and swelling ratio compared to the E-treated samples. Moreover, the H-cross-linked systems have better mechanical properties─lower stiffness and greater tensile strength. All the tested systems are biocompatible, and interestingly, due to the presence of P3KBT, they show photoresponsivity to solar radiation generated by the simulator. The results indicate that both methods of PVA cross-linking are highly effective and can be applied to a specific system depending on the target, e.g., biomedical or electronic applications. Keywords: poly(vinyl alcohol),poly[3-(potassium-5-butanoate)thiophene-2.5-diyl],electrospun nanofibers,cross-linking,fibrous hydrogel,semi-IPN Affiliations:
Zakrzewska A. | - | IPPT PAN | Zargarian S.S. | - | IPPT PAN | Rinoldi C. | - | IPPT PAN | Gradys A.D. | - | IPPT PAN | Jarząbek D.M. | - | IPPT PAN | Zanoni M. | - | other affiliation | Gualandi C. | - | University of Bologna (IT) | Lanzi M. | - | University of Bologna (IT) | Pierini F. | - | IPPT PAN |
| 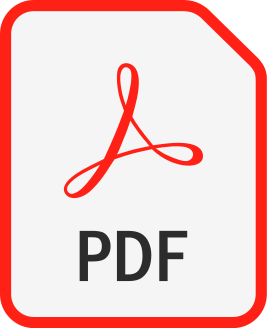 |
12. |
Jenczyk P., Jarząbek D.M., Lu Z.♦, Gadalińska E.♦, Levintant-Zayonts N., Zhang Y.♦, Unexpected crystallographic structure, phase transformation, and hardening behavior in the AlCoCrFeNiTi0.2 high-entropy alloy after high-dose nitrogen ion implantation,
Materials & Design, ISSN: 0264-1275, DOI: 10.1016/j.matdes.2022.110568, Vol.216, pp.110568-1-11, 2022 Abstract: Harsh environments, such as nuclear power plants, require the development of materials with stable properties when exposed to radiation/bombardment conditions. In this work, a bulk high-entropy alloy (HEA) was implanted with nitrogen ions accelerated at 50 kV to induce and study crystal structural defects. X-ray powder diffraction (XRD) showed that the studies HEA consisted of two phases—σ and body-centered cubic (BCC)—and underwent the σ to BCC phase transformation due to ion bombardment. Unexpectedly, XRD peaks of implanted samples could not be assigned to any known simple nitride, a finding that suggests the creation of new high- or medium-entropy ceramics. Studies of the mechanical and tribological properties with the use of nanoindentation and scratch tests revealed a hardening of both phases of the implanted surface and higher wear resistance. There were also surprising increases in the hardness-to-Young’s modulus ratio and elastic recovery for both phases. The results are promising not only for the nuclear applications, but also for space applications, mechanical engineering, and tribology. Keywords: high-entropy alloys, high-entropy ceramics, ion implantation, irradiation, phase transformation Affiliations:
Jenczyk P. | - | IPPT PAN | Jarząbek D.M. | - | IPPT PAN | Lu Z. | - | University of Science and Technology Beijing (CN) | Gadalińska E. | - | Institute of Aviation (PL) | Levintant-Zayonts N. | - | IPPT PAN | Zhang Y. | - | University of Science and Technology Beijing (CN) |
| 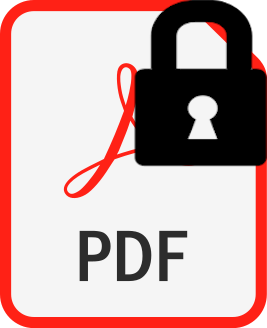 |
13. |
Jóźwiak-Niedźwiedzka D., Dąbrowski M., Dziedzic K., Jarząbek D., Antolik A., Denis P., Glinicki M.A., Effect of gamma irradiation on the mechanical properties of carbonation reaction products in mortar,
MATERIALS AND STRUCTURES, ISSN: 1359-5997, DOI: 10.1617/s11527-022-02003-w, Vol.55, pp.164-1-17, 2022 Abstract: Prediction of carbonation progress in concrete exposed to ionizing radiation is important for the durability assessment of nuclear power plants, eventually needed for operational license extension. The objective of this work is to reveal the influence of gamma irradiation on the carbonation development and resulting microstructural features of cement mortar. The composition of mortar was varied by using mineral additions. Canned specimens at elevated CO2 concentration environment were exposed to gamma irradiation up to the absorbed dose of 1.6 MGy in the vicinity of spent nuclear fuel rods in pool of research reactor. Micromechanical properties of carbonation reaction products were determined using nanoindentation tests. The carbonation depth was found to increase with increasing absorbed γ dose. The size of calcite crystals was about three times greater in irradiated specimens. Gamma irradiation improved the micromechanical properties of carbonation products. Effects of mineral additives on the characteristics of irradiated mortar are discussed. Keywords: calcite, carbonation, cement mortar, gamma irradiation, microstructure, mineral additions, nanoindentation Affiliations:
Jóźwiak-Niedźwiedzka D. | - | IPPT PAN | Dąbrowski M. | - | IPPT PAN | Dziedzic K. | - | IPPT PAN | Jarząbek D. | - | IPPT PAN | Antolik A. | - | IPPT PAN | Denis P. | - | IPPT PAN | Glinicki M.A. | - | IPPT PAN |
| 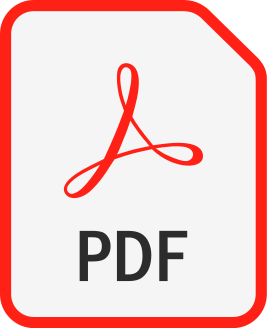 |
14. |
Alvi S.♦, Milczarek M., Jarząbek D.M., Hedman D.♦, Kohan M.G.♦, Levintant-Zayonts N., Vomiero A.♦, Akhtar F.♦, Enhanced mechanical, thermal and electrical properties of high-entropy HfMoNbTaTiVWZr thin film metallic glass and its nitrides,
Advanced Engineering Materials, ISSN: 1438-1656, DOI: 10.1002/adem.202101626, pp.2101626-1-10, 2022 Abstract: The inception of high-entropy alloy promises to push the boundaries for new alloy design with unprecedented properties. This work reports entropy stabilisation of an octonary refractory, HfMoNbTaTiVWZr, high-entropy thin film metallic glass, and derived nitride films. The thin film metallic glass exhibited exceptional ductility of ≈60% strain without fracture and compression strength of 3 GPa in micro-compression, due to the presence of high density and strength of bonds. The thin film metallic glass shows thermal stability up to 750 °C and resistance to Ar-ion irradiation. Nitriding during film deposition of HfMoNbTaTiVWZr thin film of strong nitride forming refractory elements results in deposition of nanocrystalline nitride films with compressive strength, hardness, and thermal stability of up to 10 GPa, 18.7 GPa, and 950 °C, respectively. The high amount of lattice distortion in the nitride films leads to its insulating behaviour with electrical conductivity as low as 200 S cm−1 in the as-deposited film. The design and exceptional properties of the thin film metallic glass and derived nitride films may open up new avenues of development of bulk metallic glasses and the application of refractory-based high entropy thin films in structural and functional applications. Affiliations:
Alvi S. | - | Luleå University of Technology (SE) | Milczarek M. | - | IPPT PAN | Jarząbek D.M. | - | IPPT PAN | Hedman D. | - | Luleå University of Technology (SE) | Kohan M.G. | - | Luleå University of Technology (SE) | Levintant-Zayonts N. | - | IPPT PAN | Vomiero A. | - | Luleå University of Technology (SE) | Akhtar F. | - | Luleå University of Technology (SE) |
| 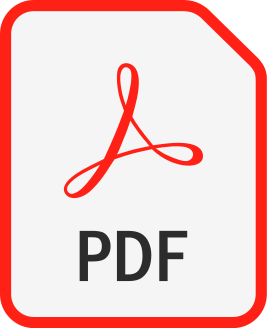 |
15. |
Grzywacz H., Jenczyk P., Milczarek M., Michałowski M.♦, Jarząbek D.M., Burger model as the best option for modeling of viscoelastic behavior of resists for nanoimprint lithography,
