1. |
Macek W.♦, Sitek R.♦, Podulka P.♦, Lesiuk G.♦, Zhu S.♦, Liu X.♦, Kopeć M., Fractography of Haynes 282 alloy manufactured by DMLS after tensile and HCF,
Journal of Constructional Steel Research, ISSN: 1873-5983, DOI: 10.1016/j.jcsr.2025.109623, Vol.232, No.109623, pp.1-12, 2025 Streszczenie: In this paper, the fracture surface topography of additively manufactured Haynes 282 alloy subjected to tensile and high-cycle fatigue loading was investigated. Haynes 282 alloy bars were printed in three different directions relative to the base plate (0°, 45°, and 90°) via Direct Metal Laser Sintering (DMLS) under an argon protective atmosphere. The specimens were subjected to monotonic tensile loading and fatigue testing under load control using full tension and compression cyclic loading (R = −1) in the range of stress amplitude from ±550 MPa to ±800 MPa. The entire surface topography was evaluated by using a 3D non-contact confocal technique and post-failure specimens after a fatigue test performed at three stress amplitudes, ±650 MPa, ±700 MPa and ±750 MPa. Such an attempt was proposed to analyse the fatigue response of AM Haynes 282 in the region near its yield strength. It was found that the printing orientation and the stress amplitude have a strong impact on service life and fracture surface characteristics. Finally, a surface topography parameter involving the mass density of furrows, root-mean-square height, and fractal dimension was successfully combined with the stress amplitude to estimate the fatigue life. The findings offer a novel approach to fatigue life prediction based on post-failure surface analysis, providing valuable insights for industrial applications and forensic engineering. Słowa kluczowe: Nickel alloys,Fatigue,Additive manufacturing,Direct Metal Laser Sintering (DMLS),Fracture,Surface topography Afiliacje autorów:
Macek W. | - | inna afiliacja | Sitek R. | - | Politechnika Warszawska (PL) | Podulka P. | - | inna afiliacja | Lesiuk G. | - | inna afiliacja | Zhu S. | - | inna afiliacja | Liu X. | - | Imperial College London (GB) | Kopeć M. | - | IPPT PAN |
| 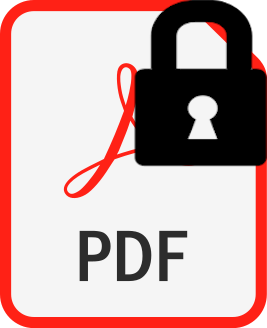 | 140p. |
2. |
Kopeć M., Przygucka D.♦, Mierzejewska I., Sitek R.♦, Kowalewski Z. L., Jóźwiak S.♦, Effect of printing orientation on microstructure and fatigue behaviour of additively manufactured Haynes 282,
JOURNAL OF ALLOYS AND COMPOUNDS, ISSN: 0925-8388, No.181777, pp.1-16, 2025 Streszczenie: In this study, Haynes 282 alloy bars were fabricated using Direct Metal Laser Sintering (DMLS) in three build orientations: 0°, 45°, and 90°. The process was conducted under an argon protective atmosphere with an energy density of 104 J/mm³, a laser power of 100 W, and a scanning speed of 800 mm/s. The additively manufactured (AM) specimens underwent fatigue testing at stress amplitudes ranging from ±550 MPa to ±800 MPa. Specimens printed at 0° and 45° showed significantly improved mechanical performance, indicating these orientations are more favorable. Notably, the AM specimens demonstrated extended service life at stress amplitudes below 700 MPa, highlighting the potential of DMLS for producing durable Haynes 282 components. Słowa kluczowe: Haynes 282,nickel alloys,fatigue,additive manufacturing,Direct Metal Laser Sintering (DMLS) Afiliacje autorów:
Kopeć M. | - | IPPT PAN | Przygucka D. | - | inna afiliacja | Mierzejewska I. | - | IPPT PAN | Sitek R. | - | Politechnika Warszawska (PL) | Kowalewski Z. L. | - | IPPT PAN | Jóźwiak S. | - | Military University of Technology (PL) |
| 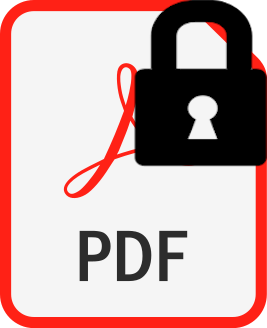 | 100p. |
3. |
Kamiński J.♦, Adamczyk-Cieślak B.♦, Kopeć M., Kosiński A.♦, Sitek R.♦, Cover Picture: Materials and Corrosion. 3/2025: Effects of Reduction-Oxidation Cycles on the Structure, Heat and Corrosion Resistance of Haynes 282 Nickel Alloy Manufactured by using Powder Bed Fusion- Laser Beam Method,
