1. |
Nosewicz S., Jenczyk P., Romelczyk-Baishya B.♦, Bazarnik P.♦, Jarząbek D.M., Majchrowicz K.♦, Pakieła Z.♦, Kowiorski K.♦, Chmielewski M.♦, The influence of spark plasma sintering on multiscale mechanical properties of nickel-based composite materials,
MATERIALS SCIENCE AND ENGINEERING A-STRUCTURAL MATERIALS PROPERTIES MICROSTRUCTURE AND PROCESSING, ISSN: 0921-5093, DOI: 10.1016/j.msea.2023.146001, Vol.891, pp.146001, 2024 Streszczenie: The paper presents a comprehensive investigation of the influence of the main process parameters of spark plasma sintering on the mechanical and microstructural properties of nickel-silicon carbide composites at various scales. Microstructure analysis performed by scanning and transmission electron microscopy revealed a significant interfacial reaction between nickel and silicon carbide due to the decomposition of silicon carbide. The chemical interaction of the matrix and reinforcement results in the formation of a multicomponent interphase zone formed by silicides (Ni31Si12 or/and Ni3Si) and graphite precipitates. Furthermore, several types of structure defects were observed (mainly nano/micropores at the phase boundaries). These significantly influenced the mechanical response of nickel-silicon carbide composites at different levels. At the macroscopic scale, uniaxial tensile tests confirmed that applying a 1000 oC sintering temperature ensured that the manufactured composite was characterised by satisfactory tensile strength, however, with a considerable reduction of material elongation compared to pure nickel. Moreover, the fractography study allowed us to identify a significant difference in the damage mode for certain nickel-silicon carbide samples. Secondly, the interface of the nickel matrix and silicate interphase was tested by bending with microcantilevers to evaluate its deformation behaviour, strength, and fracture characteristics. It was confirmed that a diffusive kind of interface, such as Ni-NiSi, demonstrates unexpected bonding properties with a relatively large range of plastic deformation. Finally, the nanoindentation of three main components of the nickel-silicon carbide composite was executed to evaluate the evolution of nanohardness, Young’s modulus, and elastic recovery due to the application of various spark plasma sintering conditions. Słowa kluczowe: nickel-based composite,silicon carbide,spark plasma sintering,multiscale characterization,mechanical properties,nanoindentation,bending of microcantilevers Afiliacje autorów:
Nosewicz S. | - | IPPT PAN | Jenczyk P. | - | IPPT PAN | Romelczyk-Baishya B. | - | Politechnika Warszawska (PL) | Bazarnik P. | - | Politechnika Warszawska (PL) | Jarząbek D.M. | - | IPPT PAN | Majchrowicz K. | - | inna afiliacja | Pakieła Z. | - | Politechnika Warszawska (PL) | Kowiorski K. | - | inna afiliacja | Chmielewski M. | - | Institute of Electronic Materials Technology (PL) |
| 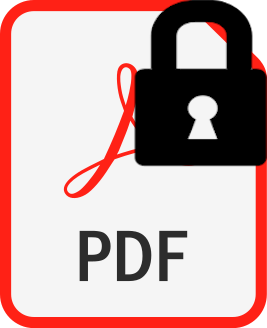 | 140p. |
2. |
Chmielewski M.♦, Zybała R.♦, Strojny-Nędza A.♦, Piątkowska A.♦, Dobrowolski A.P.♦, Jagiełło J.♦, Diduszko R.♦, Bazarnik P.♦, Nosewicz S., Microstructural Evolution of Ni-SiC Composites Manufactured by Spark Plasma Sintering,