Materials, ISSN: 1996-1944, DOI: 10.3390/ma14216639, Vol.14, No.21, pp.6639-1-12, 2021 Abstract: In this study, Atomic Force Microscopy-based nanoindentation (AFM-NI) with diamond-like carbon (DLC) coated tip was used to analyze the mechanical response of poly(methyl methacrylate) (PMMA) thin films (thicknesses: 235 and 513 nm) on a silicon substrate. Then, Oliver and Pharr (OP) model was used to calculate hardness and Young’s modulus, while three different Static Linear Solid models were used to fit the creep curve and measure creep compliance, Young’s modulus, and viscosity. Values were compared with each other, and the best-suited method was suggested. The impact of four temperatures below the glass transition temperature and varied indentation depth on the mechanical properties has been analyzed. The results show high sensitivity on experiment parameters and there is a clear difference between thin and thick film. According to the requirements in the nanoimprint lithography (NIL), the ratio of hardness at demolding temperature to viscosity at molding temperature was introduced as a simple parameter for prediction of resist suitability for NIL. Finally, thinner PMMA film was tentatively attributed as more suitable for NIL. Keywords: PMMA, atomic force microscopy-based nanoindentation, Young’s modulus, hardness, viscosity, Burger creep model, nanoimprint lithography Affiliations:
Grzywacz H. | - | IPPT PAN | Jenczyk P. | - | IPPT PAN | Milczarek M. | - | IPPT PAN | Michałowski M. | - | Warsaw University of Technology (PL) | Jarząbek D.M. | - | IPPT PAN |
| 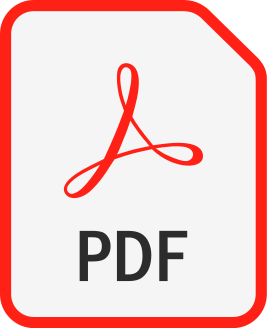 |
16. |
Psiuk R., Milczarek M., Jenczyk P., Denis P., Jarząbek D., Bazarnik P.♦, Pisarek M.♦, Mościcki T., Improved mechanical properties of W-Zr-B coatings deposited by hybrid RF magnetron – PLD method,
APPLIED SURFACE SCIENCE, ISSN: 0169-4332, DOI: 10.1016/j.apsusc.2021.151239, Vol.570, pp.151239-1-11, 2021 Abstract: In this work, novel W-Zr-B coatings were developed by a hybrid process combining pulsed laser deposited ZrB2 and radio frequency magnetron sputtered W2B5. The influence of the laser power density on the structure and mechanical properties of the deposited films was studied. Addition of zirconium causes a change in the structure of the deposited films from columnar to mainly amorphous. The nanoindentation tests and compression of nanopillars showed that doped W-Zr-B layers are still super-hard and incompressible in comparison to WB2 films without doping, but they change their behaviour from brittle to ductile. Films obtained with a fluence of 1.06 J/cm2 are superhard (H = 40 ± 4 GPa) and incompressible (12 ± 1 GPa), but possess a relatively low Young’s modulus (E = 330 ± 32 GPa) and a high elastic recovery (We = 0.9). Further increase in the fluence causes films to consist of deeply embedded fragments of laser ablated ZrB2 target in the deposited layer. Taking into account that the particles are made of ZrB2 which possess extraordinary thermal properties, and the matrix is made of W-Zr-B, a super-hard material, such a composite can also be interesting for industrial applications. Keywords: superhard tungsten borides, hybrid magnetron sputtering – pulsed laser deposition, nanopillar compression Affiliations:
Psiuk R. | - | IPPT PAN | Milczarek M. | - | IPPT PAN | Jenczyk P. | - | IPPT PAN | Denis P. | - | IPPT PAN | Jarząbek D. | - | IPPT PAN | Bazarnik P. | - | Warsaw University of Technology (PL) | Pisarek M. | - | Institute of Physical Chemistry, Polish Academy of Sciences (PL) | Mościcki T. | - | IPPT PAN |
| 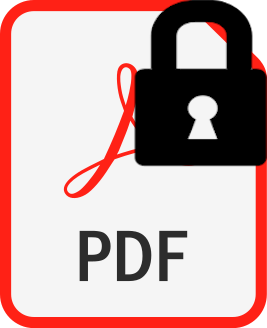 |
17. |
Nosewicz S., Bazarnik P.♦, Clozel M.♦, Kurpaska Ł.♦, Jenczyk P., Jarząbek D., Chmielewski M.♦, Romelczyk-Baishya B.♦, Lewandowska M.♦, Pakieła Z.♦, Huang Y.♦, Langdon T.G.♦, A multiscale experimental analysis of mechanical properties and deformation behavior of sintered copper–silicon carbide composites enhanced by high-pressure torsion,
ARCHIVES OF CIVIL AND MECHANICAL ENGINEERING, ISSN: 1644-9665, DOI: 10.1007/s43452-021-00286-4, Vol.21, pp.131-1-19, 2021 Abstract: Experiments were conducted to investigate, within the framework of a multiscale approach, the mechanical enhancement, deformation and damage behavior of copper–silicon carbide composites (Cu–SiC) fabricated by spark plasma sintering (SPS) and the combination of SPS with high-pressure torsion (HPT). The mechanical properties of the metal–matrix composites were determined at three different length scales corresponding to the macroscopic, micro- and nanoscale. Small punch testing was employed to evaluate the strength of composites at the macroscopic scale. Detailed analysis of microstructure evolution related to SPS and HPT, sample deformation and failure of fractured specimens was conducted using scanning and transmission electron microscopy. A microstructural study revealed changes in the damage behavior for samples processed by HPT and an explanation for this behavior was provided by mechanical testing performed at the micro- and nanoscale. The strength of copper samples and the metal–ceramic interface was determined by microtensile testing and the hardness of each composite component, corresponding to the metal matrix, metal–ceramic interface, and ceramic reinforcement, was measured using nano-indentation. The results confirm the advantageous effect of large plastic deformation on the mechanical properties of Cu–SiC composites and demonstrate the impact on these separate components on the deformation and damage type. Keywords: copper–silicon carbide composite, high-pressure torsion, metal–matrix composites, multiscale analysis, nano-indentation, small punch test Affiliations:
Nosewicz S. | - | IPPT PAN | Bazarnik P. | - | Warsaw University of Technology (PL) | Clozel M. | - | National Centre for Nuclear Research (PL) | Kurpaska Ł. | - | National Centre for Nuclear Research (PL) | Jenczyk P. | - | IPPT PAN | Jarząbek D. | - | IPPT PAN | Chmielewski M. | - | Institute of Electronic Materials Technology (PL) | Romelczyk-Baishya B. | - | Warsaw University of Technology (PL) | Lewandowska M. | - | other affiliation | Pakieła Z. | - | Warsaw University of Technology (PL) | Huang Y. | - | Bournemouth University (GB) | Langdon T.G. | - | University of Southampton (GB) |
| 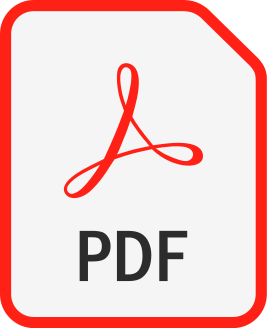 |
18. |
Jenczyk P., Grzywacz H., Milczarek M., Jarząbek D.M.♦, Mechanical and tribological properties of co-electrodeposited particulate-reinforced metal matrix composites: a critical review with interfacial aspects,
Materials, ISSN: 1996-1944, DOI: 10.3390/ma14123181, Vol.14, No.12, pp.3181-1-36, 2021 Abstract: Particulate-reinforced metal matrix composites (PRMMCs) with excellent tribo-mechanical properties are important engineering materials and have attracted constant scientific interest over the years. Among the various fabrication methods used, co-electrodeposition (CED) is valued due to its efficiency, accuracy, and affordability. However, the way this easy-to-perform process is carried out is inconsistent, with researchers using different methods for volume fraction measurement and tribo-mechanical testing, as well as failing to carry out proper interface characterization. The main contribution of this work lies in its determination of the gaps in the tribo-mechanical research of CED PRMMCs. For mechanical properties, hardness is described with respect to measurement methods, models, and experiments concerning CED PRMMCs. The tribology of such composites is described, taking into account the reinforcement volume fraction, size, and composite fabrication route (direct/pulsed current). Interfacial aspects are discussed using experimental direct strength measurements. Each part includes a critical overview, and future prospects are anticipated. This review paper provides an overview of the tribo-mechanical parameters of Ni-based co-electrodeposited particulate-reinforced metal matrix composite coatings with an interfacial viewpoint and a focus on hardness, wear, and friction behavior. Keywords: experimental mechanics, tribology, co-electrodeposited composites Affiliations:
Jenczyk P. | - | IPPT PAN | Grzywacz H. | - | IPPT PAN | Milczarek M. | - | IPPT PAN | Jarząbek D.M. | - | other affiliation |
| 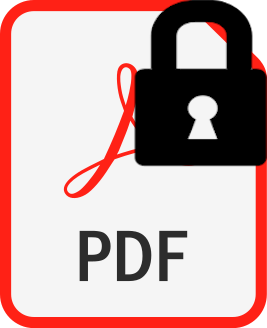 |
19. |
Grzywacz H.♦, Milczarek M., Jenczyk P., Dera W., Michałowski M.♦, Jarząbek D.M.♦, Quantitative measurement of nanofriction between PMMA thin films and various AFM probes,
MEASUREMENT, ISSN: 0263-2241, DOI: 10.1016/j.measurement.2020.108267, Vol.168, pp.108267-1-13, 2020 Abstract: This study reports the quantitative, precise and accurate results of nanoscale friction measurements with the use of an Atomic Force Microscope calibrated with a precise nanoforce sensor. For this purpose, three samples of spin-coated thin Polymethylmethacrylate (PMMA) films were prepared with the following thicknesses: 235, 343, and 513 nm. Three different AFM probes were used for the friction measurements: with diamond-like carbon (DLC) tip with a small (15 nm) or big (2 µm) tip radius, and a reference silicon tip with a small (8 nm) radius. The results show that in all of the studied cases, the coefficient of friction strongly depends on the applied load, being much higher for a lower load. Furthermore, a strong relation of the friction force on the cantilever's geometry, the scanning velocity, and the film thickness was observed. Keywords: lateral force microscopy, friction, thin PMMA films, atomic force microscope, DLC coatings, adhesion Affiliations:
Grzywacz H. | - | other affiliation | Milczarek M. | - | IPPT PAN | Jenczyk P. | - | IPPT PAN | Dera W. | - | IPPT PAN | Michałowski M. | - | Warsaw University of Technology (PL) | Jarząbek D.M. | - | other affiliation |
| 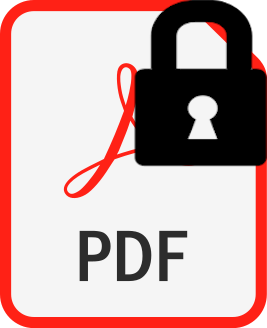 |
20. |
Alvi S.♦, Jarząbek D.M., Kohan M.G.♦, Hedman D.♦, Jenczyk P., Natile M.M.♦, Vomiero A.♦, Akhtar F.♦, Synthesis and mechanical characterization of a CuMoTaWV high-entropy film by magnetron sputtering,
ACS Applied Materials and Interfaces, ISSN: 1944-8244, DOI: 10.1021/acsami.0c02156, Vol.12, No.18, pp.21070-21079, 2020 Abstract: Development of high-entropy alloy (HEA) films is a promising and cost-effective way to incorporate these materials of superior properties in harsh environments. In this work, a refractory high-entropy alloy (RHEA) film of equimolar CuMoTaWV was deposited on silicon and 304 stainless-steel substrates using DC-magnetron sputtering. A sputtering target was developed by partial sintering of an equimolar powder mixture of Cu, Mo, Ta, W, and V using spark plasma sintering. The target was used to sputter a nanocrystalline RHEA film with a thickness of ~900 nm and an average grain size of 18 nm. X-ray diffraction of the film revealed a body-centered cubic solid solution with preferred orientation in the (110) directional plane. The nanocrystalline nature of the RHEA film resulted in a hardness of 19 ± 2.3 GPa and an elastic modulus of 259 ± 19.2 GPa. A high compressive strength of 10 ± 0.8 GPa was obtained in nanopillar compression due to solid solution hardening and grain boundary strengthening. The adhesion between the RHEA film and 304 stainless-steel substrates was increased on annealing. For the wear test against the E52100 alloy steel (Grade 25, 700-880 HV) at 1 N load, the RHEA film showed an average coefficient of friction (COF) and wear rate of 0.25 (RT) and 1.5 (300 °C), and 6.4 × 10^–6 mm^3/N m (RT) and 2.5 × 10^–5 mm^3/N m (300 °C), respectively. The COF was found to be 2 times lower at RT and wear rate 10^2 times lower at RT and 300 °C than those of 304 stainless steel. This study may lead to the processing of high-entropy alloy films for large-scale industrial applications. Keywords: high-entropy alloys, magnetron sputtering, spark plasma sintering, mechanical properties, wear Affiliations:
Alvi S. | - | Luleå University of Technology (SE) | Jarząbek D.M. | - | IPPT PAN | Kohan M.G. | - | Luleå University of Technology (SE) | Hedman D. | - | Luleå University of Technology (SE) | Jenczyk P. | - | IPPT PAN | Natile M.M. | - | other affiliation | Vomiero A. | - | Luleå University of Technology (SE) | Akhtar F. | - | Luleå University of Technology (SE) |
| 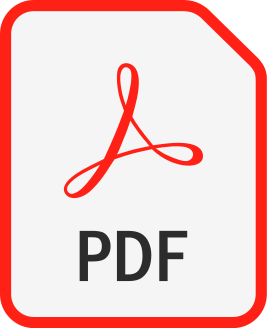 |
21. |
Jarząbek D.M., Milczarek M., Nosewicz S., Bazarnik P.♦, Schift H.♦, Size effects of hardness and strain rate sensitivity in amorphous silicon measured by nanoindentation,
METALLURGICAL AND MATERIALS TRANSACTIONS A-PHYSICAL METALLURGY AND MATERIALS SCIENCE, ISSN: 1073-5623, DOI: 10.1007/s11661-020-05648-w, Vol.51, No.4, pp.1625-1633, 2020 Abstract: In this work, dynamic mechanical properties of amorphous silicon and scale effects were investigated by the means of nanoindentation. An amorphous silicon sample was prepared by plasma-enhanced chemical vapor deposition (PECVD). Next, two sets of the samples were investigated: as-deposited and annealed in 500 °C for 1 hour. A three-sided pyramidal diamond Berkovich's indenter was used for the nanoindentation tests. In order to determine the strain rate sensitivity (SRS), indentations with different loading rates were performed: 0.1, 1, 10, 100 mN/min. Size effects were studied by application of maximum indentation loads in the range from 1 up to 5 mN (penetrating up to approximately one-third of the amorphous layer). The value of hardness was determined by the Oliver-Pharr method. An increase of hardness with decrease of the indentation depth was observed for both samples. Furthermore, the significant dependence of hardness on the strain rate has been reported. Finally, for the annealed samples at low strain rates a characteristic "elbow" during unloading was observed on the force-indentation depth curves. It could be attributed to the transformation of (β-Sn)-Si to the PI (pressure-induced) a-Si end phase. Affiliations:
Jarząbek D.M. | - | IPPT PAN | Milczarek M. | - | IPPT PAN | Nosewicz S. | - | IPPT PAN | Bazarnik P. | - | Warsaw University of Technology (PL) | Schift H. | - | Paul Scherrer Institut (CH) |
| 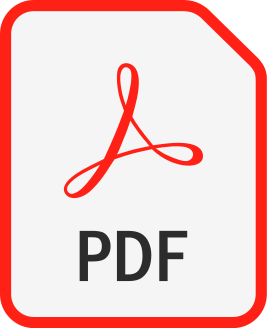 |
22. |
Jarząbek D.M., Harvey C.♦, Levintant-Zayonts N., Wojciechowski T.♦, Gniadek M.♦, Krajewski M., Pathak S.♦, Enhancement of mechanical properties of vertically aligned carbon nanotube arrays due to N+ ion irradiation,
NANOTECHNOLOGY, ISSN: 0957-4484, DOI: 10.1088/1361-6528/ab8665, Vol.31, No.28, pp.285703-1-9, 2020 Abstract: In this work we apply N+ ion irradiation on vertically aligned carbon nanotube (VACNT) arrays in order to increase the number of connections and joints in the CNT network. The ions energy was 50 keV and fluence 5 × 10^17 ions cm^−2. The film was 160 μm thick. SEM images revealed the ion irradiation altered the carbon bonding and created a sponge-like, brittle structure at the surface of the film, with the ion irradiation damage region extending ~4 μm in depth. TEM images showed the brittle structure consists of amorphous carbon forming between nanotubes. The significant enhancement of mechanical properties of the irradiated sample studied by the cyclic nanoindentation with a flat punch indenter was observed. Irradiation on the VACNT film made the structure stiffer, resulted in a higher percentage recovery, and reduced the energy dissipation under compression. The results are encouraging for further studies which will lead to create a class of materials - ion-irradiated VACNT films - which after further research may find application in storage or harvesting energy at the micro/nanoscale. Keywords: vertically aligned carbon nanotubes, ion irradiation, nanoindentation Affiliations:
Jarząbek D.M. | - | IPPT PAN | Harvey C. | - | University of Nevada (US) | Levintant-Zayonts N. | - | IPPT PAN | Wojciechowski T. | - | Institute of Physics, Polish Academy of Sciences (PL) | Gniadek M. | - | University of Warsaw (PL) | Krajewski M. | - | IPPT PAN | Pathak S. | - | University of Nevada (US) |
| 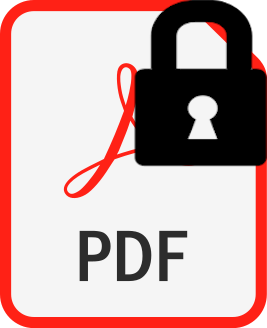 |
23. |
Nosewicz S., Romelczyk-Baishya B.♦, Lumelskyj D., Chmielewski M.♦, Bazarnik P.♦, Jarząbek D.M., Pietrzak K., Kaszyca K.♦, Pakieła Z.♦, Experimental and numerical studies of micro- and macromechanical properties of modified copper–silicon carbide composites,
INTERNATIONAL JOURNAL OF SOLIDS AND STRUCTURES, ISSN: 0020-7683, DOI: 10.1016/j.ijsolstr.2018.10.025, Vol.160, pp.187-200, 2019 Abstract: The presented research investigation comprises the study of the mechanical properties of modified copper–silicon carbide composites at the micro- and macroscopic scale. The improvement of a copper–silicon carbide composite refers to the addition of a protective layer at the ceramic reinforcement in order to prevent the dissolution of silicon in the copper matrix. The macromechanical behaviour has been evaluated by the performance in a small punch test. The investigation has been carried out with samples with varying volume content of ceramic reinforcement and different protective layers of the silicon carbide particles. Moreover, the influence of temperature during the strength test has been studied. Next, the results have been referred to the interfacial bonding strength of Cu and SiC particles. SEM characterization of samples has been performed to link the composites' microstructure with the mechanical behaviour. Finally, the experimental results of the small punch test have been predicted via a numerical approach. Finite element analysis has been employed to reproduce the response of the composite specimen during the test. Satisfactory agreement with the experimental curve has been obtained. Keywords: metal matrix composites, silicon carbide, metallic layers deposition, small punch, interface strength, finite element method Affiliations:
Nosewicz S. | - | IPPT PAN | Romelczyk-Baishya B. | - | Warsaw University of Technology (PL) | Lumelskyj D. | - | IPPT PAN | Chmielewski M. | - | Institute of Electronic Materials Technology (PL) | Bazarnik P. | - | Warsaw University of Technology (PL) | Jarząbek D.M. | - | IPPT PAN | Pietrzak K. | - | IPPT PAN | Kaszyca K. | - | Lukasiewicz Institute of Microelectronics and Photonics (PL) | Pakieła Z. | - | Warsaw University of Technology (PL) |
| 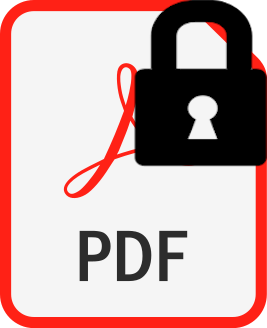 |
24. |
Jenczyk P., Gawrońska M.♦, Dera W., Chrzanowska-Giżyńska J., Denis P., Jarząbek D.M., Application of SiC particles coated with a protective Ni layer for production of Ni/SiC co-electrodeposited composite coatings with enhanced tribological properties,
CERAMICS INTERNATIONAL, ISSN: 0272-8842, DOI: 10.1016/j.ceramint.2019.08.063, Vol.45, No.17B, pp.23540-23547, 2019 Abstract: In this paper, the mechanical properties of composites consisting of electroplated Ni and co-electrodeposited SiC particles, coated with a thin protective layer of Ni, were studied. The protective layer was on the SiC particles prior to adding them to the electrolyte bath. It was demonstrated that due to the application of the protective layer it was possible to decrease sliding friction force, and improve the wear resistance, of the composite coatings in comparison with standard electroplated composite coatings made of Ni and co-electrodeposited pure SiC particles. Coating SiC particles with Ni was achieved by means of a PVD process. The main advantage of this step is avoiding oxidation of the surface of the particles during the contact with an electrolyte. Particles protected from oxidation lead to stronger interfacial bonding between the matrix and the reinforcement. Furthermore, better bonding protects the SiC particles from being extracted from the matrix by a counter-probe during friction and wear tests. The influence of the particle's concentration is studied. A smaller friction force and constant wear rate was observed. Keywords: wear, friction, interfacial bonding strength, metal matrix composites, silicon carbide, electrodeposited nickel Affiliations:
Jenczyk P. | - | IPPT PAN | Gawrońska M. | - | Warsaw University of Technology (PL) | Dera W. | - | IPPT PAN | Chrzanowska-Giżyńska J. | - | IPPT PAN | Denis P. | - | IPPT PAN | Jarząbek D.M. | - | IPPT PAN |
| 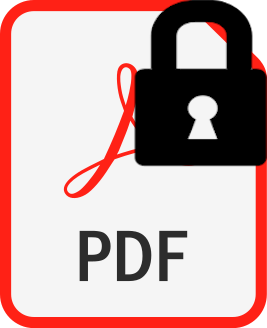 |
25. |
Jarząbek D.M., Dziekoński C., Dera W., Chrzanowska J., Wojciechowski T.♦, Influence of Cu coating of SiC particles on mechanical properties of Ni/SiC co-electrodeposited composites,
CERAMICS INTERNATIONAL, ISSN: 0272-8842, DOI: 10.1016/j.ceramint.2018.08.271, Vol.44, pp.21750-21758, 2018 Abstract: In this paper, the study of the mechanical properties of composites consisting of electrodeposited Ni and co-electrodeposited SiC particles coated with a thin Cu layer was presented. It was demonstrated that the coating allowed to increase the concentration of ceramic particles in the composite. Although the plating parameters were the same for both types of composites, the concentration of SiC was 15% for the composite containing coated particles (Ni/SiC-Cu) and 10% for the composite containing uncoated particles (Ni/SiC). Furthermore, tensile tests showed that the Ni/SiC-Cu samples exhibited higher Young's modulus than the pure electrodeposited Ni samples or Ni/SiC samples. The measured Young's modulus of the Ni/SiC-Cu composite was 250 ± 10 GPa. However, the ultimate tensile strength of the Ni/SiC-Cu composite was lower than that of pure Ni. To explain the mechanical behaviour of the Ni/SiC-Cu composite, the microstructure of the interface of this composite and its bonding strength were studied. Microstructure studies conducted using a scanning electron microscope (SEM) revealed that the SiC/Cu interface was smooth and of good quality whereas the Cu/Ni interface was rough but also of good quality. The measured bonding, normal, and shear strength values demonstrated that the SiC/Cu interface was weak, and that was the main reason for the low ultimate tensile strength of the composite. The shear strength of the SiC/Cu interface was measured using a novel method: micropillars shearing including atomic force microscopy (AFM). Finally, a simple finite element model of the Ni/SiC-Cu composite, based on cohesive elements, was developed. Keywords: Interfacial bonding strength, Metal matrix composites, Tensile strength, Silicon carbide, Electrodeposited nickel Affiliations:
Jarząbek D.M. | - | IPPT PAN | Dziekoński C. | - | IPPT PAN | Dera W. | - | IPPT PAN | Chrzanowska J. | - | IPPT PAN | Wojciechowski T. | - | Institute of Physics, Polish Academy of Sciences (PL) |
| 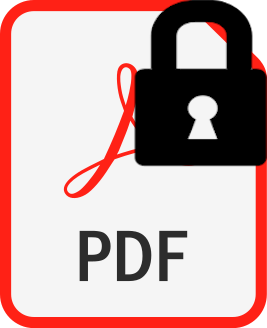 |
26. |
Jarząbek D.M., The impact of weak interfacial bonding strength on mechanical properties of metal matrix - ceramic reinforced composites,