materials and corrosion, ISSN: 0947-5117, DOI: 10.1002/maco.202570031, pp.1-1, 2025, EDITORIAL Słowa kluczowe: corrosion, DMLS, haynes 282, nickel superalloy, hydrogen , oxidation Afiliacje autorów:
Kamiński J. | - | inna afiliacja | Adamczyk-Cieślak B. | - | inna afiliacja | Kopeć M. | - | IPPT PAN | Kosiński A. | - | inna afiliacja | Sitek R. | - | Politechnika Warszawska (PL) |
| 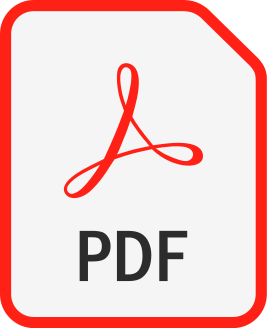 |
4. |
Sitek R.♦, Bochenek K., Maj P.♦, Marczak M.♦, Żaba K.♦, Kopeć M., Kaczmarczyk G.♦, Kamiński J.♦, Hot-Pressing of Ti-Al-N Multiphase Composite: Microstructure and Properties,
Applied Sciences, ISSN: 2076-3417, DOI: 10.3390/app15031341, Vol.15, No.1341, pp.1-15, 2025 Streszczenie: This study focuses on the development and characterization of a bulk Ti-Al-N
multiphase composite enriched with BN addition and sintered through hot pressing. The
research aimed to create a material with optimized mechanical and corrosion-resistant
properties suitable for demanding industrial applications. The composite was synthesized using a powder metallurgy approach with a mixture of AlN, TiN, and BN powders, processed under a high temperature and pressure. Comprehensive analyses, including microstructural evaluation, hardness testing, X-ray tomography, and electrochemical corrosion assessments, were conducted. The results confirmed the formation of a multiphase microstructure consisting of TiN, Ti₂AlN and Ti₃AlN phases. The microstructure was uniform with minimal porosity, achieving a hardness within the range of 500–540 HV2. Electrochemical tests revealed the formation of a passive oxide layer that provided moderate corrosion resistance in chloride-rich environment. However, localized pitting corrosion was observed under extreme conditions. The study highlights the potential of a BN admixture to enhance mechanical and corrosion-resistant properties and suggests directions for further optimization in sintering processes and material formulations. Słowa kluczowe: AlN-TiN(BN) composite,hot-pressing,μCT,corrosion resistance Afiliacje autorów:
Sitek R. | - | Politechnika Warszawska (PL) | Bochenek K. | - | IPPT PAN | Maj P. | - | Politechnika Warszawska (PL) | Marczak M. | - | inna afiliacja | Żaba K. | - | inna afiliacja | Kopeć M. | - | IPPT PAN | Kaczmarczyk G. | - | inna afiliacja | Kamiński J. | - | inna afiliacja |
| 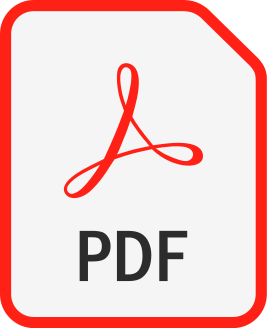 | 100p. |
5. |
Kamiński J.♦, Adamczyk-Cieślak B.♦, Kopeć M., Kosiński A.♦, Sitek R.♦, Effects of Reduction-Oxidation Cycles on the Structure, Heat and Corrosion Resistance of Haynes 282 Nickel Alloy Manufactured by Using Powder Bed Fusion-Laser Beam Method,
materials and corrosion, ISSN: 0947-5117, DOI: 10.1002/maco.202414477, pp.1-14, 2024 Streszczenie: The study investigated the effect of the oxidation–reduction cycles on the structure and corrosion resistance of the Haynes 282 nickel superalloy at ambient and elevated temperatures. The comparative studies were performed on specimens produced by the Powder Bed Fusion-Laser Beam (PBF-LB) process and those in the as-received state. The microstructure of the PBF-LB specimens was studied using optical and scanning electron microscopy, whereas the chemical composition of the scale formed after isothermal oxidation in an air atmosphere at 750°C was analysed using energy-dispersive X-ray spectroscopy and X-ray Photoelectron Spectroscopy. The phase composition of the formed scale was determined by X-ray diffraction. Laboratory-induced hydrogen atmosphere was adopted through cathodic charging. A comparison of corrosion resistance was carried out on two types