METALLURGICAL AND MATERIALS TRANSACTIONS A-PHYSICAL METALLURGY AND MATERIALS SCIENCE, ISSN: 1073-5623, DOI: 10.1007/s11661-023-06999-w, Vol.54, No.-, pp.2191-2207, 2023 Streszczenie: The presented paper concerns the technological aspects of the interface evolution in the nickel-silicon carbide composite during the sintering process. The goal of our investigation was to analyse the material changes occurring due to the violent reaction between nickel and silicon carbide at elevated temperatures. The nickel matrix composite with 20 vol pct SiC particles as the reinforcing phase was fabricated by the spark plasma sintering technique. The sintering tests were conducted with variable process conditions (temperature, time, and pressure). It was revealed that the strong interaction between the individual components and the scale of the observed changes depends on the sintering parameters. To identify the microstructural evolution, scanning electron microscopy, energy dispersive spectroscopy, transmission electron microscopy, X-ray diffraction, and Raman spectroscopy were used. The silicon carbide decomposition process progresses with the extension of the sintering time. As the final product of the observed reaction, new phases from the Ni-Si system and free carbon were detected. The step-by-step materials evolution allowed us to reveal the course of the reaction and the creation of the new structure, especially in the reaction zone. The detailed analysis of the SiC decomposition and formation of new components was the main achievement of the presented paper. Afiliacje autorów:
Chmielewski M. | - | Institute of Electronic Materials Technology (PL) | Zybała R. | - | Politechnika Warszawska (PL) | Strojny-Nędza A. | - | Institute of Electronic Materials Technology (PL) | Piątkowska A. | - | Institute of Electronic Materials Technology (PL) | Dobrowolski A.P. | - | Military University of Technology (PL) | Jagiełło J. | - | inna afiliacja | Diduszko R. | - | Tele and Radio Research Institute (PL) | Bazarnik P. | - | Politechnika Warszawska (PL) | Nosewicz S. | - | IPPT PAN |
| 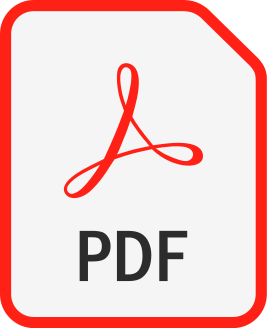 | 200p. |
3. |
Psiuk R., Milczarek M., Jenczyk P., Denis P., Jarząbek D., Bazarnik P.♦, Pisarek M.♦, Mościcki T., Improved mechanical properties of W-Zr-B coatings deposited by hybrid RF magnetron – PLD method,
APPLIED SURFACE SCIENCE, ISSN: 0169-4332, DOI: 10.1016/j.apsusc.2021.151239, Vol.570, pp.151239-1-11, 2021 Streszczenie: In this work, novel W-Zr-B coatings were developed by a hybrid process combining pulsed laser deposited ZrB2 and radio frequency magnetron sputtered W2B5. The influence of the laser power density on the structure and mechanical properties of the deposited films was studied. Addition of zirconium causes a change in the structure of the deposited films from columnar to mainly amorphous. The nanoindentation tests and compression of nanopillars showed that doped W-Zr-B layers are still super-hard and incompressible in comparison to WB2 films without doping, but they change their behaviour from brittle to ductile. Films obtained with a fluence of 1.06 J/cm2 are superhard (H = 40 ± 4 GPa) and incompressible (12 ± 1 GPa), but possess a relatively low Young’s modulus (E = 330 ± 32 GPa) and a high elastic recovery (We = 0.9). Further increase in the fluence causes films to consist of deeply embedded fragments of laser ablated ZrB2 target in the deposited layer. Taking into account that the particles are made of ZrB2 which possess extraordinary thermal properties, and the matrix is made of W-Zr-B, a super-hard material, such a composite can also be interesting for industrial applications. Słowa kluczowe: superhard tungsten borides, hybrid magnetron sputtering – pulsed laser deposition, nanopillar compression Afiliacje autorów:
Psiuk R. | - | IPPT PAN | Milczarek M. | - | IPPT PAN | Jenczyk P. | - | IPPT PAN | Denis P. | - | IPPT PAN | Jarząbek D. | - | IPPT PAN | Bazarnik P. | - | Politechnika Warszawska (PL) | Pisarek M. | - | Institute of Physical Chemistry, Polish Academy of Sciences (PL) | Mościcki T. | - | IPPT PAN |
| 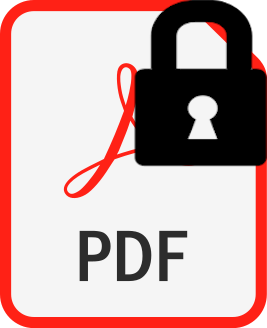 | 140p. |
4. |
Nosewicz S., Bazarnik P.♦, Clozel M.♦, Kurpaska Ł.♦, Jenczyk P., Jarząbek D., Chmielewski M.♦, Romelczyk-Baishya B.♦, Lewandowska M.♦, Pakieła Z.♦, Huang Y.♦, Langdon T.G.♦, A multiscale experimental analysis of mechanical properties and deformation behavior of sintered copper–silicon carbide composites enhanced by high-pressure torsion,
ARCHIVES OF CIVIL AND MECHANICAL ENGINEERING, ISSN: 1644-9665, DOI: 10.1007/s43452-021-00286-4, Vol.21, pp.131-1-19, 2021 Streszczenie: Experiments were conducted to investigate, within the framework of a multiscale approach, the mechanical enhancement, deformation and damage behavior of copper–silicon carbide composites (Cu–SiC) fabricated by spark plasma sintering (SPS) and the combination of SPS with high-pressure torsion (HPT). The mechanical properties of the metal–matrix composites were determined at three different length scales corresponding to the macroscopic, micro- and nanoscale. Small punch testing was employed to evaluate the strength of composites at the macroscopic scale. Detailed analysis of microstructure evolution related to SPS and HPT, sample deformation and failure of fractured specimens was conducted using scanning and transmission electron microscopy. A microstructural study revealed changes in the damage behavior for samples processed by HPT and an explanation for this behavior was provided by mechanical testing performed at the micro- and nanoscale. The strength of copper samples and the metal–ceramic interface was determined by microtensile testing and the hardness of each composite component, corresponding to the metal matrix, metal–ceramic interface, and ceramic reinforcement, was measured using nano-indentation. The results confirm the advantageous effect of large plastic deformation on the mechanical properties of Cu–SiC composites and demonstrate the impact on these separate components on the deformation and damage type. Słowa kluczowe: copper–silicon carbide composite, high-pressure torsion, metal–matrix composites, multiscale analysis, nano-indentation, small punch test Afiliacje autorów:
Nosewicz S. | - | IPPT PAN | Bazarnik P. | - | Politechnika Warszawska (PL) | Clozel M. | - | National Centre for Nuclear Research (PL) | Kurpaska Ł. | - | National Centre for Nuclear Research (PL) | Jenczyk P. | - | IPPT PAN | Jarząbek D. | - | IPPT PAN | Chmielewski M. | - | Institute of Electronic Materials Technology (PL) | Romelczyk-Baishya B. | - | Politechnika Warszawska (PL) | Lewandowska M. | - | inna afiliacja | Pakieła Z. | - | Politechnika Warszawska (PL) | Huang Y. | - | Bournemouth University (GB) | Langdon T.G. | - | University of Southampton (GB) |
| 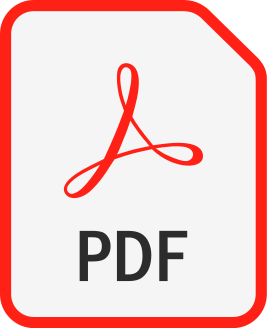 | 140p. |
5. |
Jarząbek D.M., Milczarek M., Nosewicz S., Bazarnik P.♦, Schift H.♦, Size effects of hardness and strain rate sensitivity in amorphous silicon measured by nanoindentation,