COMPOSITE STRUCTURES, ISSN: 0263-8223, DOI: 10.1016/j.compstruct.2018.06.071, Vol.201, pp.352-362, 2018 Abstract: In this work the influence of weak interface between particles and matrix on mechanical properties of metal matrix – ceramic reinforced composites is studied. Firstly, the samples made of coelectrodeposited Ni-SiC composites with 10% of SiC with poor interface bonding have been prepared. Furthermore, the tensile tests of samples have been performed. The determined Young's modulus was equal to 67 ± 8 GPa and the ultimate tensile strength to 230 ± 15 MPa. It is assumed that the very weak interface is the reason for the poor mechanical properties of the created material. In order to confirm the assumption and get the necessary parameters for the numerical model, the measurements of the normal and shear interfacial bonding strength of the interface have been performed. The measured normal interfacial bonding strength is equal to 0.1 ± 0.03 MPa and the interfacial shear strength is equal to 4.9 ± 0.2 MPa. The experimental results have been confirmed qualitatively by the computer simulations. Representative Volume Element has been created and modelled by the Finite Element Method with cohesive zone elements. The computer simulations result in the Young's modulus values from 119 GPa up to 126 GPa. Keywords: Interfacial bonding strength, Metal matrix composites, Tensile strength, Silicon carbide, Electrodeposited nickel, Cohesive elements Affiliations:
| 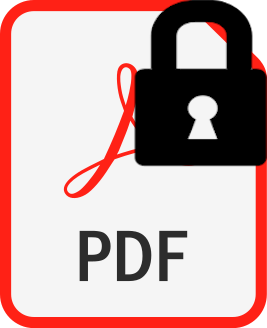 |
27. |
Frąś L.J., Dziekoński C., Dera W., Jarząbek D.M., Piezoelectric bimorph as a high-sensitivity viscosity resonant sensor to test the anisotropy of magnetorheological fluid,
REVIEW OF SCIENTIFIC INSTRUMENTS, ISSN: 0034-6748, DOI: 10.1063/1.5025123, Vol.89, No.10, pp.105111-1-7, 2018 Abstract: In this paper, we present a device which is very sensitive for small changes in the viscosity of the investigated fluid. The main part of the device is a piezo-electric bimorph which consists of the brass shim with two piezo-ceramic layers on the opposite sides. One of them is responsible for generating vibrations, whereas the second one is meant to measure system response which is produced by the damping properties of the surrounding fluid. During the experiment, the cylindrical bar is forced to move by the series of sinusoidal waves with different frequencies and at constant amplitudes. The probe is immersed in the fluid and then the amplitude vs frequency and phase vs frequency curves are obtained. Next, one can determine the viscosity according to a proper mathematical model. The resonant frequency is related to the damping coefficient which depends on the viscosity of the surrender fluid and immersion depth of the probe. The coefficients necessary for calculating viscosity are obtained by fitting the resonance curve to the amplitude vs frequency data obtained from the experiment. The device has been applied to study the anisotropy of magnetorheological fluids. The weak anisotropy of viscosity has been observed. The highest value of viscosity was observed in the case of viscosity measurement in the direction orthogonal to the magnetic field and the lowest in the direction parallel to the magnetic field. Affiliations:
Frąś L.J. | - | IPPT PAN | Dziekoński C. | - | IPPT PAN | Dera W. | - | IPPT PAN | Jarząbek D.M. | - | IPPT PAN |
| 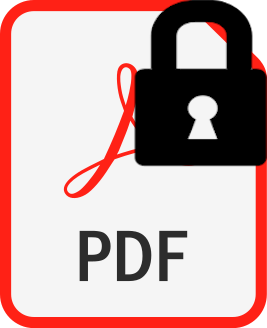 |
28. |
Jarząbek D.M., Gwiazda M.♦, Dera W., The Influence of Alkali Metal Chloride Treatments on the Wear Resistance of Silicon Surfaces for Possible Use in MEMS,
TRIBOLOGY TRANSACTIONS, ISSN: 1040-2004, DOI: 10.1080/10402004.2017.1296211, Vol.61, No.1, pp.178-184, 2018 Abstract: The wear of contacting silicon surfaces in microelectromechanical systems (MEMS) has been a longstanding concern. To address this issue, the effects of immersing silicon surfaces into alkali metal chloride solutions (LiCl, NaCl, CsCl) on their sliding friction and wear were investigated. A custom-built reciprocating tribometer was used with a sapphire ball as the counterbody. Results indicated that the friction coefficient between the silicon surface (p-doped, orientation (100)) and a sapphire ball can be reduced by up to 30% by treating the silicon surfaces in aqueous salt solutions (concentration 1 mol/L, exposure for 24 h). These modified surfaces also have higher wear resistance and a significant change in wettability. After immersion, the contact angle between the silicon surface and water was reduced by approximately 50%. These results may lead to new, simple, and inexpensive methods to increase the wear resistance of silicon surfaces for use in MEMs devices. Keywords: silicon surface, wear, friction, alkali metal chlorides Affiliations:
Jarząbek D.M. | - | IPPT PAN | Gwiazda M. | - | Warsaw University of Technology (PL) | Dera W. | - | IPPT PAN |
| 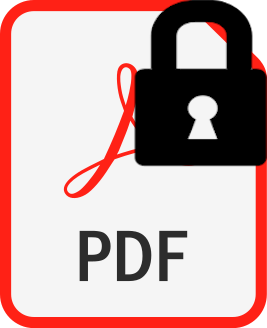 |
29. |
Strojny-Nędza A.♦, Pietrzak K.♦, Gładki A.♦, Nosewicz S., Jarząbek D.M., Chmielewski M.♦, The effect of ceramic type reinforcement on structure and properties of Cu-Al2O3 composites,
BULLETIN OF THE POLISH ACADEMY OF SCIENCES: TECHNICAL SCIENCES, ISSN: 0239-7528, DOI: 10.24425/124271, Vol.66, No.4, pp.553-560, 2018 Abstract: The purpose of this paper is to elaborate on mechanical alloying conditions for a composite powder consisting of copper and brittle aluminium oxides. Detailed analysis of the Cu-Al2O3 powder mixture structure obtained in the mechanical alloying process allows for the study of the homogenization phenomena and for obtaining grains (in composite form) with a high degree of uniformity. The Cu-5 vol.%Al2O3 composites were obtained by means of the spark plasma sintering technique. The results presented herein were studied and discussed interms of the impact of using a different form of aluminium oxide powder and a different shape of copper powder on composite properties. Research methodology included microstructure analysis as well as its relation to the strength of Cu-Al2O3 interfaces. It transpires from the results presented below that the application of electrocor undum as a reinforcement phase in composites decreases poro sity in the ceramic phase, thus improving thermal properties and interfacial strength. Keywords: metal matrix composites, spark plasma sintering, thermal conductivity, interfacial strength Affiliations:
Strojny-Nędza A. | - | Institute of Electronic Materials Technology (PL) | Pietrzak K. | - | other affiliation | Gładki A. | - | Institute of Electronic Materials Technology (PL) | Nosewicz S. | - | IPPT PAN | Jarząbek D.M. | - | IPPT PAN | Chmielewski M. | - | Institute of Electronic Materials Technology (PL) |
| 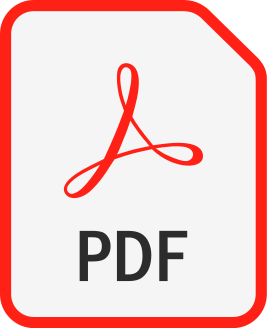 |
30. |
Dziekoński C.♦, Dera W., Jarząbek D.M., Method for lateral force calibration in atomic force microscope using MEMS microforce sensor,
ULTRAMICROSCOPY, ISSN: 0304-3991, DOI: 10.1016/j.ultramic.2017.06.012, Vol.182, pp.1-9, 2017 Abstract: In this paper we present a simple and direct method for the lateral force calibration constant determination. Our procedure does not require any knowledge about material or geometrical parameters of an investigated cantilever. We apply a commercially available microforce sensor with advanced electronics for direct measurement of the friction force applied by the cantilever's tip to a flat surface of the microforce sensor measuring beam. Due to the third law of dynamics, the friction force of the equal value tilts the AFM cantilever. Therefore, torsional (lateral force) signal is compared with the signal from the microforce sensor and the lateral force calibration constant is determined. The method is easy to perform and could be widely used for the lateral force calibration constant determination in many types of atomic force microscopes. Keywords: A precise and direct method for lateral force calibration, Inaccuracy equal to approximately 2%, Wedge method is proven to give inaccurate results Affiliations:
Dziekoński C. | - | other affiliation | Dera W. | - | IPPT PAN | Jarząbek D.M. | - | IPPT PAN |
| 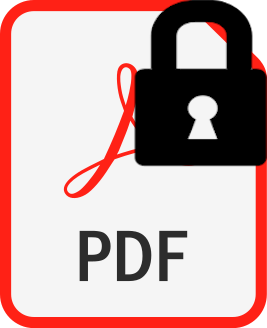 |
31. |
Jarząbek D.M., Milczarek M.♦, Wojciechowski T.♦, Dziekoński C., Chmielewski M.♦, The effect of metal coatings on the interfacial bonding strength of ceramics to copper in sintered Cu-SiC composites,
CERAMICS INTERNATIONAL, ISSN: 0272-8842, DOI: 10.1016/j.ceramint.2017.01.056, Vol.43, No.6, pp.5283-5291, 2017 Abstract: Cu-SiC composites are very promising materials which have high thermal and electrical conductivity and may find many applications. Unfortunately, the main disadvantage of these materials is the dissolution of silicon in copper at elevated temperature, which significantly reduces their properties. In order to overcome this problem particles can be coated with a protective material before sintering. In this paper– the influence of three different metallic coatings on bonding strength were investigated. SiC particles were coated with tungsten, chromium or titanium. As reference a material with uncoated particles was prepared. The experiments were carried out with the use of microtensile tester. The highest increase in strength was observed in the case of chromium coating. On the other hand, the titanium coating, which was of very poor quality, decrease the bonding strength in comparison with uncoated particles. Furthermore, scanning electron and optical microscopes were used to determine the mechanism of debonding. Keywords: interfacial bonding strength, metal matrix composites, tensile strength, silicon carbide particles Affiliations:
Jarząbek D.M. | - | IPPT PAN | Milczarek M. | - | other affiliation | Wojciechowski T. | - | Institute of Physics, Polish Academy of Sciences (PL) | Dziekoński C. | - | IPPT PAN | Chmielewski M. | - | Institute of Electronic Materials Technology (PL) |
| 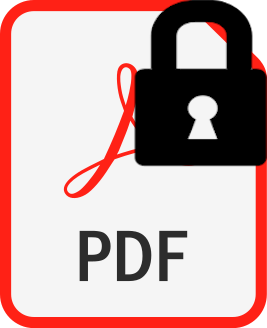 |
32. |
Chmielewski M.♦, Pietrzak K.♦, Teodorczyk M.♦, Nosewicz S., Jarząbek D.M., Zybała R.♦, Bazarnik P.♦, Lewandowska M.♦, Strojny-Nędza A.♦, Effect of metallic coating on the properties of copper-silicon carbide composites,
APPLIED SURFACE SCIENCE, ISSN: 0169-4332, DOI: 10.1016/j.apsusc.2016.12.130, Vol.421, pp.159-169, 2017 Abstract: In the presented paper a coating of SiC particles with a metallic layer were used to prepare copper matrix composite materials. The role of the layer was to protect the silicon carbide from decomposition and dissolution of silicon in the copper matrix during the sintering process. The SiC particles were covered by chromium, tungsten and titanium using Plasma Vapour Deposition method. After powder mixing of components, the final densification process via Spark Plasma Sintering (SPS) method at temperature 950C was provided. The almost fully dense materials were obtained (> 97.5%). The microstructure of obtained composites was studied using scanning electron microscopy as well as transmission electron microscopy. The microstructural analysis of composites confirmed that regardless of the type of deposited material, there is no evidence for decomposition process of silicon carbide in copper. In order to measure the strength of the interface between ceramic particles and the metal matrix, the micro tensile tests have been performed. Furthermore, thermal diffusivity was measured with the use of the laser pulse technique. In the context of performed studies, the tungsten coating seems to be the most promising solution for heat sink application. Compared to pure composites without metallic layer, Cu-SiC with W coating indicate the higher tensile strength and thermal diffusitivy, irrespective of an amount of SiC reinforcement. The improvement of the composite properties is related to advantageous condition of Cu-SiC interface characterized by well homogenity and low porosity, as well as individual properties of the tungsten coating material. Keywords: metal matrix composites, silicon carbide, metallic layers deposition, thermal conductovity, interface strength Affiliations:
Chmielewski M. | - | Institute of Electronic Materials Technology (PL) | Pietrzak K. | - | other affiliation | Teodorczyk M. | - | Institute of Electronic Materials Technology (PL) | Nosewicz S. | - | IPPT PAN | Jarząbek D.M. | - | IPPT PAN | Zybała R. | - | Warsaw University of Technology (PL) | Bazarnik P. | - | Warsaw University of Technology (PL) | Lewandowska M. | - | other affiliation | Strojny-Nędza A. | - | Institute of Electronic Materials Technology (PL) |
| 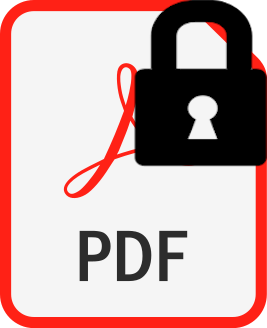 |
33. |
Chmielewski M.♦, Pietrzak K.♦, Strojny-Nędza A.♦, Jarząbek D.M., Nosewicz S., Investigations of interface properties in copper-silicon carbide composites,
ARCHIVES OF METALLURGY AND MATERIALS, ISSN: 1733-3490, DOI: 10.1515/amm-2017-0200, Vol.62, No.2B, pp.1315-1318, 2017 Abstract: This paper analyses the technological aspects of the interface formation in the copper-silicon carbide composite and its effect on the material's microstructure and properties. Cu-SiC composites with two different volume content of ceramic reinforcement were fabricated by hot pressing (HP) and spark plasma sintering (SPS) technique. In order to protect SiC surface from its decomposition, the powder was coated with a thin tungsten layer using plasma vapour deposition (PVD) method. Microstructural analyses provided by scanning electron microscopy revealed the significant differences at metal-ceramic interface. Adhesion force and fracture strength of the interface between SiC particles and copper matrix were measured. Thermal conductivity of composites was determined using laser flash method. The obtained results are discussed with reference to changes in the area of metal-ceramic boundary. Keywords: copper matrix composites, silicon carbide, interface, thermal conductivity, adhesion Affiliations:
Chmielewski M. | - | Institute of Electronic Materials Technology (PL) | Pietrzak K. | - | other affiliation | Strojny-Nędza A. | - | Institute of Electronic Materials Technology (PL) | Jarząbek D.M. | - | IPPT PAN | Nosewicz S. | - | IPPT PAN |
| 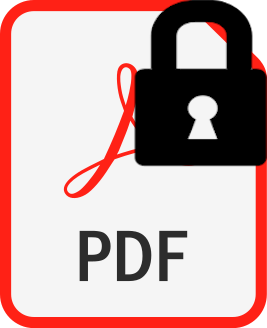 |
34. |
Kucharski S., Jarząbek D.M., Piątkowska A.♦, Woźniacka S., Decrease of Nano-hardness at Ultra-low Indentation Depths in Copper Single Crystal,
EXPERIMENTAL MECHANICS, ISSN: 0014-4851, DOI: 10.1007/s11340-015-0105-2, Vol.56, No.3, pp.381-393, 2016 Abstract: In the present study, we report a detailed investigation of the unusual size effect in single crystals. For the experiments we specified the hardness in single crystalline copper specimens with different orientations ((001), (011) and (111)) using Oliver-Pharr method. Our results indicates that with decreasing load, after the value of the hardness reached its maximum, it starts to decrease for very small indentation depths (<150 nm). For the sake of accuracy of hardness determination we have developed two AFM-based methods to evaluate contact area between tip and indented material. The proposed exact measurement of the contact area, which includes the effect of pile-up and sink-in patterns, can partially explain the strange behaviour, however, the decrease of hardness at low loads is still observed. At higher loads range the specified hardness is practically constant. Keywords: Copper, Single crystal, Nanoindentation, AFM, Size effect Affiliations:
Kucharski S. | - | IPPT PAN | Jarząbek D.M. | - | IPPT PAN | Piątkowska A. | - | Institute of Electronic Materials Technology (PL) | Woźniacka S. | - | IPPT PAN |
| 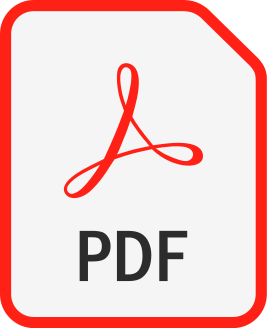 |
35. |
Jarząbek D.M., Chmielewski M.♦, Dulnik J., Strojny-Nędza A.♦, The Influence of the Particle Size on the Adhesion Between Ceramic Particles and Metal Matrix in MMC Composites,
Journal of Materials Engineering and Performance, ISSN: 1059-9495, DOI: 10.1007/s11665-016-2107-3, Vol.25, No.8, pp.3139-3145, 2016 Abstract: This study investigated the influence of the particle size on the adhesion force between ceramic particles and metal matrix in ceramic-reinforced metal matrix composites. The Cu-Al2O3 composites with 5 vol.% of ceramic phase were prepared by a powder metallurgy process. Alumina oxide powder as an electrocorundum (Al2O3) powder with different particle sizes, i.e., fine powder <3 µm and coarse powder of 180 µm was used as a reinforcement. Microstructural investigations included analyses using scanning electron microscopy with an integrated EDS microanalysis system and transmission microscopy. In order to measure the adhesion force (interface strength), we prepared the microwires made of the investigated materials and carried out the experiments with the use of the self-made tensile tester. We have observed that the interface strength is higher for the sample with coarse particles and is equal to 74 ± 4 MPa and it is equal to 68 ± 3 MPa for the sample with fine ceramic particles. Keywords: adhesion, interface strength, metal matrix composites, nanocomposites, tensile test Affiliations:
Jarząbek D.M. | - | IPPT PAN | Chmielewski M. | - | Institute of Electronic Materials Technology (PL) | Dulnik J. | - | IPPT PAN | Strojny-Nędza A. | - | Institute of Electronic Materials Technology (PL) |
| 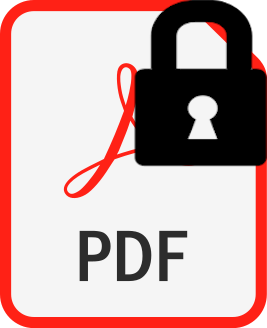 |
36. |
Jarząbek D.M., Chmielewski M.♦, Wojciechowski T.♦, The measurement of the adhesion force between ceramic particles and metal matrix in ceramic reinforced-metal matrix composites,
COMPOSITES PART A-APPLIED SCIENCE AND MANUFACTURING, ISSN: 1359-835X, DOI: 10.1016/j.compositesa.2015.05.025, Vol.76, pp.124-130, 2015 Abstract: This paper presents the method for measurement of the adhesion force and fracture strength of the interface between ceramic particles and metal matrix in ceramic reinforced-metal matrix composites. Three samples with the following Cu to Al2O3 ratio (in vol.%) were prepared: 98.0Cu/2.0Al2O3, 95.0Cu/5.0Al2O3 and 90Cu/10Al2O3. Furthermore, microwires which contain a few ceramic particles were produced by means of electro etching. The microwires with clearly exposed interface were tested with use of the microtensile tester. The microwires usually break exactly at the interface between the metal matrix and ceramic particle. The force and the interface area were carefully measured and then the fracture strength of the interface was determined. The strength of the interface between ceramic particle and metal matrix was equal to 59 ± 8 MPa and 59 ± 11 MPa in the case of 2% and 5% Al2O3 to Cu ratio, respectively. On the other hand, it was significantly lower (38 ± 5 MPa) for the wires made of composite with 10% Al2O3. Keywords: Nanocomposites, Metal matrix composites, Adhesion, Interface Affiliations:
Jarząbek D.M. | - | IPPT PAN | Chmielewski M. | - | Institute of Electronic Materials Technology (PL) | Wojciechowski T. | - | Institute of Physics, Polish Academy of Sciences (PL) |
| 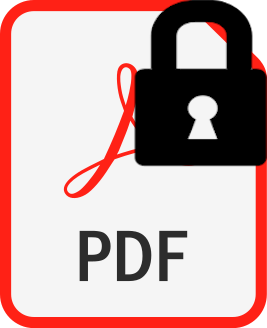 |
37. |
Jarząbek D.M., Siewert D.♦, Fabianowski W.♦, Schift H.♦, Rymuza Z.♦, Jung T.♦, Influence of Alkali Ions on Tribological Properties of Silicon Surface,
TRIBOLOGY LETTERS, ISSN: 1023-8883, DOI: 10.1007/s11249-015-0603-5, Vol.60, No.2, pp.1-8, 2015 Abstract: Tribological properties of surfaces (friction, adhesion and wear) provide challenging limitations to the design of reliable machines on the micro- and nanometer scale as the surface to volume area increases and volume, mass and inertia of the mobile parts decrease. This study reports on the reduction in the friction force of silicon surfaces after the alkali metal ion exposure in the form of aqueous solutions. A scanning force microscope equipped with a liquid cell was used to investigate the friction force and the pull-off force of a flat silicon surface immersed in water and in different alkali metal chlorides solutions: LiCl, NaCl and CsCl. The concentration ranged from 0.1 up to 1000 µmol/l. The changes in the free surface energy of the initial surface and of the modified surfaces after drying were determined from contact angle measurements and from the acid–base adhesion theory. In both cases, in the liquid environment and after drying of the exposed silicon substrates in air, the friction force is reduced by approximately 50 %. Our results provide new, fundamental insight into the exchange of surface termination layers in particular for tribology. Also it is suggested to use the procedure as a low-cost alternative to improve the tribological properties of the silicon surface in particular in applications where lubricating fluids are not appropriate, e.g., in nanomachines and devices. Keywords: Silicon surface, Scanning force microscopy, Friction, Adhesion, Alkali metal chlorides Affiliations:
Jarząbek D.M. | - | IPPT PAN | Siewert D. | - | Paul Scherrer Institut (CH) | Fabianowski W. | - | Paul Scherrer Institut (CH) | Schift H. | - | Paul Scherrer Institut (CH) | Rymuza Z. | - | other affiliation | Jung T. | - | Paul Scherrer Institut (CH) |
| 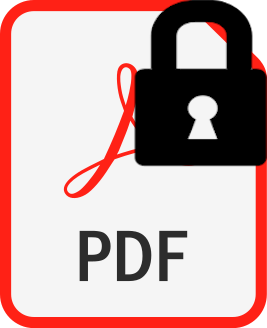 |
38. |
Jarząbek D.M., Precise and direct method for the measurement of the torsion spring constant of the atomic force microscopy cantilevers,
REVIEW OF SCIENTIFIC INSTRUMENTS, ISSN: 0034-6748, DOI: 10.1063/1.4904866, Vol.86, pp.013701-1-6, 2015 Abstract: A direct method for the evaluation of the torsional spring constants of the atomic force microscope cantilevers is presented in this paper. The method uses a nanoindenter to apply forces at the long axis of the cantilever and in the certain distance from it. The torque vs torsion relation is then evaluated by the comparison of the results of the indentations experiments at different positions on the cantilever. Next, this relation is used for the precise determination of the torsional spring constant of the cantilever. The statistical analysis shows that the standard deviation of the calibration measurements is equal to approximately 1%. Furthermore, a simple method for calibration of the photodetector’s lateral response is proposed. The overall procedure of the lateral calibration constant determination has the accuracy approximately equal to 10%. Keywords: Calibration, Atomic force microscopy, Nanotechnology, Hardness, Diffraction gratings Affiliations:
| 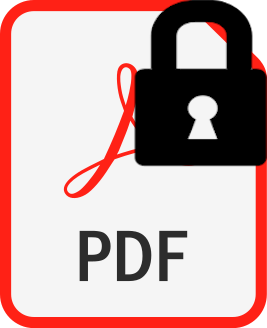 |
39. |
Kucharski S., Jarząbek D.M., Depth Dependence of Nanoindentation Pile-Up Patterns in Copper Single Crystals,