of Haynes 282 specimens, before and after the oxidation and cathodic charging processes. It was found that PBF-LB process could be effectively used to manufacture Haynes 282 nickel superalloy with low porosity and a fine crystalline microstructure. The low-porous, fine-crystalline microstructure of the tested specimens produced by the PBF-LB technique exhibited good resistance to electrochemical corrosion, slightly lower than wrought Haynes 282 nickel superalloy specimens. Słowa kluczowe: corrosion, DMLS, haynes 282 nickel superalloy, hydrogen, oxidation Afiliacje autorów:
Kamiński J. | - | inna afiliacja | Adamczyk-Cieślak B. | - | inna afiliacja | Kopeć M. | - | IPPT PAN | Kosiński A. | - | inna afiliacja | Sitek R. | - | Politechnika Warszawska (PL) |
| 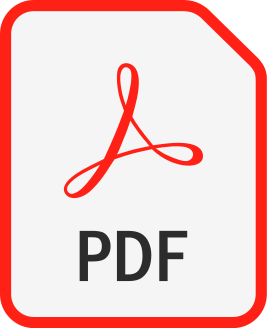 | 100p. |
6. |
Kopeć M., Mierzejewska I., Gorniewicz D.♦, Sitek R.♦, Jóźwiak S.♦, High-temperature oxidation behaviour of additively manufactured and wrought HAYNES 282,
JOURNAL OF MATERIALS SCIENCE, ISSN: 0022-2461, DOI: 10.1007/s10853-024-10207-4, pp.1-19, 2024 Streszczenie: Direct Metal Laser Sintered Haynes 282 specimens as well as wrought ones were subjected to high-temperature exposure at 1000 °C for 100h in air to compare their oxidation behaviour. The specimens were removed from the furnace after 1h, 5h, 25h, 50h and 100h to reveal and study oxidation mechanisms through morphological and cross-sectional examination by using scanning electron microscopy with energy dispersive spectroscopy attachment and X-ray diffraction. Microstructural studies revealed that the oxidation kinetics, determined by changes in thickness scale and depth of aluminium diffusion zone, were mainly driven by the formation of Cr2O3 for the wrought material, and TiO2 for DMLS one. The wrought material was characterized by the oxidation rate equal to 0.96 and followed the logarithmic law. On the other hand, DMLS-manufactured Haynes 282 exhibited oxidation rate of 0.90 and follows the linear law for the thickness scale considerations. However, when the depth of aluminium diffusion was investigated, it had an oxidation rate of 0.87 and followed cubic law. Afiliacje autorów:
Kopeć M. | - | IPPT PAN | Mierzejewska I. | - | IPPT PAN | Gorniewicz D. | - | Military University of Technology (PL) | Sitek R. | - | Politechnika Warszawska (PL) | Jóźwiak S. | - | Military University of Technology (PL) |
| 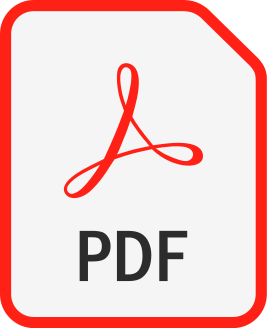 | 100p. |
7. |
Maj P.♦, Bochenek K., Sitek R.♦, Koralnik M.♦, Jonak K.♦, Wieczorek M.♦, Pakieła Z.♦, Mizera J.♦, Comparison of mechanical properties and structure of Haynes 282 consolidated via two different powder metallurgy methods: laser powder bed fusion and hot pressing,
ARCHIVES OF CIVIL AND MECHANICAL ENGINEERING, ISSN: 1644-9665, DOI: 10.1007/s43452-023-00674-y, Vol.23, No.130, pp.1-11, 2023 Streszczenie: The development of powder metallurgy methods in recent years has caused traditional casting methods to be replaced in many industrial applications. Using such methods, it is possible to obtain parts having the required geometry after a process that saves both manufacturing costs and time. However, there are many material issues that decrease the functionality of these methods, including mechanical properties anisotropy and greater susceptibility to cracking due to chemical segregation. The main aim of the current article is to analyze these issues in depth for two powder metallurgy manufacturing processes: laser powder bed fusion (LPBF) and hot-pressing (HP) methods—selected for the experiment because they are in widespread use. Microstructure and mechanical tests were performed in the main manufacturing directions, X and Z. The results show that in both powder metallurgy methods, anisotropy