METALLURGICAL AND MATERIALS TRANSACTIONS A-PHYSICAL METALLURGY AND MATERIALS SCIENCE, ISSN: 1073-5623, DOI: 10.1007/s11661-020-05648-w, Vol.51, No.4, pp.1625-1633, 2020 Streszczenie: In this work, dynamic mechanical properties of amorphous silicon and scale effects were investigated by the means of nanoindentation. An amorphous silicon sample was prepared by plasma-enhanced chemical vapor deposition (PECVD). Next, two sets of the samples were investigated: as-deposited and annealed in 500 °C for 1 hour. A three-sided pyramidal diamond Berkovich's indenter was used for the nanoindentation tests. In order to determine the strain rate sensitivity (SRS), indentations with different loading rates were performed: 0.1, 1, 10, 100 mN/min. Size effects were studied by application of maximum indentation loads in the range from 1 up to 5 mN (penetrating up to approximately one-third of the amorphous layer). The value of hardness was determined by the Oliver-Pharr method. An increase of hardness with decrease of the indentation depth was observed for both samples. Furthermore, the significant dependence of hardness on the strain rate has been reported. Finally, for the annealed samples at low strain rates a characteristic "elbow" during unloading was observed on the force-indentation depth curves. It could be attributed to the transformation of (β-Sn)-Si to the PI (pressure-induced) a-Si end phase. Afiliacje autorów:
Jarząbek D.M. | - | IPPT PAN | Milczarek M. | - | IPPT PAN | Nosewicz S. | - | IPPT PAN | Bazarnik P. | - | Politechnika Warszawska (PL) | Schift H. | - | Paul Scherrer Institut (CH) |
| 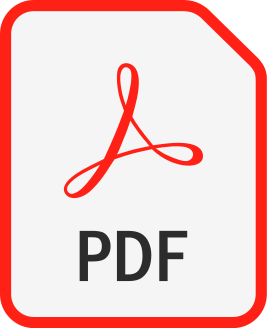 | 200p. |
6. |
Mościcki T., Psiuk R., Słomińska H., Levintant-Zayonts N., Garbiec D.♦, Pisarek M.♦, Bazarnik P.♦, Nosewicz S., Chrzanowska-Giżyńska J., Influence of overstoichiometric boron and titanium addition on the properties of RF magnetron sputtered tungsten borides,
SURFACE AND COATINGS TECHNOLOGY, ISSN: 0257-8972, DOI: 10.1016/j.surfcoat.2020.125689, Vol.390, pp.125689-1-12, 2020 Streszczenie: In this work, (W,Ti)B2 films with different stoichiometric ratio Ti/W deposited on silicon and 304 stainless steel by radio frequency magnetron sputtering are presented. The coatings were deposited from plasma spark sintered targets obtained from the mixture of pure boron, tungsten and titanium powders. It is shown that during plasma spark sintering process using overstoichiometric boron and a low content of titanium change the WB2 to WB4 phase with almost no secondary phases. Subsequently, the impact of titanium content on the films properties is investigated systematically, including the chemical and phase composition, crystalline structure, surface and cross-section morphology. Simultaneously, nano-indentation test and ball-on-disk tribometery are performed to analyse the hardness and tribological properties of the films. It is shown that deposited films with titanium content of 3.6 and 5.5 at.% are formed in the zone T of the Thornton's Structural Zone Model. In opposite to α-WB2 magnetron sputtered coatings they are more flexible and hard nanocomposite coatings. The results show that the addition of titanium is apparently changing the film structure from nanocrystalline columnar to amorphous, very dense and compact structure with the addition of TiB2 phase. That films are simultaneously hard (H > 37.5 GPa), have high hardness to effective Young's modulus ratio values (H/E* > 0.1) and elastic recovery (We > 60%) appropriate for tough and resistant to cracking materials. The presented (W,Ti)B2 films exhibit also tribological and corrosion properties better than unalloyed coatings. Słowa kluczowe: superhard films, ternary tungsten borides, RF magnetron sputtering, wear resistance, corrosion Afiliacje autorów:
Mościcki T. | - | IPPT PAN | Psiuk R. | - | IPPT PAN | Słomińska H. | - | IPPT PAN | Levintant-Zayonts N. | - | IPPT PAN | Garbiec D. | - | Metal Forming Institute, Poznań (PL) | Pisarek M. | - | Institute of Physical Chemistry, Polish Academy of Sciences (PL) | Bazarnik P. | - | Politechnika Warszawska (PL) | Nosewicz S. | - | IPPT PAN | Chrzanowska-Giżyńska J. | - | IPPT PAN |
| 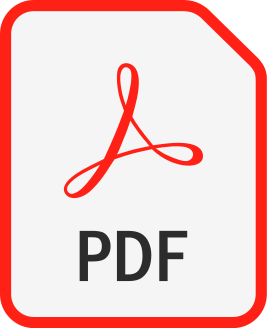 | 100p. |
7. |
Bazarnik P.♦, Nosewicz S., Romelczyk-Baishya B.♦, Chmielewski M.♦, Strojny-Nędza A.♦, Maj J., Huang Y.♦, Lewandowska M.♦, Langdon T.G.♦, Effect of spark plasma sintering and high-pressure torsion on the microstructural and mechanical properties of a Cu–SiC composite,
MATERIALS SCIENCE AND ENGINEERING A-STRUCTURAL MATERIALS PROPERTIES MICROSTRUCTURE AND PROCESSING, ISSN: 0921-5093, DOI: 10.1016/j.msea.2019.138350, Vol.766, pp.138350-1-11, 2019 Streszczenie: This investigation examines the problem of homogenization in metal matrix composites (MMCs) and the methods of increasing their strength using severe plastic deformation (SPD). In this research MMCs of pure copper and silicon carbide were synthesized by spark plasma sintering (SPS) and then further processed via high-pressure torsion (HPT). The microstructures in the sintered and in the deformed materials were investigated using Scanning Electron Microscopy (SEM) and Scanning Transmission Electron Microscopy (STEM). The mechanical properties were evaluated in microhardness tests and in tensile testing. The thermal conductivity of the composites was measured with the use of a laser pulse technique. Microstructural analysis revealed that HPT processing leads to an improved densification of the SPS-produced composites with significant grain refinement in the copper matrix and with fragmentation of the SiC particles and their homogeneous distribution in the copper matrix. The HPT processing of Cu and the Cu–SiC samples enhanced their mechanical properties at the expense of limiting their plasticity. Processing by HPT also had a major influence on the thermal conductivity of materials. It is demonstrated that the deformed samples exhibit higher thermal conductivity than the initial coarse-grained samples. Słowa kluczowe: copper, silicon carbide, high-pressure torsion, spark plasma sintering, thermal conductivity Afiliacje autorów:
Bazarnik P. | - | Politechnika Warszawska (PL) | Nosewicz S. | - | IPPT PAN | Romelczyk-Baishya B. | - | Politechnika Warszawska (PL) | Chmielewski M. | - | Institute of Electronic Materials Technology (PL) | Strojny-Nędza A. | - | Institute of Electronic Materials Technology (PL) | Maj J. | - | IPPT PAN | Huang Y. | - | Bournemouth University (GB) | Lewandowska M. | - | inna afiliacja | Langdon T.G. | - | University of Southampton (GB) |
| 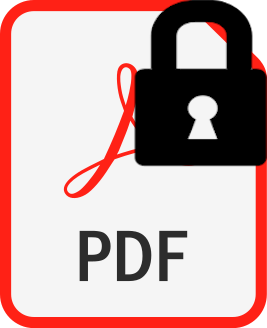 | 140p. |
8. |
Nosewicz S., Romelczyk-Baishya B.♦, Lumelskyj D., Chmielewski M.♦, Bazarnik P.♦, Jarząbek D.M., Pietrzak K., Kaszyca K.♦, Pakieła Z.♦, Experimental and numerical studies of micro- and macromechanical properties of modified copper–silicon carbide composites,