METALLURGICAL AND MATERIALS TRANSACTIONS A-PHYSICAL METALLURGY AND MATERIALS SCIENCE, ISSN: 1073-5623, DOI: 10.1007/s11661-014-2437-4, Vol.45A, pp.4997-5008, 2014 Abstract: A study of the dependence of nanoindentation pile-up patterns on the indentation load and crystallographic orientation is presented. Three different orientations—(001), (011), and (111)—of single crystal copper were investigated. Experiments were conducted on a CSM ultra-nanoindentation tester using a Berkovich tip. The topographic images were obtained using an atomic force microscope. The evolution of pile-up patterns with different applied loads was observed. The results show that for applied loads equal to 0.45 mN and smaller the pile-up patterns do not depend on the crystallographic orientation of the indented surface; instead, they depend on the tip’s geometry. On the other hand, in the case of indentation loads bigger than 2 mN, pile-up patterns on the surfaces of (001)-, (011)-, and (111)-oriented single crystals have fourfold, twofold, and sixfold (or threefold) symmetry, respectively. An intermediate state was also reported. Furthermore, a detailed analysis of residual impressions with maximal applied loads equal to 2 mN and bigger reveals that both pile-up and sink-in patterns are present. Affiliations:
Kucharski S. | - | IPPT PAN | Jarząbek D.M. | - | IPPT PAN |
| 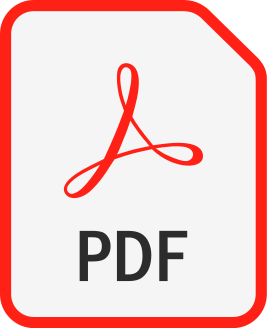 |
40. |
Jarząbek D.M., Kaufmann A.N.♦, Schift H.♦, Rymuza Z.♦, Jung T.A.♦, Elastic modulus and fracture strength evaluation on the nanoscale by scanning force microscope experiments,
NANOTECHNOLOGY, ISSN: 0957-4484, DOI: 10.1088/0957-4484/25/21/215701, Vol.25, pp.215701-1-9, 2014 Abstract: This work first reviews the capability of scanning force microscopy (SFM) to perform experiments with forces in a wide range, from low non-contact forces to high contact forces which induce mechanical deformations in the substrate. In analogy to fracture strength evaluation, as established in materials science, SFM is used to exert forces on pillars with nanometer dimensions while the cantilever deformations are monitored quantitatively. Hence, it is possible to bend the pillars until the threshold for triggering fracture is reached, and to determine the mechanical properties at the different stages of this process. Using this novel approach, in combination with 'state of the art' nanofabrication to produce nanopillar arrays on silicon and silicon dioxide substrates, a number of experiments are performed. Furthermore, quantitative measurements of the fracture strength of Si and of the SiO2/Si interface and E-modulus are presented. To analyze the experimental data obtained in the different experimental procedures and modes, finite element method calculations were used. The methods introduced herein provide a versatile toolbox for addressing a wide range of scientific problems and for applications in materials science and technology. Affiliations:
Jarząbek D.M. | - | IPPT PAN | Kaufmann A.N. | - | Paul Scherrer Institut (CH) | Schift H. | - | Paul Scherrer Institut (CH) | Rymuza Z. | - | other affiliation | Jung T.A. | - | Paul Scherrer Institut (CH) |
| 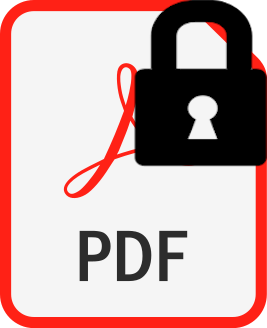 |
41. |
Abetkovskaya S.O.♦, Chizhik S.A.♦, Pogoskaya I.V.♦, Rimuza Z.♦, Jarząbek D.M.♦, Mikhalovski M.♦, Linke Ya.♦, Determining the Young Modulus of Nanosize Thickness Coatings for MEMS from the Results of Static Force Spectroscopy,
Bulletin of the Russian Academy of Sciences: Physics, ISSN: 1062-8738, DOI: 10.3103/S1062873812090031, Vol.76, No.9, pp.1009-1011, 2012 Abstract: A method for the nanoidentation of resistance coatings 1–100 nm thick and intended for use in microelectromechanical systems is proposed on the basis of atomic-force microscopy (AFM). The elastic moduli of the coatings are determined using three models of contact: the Hertz model, the Johnson–Kendall–Roberts model and the Makushkin model, with and without allowance for the influence of a solid substrate Affiliations:
Abetkovskaya S.O. | - | A.V. Lykov Heat and Mass Transfer Institute National Academy of Sciences of Belarus (BY) | Chizhik S.A. | - | A.V. Lykov Heat and Mass Transfer Institute National Academy of Sciences of Belarus (BY) | Pogoskaya I.V. | - | A.V. Lykov Heat and Mass Transfer Institute National Academy of Sciences of Belarus (BY) | Rimuza Z. | - | Warsaw University of Technology (PL) | Jarząbek D.M. | - | other affiliation | Mikhalovski M. | - | other affiliation | Linke Ya. | - | Warsaw University of Technology (PL) |
| 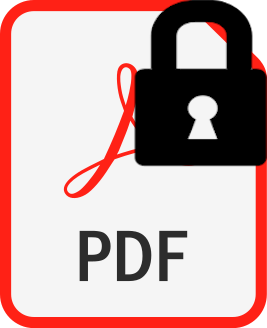 |
42. |
Atasoy H.♦, Vogler M.♦, Haatainen T.♦, Schleunitz A.♦, Jarząbek D.M.♦, Schift H.♦, Reuther F.♦, Gruetzner G.♦, Rymuza Z.♦, Novel thermoplastic polymers with improved release properties for thermal NIL,
MICROELECTRONIC ENGINEERING, ISSN: 0167-9317, DOI: 10.1016/j.mee.2011.01.080, Vol.88, pp.1902-1905, 2011 Abstract: In the nanoimprint lithography (NIL) process the mould release is a limiting step. Regardless of the carefully designed special properties a resist may have, it has to come over this challenging process step to be employed in a NIL process. Generally, the moulds are coated with anti-sticking layers. Here, an alternative solution is developed by modification of two well established NIL polymers through integration of fluorinated additives in their formulation. An effective additive concentration window was successfully defined, in which the substrate adhesion and imprint behaviour is not influenced. Defect-free patterning down to 30 nm is possible. A release force reduction of about 40% was observed with the modified polymer mr-I 7000R compared to the unmodified original Keywords: NIL polymers, Fluorinated additives, Release forces Affiliations:
Atasoy H. | - | other affiliation | Vogler M. | - | other affiliation | Haatainen T. | - | other affiliation | Schleunitz A. | - | other affiliation | Jarząbek D.M. | - | other affiliation | Schift H. | - | Paul Scherrer Institut (CH) | Reuther F. | - | other affiliation | Gruetzner G. | - | other affiliation | Rymuza Z. | - | other affiliation |
| 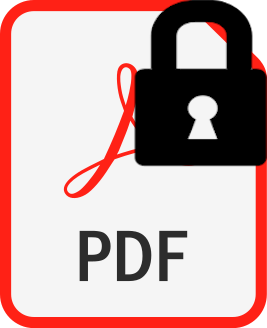 |
43. |
Jarząbek D.M.♦, Rymuza Z.♦, Horiba A.♦, Hirai Y.♦, Development of an experimental technique for testing rheological properties of ultrathin polymer films used in nanoimprint lithography,
JOURNAL OF VACUUM SCIENCE AND TECHNOLOGY B, ISSN: 1071-1023, DOI: 10.1116/1.3656377, Vol.29, No.6, pp.061603-1-6, 2011 Abstract: A new method for the measurement of rheological properties (complex viscosity, viscosity and elasticity) of thin polymeric films is presented. The probe, which is placed on the end of an arm of a mini tuning fork, is caused to oscillate and then is put into poly(methyl methacrylate) films, whose thickness ranges from 30 nm to 1080 nm. All measured properties depend on temperature, thickness of the films, indentation depth and the molecular weight of PMMA. Complex viscosity, viscosity and elasticity are found to be lower at higher temperatures and higher with greater molecular weight. They are also lower for thicker films. The results gained from this experiment may be useful in the development of nanoimprint lithography and many other branches of nanotechnology. Furthermore, the method allows for the measurement of the rheological properties of many different thin films (nanoimprint polymers, oils, lubricants) at different temperatures Affiliations:
Jarząbek D.M. | - | other affiliation | Rymuza Z. | - | other affiliation | Horiba A. | - | other affiliation | Hirai Y. | - | other affiliation |
| 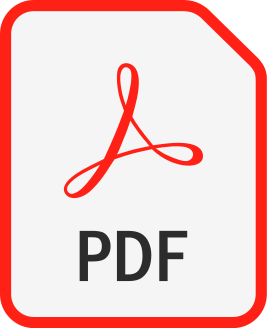 |