was an issue, although it seems that the problem was more significant for the samples produced via LPBF SLM technique, which displayed only half the elongation in the building direction (18%) compared with the perpendicular direction (almost 38%). However, it should be noted that the fracture toughness of LPBF shows high values in the main directions, higher even than those of the HP and wrought samples. Additionally, the highest level of homogeneity even in comparison with wrought sample, was observed for the HP sintered samples with equiaxed grains with visible twin boundaries. The tensile properties, mainly strength and elongation, were the highest for HP material. Overall, from a practical standpoint, the results showed that HP sintering is the best method in terms of homogeneity based on microstructural and mechanical properties. Słowa kluczowe: Haynes 282 nickel alloy, LPBF, HP, SEM , Static tensile test Afiliacje autorów:
Maj P. | - | Politechnika Warszawska (PL) | Bochenek K. | - | IPPT PAN | Sitek R. | - | Politechnika Warszawska (PL) | Koralnik M. | - | inna afiliacja | Jonak K. | - | inna afiliacja | Wieczorek M. | - | inna afiliacja | Pakieła Z. | - | Politechnika Warszawska (PL) | Mizera J. | - | Politechnika Warszawska (PL) |
| 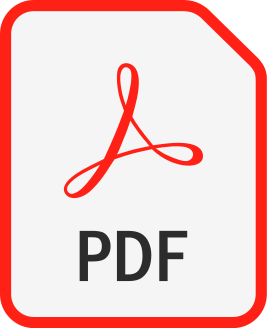 | 140p. |
8. |
Kopeć M., Liu X.♦, Kukla D., Sitek R.♦, Kowalewski Z.L., Effect of printing direction on fatigue response and damage development in additive manufactured Haynes 282 nickel superalloy,
INTERNATIONAL JOURNAL OF DAMAGE MECHANICS, ISSN: 1056-7895, DOI: 10.1177/10567895231204951, pp.1-15, 2023 Streszczenie: In this paper, three different directions of 0°, 45° and 90° were used to manufacture the Haynes 282 alloy bars by using the Direct Metal Laser Sintering (DMLS) method. The additively manufactured specimens as well as these of the wrought Haynes 282 were subsequently subjected to comparative fatigue tests in the range of stress amplitude from ±400 MPa to ±800 MPa. The AM process enhanced the fatigue response of the nickel-based alloy in question by 200 MPa. Furthermore, it was found, that the printing direction does not affect the fatigue response of additively manufactured specimens significantly as minor differences in service life were observed for the entire stress amplitude range adopted. Finally, fatigue damage measure φ and fatigue damage parameter D approaches were used to reveal the dynamics of damage development and to monitor damage development due to fatigue. Słowa kluczowe: Haynes 282, nickel alloys, fatigue, additive manufacturing, Direct Metal Laser Sintering (DMLS) Afiliacje autorów:
Kopeć M. | - | IPPT PAN | Liu X. | - | Imperial College London (GB) | Kukla D. | - | IPPT PAN | Sitek R. | - | Politechnika Warszawska (PL) | Kowalewski Z.L. | - | IPPT PAN |
| 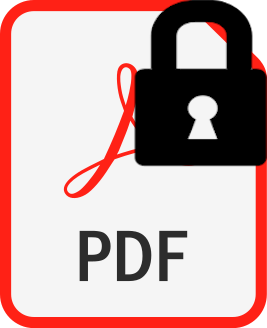 | 100p. |
9. |
Barwińska I., Kopeć M., Kukla D., Łazińska M.♦, Sitek R.♦, Kowalewski Z., Effect of Aluminizing on the Fatigue and High-Temperature Corrosion Resistance of Inconel 740 Nickel Alloy,
The Journal of The Minerals, ISSN: 1047-4838, DOI: 10.1007/s11837-022-05662-w, Vol.75, No.2, pp.1-13, 2023 Streszczenie: The fatigue response and high-temperature corrosion resistance of Inconel 740 nickel alloy in its as-received state, and the same material with aluminized surface layer, were investigated. The aluminized layer was applied by using the chemical vapor deposition process with the participation of AlCl3 vapors under a hydrogen protective atmosphere at a temperature of 1040°C for 8 h and internal pressure of 150 hPa. The microstructure of the aluminized layer was characterized through scanning electron microscopy and x-ray energy dispersive spectroscopy analysis. It was found that Inconel 740 with an aluminized surface exhibited an improved hardness and fatigue response of 100 MPa in the whole range of stress amplitudes from 350 MPa to 650 MPa. Additionally, the application of the aluminization process enhanced service life as well as the corrosion resistance of the alloy in question and effectively protected it against high-temperature corrosion. Afiliacje autorów:
Barwińska I. | - | IPPT PAN | Kopeć M. | - | IPPT PAN | Kukla D. | - | IPPT PAN | Łazińska M. | - | Military University of Technology (PL) | Sitek R. | - | Politechnika Warszawska (PL) | Kowalewski Z. | - | IPPT PAN |
| 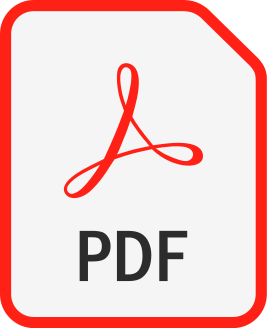 | 100p. |
10. |
Kopeć M., Gorniewicz D.♦, Kukla D., Barwińska I., Jóźwiak S.♦, Sitek R.♦, Kowalewski Z.L., Effect of plasma nitriding process on the fatigue and high temperature corrosion resistance of Inconel 740H nickel alloy,
ARCHIVES OF CIVIL AND MECHANICAL ENGINEERING, ISSN: 1644-9665, DOI: 10.1007/s43452-022-00381-0, pp.57-1-15, 2022 Streszczenie: The paper presents a comparison of microhardness, fatigue and high temperature corrosion of Inconel 740H nickel alloy in its as-received state and the same material with nitrided surface layers. The nitrided layers were produced using traditional glow discharge nitriding (specimens nitriding on the cathode potential) and an active screen (specimens nitriding at the plasma potential). A microstructure of the layers was characterized through the scanning electron microscopy, X-ray energy dispersive spectroscopy and X-ray diffraction analysis. Mechanical properties of the nitrided Inconel 740H alloy were examined using microhardness measurements and standard fatigue tests. It was found that Inconel 740H with a nitrided surface exhibited an improved fatigue response of 50 MPa in the whole range of stress amplitudes from 350 to 650 MPa and almost 325% increase of hardness for plasma modified surface and 250% for cathode modified surface. Additionally, the application of cathode nitriding enhanced the corrosion resistance of the alloy in question and effectively protected it against a high temperature oxidation. Słowa kluczowe: nitriding, nickel alloys, coatings, fatigue, corrosion Afiliacje autorów:
Kopeć M. | - | IPPT PAN | Gorniewicz D. | - | Military University of Technology (PL) | Kukla D. | - | IPPT PAN | Barwińska I. | - | IPPT PAN | Jóźwiak S. | - | Military University of Technology (PL) | Sitek R. | - | Politechnika Warszawska (PL) | Kowalewski Z.L. | - | IPPT PAN |
| 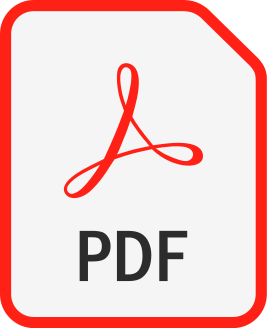 | 140p. |
11. |
Kukla D., Kopeć M., Sitek R.♦, Olejnik A.♦, Kachel S.♦, Kiszkowiak Ł.♦, A novel method for high temperature fatigue testing of nickel superalloy turbine blades with additional NDT diagnostics,
Materials, ISSN: 1996-1944, DOI: 10.3390/ma14061392, Vol.14, No.6, pp.1392-1-17, 2021 Streszczenie: In this paper, a novel method for high temperature fatigue strength assessment of nickel superalloy turbine blades after operation at different times (303 and 473 h) was presented. The studies included destructive testing (fatigue testing at temperature 950 °C under cyclic bending load), non-destructive testing (Fluorescent Penetrant Inspection and Eddy Current method), and finite element modelling. High temperature fatigue tests were performed within load range from 5200 to 6600 N using a special self-designed blade grip attached to the conventional testing machine. The experimental results were compared with the finite element model generated from the ANSYS software. It was found that failure of turbine blades occurred in the area with the highest stress concertation, which was accurately predicted by the finite element (FE) model. Słowa kluczowe: nickel superalloys, high temperature fatigue, finite element (FE) modelling, eddy current Afiliacje autorów:
Kukla D. | - | IPPT PAN | Kopeć M. | - | IPPT PAN | Sitek R. | - | Politechnika Warszawska (PL) | Olejnik A. | - | inna afiliacja | Kachel S. | - | inna afiliacja | Kiszkowiak Ł. | - | inna afiliacja |
| 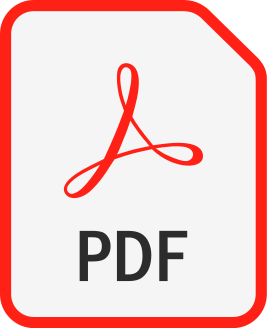 | 140p. |
12. |
Kukla D., Sitek R.♦, Influence of aluminide layer on the dynamics of the development of fatigue damage in Ni-Cr-Co alloy,
SOLID STATE PHENOMENA, ISSN: 1012-0394, DOI: 10.4028/www.scientific.net/SSP.240.101, Vol.240, pp.101-107, 2016 Streszczenie: Thermomechanical conditions in which the elements of modern aircraft engines work, require the use of protective coatings. The coatings increase the creep strength and also the local thermal stress in the near-surface areas due to the differing thermal expansion of particular material layers. For this reason it is necessary to develop a method for evaluating the operating properties of nickel superalloys with the aluminide layer, taking into consideration the surface processes related to the thermo-mechanical fatigue, taking place during the operation. In the presented work the assessment of the influence of the aluminium-coated layer, deposited on the nickel alloy specimens in the chemical deposition process (CVD) on the changes of the damage parameter in cyclic load conditions was carried out. The damage parameter was defined as a total strain in consecutive load cycles. The dynamics of damage development was analysed for two specimen lots (4 with the layer and 4 without it) displaying axial symmetry with a narrowing in the measured section. The results obtained were correlated with the results of fractography studies using SEM. The results obtained were used for the determination of the relationship between the damage parameter being the sum of the average strain and the strain amplitude, and the number of cycles, until the specimen is destroyed. Słowa kluczowe: Alumina Layer, Fatigue Damage, Super Nickel Alloy Afiliacje autorów:
Kukla D. | - | IPPT PAN | Sitek R. | - | Politechnika Warszawska (PL) |
| 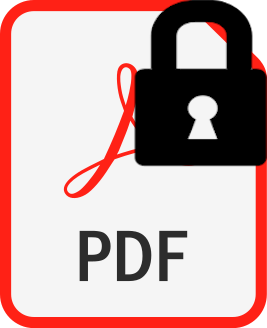 |
13. |
Sitek R.♦, Kukla D., Kobayashi A.♦, Kurzydłowski K.J.♦, Influence of High-Temperature Aluminizing on the Fatigue and Corrosion Resistanceo f Nickel Alloy Inconel 740,
Frontier of Applied Plasma Technology, ISSN: 1883-5589, Vol.7, No.1, pp.21-24, 2014 Streszczenie: The paper presents the results of studies on the structure and properties of the AlNi type diffusion layers fabricated on the IN 740 nickel alloy by chemical vapor deposition using aluminium chloride (AlCl3), introduced into a hydrogen atmosphere. The layers were examined by light microscopy and scanning electron microscopy. Their chemical composition was examined by EDS, and the phase composition - using a Bruker D8 X-ray diffractometer with CuKa radiation. Fatigue tests were carried out in Inconel 740 sample, in the initial state and covered with the diffusion intermetallic AlNi layers. The strength under dynamic load was examined using a MTS 858 testing machine using symmetric load cycles repeated at a frequency of 20 Hz. The stress amplitude was 550 MPa. Corrosion resistance tests were performed employing potentiodynamic methods, in 0.1M Na2SO4 solution, at ambient temperature. It is shown that the layers improve the fatigue resistance and corrosion resistance of the Inconel 740 substrate. Słowa kluczowe: Inconel 740, CVD, Aluminide layer, High-cycle fatigue, corrosion resistance Afiliacje autorów:
Sitek R. | - | Politechnika Warszawska (PL) | Kukla D. | - | IPPT PAN | Kobayashi A. | - | University of Technology Malaysia KL (MY) | Kurzydłowski K.J. | - | Politechnika Warszawska (PL) |
| 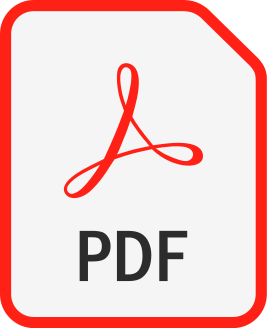 |