INTERNATIONAL JOURNAL OF SOLIDS AND STRUCTURES, ISSN: 0020-7683, DOI: 10.1016/j.ijsolstr.2018.10.025, Vol.160, pp.187-200, 2019 Streszczenie: The presented research investigation comprises the study of the mechanical properties of modified copper–silicon carbide composites at the micro- and macroscopic scale. The improvement of a copper–silicon carbide composite refers to the addition of a protective layer at the ceramic reinforcement in order to prevent the dissolution of silicon in the copper matrix. The macromechanical behaviour has been evaluated by the performance in a small punch test. The investigation has been carried out with samples with varying volume content of ceramic reinforcement and different protective layers of the silicon carbide particles. Moreover, the influence of temperature during the strength test has been studied. Next, the results have been referred to the interfacial bonding strength of Cu and SiC particles. SEM characterization of samples has been performed to link the composites' microstructure with the mechanical behaviour. Finally, the experimental results of the small punch test have been predicted via a numerical approach. Finite element analysis has been employed to reproduce the response of the composite specimen during the test. Satisfactory agreement with the experimental curve has been obtained. Słowa kluczowe: metal matrix composites, silicon carbide, metallic layers deposition, small punch, interface strength, finite element method Afiliacje autorów:
Nosewicz S. | - | IPPT PAN | Romelczyk-Baishya B. | - | Politechnika Warszawska (PL) | Lumelskyj D. | - | IPPT PAN | Chmielewski M. | - | Institute of Electronic Materials Technology (PL) | Bazarnik P. | - | Politechnika Warszawska (PL) | Jarząbek D.M. | - | IPPT PAN | Pietrzak K. | - | IPPT PAN | Kaszyca K. | - | Lukasiewicz Institute of Microelectronics and Photonics (PL) | Pakieła Z. | - | Politechnika Warszawska (PL) |
| 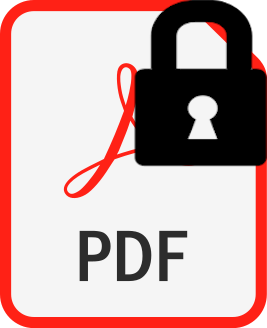 | 140p. |
9. |
Chmielewski M.♦, Nosewicz S., Wyszkowska E.♦, Kurpaska Ł.♦, Strojny-Nędza A.♦, Piątkowska A.♦, Bazarnik P.♦, Pietrzak K., Analysis of the micromechanical properties of copper-silicon carbide composites using nanoindentation measurements,
CERAMICS INTERNATIONAL, ISSN: 0272-8842, DOI: 10.1016/j.ceramint.2019.01.257, Vol.45, No.7A, pp.9164-9173, 2019 Streszczenie: The study presents a detailed analysis of the impact of the coating type of silicon carbide particles and its share by volume on the microstructure and micromechanical properties of Cu-SiC composites. In order to protect the carbide from decomposition during the manufacturing of the composites, the surface of SiC was modified via a plasma vapour deposition technique with a layer of metals (W, Cr, Ti and Ni). Composites with a variable share of the ceramic phase (10–50 %vol.) were obtained at a temperature of 950 °C using spark plasma sintering. An analysis of the structures of the composites, especially in the metal-ceramic boundary region, was conducted with the use of scanning and transmission electron microscopy. The mechanical properties of the composites in the Cu-interface-SiC system were studied via a nanoindentation technique. The comparison of the results of hardness and Young's modulus studies were completed in relation to the actual structures of the materials, which in turn made it possible to determine the impact of the interfacial structure on the global properties of the composite materials. Słowa kluczowe: copper-silicon carbide composites, nanoindentation, SPS, interface study Afiliacje autorów:
Chmielewski M. | - | Institute of Electronic Materials Technology (PL) | Nosewicz S. | - | IPPT PAN | Wyszkowska E. | - | National Centre for Nuclear Research (PL) | Kurpaska Ł. | - | National Centre for Nuclear Research (PL) | Strojny-Nędza A. | - | Institute of Electronic Materials Technology (PL) | Piątkowska A. | - | Institute of Electronic Materials Technology (PL) | Bazarnik P. | - | Politechnika Warszawska (PL) | Pietrzak K. | - | IPPT PAN |
| 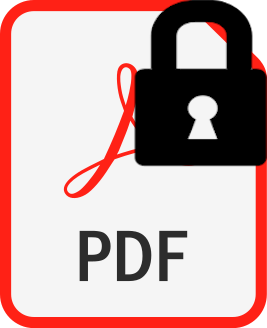 | 100p. |
10. |
Chmielewski M.♦, Pietrzak K.♦, Teodorczyk M.♦, Nosewicz S., Jarząbek D.M., Zybała R.♦, Bazarnik P.♦, Lewandowska M.♦, Strojny-Nędza A.♦, Effect of metallic coating on the properties of copper-silicon carbide composites,
APPLIED SURFACE SCIENCE, ISSN: 0169-4332, DOI: 10.1016/j.apsusc.2016.12.130, Vol.421, pp.159-169, 2017 Streszczenie: In the presented paper a coating of SiC particles with a metallic layer were used to prepare copper matrix composite materials. The role of the layer was to protect the silicon carbide from decomposition and dissolution of silicon in the copper matrix during the sintering process. The SiC particles were covered by chromium, tungsten and titanium using Plasma Vapour Deposition method. After powder mixing of components, the final densification process via Spark Plasma Sintering (SPS) method at temperature 950C was provided. The almost fully dense materials were obtained (> 97.5%). The microstructure of obtained composites was studied using scanning electron microscopy as well as transmission electron microscopy. The microstructural analysis of composites confirmed that regardless of the type of deposited material, there is no evidence for decomposition process of silicon carbide in copper. In order to measure the strength of the interface between ceramic particles and the metal matrix, the micro tensile tests have been performed. Furthermore, thermal diffusivity was measured with the use of the laser pulse technique. In the context of performed studies, the tungsten coating seems to be the most promising solution for heat sink application. Compared to pure composites without metallic layer, Cu-SiC with W coating indicate the higher tensile strength and thermal diffusitivy, irrespective of an amount of SiC reinforcement. The improvement of the composite properties is related to advantageous condition of Cu-SiC interface characterized by well homogenity and low porosity, as well as individual properties of the tungsten coating material. Słowa kluczowe: metal matrix composites, silicon carbide, metallic layers deposition, thermal conductovity, interface strength Afiliacje autorów:
Chmielewski M. | - | Institute of Electronic Materials Technology (PL) | Pietrzak K. | - | inna afiliacja | Teodorczyk M. | - | Institute of Electronic Materials Technology (PL) | Nosewicz S. | - | IPPT PAN | Jarząbek D.M. | - | IPPT PAN | Zybała R. | - | Politechnika Warszawska (PL) | Bazarnik P. | - | Politechnika Warszawska (PL) | Lewandowska M. | - | inna afiliacja | Strojny-Nędza A. | - | Institute of Electronic Materials Technology (PL) |
| 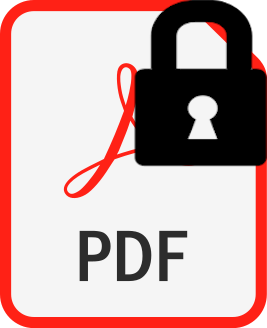 | 35p. |
11. |
Chmielewski M.♦, Pietrzak K.♦, Strojny-Nędza A.♦, Kaszyca K.♦, Zybala R.♦, Bazarnik P.♦, Lewandowska M.♦, Nosewicz S., Microstructure and thermal properties of Cu-SiC composite materials depending on the sintering technique,
SCIENCE OF SINTERING, ISSN: 0350-820X, DOI: 10.2298/SOS1701011C, Vol.49, No.1, pp.11-22, 2017 Streszczenie: The presented paper investigates the relationship between the microstructure and thermal properties of copper–silicon carbide composites obtained through hot pressing (HP) and spark plasma sintering (SPS) techniques. The microstructural analysis showed a better densification in the case of composites sintered in the SPS process. TEM investigations revealed the presence of silicon in the area of metallic matrix in the region close to metal ceramic boundary. It is the product of silicon dissolving process in copper occurring at an elevated temperature. The Cu-SiC interface is significantly defected in composites obtained through the hot pressing method, which has a major influence on the thermal conductivity of materials. Słowa kluczowe: metal matrix composites, silicon carbide, interface, spark plasma sintering, thermal conductivity Afiliacje autorów:
Chmielewski M. | - | Institute of Electronic Materials Technology (PL) | Pietrzak K. | - | inna afiliacja | Strojny-Nędza A. | - | Institute of Electronic Materials Technology (PL) | Kaszyca K. | - | Lukasiewicz Institute of Microelectronics and Photonics (PL) | Zybala R. | - | Politechnika Warszawska (PL) | Bazarnik P. | - | Politechnika Warszawska (PL) | Lewandowska M. | - | inna afiliacja | Nosewicz S. | - | IPPT PAN |
| 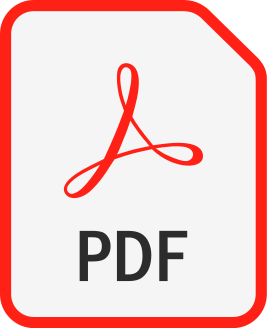 | 30p. |
12. |
Chmielewski M.♦, Nosewicz S., Jakubowska D.♦, Lewandowska M.♦, Mizera J.♦, Rojek J., Bazarnik P.♦, The influence of sintering time on the microstructural properties of chromium-rhenium matrix composites,
International Journal of Refractory Metals and Hard Materials, ISSN: 0263-4368, DOI: 10.1016/j.ijrmhm.2016.05.017, Vol.59, pp.78-86, 2016 Streszczenie: This paper comprises the results of studies of the changes in the structure of Cr-Re-Al2O3 metal matrix depending on heat treatment time in sintering temperature. The density of material with the following composition: 95%(75%Cr-25%Al2O3)+5%Re was increased using the technique of sintering under pressure (30MPa) at the temperature of 1450°C. As a result, materials characterized by a high relative density (< 97% of theoretical density) were obtained. Next, they were subjected to structural tests including scanning and transmission electron microscopy as well as X-ray diffraction. Changes in the phase composition, grains size and parameters of crystallographic structure depending on heat treatment time were analysed. It was found that during sintering rhenium is dissolved in the chromium matrix and Cr-Re solid solution is formed. When sintering time is extended to 120 min, the matrix of the composite becomes completely homogenous, which results in an increased strength of the composite. Słowa kluczowe: Metal matrix composites, Rhenium, Hot pressing, Microstructure analysis, XRD Afiliacje autorów:
Chmielewski M. | - | Institute of Electronic Materials Technology (PL) | Nosewicz S. | - | IPPT PAN | Jakubowska D. | - | inna afiliacja | Lewandowska M. | - | inna afiliacja | Mizera J. | - | Politechnika Warszawska (PL) | Rojek J. | - | IPPT PAN | Bazarnik P. | - | Politechnika Warszawska (PL) |
| 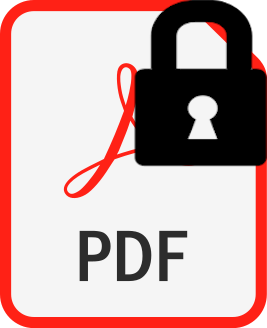 | 35p. |